Конструкция развёртки. Особенности
Основными конструктивными элементами развёртки являются режущая и калибрующая части, число зубьев, направление зубьев, углы резания, шаг зубьев, профиль канавки, зажимная часть.
Режущая часть.
§ Угол конуса φ определяет форму стружки и соотношение составляющих усилий резания. Угол φ у ручных развёрток – 1°…2°, что улучшает направление развёртки при входе и уменьшает осевую силу; у машинных при обработке стали φ = 12°…15°; при обработке хрупких материалов (чугуна) φ = 3°… 5°.
§ Стандартные развёртки делают с неравномерным окружным шагом с целью предупреждения появления в развёртываемом отверстии продольных рисок. Из-за неоднородности обрабатываемого материала на зубьях развёртки происходит периодическое изменение нагрузки, что ведёт к отжиму развёртки и появлению на обработанной поверхности следов в виде продольных рисок.
Калибрующая часть состоит из двух участков: цилиндрического и участка с обратной конусностью. Длина цилиндрического участка около 75% от длины калибрующей части. Цилиндрический участок калибрует отверстие, а участок с обратной конусностью служит для направления развертки в работе. Обратная конусность уменьшает трение об обработанную поверхность и снижает разбивку. Т.к. при ручном развертывании разбивка меньше, то и угол обратной конусности у ручной развёртки меньше, чем у машинной. При этом цилиндрический участок у ручных развёрток может отсутствовать.
|
|
Цилиндрическая ленточка на калибрующей части калибрует и выглаживает отверстие. Уменьшение её ширины снижает стойкость развертки, однако повышает точность обработки и снижает шероховатость, т.к. уменьшает трение. Рекомендуемая ширина ленточки f = 0,08…0,5 мм в зависимости от диаметра развёртки.
Число зубьев z ограничивается их жёсткостью. С увеличением z улучшается направление развертки (больше направляющих ленточек), повышаются точность и чистота отверстия, но снижается жесткость зуба и ухудшается отвод стружки. Z принимается чётное - для облегчения контроля диаметра развёртки.
Канавки чаще выполняют прямыми, что упрощает изготовление и контроль. Для обработки прерывистых поверхностей целесообразно применять развёртки с винтовым зубом. Направление канавок делается противоположным направлению вращения для избежания самозатягивания и заедания развёртки.
Задний угол выполняют небольшой (5°…8°) для повышения стойкости развёртки. Режущую часть затачивают до остра, а на калибрующей делают цилиндрическую ленточку для повышения размерной стойкости и улучшения направления в работе.
Передний угол принимают равным нулю.
|
|
Развертки – основные виды и сферы их применения.
Развёртки относят к осевому многолезвийному режущему виду инструмента. Их применяют в процессе финальной обработки сделанных ранее отверстий. В ходе такой обработки снимется очень тонкая стружка. Свою работу развертка выполняет путем вращения с одновременным выполнением поступательного движения вдоль отверстия. Подобную работу можно выполнять и с помощью шлифовального инструмента, однако в таком случае на очищаемой поверхности остаются частички абразивного материала, что впоследствии приводит к быстрому износу деталей.
По типу привода выделяют три основных вида разверток: ручные, машинные и регулируемые. Первый вид, развертки ручные, применяют при обработке отверстий путем вращения развертки воротком вручную. Квадрат цилиндрического хвостовика вставляют в середину воротка. Ручные развертки производятся из стали марки «9ХС». Калибрующую часть и длинный заборный конус ручной развертки затачивают для более точного направления развертки в обрабатываемом отверстии.
Второй вид, развертки машинные, применяются для обработки отверстий на всевозможных станках (к примеру, на координатно-расточных, токарных, сверлильных, револьверных и прочих). Развертки машинные разделяют на насадные, цельные и сборные. Хвостовики бывают либо цилиндрическими с диаметром от 1 до 9милиметров, либо коническими с диаметром от 10 до 32 миллиметров. Они имеют относительно длинную шейку и конус Морзе.
|
|
Третий вид, разверти регулируемые по диаметру, применяют зачастую при выполнении ремонтных работ. Развертки регулируемые также изготовляют из стали «9ХС». Они работают по следующему принципу. В корпусе регулируемой развертки есть отверстие, которое состоит из цилиндрической и конической частей. В первую часть помещают шарик, который передвигается вдоль оси регулировочным винтом. По мере его перемещения упомянутым винтом происходит увеличение диаметра калибрующей части, что происходит благодаря упругим деформациям стенок развертки.
Если говорить о форме обрабатываемых отверстий, то тут так же выделяют несколько видов разверток, а именно развертки цилиндрические и конические. Первые употребляют для развертывания цилиндрического отверстия, вторые, соответственно, для развертывания конического. И те и другие могут быть как ручными, так и машинными..
Рис. 32. Виды разверток: а - цилиндрическая: 1 - рабочая часть, 2 - шейка, 3 - хвостовик, б - спиральные; в - цилиндрическая насадная, г, д - конические, е - элементы рабочей части развертки: 1 - задняя поверхность, 2 - канавка, 3 - режущая кромка, 4--передняя поверхность, 5 - ленточка, 6- режущее перо, 7 -канавка, 8 - зуб
|
|
Для развертывания отверстий применяют ручные и машинные развертки, которые подразделяются на цилиндрические (с прямым и спиральным зубом) и конические (рис. 32).
Развертывают отверстия вручную при помощи воротков, а также на станках, которые применяют при сверлении. Развертка (рис. 32, а) состоит из рабочей части 1, шейки 2 и хвостовика 3 с квадратной головкой.
При развертывании отверстий диаметром до 6 мм припуск на развертывание оставляют 0,1 мм, при развертывании отверстий диаметром от 6 до 12 мм - 0,15 мм, а при развертывании отверстий диаметром от 12 мм и более -0,3 мм.
Конусные отверстия обрабатывают коническими развертками. В отличие от цилиндрических, конические развертки имеют коническую рабочую часть. Такие развертки изготовляют комплектно из двух или трех штук. В комплекте первая развертка черновая - обдирочная, вторая - переходная и третья - чистовая, которая придает отверстию окончательный размер и требуемую чистоту поверхности. Конусные отверстия диаметром до 10-12 мм можно развертывать одной конусной разверткой.
Чтобы получить в результате развертывания чистую поверхность в отверстии, необходимо применять смазочно-охлаждающие жидкости. При развертывании отверстия вручную следует направлять развертку точно по оси отверстия, без перекосов и вращать плавно, без толчков.
АНАЛИЗ СУЩЕСТВУЮЩИХ КОНСТРУКЦИЙ КОМБИНИРОВАННЫХ ИНСТРУМЕНТОВ
В настоящее время существует большое количество разновидностей комбинированных инструментов. Инструмент делится на однотипный и разнотипный. Разновидностями однотипного инструмент являются комбинированные развертки. Разнотипные инструменты образованы из разных комбинаций однотипного инструмента. Основными разновидностями разнотипного инструмента является: сверло-развёртка, свердло-зенкер-развёртка, зенкер-развёртка, развёртка-раскатка, развёртка-метчик.
Основные комбинированные инструменты, на базе развёртки, используемые на предприятиях представлены на рис. 1.
Рисунок 1 – Разновидности комбинированного инструмента:
а) – развертка двухступенчатая цельная; б) – сверло-развертка;
в) – развертка-метчик.
При обработке однотипными инструментами характер резания одинаков. Режимы резания выбираются исходя из режимов лимитирующей струпени.
Обработка разнотипным инструментом характеризуется разным характером формообразования. Необходимо учитывать силы резания и подбирать инструмент, который в комбинации с другим инструментом обеспечивал бы необходимую стойкость.
Количество степеней комбинированного инструмента может достигать шести. При обработке многоступенчатым инструментом нужно чётко представлять процесс резания и процесс удаления стружки. При неправильной конструкции инструмента, стружка может попадать в зону обработки следующей степени и наносить вред в виде царапин на поверхности. Поэтому необходимо особенно чётко следить за изготовлением чистовых инструментов.
Комбинированный инструмент может быть представлен в виде цельного, сборного или насадного.
Цельный инструмент (осевой) изготовляют из быстрорежущей стали. При обработке отверстий с малым перепадом диаметров комбинированный инструмент изготовляют из одномерного, путем перешлифовки части инструмента, предназначенную под обработку малого диаметра.
Сборный инструмент изготовляют путем соединения одинарных инструментов в разные комбинации с помощью инструментальной наладки. В зависимости от характеристик наладки комбинированный инструмент может быть переналаживаемым и специальным.
Обработка сборным инструментом более эффективна, чем обработка одномерным за счет одновременной обработки нескольких поверхностей. Обработка является совокупностью одинарных формообразующих движений, соединенных в одну операцию, поэтому необходимо точно настраивать инструментальную наладку при подготовке производства. Это добавляет дополнительные трудности.
Насадной инструмент образуется путем соединения инструментов в корпусе одного из инструментов. Такой инструмент является специальным. При износе одного из инструментов, «корпусной» инструмент перетачивают, а насадной – меняют, поскольку при его перетачивании теряется размер. В некоторых случаях, когда позволяют размеры инструмента, возможно использование регулируемого насадного инструмента.
Комбинированная развертка может работать по двум схемам резания (параллельной и последовательной). В данном случае схема резания, по которой работает инструмент, определяется конструкцией самой развертки.
Для обработки по параллельной схеме резания необходимо изготовливать инструмент так, чтобы обе степени вступали в процесс резания одновременно. Параллельная схема резания обеспечивает высокую производительность за счет сокращения машинного времени. Недостатком параллельной схемы является увеличение составляющих сил резания, которые ведут к незначительному изгибу оси инструмента, а, соответственно, увеличивают разбивание отверстия. Так же увеличивается количество выделенного тепла, которое ведет к снижению стойкости инструмента.
Последовательная схема резания устраняет недостатки параллельной, но увеличивается суммарное время.
Общий вид спроектированной двухступенчатой комбинированной развёртки представлен на рис. 2.
Рисунок 2 – Общий вид двухступенчатой комбинированной развёртки
Точность обработки по последовательной схеме резания обеспечивается формой поперечного сечения развёртки, поэтому его необходимо делать с неравномерным шагом зубьев.
При обработке по параллельной схеме резания, для упрощения изготовления развертки, можно использовать развёртку с равномерным угловым шагом. Это объясняется тем, что силы одной ступени оказуют влияние на работу второй ступени. При обработке по параллельной схеме резания фигура обхода контура секции развертки – фигура Лиссажу, которая образуется за счет влияния силы резания одна на другую.
Причины образования огранки отверстий
При обработке осевым многозубым инструментом наиболее характерными погрешностями является огранка отверстий. Установлено, что величина огранки может превосходить поле допуска на обработанное отверстие. Характерно, что такие отверстия могут считаться годными, так как традиционными средствами контроля, например, предельными калибрами и индикаторными нутромерами, она не может быть обнаружена.
Наличие огранки отверстий оказывает большое влияние на эксплуатационные свойства узла или машины в целом. Контакт сопряжённых поверхностей деталей машин происходит по вершинам микронеровностей наиболее выступающих мест контактирующих поверхностей. Отношение фактической поверхности контакта к номинальной при чистовом развертывании составляет 0,3 – 0,5 и только при тщательной доводке это соотношение может быть равно 0,9. Такой характер контакта приводит к интенсивному износу деталей, а также увеличивает зазоры между сопряжёнными поверхностями.
Согласно исследованиям Ольшанского Н.Ф., при крутильных колебаниях сумма приращений сил резания на всех зубьях инструмента сводится к паре сил относительно его оси, а равнодействующая этой пары в любой момент времени равна нулю, а значит крутильные колебания не оказывают влияния на огранку отверстия.
Исследованиями установлено, что наличие крутящего момента ведёт к радиальным перемещениям инструмента, однако это наблюдается при соотношении между длиной инструмента l и его диаметром d больше 20. Допустимо предположить, что эти выводы справедливы и для крутящих моментов, изменяющихся по периодическому закону. Учитывая, что огранка в отверстиях образуется при обработке инструментом, у которого l/d<<20, влиянием крутильных колебаний на огранку можно пренебречь.
Для составления уравнения, характеризующего траекторию движения зубьев при вынужденных колебаниях, а следовательно, и для определения формы поперечного сечения обработанного отверстия, достаточно знать уравнения движения центра инструмента.
ЗАКЛЮЧЕНИЕ
В результате выполненного курсового проекта можно сделать вывод о том что спроектированный инструмент соответствует как заданному качеству и форме.
Список литературы
1. Алексеев Г.А., Аршиков В.А., Кричевская Р.М. Конструирование инструмента. – М.: Машиностроение, 1979-383 с.
2. Аршиков В.А., Алексеев Г.А. Резание металлов и режущий инструмент. – М.: Машиностроение 1976 – 439 с.
3. Грановский Г.И., Панченко К.П. Фасонные резцы М.: Машиностроение 1975 – 309 с.
4. Денисенко В.И. Расчет и конструирование режущих инструментов, Владимир, 1973 – 164 с.
5. Иноземцев Г.Г. проектирование металлорежущих инструментов М. Машиностроение 1984 г – 270 с.
6. Кирсанов Г.Н. Руководство по курсовому проектированию металлорежущих инструментов, М.: Машиностроение, 1986 – 284 с.
7. Маргулис Д.Ж. Протяжки для обработки отверстий М.: Машиностроение, 1986 – 279 с.
8. Методические указания к курсовому проекту по курсу «Проектирование металлорежущего инструмента» Петров В.А. НПИ, 1987 г. – 24 с.
9. Нефедов Н.А., Осипов К.А. Сборник задач и примеров по резанию металлов и режущему инструменту М.: Машиностроение, 1984
10. Сахаров Г.Н. и др. Металлорежущие инструменты М.: Машиностроение, 1989 – 326 с.
11. Справочник зубореза Г.Г.Овумян, Я.И.адам М.: Машиностроение, 1983 – 223 с.
12. Справочник технолога-машиностроителя Т.2. Ю.А. Абрамов, В.Н.Андреев, М.: Машиностроение, 1986 – 496 с.
13. Фельдштейн Е.Э. Режущий инструмент. Курсовое и дипломное проектирование – М: Дизайн Про, 1997 – 384 с.
Дата добавления: 2018-06-27; просмотров: 215; Мы поможем в написании вашей работы! |
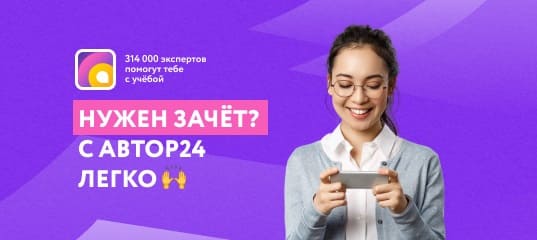
Мы поможем в написании ваших работ!