Процесс изготовления деталей из ПКМ
Полимерные композиционные материалы все шире применяются в производстве авиационной техники. На сегодняшний день доля агрегатов и узлов, изготовленных из ПКМ в гражданских авиалайнерах, достигает 50% (рис. 1). Это связано с возможностью оптимизировать характеристики и геометрические параметры отдельных конструктивных элементов планера, что позволяет получить выигрыш в весе по сравнению с традиционными материалами (сталь, алюминий, титан и т.д.) на 10-15%, при этом процесс разработки конструкции включает в себя разработку материала (подбор типов армирующих материалов и связующего, определение их объемного содержания, количество слоев и их направление).
Производство изделий из композитов с полимерной матрицей (ПКМ) основано на их способности принимать под давлением и при нагреве необходимую форму и полимеризоваться, переходя в твердое состояние. В общем случае ПКМ состоит из армирующих элементов и связующего (матрицы). К армирующим элементам относятся высокопрочные материалы (металлы и неметаллы), которые воспринимают нагрузку. Связующие служат для перераспределения нагрузки между армирующим элементами и обеспечивают технологичность итоговой конструкции. Одним из главных недостатков ПКМ является высокий разброс свойств конечного материала и необходимость проведения большого объема испытаний на начальных этапах проектирования конкретной композиции. При разработке технологического процесса изготовления деталей из ПКМ особое внимание должно уделяться контролю деталей на разных этапах производственного цикла, т.к. одновременно производится формирование материала и конечного изделия.
|
|
Рис. 1. Доля ПКМ в современных гражданских самолетах.
Все технологические процессы изготовления изделий из КМ включают следующие основные операции:
1. раскрой армирующего материала;
2. формообразование — формирование изделия вместе со структурой ПКМ; Формообразование в общем виде может выполняться двумя методами – выкладкой или намоткой (рис.2). Намоткой изготавливаются различные оболочки вращения, при этом одновременно происходит совмещение армирующего материал и связующего. При намотке могут использоваться как ленты армирующего материала, так и отдельные нити. Выкладка осуществляется лентами материала и может осуществляться как сухим материалом (рис. 3 А), так и предварительно пропитанным армирующим материалом (препрегом (рис.3 Б). Во втором случае процесс пропитки связующим производится заранее. Процесс намотки всегда осуществляется в автоматическом режиме, в то время как процесс выкладки может выполняться вручную или быть полностью автоматизированным. Для позиционирования слоев материала могут применяться проекционные системы.
|
|
А) Б)
Рис. 2. Пример формовки изделия А) намоткой, Б) выкладкой.
3. отверждение (полимеризация) связующего. В результате этой операции фиксируется форма изделия и образуется окончательная структура композита, определяющая его свойства. Процесс отверждения осуществляется при создании определенного давления, температуры и времени выдержки. Возможны различные варианты как процесса совмещения связующего и армирующих элементов, так и методы отверждения, к которым относятся прессование и автоклавные методы. Давление для тканных армирующих материалов может достигать 3-8 атм, температура формования сильно зависит от типа связующего и может варьироваться от 200 С (для связующего холодного отверждения) до 3000 С, время выдержки подбирается индивидуально и может доходить до 24 часов.
Пример задания параметров технологического процесс при формовке и пропитке под двойным вакуумным мешком представлен на рисунке 4.
4. доработка и соединение изготовленной детали с другими элементами (сборка).
|
|
Формовка и последующее отверждение может осуществляться с применение следующих методов:
¾ контактное (прикатка роликом, натяжением нити, обмотка жгутом, вибрационное формование);
¾ в пресскамерах (вакуумирование, автоклавное и гидроклавное формование);
¾ прессовое (жестким или упругим прессованием);
¾ термокомпрессионное (температурным расширением оснастки).
А) Б)
Рис. 3. Пример углеродных тканей в состоянии поставки: А) сухая ткань, Б) препрег.
Процесс возникновения дефектов может сопровождать весь цикл производства изделий из ПКМ. К основным параметрам, которые влияют на качество конструкции при формовке относятся температура формования, давление формовки, состав и свойства связующего, температура и время охлаждения. Так же уровень технологических дефектов в виде пористости засвисти от подготовки и типа связующего, наличия дренажа во время пропитки и т.д..
Рис. 4. Пример параметров технологического процесса.
На рисунке 5 представлены этапы промежуточного контроля качества при производстве изделия из ПКМ. Выполнение всех элементов контроля позволяет выявлять отклонения от серийного процесса изготовления и своевременно реагировать на возможные отклонения и оперативно устранять возможные отклонения.
|
|
Конкретные виды оценки качества (типы испытаний, виды контроля и их этапы) разрабатывает изготовитель изделия на базе рекомендаций и требований сертифицирующих производство органов и с учетом требований, предъявляемых к конкретному изделию, по допустимому уровню дефектов.
Рис. 5. Контроль качества изготовления на различных этапах технологического процесса.
Дата добавления: 2018-06-01; просмотров: 5271; Мы поможем в написании вашей работы! |
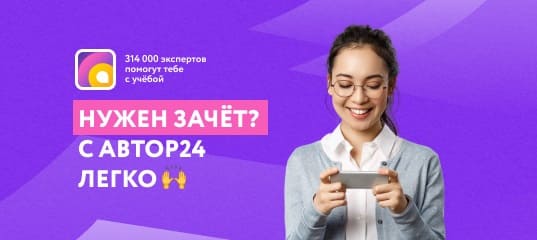
Мы поможем в написании ваших работ!