Модельный комплект для литья в песчано-глинистые формы.
Одним из основных видов литейной технологии является получение отливок в песчано-глинистых смесях (или как говорят «по земле»). Ему присущи те же недостатки, что и были в прошлое время. Однако от этого процесса до сих пор нельзя отказаться, и он, наряду с новыми технологиями, широко используется, в частности, и для получения художественного литья, в особенности крупногабаритных отливок.
Коротко технология получения отливок по этому методу заключается в приготов-лении специальной формовочной смеси - т.е. материала, из которого делают форму и в которую затем заливают металл для получения отливки. Формовочная смесь, как правило, состоит из трех компонентов: наполнителя (песок), связующего (глина) и специальных добавок. Затем следуют операции формовки отливки (по сути отпечатка модели в формовочной смеси), заливки металла, остывании отливки, выбивки и очистки отливки.
Во всех перечисленных операциях применяют разнообразное оборудование и инс-трументы, к основным из которых можно отнести следующие:
Модельным комплектом называется совокупность оснастки и приспособлений, предназначенных для получения определенной отливки. Модельный комплект состоит из модели отливки (или шаблонов для изготовления формы), моделей элементов литниковой системы, одного или нескольких стержневых ящиков, модельных или подмодельных плит и т.д. Основной оснасткой для получения отливки в песчано-глинистой форме является модель отливки и стержневой ящик.
|
|
Модель отливки. Модель – приспособление, при помощи которого в литейной форме вос-производят наружный контур будущей отливки, каналы элементов литниковой системы и знаки для крепления стержней. По наружной конфигурации модель является копией отли-вки и отличается от последней несколько увеличенными размерами, учитывающими усад-ку сплава и другие особенности процесса. Важнейшими признаками классификации моде-лей являются - вид литейного сплава, серийность производства, способ получения литей-ных форм, материал, прочность модели, конструкция и т.д.
По виду литейного сплава различают модели для чугунного, стального и цвет-ного литья.
По способу получения литейных форм различают модели для машинной и ручной формовки.
По материалу модели подразделяются на деревянные, металлические, гипсовые, цементные, пластмассовые и комбинированные.
По конструкции модели бывают разъемные, неразъемные, с отъемными частями и специальные (скелетные, шаблонные).
Деревянные модели (первый класс – бук, орех; второй класс – береза, липа; третий класс – сосна, ель) для предотвращения коробления при высыхании модели из-готавливают из сухого пиломатериала. Поверхность деревянной модели и стержней шпа-клюют, зачищают и покрывают нитролаком, не разбухающим при соприкосновении с вла-жной формовочной или стержневой смесью. Достоинства деревянных моделей – дешевиз-на, простота изготовления, малый вес. Недостаток – недолговечность..
|
|
Металлические модели характеризуются бóльшей долговечностью, точностью и чистотой рабочей поверхности. Изготавливаются они из алюминиевых сплавов – легкие, не окисляются, хорошо обрабатываются, а также чугуна. Для уменьшения массы, модели делают пустотелыми с ребрами жесткости. Модели из пластмасс устойчивы к дейст- вию влаги при эксплуатации и хранении, не подвергаются короблению, имеют малую массу.
Из-за усадки отливки при затвердевании линейные размеры моделей увеличивают: при производстве отливок из серого чугуна на 1%, ковкого чугуна и стали на 2%, цветных сплавов от 1% до 2%. Для облегчения выполнения операции протяжки (извлечение моде-ли из формы, а стержня из стержневого ящика) на их вертикальных стенках предусматри-вают формовочные уклоны с углами от 0,5 до 50. Если отливка после изготовления подве-ргается механической обработке, то модели и стержни изготавливают с учетом припуска на эту обработку.
|
|
Стержневой ящик. Из сказанного выше следует, что для получения многих отливок вну-тренние полости оформляются так называемыми стержнями. Технология изготовления стержней во многом аналогична изготовлению форм. Однако она имеет и особенности, обусловленные более высокими требованиями, предъявляемыми к их прочности, огнеу-порности, газопроницаемости, выбиваемости из отливки. Удовлетворение этих требова-ний обеспечивается прежде всего применением специальных стержневых смесей, теп-ловой сушкой, армированием, устройством вентиляционных каналов. Армирование за-ключается в том, что при изготовлении стержней в них закладывают стальную проволоку диаметром 4 – 8 мм и литые каркасы. Вентиляционные каналы в простых стержнях как и в формах прокалывают душником
Изготовление стержней осуществляется вручную или на специальных стержневых маши-нах из стержневых смесей. По форме стержень должен соответствовать форме внутрен-ней полости в отливке. Готовые стержни подвергаются сушке при температуре 200…
230 0С, для увеличения газопроницаемости и прочности.
Стержни в ручную изготавливаютвспециальных стержневых ящиках. Стержне-вой ящик –формообразующее изделие, имеющее рабочую полость для получения в ней литейного стержня нужных размеров и очертаний из стержневой смеси. Рабочая полость оформляется с помощью модели стержня. В стержневом ящике обеспечивают равноме-рное уплотнение смеси и быстрое извлечение стержня. Стержневые ящики могут быть разъемными и неразъемными (вытряхными), а иногда с нагревателями.
|
|
Опоки. Опоки представляют собой ящики без дна и крышки, куда набивается формовоч-ная смесь и в которых изготовляется верхняя и нижняя (если требуется) полуформы; опо-ки оформляют наружные боковые поверхности форм. Они имют приспособления для тра-нспортировки и сборки полуформ.
Литниковая система. Следующим важным моментом является вопрос о том, как расплав-ленный металл попадает в форму, где и образуется отливка. Для этого служит литниковая система. Для ее описания еще раз рассмотрим литейную форму и ее важнейший элемент – литниковую систему ( рис. 9 ).
Литейная форма на рис. 9 состоит из верхней и нижней полуформ, которые изго-тавливаются в опоках 1 – приспособлениях для удержания формовочной смеси. Полуфо-рмы ориентируют с помощью штырей 7. Для образования полостей отверстий или иных сложных контуров в формы устанавливают литейные стержни 8, которые фиксируют по-средством выступов, входящих в соответствующие впадины формы (знаки). Литейную форму заливают расплавленным металлом через литниковую систему.
Литниковая система – совокупность каналов и резервуаров, по которым расплав по-ступает из разливочного ковша в полость формы. Основными элементами литниковой си-стемы являются: литниковая чаша 3, которая служит для приема расплавленного металла и подачи его в форму; стояк 2 – вертикальный или наклонный канал для подачи металла из литниковой чаши в рабочую полость или к другим элементам; шлакоуловитель 5, с по-мощью которого удерживается шлак и другие неметаллические примеси; питатель 6 – один или несколько, через которые расплавленный металл непосредственно подводится в полость литейной формы. Для вывода газов, контроля заполнения формы расплавленным металлом и питания отливки при ее затвердевании служат прибыли или выпор 4. Для вывода газов предназначены и вентиляционные каналы 11.
Рис. 9. Эскиз формы в сборе:
1 – опоки; 2 – стояк; 3 – литниковая чаша; 4 – выпор; 5 – шлакоуловитель; 6 – пита-тель; 7 – штырь; 8 – стержень; 9 – полость формы; 10 – формовочная смесь; 11 – ве-нтиляционные каналы.
Модель литниковой системы изготовляемая по своим чертежам из формовочных смесей устанавливается на основной модели отливки, а после операции формовки удаляется вме-сте с основной моделью, в результате чего формируются показанные выше каналы и по-лости.
Модельные плиты формируют разъем литейной формы, на них закрепляют части модели. Их используют для изготовления как опочных так и безопочных полуформ. Для машин-ной формовки применяют координатные модельные плиты и плиты со сменными вклады-шами (металлическая рамка плюс металлические или деревянные вкладыши).
Кроме сказанного существует еще много специального оборудования и инструмен-та, который используется для приготовления формовочной смеси, заполнения ею опоки с моделью, подрезания при необходимости части формовки, заливки металла в литниковую систему, остывания отливки и т.д.
Материалы, применяемые для изготовления разовых литейных форм и стержней, делятся на исходные формовочные материалы и формовочные смеси; их масса равна в среднем 5—6 т на 1 т годных отливок в год. При изготовлении формовочной смеси ис-пользуют отработанную формовочную смесь, выбитую из опок, свежие песчано-глинис-тые или бентонитовые материалы, добавки, улучшающие свойства смеси, и воду. В стерж-невую смесь обычно входят кварцевый песок, связующие материалы (масло, смола и др.) и добавки. Приготовление смеси производят в определённой последовательности на сме-сеприготовительном оборудовании; ситах, сушилах, дробилках, мельницах, магнитных сепараторах, смесителях и т. п.
Затвердевшие отливки обычно выбивают на вибрационных решётках или коромыслах. При этом смесь просыпается через решётку и поступает в смесеприготовительное отделение на переработку, а отливки — в очистное отделение. При очистке отливок с них удаляют пригоревшую смесь, отбивают (отрезают) элементы литниковой системы и зачищают заливы сплава и остатки литников. Эти операции проводят в галтовочных барабанах, дробеструйных и дробемётных установках. Крупные отливки очищают гидравлическим способом в специальных камерах. Обрубку и зачистку отливки осуществляют пневматическими зубилами и абразивным инструментом. Отливки из цветных металлов обрабатывают на металлорежущих станках.
Кокильное литье.
Особенность литья в кокиль состоит в многократном использовании металлической формы (кокиля). Высокая прочность материала металлической формы позволяет более точно выполнять рабочие полости формы, что обеспечивает высокое качество литой поверхности. Благодаря высокой теплопроводности формы отливка быстро затвердевает.
К числу преимуществ литья в кокиль относится также резкое (по сравнению с литьем в песчаные формы) сокращение механической обработки отливок, сокращение (а во многих случаях и полное исключение) расхода формовочных материалов.
К недостаткам технологии относятся высокая стоимость металлической формы, плохая заполняемость тонкостенных отливок с поднутрениями, опасность возникновения трещин на отливках.
Металлическая форма (рис. 9.10) обычно состоит из двух полуформ 5, которые фиксируются штырями (фиксаторами) 3 и перед заливкой металла закрепляются замками 4. Питание отливки осуществляется прибылями ;, вентиляция формы происходит через выпоры 2 и специальные вентиляционные пробки.
Применяют и неразъемные металлические формы — так называемый вытряхной кокиль (рис. 911).
Перед заливкой на рабочую поверхность формы наносят слой огнеупорного покрытия, который предохраняет
форму от резкого термического удара при заливке и от опасности схватывания металла отливки
с формой.
В состав огнеупорного покрытия при изготовлении стальных и чугунных отливок входят: пылевидный кварц, графит, огнеупорная глина, жидкое стекло. Для медных сплавов применяется графитовый порошок, замешанный на вареном масле или на его аналогах. Для алюминиевых сплавов используют окись цинка, прокаленный асбест в смеси с жидким стеклом, для магниевых — тальк, борную кислоту и жидкое стекло.
Затем форму подогревают до температуры не ниже 200 ° С. Температура подогрева зависит от состава заливаемого сплава и толщины
стенок отливки.
Основное требование, предъявляемое к материалу формы,— высокая стойкость к термическому удару, возникающему при заливке металла. Формы для стальных и чугунных отливок изготавливают из легированного чугуна, для алюминиевых и магниевых — из серого перлито-ферритного чугуна.
Одной из разновидностей рассматриваемой технологии является литье в облицованный кокиль (литье в металлопесчаные формы), которое лишено недостатков оболочкового и кокильного литья, но совмещает в себе их достоинства.
Облицованный кокиль обладает высокой трещиностойкостью, податливостью. Он обеспечивает высокую точность отливки. Расход дорогостоящего формовочного материала минимален по сравнению с оболочковым литьем.
Для изготовления облицованной металлической формы (рис. 9.12) в пространство между рабочей поверхностью кокиля и металли- ? ческой модели отливки пескострельным способом вдувается плакированная песчано-смоляная смесь (2,5—3% пульвербакелита). За счет тепла кокиля и модели, нагретых до 200—220°С, происходит упроч-
нение смеси и образование облицовки обычно толщиной 3—5 мм. Полости в отливках выполняют при помощи обычных или оболочковых стержней.
Считается, что литье в кокиль экономически целесообразно при серийном и массовом производстве. Поэтому для художественного литья технология малоперспективна. Этим методом, очевидно, стоит изготавливать литые изделия простой конфигурации при большой потребности в них.
9.5.ЛИТЬЕ ПО ГАЗИФИЦИРУЕМЫМ МОДЕЛЯМ
В отличие от других методов литья, предусматривающих удаление модели перед заливкой металла тем или иным способом, при литье по газифицируемым моделям (моделям из пенопласта) могут быть созданы условия, позволяющие не удалять модель из формы перед заливкой. В некоторых случаях модели из пенопласта перед заливкой металла удаляются из формы путем выжигания, возгонки, растворения и т. д.
Благодаря сравнительной простоте механической обработки полистирола и изготовления моделей из этого материала литье по газифицируемым моделям нашло применение для изготовления художественных отливок. Эту технологию целесообразно использовать, когда необходимо изготовить единичный экземпляр несложной по конфигурации отливки, например фирменной доски, различных накладок с простым орнаментом и т. п.
Для изготовления моделей используют гранулы полистирола, которые готовят путем полимеризации стирола с одновременным введением в состав гранул низкокипящих компонентов. Это позволяет в дальнейшем при нагреве гранул до 80—100 °С получить пористый полистирол.
Выпускаемый отечественной промышленностью суспензионный полистирол имеет следующие характеристики:
Влажность, % ......................... 1,0—4,5
Содержание мономера, % .................. 0,25—1,0
Содержание порообразователя, % ............. 4,0—4,5
Насыпная плотность, г/л ................... 20,0—50,0
Гранулометрический состав (остаток на сите № 1),% . . 10,0—50,0
Одной из важных характеристик гранул суспензионного полистирола, определяющей его свойства и режим переработки, является молекулярная масса. С увеличением молекулярной массы повышается механическая прочность и теплостойкость полистирола. Молекулярная масса может составлять от 30 000 до 60 000.
Для изготовления литейных моделей гранулы полистирола, как правило, подвергаются предварительному подвспениванию — нагреву, который сопровождается ростом гранул. Предварительным процесс называют потому, что его прерывают и продолжают в дальнейшем при оформлении моделей в пеноформах. При вторичном нагревании гранулы, расширяясь, заполняют все промежутки и пустоты в пеноформе и спекаются между собой под влиянием возникшего давления. В качестве источника нагрева используются горячая вода, водяные растворы солей, паровоздушная смесь, токи высокой частоты, горячий воздух.
Изготовление литейных моделей методом вспенивания в пеноформах осуществляется в основном при серийном и массовом производстве.
При индивидуальном производстве модели изготавливают путем механической обработки плит и блоков, поставляемых промышленностью.
Механическая обработка пенополистирола может производиться на деревообрабатывающем оборудовании. Пенополистирол хорошо обрабатывается проволокой, нагреваемой электрическим током.
Соединение отдельных элементов литейных моделей осуществляется склеиванием, сваркой и спеканием токами высокой частоты.
Применяются различные клеи, которые не разрушают полистирол, не влияют на газификацию модели и на химический состав металла, а также легко выгорают.
Формовка моделей может осуществляться различными способами: трамбованием, встряхиванием, вибрацией. При этом используют пес-чано-глинистые, жидкостекольные, самотвердеющие, цементные смеси. Одним из преимуществ рассматриваемой технологии является возможность формовки в сухой песок, не содержащий связующего. При этом целостность формы сохраняется за счет того, что песок удерживается металлом, замещающим в форме модель, и парами стирола, которые, проникая в форму, скрепляют между собой частички песка.
При заливке металла пенополистирол вначале быстро расплавляется, затем газифицируется и воспламеняется. Горение паров стирола сопровождается выделением копоти и продуктов разложения модели. При литье в закрытую форму, т. е. без доступа воздуха, горение не происходит. Пенополистирол только плавится и газифицируется, а пары стирола, проникая в форму, конденсируются в ней.
К числу недостатков литья по газифицируемым моделям кроме выделения сажи и паров стирола можно отнести науглероживание отливок. Так, в отливках из стали 40 с толщиной стенок 106 мм концентрация углерода на глубине 4 мм может достигать 0,8%.
9.6. ЛИТЬЕ НА ЗАМОРАЖИВАЕМОМ СВЯЗУЮЩЕМ
Одним из прогрессивных методов художественного литья, который еще не нашел широкого применения, но обладает рядом преимуществ перед другими технологиями, является изготовление литых изделий в керамических оболочках на замораживаемом связующем в виде водной суспензии.
Технология изготовления литейных форм путем предварительного замораживания водной суспензии основана на известном явлении коагуляции гидрозолей оксидов металлов при охлаждении до температур ниже точки замерзания. Суспензия состоит из твердых частичек кремнезема с гидратированной поверхностью и свободной воды (рис. 9.13, а)
Замораживание включает две стадии.
На первой стадии происходит замораживание свободной воды. В процессе роста кристаллов льда происходит сжатие твердой фазы. В результате формируется структура коагуляционного типа. Твердые частицы находятся в дальнем взаимодействии. Их сближению препятствует расклинивающее действие гидратных оболочек. Замораживание носит обратимый характер: при нагревании система возвращается в жидкое состояние.
Вторая стадия начинается с момента достижения системой температуры замерзания воды, входящей в состав гидратных оболочек. Вымораживается главным образом вода, адсорбированная физически, и вода
гидроксильных групп, связанных водородной связью. Это снижает расклинивающее действие гидратных оболочек. Снижение расклинивающего действия и одновременный рост давления за счет увеличения объема замерзшей воды сближают частицы твердой фазы. Они вступают в ближнее взаимодействие или даже непосредственный контакт. Формируется структура конденсационного типа, неспособная к регид-ратации (рис. 9.13, б)
Изготовленная таким способом смесь после термической сушки и обжига сохраняет свою форму и размеры.
Технологический процесс состоит из следующих операций: приготовление суспензии (шликера), подготовка модельной оснастки, заполнение оснастки суспензией, замораживание керамической оболочки, отделение керамической оболочки, сушка и прокаливание оболочки.
Суспензию готовят двумя способами — мокрым помолом огнеупорного материала или смешением мелкодисперсного огнеупора в гидрозоле диоксида кремния.
Мокрый помол производится в шаровых мельницах. В результате помола происходит гидратация свежеобразованных поверхностей огнеупора, намол коллоидных фракций и частичное растворение кремнезема в воде.
Смешение желательно проводить в быстроходных смесителях.
При литье на замораживаемом связующем используется огнеупорный материал, применяемый при литье по выплавляемым моделям. Гидрозоль SiCb должен содержать не менее 10% твердой фазы (гидрозоль производит химический завод им. Карпова в г. Менделеевске).
Керамические оболочки изготавливают или неразъемными по ледяным моделям, или в постоянных пресс-формах.
Постоянные пресс-формы предварительно охлаждают до температуры —25...—35 °С. Материалом пресс-формы может служить алюминиевый сплав Д16. По конструкции предпочтительны массивные пресс-формы с внешним постоянным теплообменником.
Охлажденную модельную оснастку заполняют суспензией свободной заливкой или под избыточным давлением. Второй вариант реализуется на установках вакуумного всасывания, с поршневым давлением или с низким газовым давлением.
Замораживание производится в пресс-форме при температуре не выше —20° С. При этом должны соблюдаться условия направленного затвердевания, поскольку суспензия при замерзании увеличивает свой объем на 3—4 %.
Ледяные модели вытапливают в потоке нагретого осушенного воздуха при температуре не выше 200 ° С.
После удаления модели керамическая оболочка поступает в печь для сушки и прокаливания. При загрузке оболочки температура в печи должна быть не выше 500 ° С. Затем оболочка нагревается с печью до температуры 800—9ОО°С, выдерживается при этой температуре при-
близительно в течение часа, после чего охлаждается в печи до 300— 400 "Си далее на воздухе.
Литьем в керамических оболочках на замораживаемом связующем можно изготавливать мелкие ювелирные отливки массой несколько грамм и более тяжелые отливки — массой до 10 кг.
Основные преимущества технологии — экологическая безопасность, относительная простота и дешевизна литейных материалов.
Литье под давлением.
Литье под давлением является одним из высокопроизводительных способов изготовления отливок, обеспечивающим высокое качество поверхности.
Расплавленный металл заливается в камеру прессования (рис. 9.4) специальной машины, а затем под действием прессующего поршня 2, перемещающегося в этой камере, через литниковые каналы заполняют с высокой скоростью полость формы. Затвердевание металла происходит под высоким давлением. По окончании затвердевания отливки сначала извлекаются стержни 3, затем форма раскрывается гидроцилиндром, и толкатель 4 удаляет отливку из пресс-формы.
Литьем под давлением обычно изготавливают отливки из алюминиевых, цинковых, магниевых и медных сплавов. Масса отливок варьируется от нескольких граммов до нескольких десятков килограммов.
Скорость впуска жидкого металла в пресс-форму колеблется от 0,5 до 120 м/с, а конечное давление на металл может составить до 500 МПа. Форма заполняется за десятые, а особо тонкостенные отливки — за сотые доли секунды. Это позволяет, несмотря на высокую скорость охлаждения металла в форме, изготавливать отливки с очень тонкими стенками.
Машины для литья под давлением имеют или горячую, или холодную камеры прессования. Горячая камера располагается в плавильном тигле и сообщается специальным каналом с пресс-формой (рис. 9.5). Холодную камеру заполняют вручную. Машины с холодной камерой прессования (см. рис. 9.4) способны развивать несколько более высокое давление на жидкий металл.
К числу недостатков литья под давлением можно отнести: высокую стоимость пресс-форм, трудность получения отливок со сложными поверхностями, опасность возникновения трещин на отливках, появление в отливках воздушно-газовой пористости.
Изготовление художественных отливок литьем под давлением можно считать малоперспективным. Этот метод может пригодиться для массового производства тонкостенных отливок из цветных сплавов сравнительно простой конфигурации.
Одной из разновидностей рассматриваемой технологии является литье под низким давлением (рис. 9.6). Тигель с жидким металлом 5 герметически закрыт крышкой 2, в которую вмонтирован ме-таллопровод 4. Металлопровод погружен в металл на глубину 40—50 мм от дна тигля. Песчаную форму 1 устанавливают на крышке и соединяют с металлопроводом.
Воздух или инертный газ закачивается под давлением до 0,1 МПа внутрь тигля и давит на зеркало жидкого металла. Под действием избыточного давления металл поступает в форму со скоростью, регулируемой давлением. По окончании заполнения формы и затвердевания отливки полость камеры соединяют с атмосферой, и незатвердевший металл из металлопровода стекает в тигель.
Литьем под низким давлением изготавливают отливки из алюминиевых и магниевых сплавов, реже — из медных сплавов при серийном и массовом производстве.
Одним из существенных преимуществ метода является возможность регулировать скорость потока заполнения формы, что важно для улучшения качества тонкостенных крупногабаритных отливок.
Специализированное оборудование для литья под низким давлением широкого распространения не получило, так что возможность его использования для художественного литья маловероятна.
9.3. ЦЕНТРОБЕЖНОЕ ЛИТЬЕ
При центробежном литье заполнение формы жидким металлом и его кристаллизация происходят под воздействием центробежных сил. Эту технологию в машиностроении используют в основном для изготовления отливок, которые являются телами вращения (кольца, втулки, гильзы, трубы, вальцы и т. п.). При этом преследуют цели обеспечить лучшую заполняемость формы, получить более плотную отливку, изготовить отливки из сплавов с низкой жидкотекучестью. Для изготовления фасонных отливок центробежный способ применяется сравнительно редко, за исключением литья тонкостенных деталей из титановых сплавов.
Литые ювелирные изделия изготавливают исключительно центробежным способом.
Рассмотрим, какие силы действуют на металл при центробежной заливке.
Из гидравлики известно, что напряженность поля центробежных сил q определяется центробежной силой, приходящейся на единицу объема вращающегося металла, и выражается формулой
шгт
q-p—.
где р — плотность металла, г/см ; ш — угловая скорость вращения, с"1; г — радиус вращения произвольной точки, см; д — ускорение силы тяжести (981 см/с2).
Согласно принципу эквивалентности воздействие центробежных сил на какую-либо систему физически тождественно действию сил тяжести. На этом основании действующие на металл центробежные
силы можно заменить силами тяжести равной величины и того же направления, а сам металл считать соответственно утяжелившимся. На том же основании величину g можно рассматривать как плотность вращающегося металла. Величину q называют эффективной плотностью, а отношение G = w гт/д, являющееся коэффициентом пропорциональности между величинами р и q называют гравитационным коэффициентом.
Численное значение гравитационного коэффициента при центробежном литье колеблется от нескольких единиц (при литье фасонных отливок) до нескольких сотен (при изготовлении полых цилиндров в металлических формах).
В соответствии с положениями гидравлики удельное давление на стенку сосуда, развиваемое вращающейся в нем жидкостью, определяется уравнением
,-£,г>-,Ь
где г и т I — соответственно наружный и внутренний радиусы отливки. Из этого уравнения следует, что во вращающемся металле давление изменяется пропорционально квадрату расстояния рассматриваемой точки от оси вращения и что на свободной поверхности металла (г) при любой скорости вращения избыточное давление равно нулю.
Центробежные силы увеличивают развитие ликвационных процессов особенно если компоненты сплавов взаимно нерастворимы и не образуют друг с другом ни эвтектических смесей, ни химических соединений. Например, в свинцовистой бронзе при неправильно назначенных технологических режимах ликвация проявляется настолько резко что весь содержащийся в сплаве свинец сосредоточивается на наружной поверхности. Если же компоненты в сплаве взаимно растворимы, то процесс ликвации в таких сплавах ограничивается обогащением внутренних слоев отливки менее плотными структурными составляющими и примесями.
Во внутренних слоях толстостенных чугунных отливок наблюдается повышенное содержание свободного углерода, сернистого марганца, фосфидной эвтектики. В стальных отливках концентрируются оксиды, нитриды, силикатные включения. Внутренняя зона отливок из медных сплавов часто обогащается оловом, цинком, алюминием, кремнием.
Для центробежного литья применяются машины с горизонтальной (рис 9 7) и вертикальной (рис. 9 8) осями вращения.
Сравнительно мелкие цилиндрические отливки, как правило, изготавливают на шпиндельных машинах с горизонтальной осью вращения, форму крепят на шпинделе консольно.
Массивные отливки, например артиллерийские стволы, получают на роликовых машинах.
В машинах с вертикальной осью вращения исключается применение заливочных устройств, которые для машины с горизонтальной осью необходимы.
На рис. 9.9 показана схема изготовления фасонных отливок центробежным способом в металлических (а) и песчаных (б) формах.
Дата добавления: 2018-05-12; просмотров: 3654; Мы поможем в написании вашей работы! |
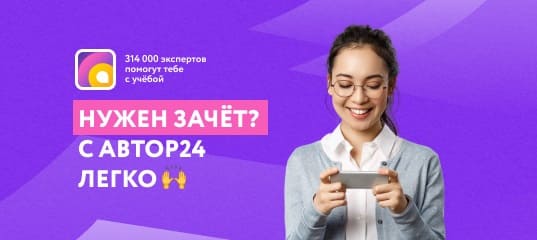
Мы поможем в написании ваших работ!