ГЛАВА 3. МЕТОДЫ ИССЛЕДОВАНИЯ ВНУТРЕННЕЙ СТРУКТУРЫ ПКМ
При формировании и эксплуатации образца (изделия) из ПКМ возможно протекание различных процессов, сказывающихся на их характеристиках. Поэтому при анализе технических и эксплуатационных характеристик композитов и изделий из них необходимо учитывать широкий набор свойств. При этом многие характеристики необходимо измерять после различных воздействий (температура, среда, вибрация, длительные нагрузки) на образец (изделие) для оценки возможных изменений.
Таким образом, методы анализа свойств композитов можно разделить на несколько групп методов, причем многие из них необходимо применять как до воздействия на материал, так и после, для оценки произошедших в композите изменений (рис.6) [5]
Конкретный метод контроля подбирается в зависимости от достаточно большого количества факторов – время контроля, необходимая точность, возможность автоматизации и т.д. Эти методы не определяют значения параметров материалов, а используются для выявления дефектов, возникших при изготовлении детали из-за нарушения технологии или обусловленные этой технологией. Также эти методы применяют для выявления дефектов возникших в процессе эксплуатации детали.
Практика неразрушающего контроля композиционных материалов показала, что для выявления дефектов нашли применение практически все методы и способы, традиционно применяемые в условиях производства, испытаний и эксплуатации техники, особенно при контроле материалов с неметаллической матрицей и наполнителем или комбинированные[6]:
|
|
- ультразвуковые методы,
- вибрационные методы,
- тепловые методы,
- методы акустико-эмиссионной диагностики,
- оптико-акустические методы
- рентгеновские.
Наиболее информативным является применение одновременно нескольких методов контроля, что значительно увеличивает информативность и качество контроля, но при этом повышает трудозатраты на выполнение работ.
Рис. 6. Методы анализа свойств изделий и образцов из ПКМ
При этом используемые методы контроля могут применяться как по отдельности, так и в комплексе, но применение большого методов контроля приводит к снижению производительности и повышения стоимости итогового изделия. Наиболее распространены методы ультразвуковой диагностики, однако в последние годы разрабатывается и ведется активное внедрение более современных методов неразрушающей диагностики композитов. В настоящее время разрабатываются специальные устройства для эксплуатационного контроля (начало работ в этом направлении связано с вводом в эксплуатацию самолета Boeing 787 конструкция которого на 50% составляет изделия, в том числе высоконагруженные, из ПКМ). Основным требованием к данному прибору является отсутствие специальных требований к линейному персоналу наземных служб. А основное назначение – поиск подповерхностных повреждений, вызванных ударным воздействием.
|
|
Ниже приведены наиболее распространенные методы контроля, применяемые при дефектоскопии изделий из ПКМ на различных этапах жизненного цикла.
Ультразвуковой метод контроля
Акустические методы, благодаря своей мобильности, составляют более 60% по отношению к другим методам неразрушающего контроля для изделий из ПКМ. Ультразвуковой метод контроля является универсальным методом неразрушающего контроля основанном на прохождении звуковых волн высокой частоты внутри материала. При ультразвуковом контроле из-за значительного затухания колебаний в ПКМ необходимо использовать значение возбуждаемых колебаний ниже 1 МГц. Для объектов с толщинами более 100 мм частотный диапазон может быть от 55 до 500 кГц. Однако снижение частоты снижает разрешающую способность и чувствительность ультразвукового контроля, а увеличение частоты уменьшает диапазон контролируемых толщин.
Одним из преимуществ данного метода является его универсальность - он может применяться на различных этапах жизненного цикла. Возможно различное исполнение ультразвуковых дефектоскопов – мобильные (Рис 7), на автоматизированной платформе (рис. 8) или лабораторные. Автоматизированные системы обладают достаточно высокой скоростью исследования с возможностью автоматического определения недопустимых дефектов. Лабораторные ультразвуковые установки обладают низкой скоростью исследования, одновременно с этим обеспечивая высокое разрешение итогового изображения.
|
|
Рис. 7. Мобильный ультразвуковой дефектоскоп.
Принцип проведения контроля при помощи ультразвукового эхо- импульсного метода основан на том, что излучатель посылает в изделие ультразвуковые импульсы. При встрече с преградой, например, с дефектом или обратной (донной) поверхностью, часть энергии ультразвуковой волны отражается и возвращается обратно к излучателю. Приёмник ультразвуковых колебаний преобразует прошедшие через изделие ультразвуковые колебания в электрические, которые поступают на экран – основной индикатор дефектоскопа. В результате сканирования выводится информация о прохождении сигнала (А-скан) и цветовые изображения о состоянии структуры в различных плоскостях (B, C и D-сканы) (рис. 9).
|
|
Рис. 8. Автоматизированный ультразвуковой дефектоскоп.
Недостатком ультразвукового метода исследования является быстрое затухание сигнала и не проходимость излучения за воздушные включения. Преимущество данного метода – возможность автоматизации и мобильность.
Рис. 9. Результаты ультразвукового контроля пластины.
Шерография
Шерография, (от англ. Shearography, shear — сдвиг), или сдвиговая спекл-интерферометрия — это разновидность интерферометрических методов неразрушающего контроля (методов дефектоскопии), с помощью которой внутренние разрушения или дефекты компонентов могут быть определены посредством измерения и анализа поверхностных деформаций. Принцип работы шерографии показан на рисунке 10. Деформации образуются как ответная реакция внутренней структуры на некоторую внешнюю незначительную нагрузку. Совмещая показываемые изображения объекта в ненагруженном состоянии с изображением, взятым в нагруженном состоянии, можно определить изменение любой заданной точки изображения. Таким образом, даже сравнительно невысокая нагрузка компонента приводит к однозначным результатам измерений при проведении неразрушающего контроля объекта.
В процедуру шерографической дефектоскопии на аппаратном уровне заложены две основополагающие составляющие, это получение опорного изображения поверхности инспектируемого объекта в ненагруженном и нагруженном состоянии. Специальный алгоритм программного обеспечения автоматически вычитает изображение одно из другого, получая результирующую картину.
Тепловое и/или вакуумное нагружение являются типичными видами испытательной нагрузки. Оптимальный тип нагрузки зависит от структуры и материала компонента, а также от размера, положения (глубины залегания) и типа дефектов. Тип нагрузки по этой причине должен быть определен заранее в процессе проведения ряда экспериментов с использованием образцового объекта (т.е. с аналогичной структурой). Затем нагрузка может быть оптимизирована по интенсивности и длительности. Как и для большинства методов НК предварительными работами при серийной эксплуатации данной системы является формирование базы данных с типовыми дефектами, что значительно повысит эффективность определения конкретного дефекта. Данная база может быть сформирована на образцах с заложенными дефектами.
Поверхность объекта испытания засвечивается лазерным излучением и отражается на CCD-камеру, оснащённую, так называемой, «сдвигающей оптикой». Эта «сдвигающая оптика» проецирует изображение объекта на матрицу камеры дважды и каждая точка объекта, таким образом, является дважды отображаемой на CDD-чипе (CDD-матрице). Когда объект испытания деформируется под нагрузкой, лазерное излучение, отражённое каждым участком поверхности, также изменяется, что регистрируется приемником. Метод может применяться как в ручном, так и автоматизированном варианте (рис. 11). При этом контролю подвергается определённая зона объекта, что увеличивает скорость исследования.
Система также даёт возможность инспектирования видимых повреждений и поиск дефектов (с обязательным определением их параметров - размера, оценки значимости) в более глубоких слоях, невидимых человеческому глазу. (рис.12) [8]
Рис. 10. Принцип работы интерферометрических методов контроля.
А Б
Рис. 11. А – мобильный шерограф, Б – автоматизированный комплекс для шерографии
Рис.12. Результат измерения поверхностной деформации
Термография
Тепловизионное обследование (рис. 13) включает в себя все методы, при которых производится измерение температуры на поверхности объекта контроля. В основу этого метода положен анализ признаков наличия дефектов по изменениям температурных полей с использованием инфракрасной техники (тепловизор или пирометр). Термография фиксирует изменения температуры на уровне 0,01 °С. Поэтому даже при механическом нагружении фиксируются места концентрации энергии (рис. 14), где может происходить пластическая деформация с выделением тепла. Зафиксировав температурное поле на поверхности, можно определить местоположение концентратора энергии относительно поверхности изделия [7].
Рис. 13. Пример использования термографии при контроле обшивки.
Рис. 14. Примеры выходных изображений.
Дата добавления: 2018-06-01; просмотров: 1770; Мы поможем в написании вашей работы! |
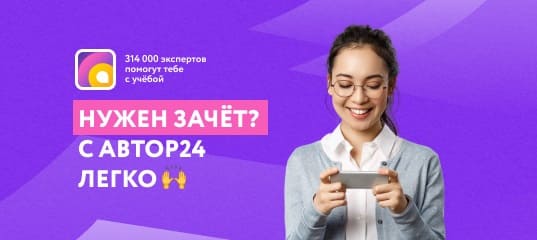
Мы поможем в написании ваших работ!