Вычислительная рентгеновская томография
Промышленная рентгеновская вычислительная томография (ВРТ)– высокоэффективный метод радиационного контроля, сочетающий возможности рентгеновского излучения и цифровой техники, позволяющий с высокой точностью получать плоские сечения и объемные изображения контролируемых изделий.[9]
В зависимости от мощности источника излучения томографы могут устанавливаться в отдельном помещении с защитными стенами (максимальная энергия источника 5 МэВ) или располагаться в общей производственной зоне в виде бокса со свинцовыми стенками (рис. 15).
Принцип работы томографа (рис. 16) основан на реконструкции и визуализации внутренней структуры поперечных сечении объекта контроля (томограмм) в результате совместной вычислительной обработки теневых проекций, полученных при рентгеновском просвечивании объекта контроля в различных направлениях. Послойный характер исследования и визуализации объемной структуры исследуемого объекта связан с используемым упрощающим приемом, сводящим трехмерную задачу неразрушающего контроля к серии двумерных томограмм (сечений).
А Б
Рис.15. Общий вид вычислительного рентгеновского томографа
А) томограф ВТ-600ХА ООО «Проминтро», Б) X-50 North Star Imaging, Inc
Рис.16. Принцип работы томографа.
В общем виде в состав томографа входит ряд ключевых блоков - рабочий стол (обеспечивает фиксацию объекта контроля и его перемещение между источником и приемником излучения), источник излучения (в промышленных томографах в большинстве случаев применяются источники рентгеновского излучения), блок сбора проекционных данных, блок обработки данных и блок визуализации и управления работой томографа. Структурно томограф можно разделить на сканирующую систему, включающую источник излучения, рабочий стол и блок сбора проекционных данных, и вычислительный комплекс, отвечающий за управление, обработку и предоставление конечных данных пользователю.
|
|
В общем виде метод ВРТ сводится к реконструкции пространственного распределения линейного коэффициента ослабления (ЛКО) (рис. 17) рентгеновского излучения при прохождении через объект исследования, т.е. позволяет определить плотность объекта в каждой точке рабочей области томограммы [8,9].
Рис. 17. График распределения линейного коэффициента ослабления.
После обработки эта информация, распределенная по томограмме в виде матрицы значений, пересчитывается в яркостное изображение, которое выводится на рабочий экран оператора. В дальнейшем, при достаточном шаге сканирования, яркостные изображения могут объединяться в трехмерное изображение, которое можно использовать как непосредственно для оценки состояния структуры, так и для реверс инжиниринга или сравнения с CAD моделью. (рис. 18)
|
|
А Б В
Рис. 18. Анализ изделия методом ВРТ А – анализ дефектов структуры, Б – получение геометрических размеров, В – определение отклонений геометрии по сравнению с CAD моделью.
Процесс исследования структуры материала с применением ВРТ состоит из следующих основных этапов:
- выбор режимов рентгеновского облучения исследуемых образцов и сечений сканирования;
- сканирование выбранных сечений и измерение коэффициента ослабления рентгеновского излучения;
- реконструкция полученных результатов сканирования, получение диаграмм распределения коэффициента ослабления и геометрических параметров сечений:
- обработка полученных данных реконструкции сечений при помощи критериев корреляции;
- построение визуальной картины, отображающей состояние структуры исследуемого образца.
Самым технологичным в настоящее время является процесс объемного (спирального) сканирования (рис. 19), при котором происходит практически полное исключение пропусков сканирования по высоте изделия [5].
|
|
Рис.19. Спиральное томографическое сканирование, встроенное в технологическую линию.
Определение уровней ЛКО производится на основе вычислительной обработки теневых проекций, полученных при просвечивании объекта под разными углами. При анализе изделий с известной плотностью ЛКО может быть пересчитан в количественное значение плотности через переводной коэффициент, определяемый экспериментально для выбранных параметров сканирования. Томографическая информация позволяет вводить параметры, позволяющие качественно или количественно оценивать состояние структуры материала.
Томографические параметры могут быть определены двумя основными способами:
1. Вдоль линии на томограмме с определением среднего значения ЛКО и вариацией ЛКО (рис.20)
Рис. 20. Распределение ЛКО вдоль линии на томограмме
2. В определённой зоне на томограмме изделия. (рис. 21) В данном случае идет определение по 90-95% процентам площади объекта контроля.
Рис.21. Определение томографических параметров по выбранной зоне внутри образца
|
|
Базовыми параметрами, определяемыми в выбранной зоне изделия, при исследовании методом ВРТ являются:
1. Среднее значение ЛКО - количественно характеризует структурную плотность в отсканированном сечении;
2. Максимальное и минимальное значения ЛКО, характеризующие наибольшие пики в выбранной зоне.
3. Среднеквадратичное отклонение (СКО) значения линейного коэффициента ослабления в отсканированном сечении характеризует амплитуду абсолютного отклонения ЛКО от наиболее вероятного значения, т.е. «рыхлость» материала.
Томограммы отдельных видов дефектов в ПКМ представлены на рисунках 22-26.
Рис. 22. Микроструктура ПКМ с воздушными включениями.
Рис. 23. Расслоение материала в стенке конструкции.
Рис. 24. Визуализация вымывания связующего на примере двух образцов.
Рис. 25. Раковины в приформовочном угольнике.
Рис. 26. Расслоение в приформовочном угольнике.
Конструкционный контроль
Диагностический контроль состояния конструкционных элементов (structural health monitoring, SHM) — данная технология относится к технологиям, позволяющий контролировать весь жизненный цикл изделия из ПКМ, начиная с процесса отверждения. Процедура постоянного контроля состояния материала конструкции входит в состав технологии, называемой «интеллектуальные конструкции», которые должны в перспективе уметь распознавать возникшую ситуацию и сформировать ответную реакцию. Система SHM выполняет сенсорную функцию, т.е. должна определить воздействия и последствия данного воздействия на материал. Одним из вариантов построения такой системы является использование оптоволоконных линий и датчиков, снимающих информацию о внешних воздействиях и действующих нагрузках.
Датчики устанавливаются на поверхности контролируемой детали (в случае металла) или располагаются внутри материала (в случае изделий из ПКМ).
Такие системы позволяют диагностировать поведение конструкции в режиме реального времени (рис. 27) как при стандартной эксплуатации, так и в экстремальных условиях, путем сбора данных об изменениях напряженно-деформированного состояния (нагрузок) и регистрации повреждений, в том числе и ударных воздействий (дислокация и энергия удара).
Состав волоконно-оптической системы мониторинга:
1. Волоконно-оптические датчики физических величин (температура, деформация, виброакустика) (рис. 28)
2. Оптоволоконные линии связи (кабели)
3. Регистрирующая аппаратура (блок-регистратор).
Для интерпретации данных в режиме реального времени разрабатывается программное обеспечение и математическая модель конструкции летательного аппарата.
Обладая уникальными механическими характеристиками и сверхмалыми габаритами, сравнимыми с размерами компонентов композита, оптическое волокно может быть интегрировано в состав композита при его изготовлении, тем самым позволяя диагностировать технологический процесс изготовления деталей и контролировать элементы конструкций на начальном этапе жизненного цикла изделия.
Рис. 27. Принцип работы системы непрерывного мониторинга состояния конструкции.
В зонах, где необходимо производить непрерывный мониторинг величины приложенных нагрузок или возникновения дефектов, устанавливаются датчики. Сигнал, коррелирующий со значением деформации (нагрузки) или с возникновением дефекта, поступает от датчика на блок аналого-цифрового преобразователя по каналу данных. Данные от датчика усиливаются (в случае необходимости) и проходят аналого-цифровое преобразование, после чего по помехозащищенному цифровому интерфейсу передаются для математической обработки в микропроцессор или компьютер. В них производится накопление данных со всех сенсорных элементов летательного аппарата и их преобразование после соответствующей математической обработки в значения деформации (либо нагрузок) или регистрируется появление дефекта. Преобразованные данные поступают с определенной периодичностью на бортовую вычислительную машину, где в соответствии с установленными правилами записываются регистратором параметров полета («черный» ящик), и отображаются на информационном табло пилота только при возникновении нагрузки, недопустимой для контролируемой конструкции.
А Б
Рис. 28. А – результирующий сигнал с оптоволоконных датчиков, Б – оптоволоконные датчики и система регистрации
Система сбора и обработки информации позволяет получить данные о текущем состоянии труднодоступных и высоконагруженных мест на летательном аппарате, спрогнозировать остаток ресурса конструкции и предупредить о возможном разрушении ее материала.
БИБЛИОГРАФИЧЕСКИЙ СПИСОК
1. В.В. Сухоруков, Э.И. Вайнберг и др. Неразрушающий контроль, кн.5 - М. «Высшая школа», 1993.- 340С.
2. Сударикова Е. В. Неразрушающий контроль в производстве: учеб. пособие. Ч. 1.; ГУАП. — СПб., 2007. — 137 с.: ил
3. Principles of the Manufacturing of Composite Materials, Suong V. Hoa, DEStech Publications, Inc., USA, 2009, 337 p.
4. Воробей, В.В. Контроль качества изготовления и технология ремонта композитных конструкций [Текст] / В.В. Воробей, В.Б. Маркин. – Новосибирск: Наука, 2006. – 400 с
5. Связующие для полимерных композиционных материалов А.Ю. Алентьев, М.Ю. Яблокова// Учебное пособие для студентов по специальности «Композиционные наноматериалы». М.: 2010.- 70 с.
6. Методы неразрушающего контроля, применяемые для конструкций изперспективных композиционных материалов Труды МАИ Выпуск №49, Бойцов Б. В., Васильев С. Л., Громашев А. Г., Юргенсон С. А.
7. Барынин В. А., Будадин О. Н., Кульков А. А. Современные технологии неразрушающего контроля конструкций из полимерных композиционных материалов. – М.: Спектр, 2013. – 242 с
8. Рекламные материалы ООО «Нева Технолоджи».
9. Неразрушающий контроль и диагностика: Справочник / В.В. Клюев, Ф.Р. Сосин, А.В. Ковалев, Э.И. Вайнберг и др. 2-е изд. М. Машиностроение, 2003. 656 с.
ПРИЛОЖЕНИЕ А
Дата добавления: 2018-06-01; просмотров: 1911; Мы поможем в написании вашей работы! |
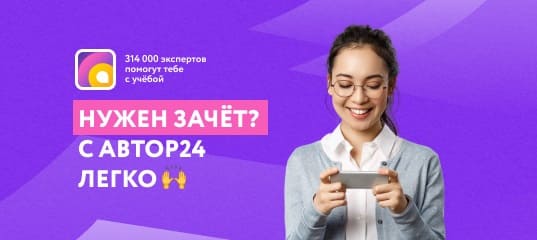
Мы поможем в написании ваших работ!