Классификация фасонных резцов.
1) По форме:
стержневые
призматическиекруглые
2) По установке относительно заготовки:
радиальные и тангенциальные
3) По расположению оси отверстия или базы крепления резца: с параллельным расположением оси или базы крепления резца относительно оси заготовки; с повернутой базой.
4) По форме образующих фасонных поверхностей: с кольцевыми образующими и с винтовыми.
5) По расположению обработанной поверхности: наружные и внутренние.
6) По расположению передней поверхности:
γ→(+) или =0; γ=(+) и углом λ
7) По конструкции: цельные, составные, насадные, хвостовые.
Общие понятия об установке и заточке резцов.
С помощью винта в державке резец устанавливают на высоту центров.
При переточках резец укорачивается, но имеет туже форму.
При заточке и переточках выдерживают угол равный сумме α+γ.
Для обеспечения заднего угла у круглого резца его ось поднимают над осью заготовки на величину h.
|
H – высота, которая выдерживается при переточках, что обеспечивает получение заданного переднего угла
h=R ∙ sinλ ; H=R ∙ sin (α+γ) ;
Фасонные резцы всегда затачивают по передней поверхности.
Круглые резцы имеют на много больше переточек, чем призматические.
5.3. Понятия о профиле детали и резца
Точку, имеющую min диаметр обычно выбирают за базовую – т.1.
На профиле детали отмечают характерные точки. Их обычно находят на стыках участков профиля с различным характером образующих. На конических участках берут дополнительную точку (примерно в середине), а для участков с криволинейной образующей – не менее трех дополнительных точек (кроме крайних).
|
|
Профиль имеет: радиальные или высотные размеры и осевые или продольные размеры.
Размер t = rmax– rmin – называют глубиной профиля
b = ℓmax – ℓmin– шириной фасонного профиля
Из-за наличия углов α и γ высотные размеры профиля резца не равны высотным размерам профиля детали. Поэтому надо для их нахождения рассчитывать их.
|
Рi– высотный размер – измеряется в нормальном сечении (N – N) к базе.
Li– продольные размеры измеряются вдоль базы.
У круглого резца базой является отверстие или ось.
Проектирование фасонных резцов.
Проектирование фасонного резца начинается с выбора типа резца.
В большинстве случаев рекомендуется применять круглые резцы (больше переточек, легче изготавливать), но при больших размерах профиля крепление круглых резцов нежесткое.
Призматические резцы применяют при больших размерах профиля, при повышенных требованиях к точности профиля.
Для внутренней обработки применяют круглые резцы, иногда винтовые.
|
|
В основном применяются радиальные резцы.
Дальнейшее проектирование фасонных резцов предусматривает решение следующих задач:
1) назначение и расчет геометрических и конструктивных параметров;
2) профилирование резца, т.е. определение его профиля.
1) Назначение геометрических параметров режущей части резца.
γ – в зависимости от материала заготовки.
По мере удаления от точки 1 угол γ – уменьшается, что учтено в справочных таблицах.
α – для круглых резцов обычно 8…12°, призматических 10…15°, но могут быть и другие.
Углы α и γ всегда задаются в точке 1, т.е. имеющей min радиус в сечении, перпендикулярном к базе резца.
Далее определяют габаритные размеры и основные конструктивные размеры. Обычно эти размеры определяются из конструктивных соображений в зависимости от глубины и ширины профиля.
Габаритный радиус дисковых резцов определяется по формуле:
R = (tmax + e + k + d0 /2) / cos α
e – пространство для размещения стружки 3…8 мм;
tmax= (rmax– rmin) – глубина профиля;
к = 8…10 мм или 0,4d0 – толщина стенки резца, мм;
d0 – диаметр посадочного отверстия выбирают из таблиц или рассчитывают по эмпирическим формулам в зависимости от глубины, ширины профиля и возникающих сил.
|
|
Диаметр резца D = 2Rокругляют в большую сторону до целого, кратного пяти (обычно).
Диаметр внутреннего резца D = (0,7…0,8) dотв.
. Коррекционные расчеты фасонных резцов
обычной установки.
Для резцов обычной установки коррекции подлежат высотные размеры профиля. Осевые размеры у этих резцов остаются такими же, как у детали.
Существует два метода нахождения профиля резца:
1) Графический.
Недостаток – низкая точность, применяют когда деталь не требует особой точности;
2) Аналитический
Можно рассчитывать вручную (для деталей не сложного профиля) и с применением ЭВМ (для деталей, имеющих сложные криволинейные профили).
В качестве расчетных величин для характерных и выбранных точек принимают средние размеры, т.е. те, которые лежат в середине поля допуска.
Размеры инструмента принято считать до 3-го знака.
. Общая часть коррекционного расчета.
Цель – определение высотных размеров профиля фасонного лезвия, лежащих в передней плоскости резца, в направлении, перпендикулярном базе резца Сi.
1. m = r1 ∙ sinγрасчет производится только
2. A1 = r1 ∙ cosγ один раз
3. А2 = √ r2 ² - m² расчет повторяется для всех
|
|
4. C2 = ± (A2 – A1) точек профиля
(+) – наружная обработка; (–) – внутренняя
Определение размеров профиля призматического и круглого
фасонных резцов обычной установки с углом λ = 0.
Исходными данными при расчете призматического резца являются углы α и γ, а также размеры С2,3,…,i
Исходными данными для круглых резцов являются углы α и γ, наружный радиус резца, соответствующий базовой точке и размеры Сi
1. H = R1 ∙ sin (α + γ) рассчитывают один раз
2. B1 = R1 ∙ cos (α + γ)
3. Bi = B1 – Ci
4. Ri= √H² + Bi² рассчитывают для каждой точки
5. Pi = R1 – Ri
Погрешность профиля деталей обработанных фасонными
резцами радиального типа.
|
|
Линия 1 – 2 не опишет коническую поверхность, т.к. она не проходит через ось конуса. Поэтому для повышения точности необходимо вводить промежуточные точки.
Для полного устранения погрешности в необходимых случаях выполняют наклон передней поверхности на угол λ.
q = (r2 – r1) ∙ sinγ
tgλ = q / ℓ2 = ((r2 – r1) ∙ sinγ) / ℓ2
tgλ = tgσ ∙ sinγ
Такие резцы называют резцами с базовым участком режущей кромки, расположенном на высоте оси детали.
У круглых резцов погрешность профиля детали вызвана также тем, что их режущая кромка образуется пересечением конуса плоскостью, не проходящей через ось конуса, отсюда криволинейная режущая кромка.
Таким образом, круглые резцы менее точные, чем призматические.
Двойной наклон передней грани применяют также и для улучшения условий резания:
|
|
т.к. во всех точках сохраняются одни и те же значения углов.
Величины задних углов резца в различных точках лезвия
Они различны. Причины:
1) Различное положение точек лезвия по высоте. Чем ниже точка – тем больше α.
2) Истинные задние углы измеряются в сечении, перпендикулярном проекции режущей кромки на основную плоскость.
|
tgαN= tgα ∙ sinφ
φ – угол профиля
Особенно малые значения задних углов получаются на торцовых участках профиля.
Для увеличения α на этих участках применяют следующие меры:
1) Выполняют кромку со вспомогательным углом φ.
|
2) Оставление ленточки (дальше резцы могут обеспечивать размер детали).
|
3) Изменением положения резца.
Такие резцы называют резцами с развернутой базой.
Разворот базы может выполняться:
a) в горизонтальной плоскости:
|
tgαб = tgα ∙ sinψ
αmin = 3°
sin ψ = tg αб(N-N)/ tg α
b) в вертикальной плоскости
|
Для внутренних отверстий применяют винтовые резцы. Шаг винтовой канавки определяют следующим образом:
Т = 2πR ∙ tgαб
Протяжки.
Протяжка – многолезвийный инструмент с рядом последовательно выступающих одно над другим лезвий в направлении, перпендикулярном к направлению скорости главного движения, предназначенный для обработки пир поступательном или вращательном главном движении лезвия и отсутствии движения подачи.
Применяют при массовом и серийном изготовлении различных деталей.
Прошивка отличается от протяжки направлением приложения тяговой силы, которая приложена не к передней части, а к задней.
Протяжка работает на растяжением, прошивка на сжатие. Поэтому прошивки выполняются короткими. Они имеют небольшое число зубьев и применяются в основном при калибровке.
Типы протяжек.
Подразделяют на две основные группы:
– внутренние (для обработки отверстий)
– наружные.
По типу протягиваемых поверхностей протяжки разделяют на:
– круглые
– шпоночные
– шлицевые
– гранные
– фасонные
– комбинированные
– плоские.
Протяжки бывают режущие, имеющие острые зубья и уплотняющие (выглаживающие, работа зубьев которых основана на давлении и уплотнении материала).
По методу протягивания можно разделить протяжки со свободным протягиванием и координатным протягиванием.
При свободном протягивании протяжка самоустанавливается под действием сил резания.
При координатном протягивании обеспечивается и точность размеров протягиваемой поверхности, и точность ее положения относительно баз. Для этого применяют специальные приспособления (адаптеры).
Дата добавления: 2018-06-27; просмотров: 514; Мы поможем в написании вашей работы! |
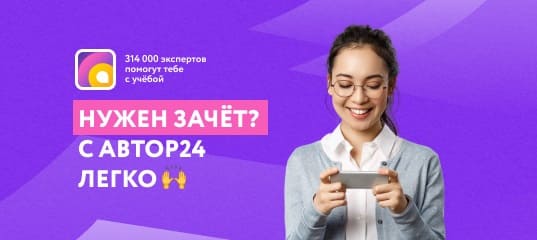
Мы поможем в написании ваших работ!