Подготовка к дальнему транспорту
И транспорт газа
Очистка газа от механических примесей осуществляется в сепараторах циклонного и объемного типов, осушка в адсорберах и абсорберах. Они производятся на УКПГ, головных сооружениях или на КС (компрессорных станциях) газопровода. Сепарационное оборудование служит для очистки газа от капельной влаги, углеводородного конденсата и механических примесей.
|
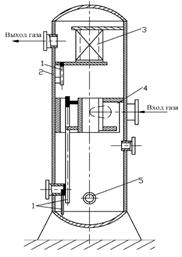
|
Рис. 3.1 «а» и «б»
Газосепараторы объемного и циклонного типов (соответственно)
«а» Вертикальный газовый «б» Циклонный
(объемный) сепаратор сепаратор
1 – дренажные трубки; 1 – корпус;
2 – корпус; 2 – выходная труба;
3 – жалюзийная насадка (каплеуловитель); 3 – винтовая камера;
4 – устройство для направления потока газа; 4 – сливной патрубок;
5 – патрубок (дренаж) для слива 5 – уравнительная
жидкости. трубка d = 25…38 мм.
Для газовых систем чаще всего используют вертикальные сепараторы объемного (рис. 3.1 «а») и циклонного (рис. 3.1 «б») типов. Штуцер для ввода газа в объемный сепаратор (рис. 3.1 «а») может быть вварен как для радиального, так и для тангенциального ввода в него газа. Жидкая фаза, в сепараторе пройдя каплеуловительную насадку 3 сливается по дренажной трубке 1, механические примеси и крупные капли сразу же осаждаются в нижней части корпуса аппарата 2. Накопившийся шлам (жидкость и механическая взвесь) в корпусе аппарата продуваются через патрубок 5.
|
|
В циклонный сепаратор газ подается в корпус 1 по тангенциальному трубопроводу через винтовую камеру 3. В месте разрыва выходной трубы 2 жидкость и механическая взвесь под действием центробежных сил отбрасывается к стенкам аппарата и по кольцевому пространству стекает в нижнюю его часть. Благодаря оригинальности конструкции циклонные сепараторы имеют большую производительность при небольших габаритных размерах.
Сепарация и осушка газа
Для тонкой осушки газа от влаги и тяжелых углеводородов используются колонные аппараты. Адсорберы и абсорберы используются в следующих технологических схемах подготовки газа: компрессорный, адсорбционный и абсорбционный, осуществляемых на головных сооружениях, иногда на УКПГ. Применяют и низкотемпературные сепараторы для вымораживания влаги.
Компрессионный метод (рис. 3.2) основан на различии давлений и температур конденсации отдельных компонентов смеси углеводородных газов, составляющих попутный преимущественно нефтяной газ. В этом случае исходный попутный газ после очистки в сепараторе 1 от взвешенных частиц нефти, влаги и пыли сжимается в компрессоре 2 до 20 атм. (2,0 МПа) и затем последовательно охлаждается в конденсаторах 3 и 5.
|
|
|
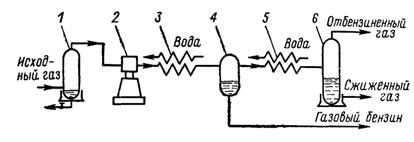
Рис. 3.2. Схема разделения углеводородов методом компрессии
В процессе первой стадии охлаждения из смеси конденсируются и собираются в сепараторе сырого бензина 4 наименее упругие пары пентана, в конденсаторе 5 конденсируются пары пропана и бутана. После разделения в сепараторе 6 сконденсированные пропан и бутан поступают в емкости сжиженного газа, а сохранившие газообразное состояние метан и этан по газопроводу направляется потребителю.
Адсорбционный метод основан на способности некоторых пористых тел (активированного угля, алюмогеля, перлита, силикагеля) и др. удерживать (адсорбировать) на поверхности пор тяжелые углеводороды и выделять их при последующем нагреве и увлажнении. Основным аппаратом адсорбционной установки (рис. 3.3) является адсорбер 1, заполненный например активированным углем. Очищенный исходный попутный газ проходит в адсорбере снизу вверх через слой угля и насыщает его поры тяжелыми углеводородами, а легкие углеводороды — метан и этан, не осевшие в порах угля, выходят из адсорбера в газопровод отбензиненного газа. По окончании насыщения угля углеводородами через адсорбер сверху вниз подается водяной пар, который, нагревая и увлажняя уголь, осуществляет десорбцию тяжелых углеводородов и уносит их в виде паров. Пары воды и углеводородов проходят через конденсатор 2 и поступают в сепаратор 3, в нижней части которого скапливается конденсат водяного пара, над ним – более легкий конденсат пентана, а в паровом пространстве – пары пропана и бутана. Через регуляторы уровня вода из сепаратора сбрасывается в канализацию, пентан – в емкости сырого бензина, а пары пропана и бутана поступают под купол газгольдера 4. По мере скопления в газгольдере пары пропана и бутана сжимаются компрессором 5 до 17–20 кгс/см2 (1,7-2,0 МПа) и после охлаждения в конденсаторе 6 накапливаются в виде конденсата в сепараторе сжиженного газа 7, а из него периодически перемещаются в сборные емкости.
|
|
Для восстановления адсорбционной активности угля его надо просушить и охладить. Для этого дутьевой вентилятор 8 нагнетает в адсорбер 1 выбрасываемые через свечу 10 горячий воздух, нагреваемый в калорифере 9, а затем подается холодный воздух, поступающий мимо калорифера. Непрерывность действия установки обеспечивается комплектованием групп адсорберов, по три в каждой. Это позволяет одновременно осуществлять в группе все основные операции: адсорбцию, десорбцию и регенерацию активных адсорбционных свойств угля или другого адсорбера.
|
|
Рис.3.3. Адсорбционная установка
1 – адсорбер 6 - теплообменник
2 – теплообменник 7 - сепаратор
3 – сепаратор 8 - насос
4 – газгольдер 9 - теплообменник
5 – компрессор 10 – факел или свеча
Абсорбционный (маслопоглотителъный) метод основан на способности масел или солярового топлива в холодном виде избирательно растворять в себе (абсорбировать) тяжелые углеводороды, а при нагревании выделять их обратно. Очищенный попутный нефтяной газ (рис. 3.4) поступает в нижнюю часть абсорбера 1, представляющего собой колонну с тарельчатыми насадками, в которой снизу вверх движется газ, а противотоком сверху вниз стекает по тарелкам масло. Конструкция тарелок обеспечивает хороший контакт газа с маслом, в результате чего масло растворяет основную массу тяжелых углеводородов. Легкие углеводороды поступают в верхнюю часть абсорбера и по газопроводу отбензиненного газа направляются к потребителю. Скапливающееся в нижней части абсорбера масло, насыщенное углеводородами, подается в подогреватель 2, затем десорбер 3. Выделяющиеся из нагретого масла тяжелые углеводороды поступают в компрессор 4, где сжимаются до 17–20 кгс/см2 (1,7-2,0 МПа). Охлаждаются они в две стадии – в конденсаторах 5 и 7. После первой стадии в сепараторе 6 сырого бензина накапливается жидкий пентан, а в сепараторе 8 – сжиженная пропан-бутановая фракция. Освободившееся от углеводородов нагретое масло из нижней части десорбера 3 насосом 9 перекачивается через холодильник 10 в верхнюю часть абсорбера 1 для повторения цикла.
Из рассмотренных методов в газобензиновом производстве наиболее распространен метод масляной абсорбции, отличающийся простотой установки, большой производительностью и достаточно высокой степенью извлечения тяжелых углеводородов из исходных газов.
|
Исходный газ |
|
Рис.3.4. Абсорбционный метод
1 – абсорбер 6 - сепаратор
2 – подогреватель 8 - сепаратор
3 – десорбер 9 - насос
4 – компрессор 10 - холодильник
5, 7 – конденсаторы
В абсорбер 1 снизу вверх подается исходный очищенный в сепараторах газ, проходит абсорбент стекающий через тарелки сверху вниз. Отбензиненный сухой газ из абсорбера 1 уходит в газопровод. Скопившееся масло из нижней части абсорбера подается в подогреватель 2, затем – в десорбер 3, где освобождаются от более тяжелых углеводородов и масла. Более легкая фракция проходит компрессор 4, где получает давление Р=17-20 атм. (1,7-2,0 МПа). Охлаждается эта фракция в 2 стадии, в конденсаторах 5 и 7. После 1-й стадии в сепараторе 6 сырого бензина накапливается жидкий пентан, а в
сепараторе 8 – сжиженная пропан-бутановая фракция. Освободившееся от тяжелых углеводородов нагретое масло из нижней части десорбера 3насосом 9 перекачивается через холодильник 10 в верхнюю часть абсорбера 1 для распыления в колонне (цикл работы повторяется).
Этот метод наиболее приемлем, так как осуществляется высокая степень отбензинивания газа и достигается высокая производительность.
Из жидких поглотителей используется диэтиленгликоль (С4Н10О3) или триэтиленгликоль (С6Н14О2). При нагреве сорбента влага из него удаляется и он возвращается в абсорбер 1.
Эффективнейшим способом удаления влаги является низкотемпературная сепарация, т.е. вымораживание влаги. Газ с Р=10МПа дросселируют и влагу и углеводородный конденсат при отрицательных температурах выпадают.
Смеси полученных углеводородов (пропана, пропилена, бутана, бутилена, небольших количеств этана и этилена), находятся при относительно небольших давлениях или при пониженных температурах в жидком состоянии, а при нормальных условиях - в газообразном состоянии, они составляют группу сжиженных углеводородных газов.
Технология разделения углеводородов по представленным технологическим схемам основана на различной упругости насыщения паров и на различии в давлениях конденсации отдельных компонентов смеси.
При изменениях температуры или давления, а также объема такой двухфазной системы (пар-жидкость) равновесие ее нарушается и жидкая фаза выпадает.
Например, при постоянстве температуры сжатие паровой фазы приводит к конденсации части паров, а при увеличении объема жидкость выпадает в сепараторе объемного или циклонного типа. В обоих случаях давление паровой фазы, соответствующее данной температуре, остается неизменным.
Очистка газа от сероводорода и СО2 выполняется с использованием жидких и твердых поглотителей. Осуществляется очистка щелочными растворами этаноломина или моноэтаноламина, которые при взаимодействии с Н2S и СO2 образуют нестойкие соединения. Реакции моноэтаноламина с Н2S и водного раствора моноэтаноламина с С02 протекают по следующим уравнениям:
(3.1)
Обе реакции обратимы т.к. при температурах 20-40°С они идут слева на право с поглощением Н2S и СO2, а с повышением температуры до 105°С и боле - с права налево, т.е. происходит регенерация этаноламина.
При очистке газа этаноламинами (см. схему рис. 3.5) неочищенный газ поступает по газопроводу 1, проходит через абсорбер 2 снизу вверх, контактирует с встречным потоком этаноламина, переливающегося через тарелки сверху вниз, освобождается от сероводорода и углекислого газа и через газопровод 3 уходит в магистральный газопровод.
![]() |
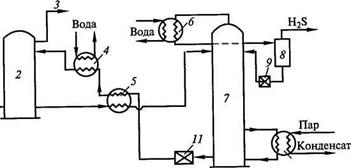
|
Рис. 3.5. Схема установки очистки газа от сероводорода:
1, 3-газопроводы; 2- абсорбер; 4, 6-холодильники; 5- теплообменник; 7- выпарная колонна; 8- сепаратор; 9, 11- насосы; 10- кипятильник
Раствор этаноламинов из нижней части абсорбера 2 насосом 11 подается в выпарную колонну 7 для регенерации которая происходит при 105 °С. Далее раствор охлаждается в теплообменнике 5 и холодильнике 4 и направляется в верхнюю часть абсорбера 2. Степень очистки при этом достигает 99 % и выше.
Основные достоинства рассмотренного способа очистки: достаточно высокая степень очистки, легкая регенерируемость раствора, незначительные потери реагента, компактность установки, небольшой расход воды и электроэнергии, возможность автоматизации процесса.
Очистка газа этим способом позволяет снизить Н2S и СО2 до приемлемой величины 2г на 100м3 газа.
Одоризация необходима для обнаружения утечек, т.к. газ не имеет запаха. Она осуществляется путем подачи в газ одоранта (этилмеркаптана
С2Н5SH). Одорируют газ чаще всего на ГРС, но иногда осуществляют и на головных сооружениях. Универсальный одоризатор УОГ-1 разработан ВНИПИГаздобыча и изготовляется Щекинским заводом РТО. Применяют также одоризационные установки капельного, барботажного и эжекторного типов.
Транспорт газа
Схема сбора и транспорта газа представлена на рисунке 3.6.
3.6. Схема сбора и транспорта газа
Природный газ из скважин 1 по шлейфам - газопроводам 2 поступает на установку комплексной подготовки газа УКПГ (газосборный пункт) 3 (или римские цифры .I, II, III, IV, V, VI). На УКПГ замеряется количество поступающего газа от каждой скважины и в сепараторах производится грубая его очистка от влаги и механической взвеси (песка, пыли, продуктов коррозии). Далее по газопроводу 4 через клапан отсекатель (обратный клапан) 4А газ поступает в газосборный коллектор 5, который, в зависимости от расположения скважин на промысле, может быть линейным, кольцевым или лучевым.
На головных сооружениях 6, газ тщательно осушают от воды, тяжелых углеводородов, удаляют СО2, Н2S и избавляются балласты от компонентов.
В состав промысловых объектов входят скважины 1 насчитывающие десятки на каждом УКПГ, УКПГ 3 (от 1 до 10 штук и более на промысле), газосборный коллектор 5, головные сооружения 6. Все эти сооружения соединены через ГС с магистральным газопроводом 7 (МГ).
Особенно ответственными участками магистрального газопровода являются участки на болотах и узлы переходов через реки, железные дороги, овраги. Двухниточный переход (дюкер) через реку 11 показан на схеме (рис. 3.6). К магистральному газопроводу могут быть подключены ответвления (газопроводы-отводы) 13 промежуточному потребителю.
Поднятие давления в МГ и перекачка газа по нему осуществляется компрессорными станциями 8 установленными по трассе газопровода примерно через 150 км.
Заданная производительность в МГ в пиковые сезоны может быть обеспечена из подземных хранилищ газа 12, расположенных недалеко от трассы МГ и наибольшего потребителя газа. Хранилища могут быть естественными и искусственными. Естественными являются хранилища образованные на выработанных промыслах.
Передача газа из МГ потребителю осуществляется через газораспределительные станции 9а и далее через газораспределительные пункты 14 (показаны линиями).
Осушка газа от воды в технологическом процессе необходима в первую очередь для предотвращения в МГ кристаллогидратов, которые образуются при высоких давлениях при наличии паров воды и легких углеводородов (метан), а также предотвращения образования пробок из воды и тяжелых углеводородов, находящихся в жидком виде в пониженных местах газопроводов, уменьшающих пропускную способность трубопроводной системы. Кристаллогидраты похожи на лед и способны забивать сужающиеся места трубопроводов, и особенно участки трассы с поворотами.
Вопросы для самопроверки
1.На какой глубине в недрах земли находятся газоносные пласты?
2.Какие виды обнаружения газо- и нефтеносных пластов Вы знаете?
3.Поясните, как осуществляется поиск газоносного горизонта с помощью локации?
4.Что называется нефтяной или газовой залежью?
5.В каком случае залежь называется нефтегазовой, в каком газоконденсатной, а в каком нефтегазоконденсатной?
6.В каком случае газовая залежь называется промышленной?
7.В каких породах присутствуют запасы газа?
8.Представьте схему нефтегазовой залежи.
9.Представьте схему газовой скважины, из каких элементов она состоит?
10.Что такое дебит газовой скважины? Что такое рабочий дебит скважины?
11.Что Вы знаете об эксплуатации нефтяных и газовых скважин?
12.Представьте схему куста скважин.
13.Для каких целей возводятся газохранилища у магистральных газопроводов и какие газохранилища вы знаете?
Магистральные газопроводы
К магистральному относится газопровод диаметром 100 и более мм. и длиною свыше 50 км. Магистральные газопроводы достигают диаметра 1420 мм. Больший диаметр МГ является и технически и экономически не эффективным.
Наиболее часто встречающимися газопроводами-отводами присоединяемыми к магистральным газопроводам являются диаметры: 520 мм., 720 мм., 820 мм., 1020 мм., 1220 мм. и 1420 мм. Первые МГ имели давление 4,0 МПа, 5,5 МПа, 6,4 МПа и 7,5 МПа. В настоящее время проектируются МГ на давление 8,4 МПа и рассматриваются МГ на давление 12 МПа.
От газовых скважин до установок комплексной подготовки газа (УКПГ) используют газопроводы – шлейфы (шлейфы), чаще всего не превышающие диаметр 375 мм, давлением 7,5-10 МПа.
Между УКПГ и головными сооружениями (ГС) газового промысла применяют межпромысловые газопроводы.
На МГ монтируют запорные устройства – стальные шаровые краны бесколодезного типа (на газопроводах отводах могут использоваться задвижки), продувочные конденсатоотводчики для сбора и удаления конденсата.
Переходы газопроводов через большие судоходные реки обычно выполняются двумя-тремя нитками подводных трубопроводов, называемых дюкерами. Пропускная способность одного дюкера обычно составляет 70% от всего транспортируемого газа. Дюкер выполняют из труб с утолщенной стенкой, покрывают антикоррозионным покрытием весьма усиленного типа, балластируют
железобетонными, иногда чугунными пригрузами для придания отрицательной плавучести и заглубляют на 0,5 м в грунт от дна реки.
На пересечении нешироких рек, например горных с быстрым течением, а также ущелий и глубоких оврагов сооружают, как правило, воздушные переходы газопроводов балочной, подвесной, вантовой, арочной конструкций.
Под автомобильными и железными дорогами МГ прокладывают в гильзах (стальном кожухе), концы гильзы герметизируют, а к полости подсоединяется свеча, удаляемая от дороги не менее чем на 2,5 м, и поднимается над землей не менее 5 м.
Линейная часть газопровода
Линейная часть – основная составляющая часть магистрального трубопровода, она представляет собой непрерывную нить, сваренную из отдельных труб и уложенную тем или иным способом в зависимости от особенностей ее эксплуатации и природно-климатических условий местности.
К линейной части относятся лупинги и отводы от основной магистрали, отключающая и запорная арматура, переходы через естественные и искусственные препятствия, узлы запуска и приема очистных устройств, компенсаторы и конденсатосборники. Как правило, в состав линейных сооружений включают систему электрохимической защиты газопровода от коррозии и вдольтрассовые дороги.
Таблица 4.1
Дата добавления: 2018-06-27; просмотров: 877; Мы поможем в написании вашей работы! |
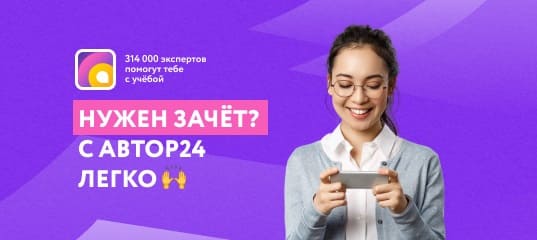
Мы поможем в написании ваших работ!