Основные понятия и определения (по ГОСТ 2601).
Сварка — получение неразъемных соединений посредством установления межатомных связей между соединяемыми частями при их нагревании и (или) пластическом деформировании.
Свариваемость — свойство металла или сочетания металлов образовывать при установленной технологии сварки соединение, отвечающее требованиям обусловленных конструкцией и эксплуатацией изделия.
Сварка на подъем — сварка плавлением в наклонном положении, при которой сварочная ванна перемещается снизу вверх.
Сварка на спуск — сварка плавлением в наклонном положении, при которой сварочная ванна перемещается сверху вниз.
Сварка неповоротных стыков — сварка по замкнутому контуру во всех пространственных положениях, при которых объект сварки неподвижен.
Сварное соединение — неразъемное соединение, выполненное сваркой.
Сварной шов — участок сварного соединения, образовавшийся в результате кристаллизации расплавленного металла или в результате пластической деформации при сварке давлением или сочетанием кристаллизации и деформации.
Подварочный шов — меньшая часть двухстороннего шва, выполняемая предварительно для предотвращения прожогов при последующей сварке, ими накладываемая в последнюю очередь в корень шва.
Прихватка — короткий сварной шов для фиксации взаимного расположения подлежащих сварке деталей.
Валик — металл сварного шва, наплавленный или переплавленный в один проход.
|
|
Слой сварного металла — часть металла сварного шва, которая состоит из одного или нескольких валиков, располагающихся на одном уровне поперечного сечения шва.
Корень шва — часть сварного шва, наиболее удаленного от его лицевой поверхности.
Особенности сварного шва и его структуры.
Основной металл — металл подвергающейся сварке и принадлежащий соединяемым частям.
Присадочный металл — металл для введения в сварочную ванну в дополнение к расплавленному основному металлу.
Наплавленный металл — переплавленный присадочный металл, введенный в сварочную ванну или наплавленный на основной металл.
Металл шва — сплав, образованный расплавленным основным и наплавленным металлом или только переплавленным основным металлом.
Сварочная ванна — часть металла свариваемого шва, находящаяся при сварке плавлением в жидком состоянии.
Глубина проплавления — наибольшая глубина расплавления основного металла в сечении шва или наплавленного валика.
Провар — сплошная металлическая связь между свариваемыми поверхностями основного металла, слоями и валиками сварного шва.
Зона сплавления при сварке — зона частично оплавившихся зерен на границе основного металла и металла шва.
|
|
Зона термического влияния (околошовная зона) при сварке — участок основного металла, не подвергшийся расплавлению, структура и свойства которого изменились в результате нагрева при сварке или наплавке.
Угар при сварке — потери металла на испарение и окисление при сварке.
Сварочные материалы.
Основные — сварочная проволока, порошки, сварочные электроды.
Вспомогательные — флюсы, газы.
Сварочная проволока: (применение: 1) при полуавтоматической и автоматической сварке в среде СО2 и под слоем флюса и как присадочный материал; 2) присадочные прутки).
Стандарт по ГОСТ 2246 предусматривает 77 марок сварочной проволоки холоднотянутой Æ0.2 – 12 мм. Ее делят на три основные группы:
– низкоуглеродистую (Св–08, Св–08А, Св–08ГС и др.);
– легированную (Св–18ХГС; Св–10ХМ и др.);
– высоколегированную (Св–10Х20Н15 и др.).
Обозначение:
3- | Св- | 08 | ГС | А | О |
1 | 2 | 3 | 4 | 5 | 6 |
1 – диаметр проволоки (3 мм);
2 – сварочная проволока (Св);
3 – содержание углерода;
4 – химический состав (Г – марганец, С – кремний);
5 – качественная проволока, менее 0.03% S и F (А);
6 – омедненная поверхность (О).
Особенности — а) содержание углерода С не превышает 0.12–015% (за редким исключением), что снижает склонность металла шва к пористости и образованию закалочных структур;
|
|
б) содержание кремния Si£0.03% — так как превышение приводит к созданию пор при сварке;
в) предотвращение пористости швов Mn/Si=1.4/1.6.
Сварочные электроды:
а) неплавящиеся (угольные, графитовые, вольфрамовые);
б) плавящиеся.
Классификация плавящихся электродов
I. По назначению:
На 5 классов:
1) для сварки углеродистой и низколегированной стали с sв£600 МПа;
2) легированной конструкционной стали с sв³600 МПа;
3) легированных жаропрочных сталей;
4) высоколегированных сталей с особыми свойствами;
5) для наплавки.
Электроды делят на типы. Тип электрода Э42 (sв=420 МПа) — учитывает предел прочности сварного соединения наплавленного металла. Каждый тип делится на несколько марок. Марка — это его промышленное обозначение, характеризующее стержень и покрытие.
II. По виду покрытия:
1. По толщине покрытия:
– тонкие (стабилизирующие или ионизирующие);
– толстые (качественные).
Свойства и назначение:
Назначение тонкого покрытия — обеспечить возбуждение дуги и стабилизировать ее горение (содержат Ca, K, Na и Ba и др.) с СаСО3.
|
|
Недостаток: не создает защиты и происходит окисление и азотирование ванны — для неответственных швов (меловое покрытие).
Толстые:
1. Обеспечивает устойчивое горение дуги.
2. Защищает расплавленные металл от О2 и N воздуха.
3. Раскисляет окислы и удаляет в шлак.
4. Изменяет состав металл вводом в него легирующих элементов (феррохром, ферросилиций).
5. Удаляет S и Р из шва (т.е. оно содержит весь комплекс химических соединений).
III. По химическому составу:
а) кислым (А);
б) основным (Б);
в) Рутиловым (Р);
г) целлюлозным (органическим) покрытием (Ц).
Электроды с кислым покрытием А
Особенности:
1. Наплавленный металл не склонен к образованию пор при наличие на кромках окалины или ржавчины, или при удлинении дуги.
2. При повышенном содержании серы в основном металле проявляется склонность металла шва к образованию горячих трещин.
3. Допускается сварка во всех пространственных положениях.
4. Высокая токсичность.
Назначение:
Сварка в монтажных условиях (или в хорошо проветриваемых помещениях) неответственных конструкций из низколегированных сталей.
Электроды с основным видом покрытия Б
Особенности:
1. Позволяет легировать металл различными элементами.
2. Наличие большого количества соединений кальция, хорошо связывающие серу и фосфор в шлак, обеспечивая:
а) высокую чистоту наплавленного металла;
б) повышенные пластические свойства при низких температурах;
в) легирование Mn и Si придает высокую прочность.
3. Наплавленный металл мало склонен к старению (упрочнению) и стоек против образования кристаллизационных трещин (горячих).
4. Наличие масла, окалины или ржавчины, а также увеличение длины дуги приводит к образованию пор в металле.
5. Необходимо: а) строго выполнять требования по подготовке изделия и электродов к работе;
б) выдерживать технологический режим процесса.
Назначение:
1. Рекомендуется для сварки особо ответственных конструкций (магистральные трубопроводы, резервуары и т.д.), но с учетом требований.
2. Для поворотных и неповоротных стыков.
Электроды с рутиловым видом покрытия Р
Особенности:
1. Склонность металла шва к трещинам такая же, как и у А.
2. В металле шва могут появляться поры при колебании длины дуги, при окислении и загрязнении поверхности.
3. Остальное близко к Б.
Назначение:
Для сварки металлоконструкций и трубопроводов из малоуглеродистых сталей.
Электроды с целлюлозным покрытием Ц
Особенности:
1. Высокая склонность к образованию "газового дутья" и боле глубокого проплавления металла.
2. Свойства наплавленного металла близки к рутиловым.
3. Происходит легкое отделение шлака от основного металла.
4. Высокий коэффициент наплавки и возможность сварки сверху вниз (на спуск) при соединении неповоротных стыков трубопроводов. Следовательно — возможность повышения производительности сварочно–монтажных работ.
5. Обмазка электродов (покрытие) обладает повышенной гигроскопичностью, но и не допускает перегрева как в процессе сушки, так и при сварке (обязателен "горячий проход.
6. Число слоев больше чем у Б.
Назначение:
Для неповоротных стыков.
Подготовка электродов к сварке
Особенность электродов — содержатся в покрытии гигроскопические соединения (способные натягивать влагу).
Область применения: Сварка при монтаже в любых пространственных положениях. Сварка неповоротных стыков трубопроводов.
Факторы, влияющие на увлажнение покрытия
1. Тип упаковки и способ хранения электродов.
2. Влажность воздуха.
3. Температура окружающей среды.
4. Время пребывания на воздухе или во влажном помещении.
Контроль качества по ГОСТ 9466 не должны разрушаться при падении на стальную плиту с высоты 1 м — для Æ<4мм, с 0.5 м — для Æ 4 мм и более.
Причины прокаливания электродов
1. Водород из влаги в шве приводит к пористости соединений и к образованию холодных трещин.
2. Уменьшается адгезия (связь) покрытия со стержнем (возможны сколы) и понижение свойств при сварке (исчезновение дуги).
3. При отсыревании в целлюлозных покрытиях — происходят необратимые структурные изменения — ухудшающие технологические свойства электродов.
Особенности подготовки (прокалки)
( данные ориентировочные)
1. Запрещается хранение электродов на монтажной площадке в раскрытых пачках более 4 часов.
2. Непосредственно перед выдачей — прокалка:
для Б — 350–400°С´1ч (если Б хранят при t=135–150°С, то прокалка не нужна);
Р — 180–200°С´1ч;
Ц — 80–100°С´1ч.
3. Просушивание в специальных электропечах, что исключает непосредственное воздействие пламени на покрытие.
Хранение — при t³+15°С в условиях предохранения от увлажнения, загрязнения и механического повреждения.
4. Ц — не перегревать.
Защитные газы
Защитные газы: аргон, гелий, углекислый газ или их смесь.
Особенности применения:
Углекислый газ: для сварки в монтажных условиях соединений труб и листов из углеродистых и низколегированных сталей.
Углекислый газ (двуокись углерода газообразная и и жидкая ГОСТ 8050) — бесцветный с едва ощутимым запахом. При испарении 1 кг. жидкой кислоты выделяется 509 л газа. Хранится в стальных баллонах под давление 5–6 МПа, баллон 40 л. — 25 кг. углекислоты.
Требования:
Запрещено содержание минерального масла, воды и т.д.
Причина: повышенное содержание паров приведет к образованию пор в швах и понижению пластических свойств.
Метод решения:
1. Опрокидывание баллона и удаление через вентиль.
2. Пропускание через влагоотделитель (осущитель) (силикагель и т.д.).
Аргон, гелий — для сварки алюминия и его сплавов, для сварки высоколегированных или жаропрочных сталей.
Аргон (по ГОСТ10157).
Химически не взаимодействует с металлом.
3 сорта: высший — 99,99% (остальное примеси О2, N и влага);
первый — 99,98% (остальное примеси О2, N и влага);
второй — 99,95% (остальное примеси О2, N и влага).
Особенности применения:
Высший сорт — для сварки очень активных и редких металлов (Ti, Nb, циркона) и особо ответственных деталей.
Первый сорт — для сварки сплавов на основе Al, Mg.
Второй сорт — для сварки сплавов на основе алюминия, легированных сталей и нержавеющих, жаропрочных сталей.
Хранят в баллонах Р=14,7 МПа.
Газы (маркировка и окрас баллонов) по «Правилам устройства и безопасной эксплуатации сосудов, работающих под давлением »
Таблица 10 - Основные виды применяемых газов
Газ | Окраска баллона | Текст | Цвет надписи | Цвет полосы |
Аргон сырой | Черная | Аргон сырой | Белый | Белая |
Аргон технический | Черная | Аргон технический | Синий | Синяя |
Аргон чистый | Серая | Аргон чистый | Зелёный | Зелёная |
Ацетилен | Белая | Ацетилен | Красный | — |
Бутан | Красная | Бутан | Белый | — |
Кислород | Голубая | Кислород | Черный | — |
Углекислота | Черная | Углекислота | Желтый | — |
Таблица 11 – Некоторые дефекты сварных швов (причины, методы контроля, способы устранения)
Название дефекта | Причины возникновения | Методы контроля | Способы устранения |
1 | 2 | 3 | 4 |
Внешние дефекты | |||
Отклонения от ширины и высоты шва | 1. Неравномерный зазор между кромками свариваемых деталей. 2. Неравномерное передвижение электрода или горелки и присадочной проволоки вдоль шва. 3. Несоблюдение установленного режима сварки. 4. Некачественное электродное покрытие. | 1. Внешний осмотр. 2. Измерение шаблонами и обычным инструментом. | Зачистка с подваркой шва и срубанием излишка металла. |
Грубая чешуйчатость шва и наплывы | 1. Низкое качество электродов. 2. Неумение манипулировать электродом или горелкой. | Внешний осмотр. | Срубание или вырезка наплыва, проварка непроваров. Заварка дефектного участка шва. |
Наружные трещины | 1. Напряжения, возникающие в металле вследствие неравномерного нагрева, охлаждения, садки. 2. Свойство высокоуглеродистых и легированных сталей подвергаться закалке при охлаждении после сварки. 3. Повышенное содержание вредных примесей. | Внешний осмотр. | Вырубка и последующая заварка дефектного участка. |
Подрезы | 1. Применение чрезмерно большого сварочного тока. 2. Сварка длинной дугой. 3. Повышенная мощность горелки. | Внешний осмотр. | Зачистка и заварка дефектного участка. |
Незаплавленные углубления (кратеры), остатки шлака и неровная поверхность | Низкая квалификация сварщика или небрежное выполнение сварки. | Внешний осмотр. | Тщательное заплавление кратера шва. Вырубка до основного металла и заварка вновь. |
Прожог | 1. Большая сила сварочного тока. 2. Малая скорость сварки. 3. Большой зазор. 4. Малое притупление кромок. | Внешний осмотр. | Зачистка и заварка дефектного участка. |
Деформация сварных конструкций | Неправильная последовательность сварки. | Внешний осмотр и обмер конструкций. | Механическая правка, тепловая правка. |
Внутренние дефекты | |||
Пористость металла | 1. Несоответствие химического состава металла электрода или присадочного прутка. 2. Влажное покрытие. 3. Окалина и ржавчина на кромках свариваемого металла. | 1. Испытание давлением водой или сжатым воздухом. 2.Просвечивание рентгеновскими или гамма–лучами. | Вырубка пористых участков до основного металла и последующая заварка. |
Шлаковые включения | 1. Неудовлетворительная очистка кромок. 2. Неумение манипулировать электродом. 3. Сварка длинной дугой. 4. Сварка окислительным пламенем. | 1.Магнитографический контроль. 2. Просвечивание рентгеновскими или гамма–лучами. | Вырубка дефектного участка и последующая заварка. |
Непровар кромки. Непровар притуплений Непровар сечения шва | 1. Сварка длинной дугой. 2. Недостаточная сила сварочного тока. 3. Большая скорость перемещения электрода или горелки. 4. Малый угол скоса или большое притупление. 5. Малая величина зазора. 6. Чрезмерно большой диаметр электрода. 7. Затекание шлака в зазор между свариваемыми кромками. 8. Магнитное дутье при сварке на постоянном токе. 9. Неправильный выбор полярности для данной марки электрода. 10. Неудовлетворительная очистка от ржавчины, масла, окалины и других загрязнений. | 1.Магнитографический контроль. 2.Ультразвуковой контроль. 3.Просвечивание рентгеновскими или гамма–лучами. | Вырубка дефектного участка и последующая заварка. |
Перегрев и пережог металла | 1. Чрезмерно большая сила сварочного тока. 2. Слишком медленное перемещение электрода. 3. Избыток кислорода в пламени горелки. | 1. Внешний осмотр. 2. Осмотр микрошлифов сварного соединения. | Устранение перегрева термической обработкой. Удаление пережженных участков и последующая заварка. |
Внутренние трещины: а) в металле шва, в зоне термического воздействия, в основном металле; б) продольные и поперечные; в) холодные и горячие. | 1. Напряжения, возникающие в металле вследствие неравномерного нагрева, охлаждения, садки. 2. Свойство высокоуглеродистых и легированных сталей подвергаться закалке при охлаждении после сварки. 3. Повышенное содержание вредных примесей. | 1.Рентгеновское и гамма-просвечивание. 2.Ультразвуковая дефектоскопия. 3.Магнитные способы контроля. 4.Металлографические методы исследования. | Вырубка дефектного участка и последующая заварка. |
НЕРАЗРУШАЮЩИЕ И РАЗРУШАЮЩИЕ МЕТОДЫ КОНТРОЛЯ МЕТАЛЛА И СВАРНЫХ ШВОВ И СВАРНЫХ СОЕДИНЕННИЙ
В настоящее время используются следующие методы:
1) внешним осмотром и измерениями;
2) ультразвуковой дефектоскопией;
3) радиографией (рентгено-, гаммаграфированием и др.);
4) механическими испытаниями;
5) металлографическим исследованием;
6) испытанием на стойкость против межкристаллитной коррозии;
7) гидравлическим испытанием;
8) пневматиче6ским испытанием;
9) другими методами (магнитографией, цветной дефектоскопией, стилоскопированием, замером твердости, акустической эмиссией, определением в металле шва ферритной фазы и др.), если таковые предусмотрены технической документацией.
Все вышеперечисленные методы контроля можно разделить на две группы:
1) разрушающие методы контроля (с вырезкой образцов для испытания).
- механические испытания (статическое растяжение, статический изгиб, ударный изгиб);
- металлографические исследования (макро- и микрошлифы, испытания на стойкость против МКК).
2) неразрушающие методы контроля.
- УЗТ, УЗД, радиография, цветная и магнитная дефектоскопия, акустическая эмиссия, измерение поверхностной твердости (дюраметрический метод определения мехсвойств), ГИ;
По ГОСТ 18353-82 МНК классифицируют на виды: акустический, магнитный, оптический, проникающими веществами, радиационный, волновой, тепловой, электрический и электромагнитный.
Контроль сварных соединений и швов сосудов, работающих под давлением (содержание контроля качества, виды недопустимых дефектов)
Контроль сварных соединений и швов сосудов, работающих под давлением, включает в себя:
1) визуальный осмотр,
2) испытания на твердость,
3) дефектоскопия,
4) микроструктурные исследования,
5) определение механических характеристик металла.
6) необходимость проведения работ по 4 и 5 пунктам определяется на основании результатов 1-3.
Оценку качества сварных соединений проводят по следующим пунктам:
1. В сварных соединениях сосудов и их элементов не допускаются следующие дефекты: трещины всех видов и направлений, расположенные в металле шва, по линии сплавления и в околошовной зоне основного металла, в том числе микротрещины, выявляемые при микрообследовании контрольного образца;
- непровары (несплавления) в сварных швах, расположенные в корне шва или по сечению сварного соединения (между отдельными валиками и слоями шва и между основным металлом и металлом шва);
- порезы основного металла, поры, шлаковые и другие включения, размеры которых превышают допустимые значения, указанные в ТНПА;
- наплывы (натеки);
- незаваренные кратеры и прожоги;
- свищи;
- смещение кромок свыше норм, предусмотренных Правилами устройства и безопасной эксплуатации сосудов, работающих под давлением;
- смещение основного и плакирующего слоев сварных соединений двухслойных сталей выше норм, предусмотренными Правилами устройства и безопасной эксплуатации сосудов, работающих под давлением.
2. Качество сварных соединений считается неудовлетворительным, если в них при любом виде контроля будут обнаружены внутренние или наружные дефекты, выходящие за пределы норм, установленными настоящими правилами и техническими условиями.
3. Дефекты, обнаруженные в процессе изготовления, должны быть устранены с последующим контролем исправленных участков. Методы и качество исправления дефектов должны обеспечивать необходимую надежность и безопасность работы сосуда.
4. Возможность допущения местных непроваров в сварных соединениях сосудов оговаривается в КД, согласованной с органом технадзора.
5. При определении класса дефектности сварного соединения следует руководствоваться действующими ТНПА.
Дата добавления: 2018-06-01; просмотров: 258; Мы поможем в написании вашей работы! |
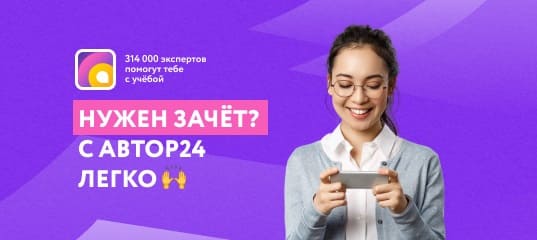
Мы поможем в написании ваших работ!