Пневматические, гидравлические, акустические методы обнаружения скрытых дефектов. Разновидности. Сущность. Область применения.
Для выявления скрытых дефектов в конструкционных материалах используются различные методы неразрушающего контроля (дефектоскопии).
Известно, что дефекты в металле являются причиной изменения его физических характеристик: плотности, электропроводности, магнитной проницаемости, упругих и других свойств. Исследование этих характеристик и обнаружение с их помощью дефектов составляет физическую сущность методов неразрушающего контроля. Эти методы основаны на использовании проникающих излучений рентгеновских и гамма-лучей, магнитных и электромагнитных полей, колебаний, оптических спектров, явлений капиллярности и других.
Акустические методыоснованы на регистрации параметров упругих колебаний, возбужденных в исследуемом объекте. Эти методы широко применяются для контроля толщины деталей, оплошности (трещин, пористости, раковин и т. п.) и физико-механических свойств (зернистости, межкристаллитной коррозии, глубины закаленного слоя и др.) материала. Контроль выполняется на основании анализа характера распространения звуковых волн в материале детали (амплитуды, фазы, скорости, угла преломления, резонансных явлений). Метод пригоден для деталей, материал которых способен упруго сопротивляться деформациям сдвига (металлы, фарфор, оргстекло, некоторые пластмассы)
В зависимости от частоты акустические волны подразделяют на инфракрасные – с частотой до 20 Гц, звуковые (от 20 до 2∙104 Гц), ультразвуковые (от 2∙104 до 109 Гц) и гиперзвуковые (свыше 109 Гц). Ультразвуковые дефектоскопы работают с УЗК от 0,5 до 10 МГц.
|
|
К основным недостаткам ультразвуковых методов относятся необходимость достаточно высокой чистоты поверхности деталей и существенная зависимость качества контроля от квалификации оператора-дефектоскописта.
Метод пневматического испытания применяют при контроле на герметичность таких деталей, как радиаторы, баки, трубопроводы и др. Полость детали в этом случае заполняют сжатым воздухом под давлением, соответствующим техническим условиям на испытание, и затем погружают в ванну с водой. Выходящие из трещины пузырьки воздуха укажут место нахождения дефектов.
Метод гидравлического испытания применяют для выявления трещин в корпусных деталях (блок и головка цилиндров). Испытание производится на специальных стендах, которые обеспечивают герметизацию всех отверстий в контролируемых деталях. При испытании полость детали заполняют горячей водой под давлением 0,3.. .0,4 МПа. О наличии трещин судят по подтеканию воды.
Сборка прессовых соединений.
Качество сборки прессовых соединений формируется под воздействием следующих факторов: значения натяга, материала сопрягаемых деталей, геометрических размеров, формы и шероховатости поверхностей, соосности деталей прилагаемого усилия запрессовывания, наличия смазки и др.
|
|
Применение смазочного материала уменьшает требуемое усилие запрессовки и предохраняет сопрягаемые поверхности от задиров. Качество сборки прессовых соединений определяется также точностью центрирования сопрягаемых деталей (с помощью приспособлений и оправок).
Повышение прочности неподвижных соединений с натягом в 1,5...2,5 раза обеспечивается применением сборки с термовоздействием -- нагревом охватывающей и (или) охлаждением охватываемой детали. При этом образуется необходимый сборочный зазор и не требуется приложение осевой силы. Нагрев деталей осуществляется в масляных ваннах, электропечах, индукционных установках и др. Для охлаждения деталей применяют жидкий азот, сухой лед (твердую углекислоту) в смеси с ацетоном, бензином или спиртом.
Прессовые соединения получают путем напрессовки одной детали на другую (например, зубчатого венца на маховик двигателя) или запрессовкой одной детали в отверстие другой (например, направляющей втулки клапана в отверстие в блоке цилиндров двигателя).
|
|
Трудоемкость сборки прессовых соединений составляет 10—15% общей трудоемкости сборочных работ.
Сборка прессовых соединений осуществляется с помощью различных гидравлических, пневматических и рычажных прессов, а также вручную, с помощью оправки и молотка.
Для нормальной работы прессового соединения большое значение имеет плотность посадки деталей, которая определяется необходимой величиной натяга, создаваемого при запрессовке. При сборке некоторых соединений даже незначительное увеличение натяга может привести к разрыву деталей (например, при запрессовке гильз в цилиндры блока двигателя). Поэтому при сборке таких соединений необходимо контролировать усилие запрессовки, величина которого зависит от величины натяга. На гидравлических прессах это усилие контролируют по манометру.
Как при запрессовке, так и при напрессовке деталей необходимо исключить возможность их перекосов, а также обеспечить равномерное распределение прикладываемого усилия. Это достигается применением различного рода центрирующих оправок и наставок.
В некоторых случаях сборка прессовых соединений облегчается путем нагрева охватывающей детали. Таким образом, например, собирают маховик с зубчатым венцом. Нагретый зубчатый венец напрессовывают на маховик легким постукиванием молотка.
Дата добавления: 2018-06-01; просмотров: 1001; Мы поможем в написании вашей работы! |
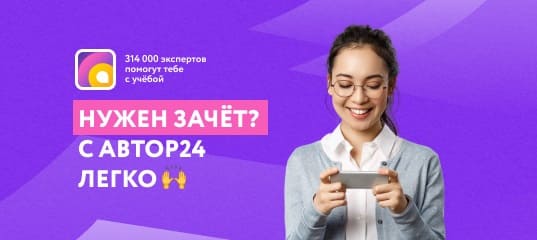
Мы поможем в написании ваших работ!