Сущность процесса, виды газотермических способов нанесения покрытий, их достоинства, недостатки и область применения.
Разностороннюю быстро развивающуюся область техники представляет нанесение покрытия из металлических, керамических и полимерных материалов методами газотермического напыления.
Эти процессы основаны на нагреве или расплавлении наносимого материала и распылении его на обрабатываемую поверхность с целью получения покрытия, обладающего заданными свойствами и прочностью сцепления с основой.
Наиболее распространенными источниками теплоты для нагрева или расплавления наносимого материала являются газокислородное пламя, электрическая дуга или плазменная дуга.
Известны и другие способы нагрева наносимого материала, например токами высокой частоты, импульсным разрядом тока высокого напряжения, детонационным горением топливно-кислородной смеси и т. д. Однако эти способы получили менее широкое применение.
Поэтому в дальнейшем изложении мы ограничимся рассмотрением главным образом трех основных по типу применяемого источника нагрева методов газотермического напыления: газопламенного, электродугового и плазменного.
Этими методами можно напылять покрытия практически из любых металлов и материалов (керамики, термопластов и др.) в виде проволоки, прутков (стержней), жилок или порошков.
Напыленные покрытия нельзя использовать самостоятельно как конструкционный материал для изготовления деталей машин, подвергающихся растягивающим и изгибающим усилиям. Однако покрытие работает вполне удовлетворительно совместно с материалом основания.
|
|
В качестве последнего можно использовать изделия не только из черных и цветных металлов, но также из других самых разнообразных материалов, в том числе из бумаги, ткани, дерева, керамики и прочих, так как при напылении температура нагрева
изделия не превышает 50—100° С. Вследствие этого основной материал не претерпевает структурных изменений, сохраняя полностью свои механические свойства, за исключением случаев, когда напыленное покрытие подвергается последующему оплавлению, например при напылении твердых сплавов.
Процессы газотермического напыления отличаются технологической простотой, несложностью, компактностью и транспортабельностью оборудования. Они позволяют регулировать в широких пределах физико-механические и другие свойства получаемых покрытий (прочность сцепления, твердость, пористость, износостойкость и т. д.) в зависимости от рода напыляемого материала, вида обработки поверхности изделия, режимов напыления и т. д.
Эти особенности процессов газотермического напыления обусловливают универсальность их применения, многообразие областей и видов возможного использования.
|
|
Общим для всех известных процессов получения напыленных покрытий является термическая обработка (нагрев) наносимого материала до пластического состояния или расплавления и направленное перемещение (перенос) частиц материала в дисперсной форме на обрабатываемую основу.
Поскольку перенос нагретых частиц, как правило, осуществляется газовой фазой (струей воздуха, плазменной струей и т. д.) или продуктами сгорания горючей смеси (при детонационном напылении), наиболее полно отражает природу процесса термин «газотермическое напыление».
Привычный термин «металлизация», возникший до развития методов напыления неметаллических материалов (пластмасс, керамики, окислов, карбидов и т. д.), в настоящее время уже не может служить собирательным термином, охватывающим все многообразие существующих процессов.
Достижение конечной цели процесса газотермического напыления — получение покрытий с заданными свойствами, зависит от совокупности условий, определяемых составом и видом напыляемых материалов, взаимодействием их с окружающей средой, а также применяемой технологии и аппаратуры.
Способы и технология нанесения полимерных материалов на поверхности деталей.
|
|
Изобретение относится к способам нанесения покрытий на детали из усиленных волокнами полимерных композиционных материалов. Согласно способу сначала на покрываемую поверхность детали посредством термического напыления наносят слой сцепления из соединения, состоящего из органического компонента в виде полимера и металлического компонента. На слой сцепления посредством термического или кинетического напыления наносят промежуточный слой на основе металлических компонентов. Затем на промежуточный слой посредством термического или кинетического напыления наносят функциональный наружный слой из металла или соединения металла с карбидом, или оксидной керамики, или смеси из вышеупомянутых материалов. Технический результат - повышение износостойкости поверхности. 12 з.п. ф-лы.
Изобретение касается изготовления функциональных поверхностей на композиционных материалах, усиленных волокнами с использованием термического и кинетического напыления, причем придается особенное значение защите поверхностей против износа, механического повреждения, нанесению покрытия и адгезии, а также улучшению в отношении отделения листа (отделяемости).
|
|
С помощью композиционных материалов, усиленных волокном, в особенности материалов с полимерной основой, а также полимеров, армированных угольным волокном, можно изготовить детали, которые обладают исключительными механическими и физическими свойствами, как например низкой плотностью, высоким пределом прочности при растяжении и пределом прочности при кручении, высоким модулем упругости или соответственно высокой жесткостью. Множество высокопрочных волокнистых материалов могут применяться, включая угольное волокно, стекловолокно, волокно карбида кремния и волокна многих других оксидов, карбидов и других материалов. Таким же образом может использоваться большое количество полимерных материалов, включая термоотверждаемые полимеры, как например фенольная смола, эпоксидная смола и многие другие материалы. Волокна могут быть очень длинными и располагаться в специальных образцах, или они могут быть относительно короткими и иметь случайное распределение. Если длинные волокна располагаются в специфических образцах, то они могут быть ориентированными в единственном направлении или упорядочиваться в образцах, которые рассчитаны для придания усиленным волокнами композиционным материалам двух- или трехмерной прочности. Таким образом, механические свойства структуры усиленных волокнами композиционных материалов могут согласовывать со специфическими требованиями составляющей.
К сожалению, поверхности композиционных материалов, усиленных волокнами, обладают низкой износостойкостью, в особенности в отношении адгезивного износа, абразивного износа и эрозионного износа и их свойства склеивания и смачивания недостаточны для многих применений, как в случае бумажной промышленности. Кроме того, они нередко подвержены окислению или другим формам коррозии, нуждаются в термозащите, не располагают необходимыми оптическими и электрическими характеристиками и тому подобное. Вследствие этого применение композиционного материала, усиленного волокнами, ограничено при частых использованиях или требуется применение металлических или керамических вставок, или покрытия в тех областях, которые подвержены контакту с другими деталями или материалами и при этом подвержены повышенному износу.
Несмотря на то, что особенно интересно применение роликов из усиленных волокнами композиционных материалов в печатной индустрии, бумажной промышленности и в промышленности полимерной пленки (фольги), т.к. они существенно легче и тверже и вследствие чего могут проще и надежней использоваться, по сравнению, например, с роликами, изготовленными из стали, и таким образом, по причине их низкой инерции, требуются меньше энергии и времени для их ускорения и торможения, что позволяет экономить затраты не только при обслуживании и монтаже, но и при эксплуатации. Для того чтобы предусмотреть рабочие поверхности роликов с требуемыми свойствами, ролики имеют металлическое, керамическое или карбидное покрытие, или их смеси с полимерными материалами, что дает требуемую износостойкость, а также другие необходимые свойства. Посредством применения термического метода напыления можно получать большое количество металлических и керамических покрытий, металлокерамических покрытий, т.е. включение частиц карбидов в металлическую матрицу, а также некоторые полимерные покрытия.
Группа термических методов напыления содержит детонационное напыление (среди прочего, Super D-GunTM), высокоскоростное газопламенное напыление и его варианты, как например, напыление посредством топлива и воздуха, плазменное напыление, газопламенное напыление, электродуговое напыление. В большинстве термических способов нанесения покрытий напыляемый материал в виде порошка, проволоки или прутка нагревается до температуры, которая лежит у или несколько выше точки плавления, и капельки или наплавляемые частицы материала ускоряются в газовом потоке. Капельки подводят к внешней поверхности подложки (участка или компонента), который нужно покрыть, где они прилипают, затвердевают и образуют сплошное покрытие со слоистой структурой. В качестве особенности процесса детонационного напыления, осуществляющегося прерывисто, возникает покрытие из отдельных, наложенных внахлестку, жестко связанных пятен (крапинок) напыления. Такого рода методы знакомы специалистам и подробно описаны в многочисленных брошюрах.
Несмотря на то, что проводилось много попыток нанести термическое напыление покрытия на основе металла, керамики или карбида непосредственно на поверхности усиленных волокнами композиционных материалов, обычно можно было добиться только низкого сцепления покрытия, нередко слои покрытия не прилипали к усиленному волокнами подслою или отслаивались уже после осаждения маленькой толщины слоя. Обычно поверхности детали перед термическим напылением покрытия придают шероховатость для улучшения прилипания (адгезии). Шероховатость поверхности придают чаще всего посредством струи корунда. Однако струи корунда или другие формы придания шероховатости покрываемых поверхностей могут привести к неприемлемой эрозии полимерной основы, связанной с обнажением волокон. Последнее, в свою очередь, может постоянно наносить ущерб свойствам покрытия.
Эти и другие проблемы имели место, например, при применении способа, описанного в US-A-5857950. В данном способе поверхность ролика с угольным волокном подвергают пескоструйной обработке, затем наносят покрытие цинка, действующее как тепловая защита. После повторной пескоструйной обработке роликов, теперь покрытых цинком, наносят слой сцепления, при котором речь может идти о смеси из алюминиевой бронзы и сложного полиэфира. Затем проводят пескоструйную обработку слоя сцепления и наносят покрытие напылением керамики и гравируют. Этот метод оказался неприемлемым.
Если целью покрытия материала, усиленного волокнами, является прежде всего повышение износостойкости, то функциональный наружный слой системы слоев состоит предпочтительно из оксидной керамики (например, оксид хрома) или из кермета (металлокерамика, например частицы карбида вольфрама, включенные в металлическую основу кобальта).
1. Способ нанесения покрытия на деталь из усиленного волокнами полимерного композиционного материала, отличающийся тем, что сначала на покрываемую поверхность детали посредством термического напыления наносят слой сцепления из соединения, состоящего из органического компонента в виде полимера и металлического компонента, на слой сцепления посредством термического или кинетического напыления наносят промежуточный слой на основе металлических компонентов, и затем на промежуточный слой посредством термического или кинетического напыления наносят функциональный наружный слой из металла или соединения металла с карбидом, или оксидной керамики, или смеси из вышеупомянутых материалов.
Дата добавления: 2018-06-01; просмотров: 993; Мы поможем в написании вашей работы! |
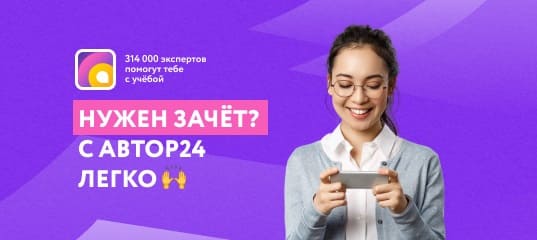
Мы поможем в написании ваших работ!