КОНЦЕНТРАТОРЫ НАПРЯЖЕНИЙ В КОНСТРУКЦИЯХ
Факультет повышения квалификации и переподготовки руководящих
работников и специалистов инженерного профиля ИПК УО "ПГУ"
Подразделение переподготовки и повышения квалификации
по специальности «Химическая технология производства
и переработки органических материалов»
МЕТОДИЧЕСКИЕ УКАЗАНИЯ
для слушателей курсов
повышения квалификации специалистов,
на предприятии
НОВОПОЛОЦК 2007
Надежность оборудования потенциально опасных производств
Надежность - свойство объекта выполнять заданные функции, сохраняя во времени значения установленных эксплуатационных показателей в заданных пределах, соответствующих заданным режимам и условиям использования, технического обслуживания, ремонтов, хранения и транспортирования (ГОСТ "Надежность в технике. Термины и определения").
В зависимости от назначения объекта и условий его эксплуатации надежность включает:
1) безотказность;
2) долговечность;
3) ремонтопригодность
в отдельности или сочетание этих свойств.
Безотказность - свойство объекта непрерывно сохранять работоспособность в течение некоторого времени или некоторой наработки.
Долговечность- свойство объекта сохранять работоспособность до наступления предельного состояния при установленной системе технического обслуживания и ремонтов.
Ремонтопригодность - свойство объекта, заключающееся в приспособленности к предупреждению и обнаружению причин возникновения его отказов, повреждений и устранению их последствий путем проведения ремонтов и технического обслуживания.
|
|
В каждый определенный момент времени объект может находиться в работоспособном, неработоспособном и предельном состояниях.
Объект работоспособен, если он выполняет свои функции, а значения всех его основных эксплуатационных характеристик соответствуют нормативно-технической документации. При несоблюдении этих условий объект неработоспособен.
Предельным называют такое состояние объекта, при котором возникает необходимость во временном или окончательном прекращении применения объекта по назначению. Переход объекта из работоспособного состояния в неработоспособное называют отказом, а переход в предельное состояние – исчерпанием ресурса.
Критерии отказа – это совокупность признаков, характеризующих неработоспособное состояние объекта, при котором использование объекта по назначению должно быть прекращено и он должен быть отправлен в ремонт или списан.
В соответствии с требованиями ГОСТ 27.002-89 и ГОСТ 27.003-90 критерии отказов и предельных состояний устанавливаются индивидуально для каждого вида объекта техническими условиями или стандартами.
|
|
ОСНОВНЫЕ ТРЕБОВАНИЯ ПРЕДЪЯВЛЯЕМЫЕ К КОНСТРУКЦИОННЫМ МАТЕРИАЛАМ ДЛЯ НЕФТЕПЕРЕРАБАТЫВАЮЩЕЙ ОТРАСЛИ С ПОЗИЦИИ НАДЕЖНОСТИ.
Для материалов нефтехимического оборудования, аккумулирующих большое количество упругой энергии (сжатого газа), наряду с пластичностью и вязкостью особое значение приобретает и показатель прочности. При этом следует отметить, что, как правило, пластичность, трещиностойкость и сопротивление хрупкому разрушению стали снижаются с повышением ее прочности.
Однако и для нефтехимического оборудования не стоит забывать про возможность возникновения циклических нагрузок. Циклические нагрузки в большинстве случаев приводят к образованию усталостных трещин у концентраторов напряжений, которые в конечном итоге могут привести к разрушению оборудования.
Сопротивление материала зарождению трещины определяется способностью металла и сварных соединений к локальной пластической деформации в концентраторе напряжений.
Сопротивление стали развитию трещины, зависит от вязкости стали. Разрушения по телу металла чаще всего происходят в сталях с недостаточным уровнем вязких свойств.
|
|
Дополнительная особенность. Испытания, максимально гарантирующие отсутствие хрупкого разрушения материалов нефтехимического оборудования, а также его хладостойкость являются испытания на ударную вязкость полнотолщинных образцов – образцов ДВТТ (DWTT). Проведение именно указанных испытаний следует указывать в требованиях проекта, что в последствии должно отражаться в сертификате качества на трубы.
Таким образом, надежность и долговечность нефтехимического оборудования в значительной мере определяются уровнем механических свойств и качеством материала.
Под механическими свойствами материала подразумеваются, прежде всего, прочность и вязкопластические характеристики стали.
Под качеством стали для нефтехимического оборудования целесообразно понимать однородность металла по объему и отсутствие поверхностных дефектов, что определяется, в частности, химическим составом, содержанием вредных примесей и неметаллических включений, а также технологией производства металла. Только в этом случае механические свойства стали могут характеризовать пригодность и надежность материала для нефтехимического оборудования.
В общем случае требования к сталям для нефтехимического оборудования можно сформулировать следующим образом:
|
|
- по механическим свойствам - повышенный уровень предела текучести, относительного удлинения, ударной вязкости при средних значениях предела прочности;
- по химическому составу – сталь должна содержать такие элементы, как ниобий, ванадий, титан, алюминий; содержание углерода, марганца, серы, фосфора должно быть минимальным.
Указанные требования могут быть реализованы следующими технологическими приемами: выплавка стали в конвертере или электропечи, внепечная обработка, прокатка в регулируемых интервалах температур, в частности при пониженных температурах и с ускоренным охлаждением.
МЕХАНИЧЕСКИЕ СВОЙСТВА КОНСТРУКЦИОННЫХ МАТЕРИАЛОВ
Основными механическими свойствами являются прочность, пластичность, твердость. Зная механические свойства, конструктор обоснованно выбирает соответствующий материал, обеспечивающий надежность и долговечность конструкций при их минимальной массе.
Механические свойства определяют поведение материала при деформации и разрушении от действия внешних нагрузок.
В зависимости от условий нагружения механические свойства могут определяться при:
1. статическом нагружении – нагрузка на образец возрастает медленно и плавно.
2. динамическом нагружении – нагрузка возрастает с большой скоростью, имеет ударный характер.
3. повторно, переменном или циклическим нагружении – нагрузка в процессе испытания многократно изменяется по величине или по величине и направлению.
Для получения сопоставимых результатов образцы и методика проведения механических испытаний регламентированы ГОСТами.
При статическом испытании на растяжение: ГОСТ 1497-90 получают характеристики прочности и пластичности.
Прочность – способность материала сопротивляться деформациям и разрушению.
Испытания проводятся на специальных машинах, которые записывают диаграмму растяжения, выражающую зависимость удлинения образца (мм) от действующей нагрузки Р, т.е.
.
Но для получения данных по механическим свойствам перестраивают: зависимость относительного удлинения Δl от напряжения σ
Рис. 1. Диаграмма растяжения: а – абсолютная, б – относительная; в – схема определения условного предела текучести
Проанализируем процессы, которые происходят в материале образца при увеличении нагрузки.
Участок оа на диаграмме соответствует упругой деформации материала, когда соблюдается закон Гука. Напряжение, соответствующее упругой предельной деформации в точке а, называется пределом пропорциональности.
Предел пропорциональности ( ) – максимальное напряжение, до которого сохраняется линейная зависимость между деформацией и напряжением.
При напряжениях выше предела пропорциональности происходит равномерная пластическая деформация (удлинение или сужение сечения).
Каждому напряжению соответствует остаточное удлинение, которое получаем проведением из соответствующей точки диаграммы растяжения линии параллельной оа.
Так как практически невозможно установить точку перехода в неупругое состояние, то устанавливают условный предел упругости, – максимальное напряжение, до которого образец получает только упругую деформацию. Считают напряжение, при котором остаточная деформация очень мала (0,005…0,05%).
В обозначении указывается значение остаточной деформации .
Предел текучести характеризует сопротивление материала небольшим пластическим деформациям.
В зависимости от природы материала используют физический или условный предел текучести.
Физический предел текучести – это напряжение, при котором происходит увеличение деформации при постоянной нагрузке (наличие горизонтальной площадки на диаграмме растяжения). Используется для очень пластичных материалов.
Но основная часть металлов и сплавов не имеет площадки текучести.
Условный предел текучести – это напряжение вызывающее остаточную деформацию
Физический или условный предел текучести являются важными расчетными характеристиками материала. Действующие в детали напряжения должны быть ниже предела текучести.
Равномерная по всему объему пластичная деформация продолжается до значения предела прочности.
В точке в в наиболее слабом месте начинает образовываться шейка – сильное местное утомление образца.
Предел прочности – напряжение, соответствующее максимальной нагрузке, которую выдерживает образец до разрушения (временное сопротивление разрыву).
Образование шейки характерно для пластичных материалов, которые имеют диаграмму растяжения с максимумом.
Предел прочности характеризует прочность как сопротивления значительной равномерной пластичной деформации. За точкой b, вследствие развития шейки, нагрузка падает и в точке c происходит разрушение.
Истинное сопротивление разрушению – это максимальное напряжение, которое выдерживает материал в момент, предшествующий разрушению образца (рис. 2.).
Истинное сопротивление разрушению значительно больше предела прочности, так как оно определяется относительно конечной площади поперечного сечения образца.
Рис. 2. Истинная диаграмма растяжения
- конечная площадь поперечного сечения образца.
Истинные напряжения определяют как отношение нагрузки к площади поперечного сечения в данный момент времени.
Si=Pi/Fi
При испытании на растяжение определяются и характеристики пластичности.
Пластичность –– способность материала к пластической деформации, т.е. способность получать остаточное изменение формы и размеров без нарушения сплошности.
Это свойство используют при обработке металлов давлением.
Характеристики:
относительное удлинения.
и
– начальная и конечная длина образца.
– абсолютное удлинение образца, определяется измерением образца после разрыва.
относительное сужение
- начальная площадь поперечного сечения
-площадь поперечного сечения в шейке после разрыва.
Относительное сужение более точно характеризует пластичность и служит технологической характеристикой при листовой штамповке.
Пластичные материалы более надежны в работе, т.к. для них меньше вероятность опасного хрупкого разрушения.
Твердость – это сопротивление материала проникновению в его поверхность стандартного тела (индентора), не деформирующегося при испытании.
Широкое распространение объясняется тем, что не требуются специальные образцы.
Это неразрушающий метод контроля. Основной метод оценки качества термической обработке изделия. О твердости судят либо по глубине проникновения индентора (метод Роквелла), либо по величине отпечатка от вдавливания (методы Бринелля, Виккерса, микротвердости).
Во всех случаях происходит пластическая деформация материала. Чем больше сопротивление материала пластической деформации, тем выше твердость.
Наибольшее распространение получили методы Бринелля, Роквелла, Виккерса и микротвердости. Схемы испытаний представлены на рис. 7.1.
Рис. 3. Схемы определения твердости: а – по Бринеллю; б – по Роквеллу; в – по Виккерсу
Твердость по Бринеллю (ГОСТ 9012-79)
Испытание проводят на твердомере Бринелля (рис.3 а)
В качестве индентора используется стальной закаленный шарик диаметром D 2,5; 5; 10 мм, в зависимости от толщины изделия.
Нагрузка Р, в зависимости от диаметра шарика и измеряемой твердости: для термически обработанной стали и чугуна – , литой бронзы и латуни –
, алюминия и других очень мягких металлов –
.
Продолжительность выдержки τ: для стали и чугуна – 10 с, для латуни и бронзы – 30 с.
Полученный отпечаток измеряется в двух направлениях при помощи лупы Бринелля.
Твердость определяется как отношение приложенной нагрузки Р к сферической поверхности отпечатка F:
Стандартными условиями являются D = 10 мм; Р = 3000 кгс; τ= 10 с. В этом случае твердость по Бринеллю обозначается НВ 250, в других случаях указываются условия: НВ D / P /τ, НВ 5/ 250 /30 – 80.
Метод Роквелла ГОСТ 9013
Основан на вдавливании в поверхность наконечника под определенной нагрузкой (рис. 3 б)
Индентор для мягких материалов (до НВ 230) – стальной шарик диаметром 1/16” ( 1,6 мм), для более твердых материалов – конус алмазный.
Нагружение осуществляется в два этапа. Сначала прикладывается предварительная нагрузка (10 кгс) для плотного соприкосновения наконечника с образцом. Затем прикладывается основная нагрузка Р1, в течение некоторого времени действует общая рабочая нагрузка Р. После снятия основной нагрузки определяют значение твердости по глубине остаточного вдавливания наконечника h под нагрузкой
.
В зависимости от природы материала используют три шкалы твердости (табл. 1)
Таблица 1.Шкалы для определения твердости по Роквеллу
Метод Виккерса (ГОСТ 2999-85)
Твердость определяется по величине отпечатка (рис.3 в).
В качестве индентора используется алмазная четырехгранная пирамида с углом при вершине 136o.
Твердость рассчитывается как отношение приложенной нагрузки P к площади поверхности отпечатка F:
Нагрузка Р составляет 5…100 кгс. Диагональ отпечатка d измеряется при помощи микроскопа, установленного на приборе.
Преимущество данного способа в том, что можно измерять твердость любых материалов, тонкие изделия, поверхностные слои. Высокая точность и чувствительность метода.
Способ микротвердости (ГОСТ 9450-92) – для определения твердости отдельных структурных составляющих и фаз сплава, очень тонких поверхностных слоев (сотые доли миллиметра).
Аналогичен способу Виккерса. Индентор – пирамида меньших размеров, нагрузки при вдавливании Р составляют 5…500 гс
Метод царапания.
Алмазным конусом, пирамидой или шариком наносится царапина, которая является мерой. При нанесении царапин на другие материалы и сравнении их с мерой судят о твердости материала.
Можно нанести царапину шириной 10 мкм под действием определенной нагрузки. Наблюдают за величиной нагрузки, которая дает эту ширину.
Динамический метод (по Шору)
Шарик бросают на поверхность с заданной высоты, он отскакивает на определенную величину. Чем больше величина отскока, тем тверже материал.
В результате проведения динамических испытаний на ударный изгиб специальных образцов с надрезом оценивается вязкость материалов и устанавливается их склонность к переходу из вязкого состояния в хрупкое.
Вязкость – способность материала поглощать механическую энергию внешних сил за счет пластической деформации.
Является энергетической характеристикой материала, выражается в единицах работы Вязкость металлов и сплавов определяется их химическим составом, термической обработкой и другими внутренними факторами.
Также вязкость зависит от условий, в которых работает металл (температуры, скорости нагружения, наличия концентраторов напряжения).
Влияние температуры.
С повышением температуры вязкость увеличивается (см. рис. 4).
Предел текучести Sт существенно изменяется с изменением температуры, а сопротивление отрыву Sот не зависит от температуры. При температуре выше Тв предел текучести меньше сопротивления отрыву. При нагружении сначала имеет место пластическое деформирование, а потом – разрушение. Металл находится в вязком состоянии.
При температуре ниже Тн сопротивление отрыву меньше предела текучести. В этом случае металл разрушается без предварительной деформации, то есть находится в хрупком состоянии. Переход из вязкого состояния в хрупкое осуществляется в интервале температур
Хладоломкостью называется склонность металла к переходу в хрупкое состояние с понижением температуры.
Хладоломкими являются железо, вольфрам, цинк и другие металлы, имеющие объемноцентрированную кубическую и гексагональную плотноупакованную кристаллическую решетку.
Рис. 4. Влияние температуры на пластичное и хрупкое состояние
Способы оценки вязкости.
Ударная вязкость характеризует надежность материала, его способность сопротивляться хрупкому разрушению
Испытание проводят на образцах с надрезами определенной формы и размеров. Образец устанавливают на опорах копра надрезом в сторону, противоположную удару ножа маятника, который поднимают на определенную высоту (рис. 5)
Рис.5. Схема испытания на ударную вязкость: а – схема маятникового копра; б – стандартный образец с надрезом; в – виды концентраторов напряжений; г – зависимость вязкости от температуры
На разрушение образца затрачивается работа:
где: Р – вес маятника, Н – высота подъема маятника до удара, h – высота подъема маятника после удара.
Характеристикой вязкости является ударная вязкость (ан), - удельная работа разрушения.
где: F0 - площадь поперечного сечения в месте надреза.
ГОСТ 9454 – 78 ударную вязкость обозначает KCV. KCU. KCT. KC – символ ударной вязкости, третий символ показывает вид надреза: острый (V), с радиусом закругления (U), трещина (Т) (рис. 5 в)
Серийные испытания для оценки склонности металла к хладоломкости и определения критических порогов хладоломкости.
Испытывают серию образцов при различных температурах и строят кривые ударная вязкость – температура ( ан – Т) (рис. 5 г), определяя пороги хладоломкости.
Порог хладоломкости - температурный интервал изменения характера разрушения, является важным параметром конструкционной прочности. Чем ниже порог хладоломкости, тем менее чувствителен металл
– к концентраторам напряжений (резкие переходы, отверстия, риски),
– к скорости деформации.
Оценка вязкости по виду излома.
При вязком состоянии металла в изломе более 90 % волокон, за верхний порог хладоломкости Тв принимается температура, обеспечивающая такое состояние. При хрупком состоянии металла в изломе 10 % волокон, за нижний порог хладоломкости Тн принимается температура, обеспечивающая такое состояние. В технике за порог хладоломкости принимают температуру, при которой в изломе 50 % вязкой составляющей. Причем эта температура должна быть ниже температуры эксплуатации изделий не менее чем на 40oС.
Испытания на выностивость (ГОСТ 2860) дают характеристики усталостной прочности.
Усталость - разрушение материала при повторных знакопеременных напряжениях, величина которых не превышает предела текучести.
Усталостная прочность – способность материала сопротивляться усталости.
Процесс усталости состоит из трех этапов, соответствующие этим этапам зоны в изломе показаны на рис.6.
1 – образование трещины в наиболее нагруженной части сечения, которая подвергалась микродеформациям и получила максимальное упрочнение
2 – постепенное распространение трещины, гладкая притертая поверхность
3 – окончательное разрушение, зона “долома“, живое сечение уменьшается, а истинное напряжение увеличивается, пока не происходит разрушение хрупкое или вязкое
Рис 6. Схема зарождения и развития трещины при переменном изгибе круглого образца
Характеристики усталостной прочности определяются при циклических испытаниях “изгиб при вращении“. Схема представлена на рис. 7.
Рис. 7. Испытания на усталость (а), кривая усталости (б)
Основные характеристики:
Предел выносливости ( – при симметричном изменении нагрузки,
– при несимметричном изменении нагрузки) – максимальное напряжение, выдерживаемое материалом за произвольно большое число циклов нагружения N.
Ограниченный предел выносливости – максимальное напряжение, выдерживаемое материалом за определенное число циклов нагружения или время.
Живучесть – разность между числом циклов до полного разрушения и числом циклов до появления усталостной трещины.
КОНЦЕНТРАТОРЫ НАПРЯЖЕНИЙ В КОНСТРУКЦИЯХ
(виды и способы выявления)
Концентраторы напряжений можно разделить на две группы наружные и внутренние.
Наружными концентраторами напряжений являются чаще всего конструктивные элементы:
– отверстия;
– канавки;
– наружные элементы сварных швов;
– переходы разнотолщинных элементов и др.
Внутренними концентраторами напряжений являются чаще всего различные дефекты внутреннего строения металлов и сварных швов:
– структурная неоднородность;
– неметаллические включения
– трещины внутренние и наружные в том числи и микротрещины и др.
Кроме того, концентраторы напряжений можно разделить на явные (выявляемые визуально при внешнем осмотре) и скрытые (можно обнаружить только при помощи специальных инструментов или приборов).
Концентраторы напряжений в конструкции можно выявить при следующих видах работ:
– изучении технической документации;
– визуальном осмотре;
– толщинометрии элементов конструкции;
– испытании на твердость;
– дефектоскопии;
– микроструктурных исследованиях
Дата добавления: 2018-06-01; просмотров: 2082; Мы поможем в написании вашей работы! |
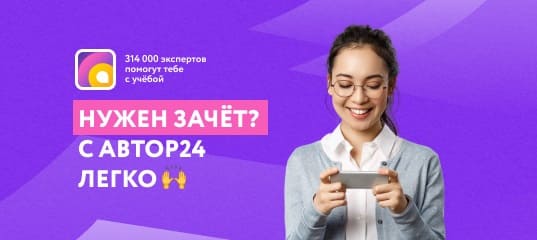
Мы поможем в написании ваших работ!