Конструирование внутренних протяжек.
Внутренние протяжки имеют следующие основные конструктивные элементы:
1. передняя замковая (присоединительная) часть
2. шейка
3. передняя направляющая часть
4. режущая часть
5. калибрующая часть
6. задняя направляющая часть
7. задняя замковая (присоединительная) часть.
Диаметр хвостовика d1должен соответствовать диаметру отверстия патрона станка и быть меньше (на 1…2 мм) диаметра предварительного отверстия.
Для круглых протяжек применяют несколько типов хвостовиков (ГОСТ 4044 – 70).
Длина ℓ4 передней направляющей части берется от 0,6 при большой длине отверстия до 1,0 ее длины.
Расстояние от переднего торца до первого зуба должно обеспечить возможность установки протяжки на станке.
ℓ´ = ℓ1 +ℓст+ℓзаг
Расчет внутренней протяжки.
При расчете протяжек определяют:
1) размеры конструктивных элементов режущей части исходя из:
– прочности тела протяжки;
– тяговой силы станка;
– условий размещения стружки в канавках;
– длины хода ползуна станка;
2) размеры калибрующих зубьев, обеспечивающие требуемые параметры обработанных поверхностей.
Исходные данные для расчета:
1) данные о детали: форма, размеры до и после протягивания с данными о точности и шероховатости, материал и его свойства, характер
2) данные об оборудовании: характеристика станка (сила тяги, длина хода ползуна, расстояние от опорной поверхности до патрона, скорость ползуна и прочее). Оборудование может быть выбрано и по результатам расчета.
|
|
Порядок расчета.
1. Определяют размеры отверстия до протягивания и припуск под протягивание (А).
А = 0,005 D + (0,1¸0,2) √ℓ
D0 = D – A
Часто отверстие до протягивания уже задано, тогда А = Dmax–D0 min
По D0 выбирают размеры хвостовика и передней направляющей части.
2. Назначают подъем на зуб аzпо справочной литературе.
3. Определение размеров зубьев и стружечных канавок.
Форма режущих зубьев в сечении, проходящем через ось протяжки, может быть нескольких видов. Она устанавливается исходя из условий возможности резания, образования стружки, размещения стружки в канавке и прочности зуба.
Наиболее распространены формы зуба с прямолинейной под углом 35 – 45° спинкой зуба или со спинкой по форме балки равного сопротивления круговой вогнутой формы для увеличения пространства для размещения стружки.
t – шаг зубьев
h – высота стружечной канавки
b – ширина спинки зуба
r – радиус основания канавки
R= 1,6 hk – радиус спинки зуба
(в среднем)
В некоторых случаях канавки делают удлиненной формы.
Применяются для обработки отверстий большой длины, с целью уменьшения силы резания и сохранения размера тела протяжки, при обработке прерывистых поверхностей.
|
|
Передний γ и задний α углы выбирают из справочной литературы. Передний угол выбирают в зависимости от материала заготовки. У внутренних протяжек задний угол α небольшой 2…3°, что необходимо для небольшого изменения положения режущих кромок при переточках.
Высоту стружечных канавок определяют из условия размещения стружки во впадине зуба.
-коэффициент укладки стружки.
к- зависит от материала заготовки и схемы резания.
Для стали при одинарной схеме резания к=4, при групповой 3, для чугуна соответственно 2,5 и 2.
Для сливной стружки h = 1,1283 √k ∙ℓ ∙ az
Для стружки надломаh = 0,8917 √k ∙ ℓ∙az
По расчетному значению выбирается ближайшее большее значение из справочников, а также и все остальные размеры стружечной канавки (b, R, r), а также и шаг зубьев.
Последовательность выполнения пунктов 2 и 3 может быть обратной, т.е. вначале определяют предварительно шаг режущих зубьев из условия получения достаточного числа зубьев, находящихся одновременно в работе.
t = Q√ℓ
Для одинарной схемы резания Q = 1,25…1,5, при групповой Q = 1,45…1,9.
Величина t корректируется при дальнейшем расчете. По t определяют все остальные размеры стружечной канавки.
|
|
Затем уже определяют подъем на зуб из условия размещения стружки в канавке
az = Fa / k ∙ ℓ
4. Определение числа одновременно работающих зубьев.
zi= ℓ / z ; zimin ; zimax
желательно, чтобы ziбыло ближе к целому числу (лучше к большему, но не равнялось ему)
ziminне должно быть меньше 2, в противном случае протяжка может потерять центрирование.
Если деталь короткая, рекомендуется протягивание
5. Определение силы протягивания.
Р = Сp ∙ аzx∙ Σb ∙ zi∙ kγ∙ kсож∙ kи Н
γ, СОЖ, износ
(Σb ∙ zi) – суммарная ширина срезаемых слоев всеми зубьями.
6. Проверка прочности протяжки в опасных сечениях.
Опасными сечениями обычно являются замковая часть или шейка хвостовика и сечение по впадине первого зуба.
Площадь сечения во впадине первого зуба равна:
Foc1= 0,25 ∙ π (D1 – 2h)²
Растягивающие напряжения σр = Р / Foc ≤ [σр]
При невыполнении неравенства следует изменить конструктивные параметры протяжки: схему резания, увеличить шаг, уменьшить подъем на зуб.
Тяговое усилие станка должно быть >P.
7. Число зубьев режущей части
zp = A / az + (2…3)
Дополнительные 2…3 зуба являются переходными и чистовыми, с уменьшенным подъемом на зуб для уменьшения шероховатости, плавного снижения силы протягивания и для запаса на переточки. Они имеют такой же шаг, как и режущие.
|
|
Первый зуб в протяжке равен диаметру предварительного отверстия – для среза неровностей.
8. Длина режущей части
ℓр = zp∙ t
В некоторых случаях шаг делают неравномерным для избежания циклических нагрузок при протягивании.
9. Длина калибрующей части
zkобычно от 4 до 8, чем выше качество поверхности, тем больше zk. Шаг калибрующих зубьев делают или равным шагу режущих, или tк = 0,6 t.
Форму зубьев устанавливают в зависимости от шага.
γк равны γ режущих, задние углы αк= 1…2°. На задней поверхности оставляют ленточку, ширина которой увеличивается от зуба к зубу на 0,2 мм (от 0,2 до 0,6 мм).
ℓк= zk ∙ tк
10. Общая длина протяжки (L) – получается сложением длин всех частей протяжки. Она должна быть согласована с длиной хода ползуна станка
L - ℓ1 < Lст
и удовлетворять технологическим условиям возможности ее изготовления: обычно для протяжек средних размеров
L ≤ 40 D
Если L– большая, то рабочую часть делят на несколько протяжек. Их называют комплектом. Длина протяжек в комплекте одинаковая. Первый зуб последующей протяжки должен быть равен по размеру калибрующим зубьям предыдущей.
Наружные протяжки.
Обработку ими осуществляют на специальных станках горизонтального или вертикального типа.
Протяжка не имеет гладких частей, а только режущую часть. Часто протяжка это набор рабочих частей, закрепленных определенным образом в корпусе. Каждая секция предназначена для обработки определенного участка поверхности заготовки.
Расположение секции на плите может быть последовательным, параллельным и параллельно – последовательным.
Последняя применяется наиболее часто, что уменьшает длину протяжки и обеспечивает хороший отвод стружки и удобство крепления и регулировки положения секций.
Желательно, чтобы общая ширина для одновременно работающих секций была бы постоянной (равные усилия, равномерная загрузка станка).
Схема резания выбирается в зависимости от припуска, так чтобы длины протяжек каждой секции были одинаковы.
Расчет режущей части не имеет принципиальных отличий.
Подъем на зуб несколько больше (условия работы лучше).
Можно несколько уменьшить К. Легче сделать косые зубья, что обеспечивает плавность работы.
Можно сделать больше задние углы α.
Применяют разные способы крепления секций на плите: в паз, в уступ, клиновыми планками и через промежуточную деталь.
Для регулировки размеров по высоте и ширине применяют продольные клинья или подкладки.
Для точной установки секции в заданное положение используют: направляющие планки или иногда делают бурт.
Корпус по технологическим соображениям легче сделать разборными.
1 – общая плита
2 – корпус для закрепления секций протяжки
3 – секция протяжки
4 – поперечные упоры (шпонки)
Дата добавления: 2018-06-27; просмотров: 479; Мы поможем в написании вашей работы! |
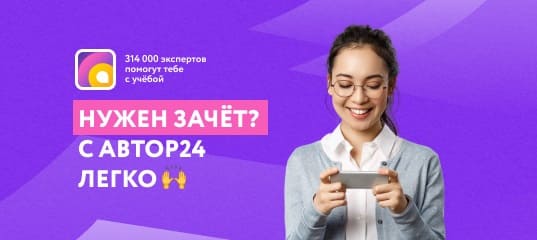
Мы поможем в написании ваших работ!