Сушность и технология процесса волочения.
Волочение. Сущность и схема волочения.
Исходными заготовками для волочения служат прокатанные или прессованные прутки и трубы из стали, цветных металлов и их сплавов.
Волочение труб можно выполнять без оправки (для уменьшения внешнего диаметра) и с оправкой (для уменьшения внешнего диаметра и толщины стенки). На рис. 3.16, а показана схема волочения трубы / на короткой удерживаемой оправке 3. В этом случае профиль полученной трубы определяется зазором между волоком 2 и оправкой 3.
Поскольку тянущая сила, приложенная к заготовке, необходима не только для деформирования металла, но и для пре-" одоления сил трения металла об инструмент, эти силы трения стараются уменьшить применением смазки и полированием отверстия в волоке.
Волочением обрабатывают различные марки стали, цветные металлы и их сплавы. Сортамент изделий, изготовляемых волочением, очень разнообразен: проволока диаметром 0,002 ... 5 мм и фасонные профили (рис. 3.16, б). Поскольку волочение производят в условиях холодной деформации, оно обеспечивает точность размеров, низкую шероховатость поверхности, получение очень тонкостенных профилей. Волоку изготовляют из инструментальных сталей, металлокерамических сплавов и технических алмазов. Волочение производят на барабанных и цепных волочильных станах. Барабанные станы (рис. 3.17) служат для волочения проволоки, труб небольшого диаметра, наматываемых в бунты. Исходную заготовку в виде бунта укладывают на барабан. Предварительно заостренный конец проволоки пропускают через отверстие волоки и закрепляют на барабане, который приводится во вращение от электродвигателя через редуктор и зубчатую передачу. На цепных станах тянущее устройство совершает прямолинейное возвратно-поступательное движение. Такие станы применяют для волочения прутков и труб, которые нельзя наматывать в бунты.
|
|
33. Свободная ковка. Сущность. Область применения. Основные операции свободной ковки.
Процесс ковки состоит из чередования в определенной последовательности основных и вспомогательных операций. Каждая операция определяется характером деформирования и применяемым инструментом. К основным операциям ковки относятся осадка, протяжка, прошивка, отрубка, гибка.
Осадка - операция уменьшения высоты заготовки при увеличении площади ее поперечного сечения. Осаживают заготовки между бойками или подкладными плитами. Разновидностью осадки является высадка, при которой металл осаживают лишь на части длины заготовки. Протяжка - операция удлинения заготовки или ее части за счет уменьшения площади поперечного сечения. Протяжку производят последовательными ударами или нажатиями на отдельные участки заготовки, примыкающие один к другому, с подачей заготовки вдоль оси протяжки и поворотами ее на 90° вокруг этой оси. При каждом нажатии уменьшается высота сечения, увеличиваются ширина и длина заготовки. Протяжка имеет ряд разновидностей. Разгонка - операция увеличения ширины части заготовки за счет уменьшения ее толщины. Протяжка с оправкой - операция увеличения длины пустотелой заготовки за счет уменьшения толщины ее стенок. Раскатка на оправке - операция одновременного увеличения наружного и внутреннего диаметров кольцевой заготовки за счет уменьшения толщины ее стенок. Прошивка - операция получения полостей в заготовке за счет вытеснения метала. Прошивкой можно получить сквозное отверстие или углубление (глухая прошивка). Инструментом для прошивки служат прошивни сплошные и пустотелые; последними прошивают отверстия большого диаметра. При сквозной прошивке сравнительно тонких поковок применяют подкладные кольца. Отрубка - операция отделения части, заготовки по незамкнутому контуру путем внедрения в заготовку деформирующего инструмента - топора. Гибка - операция придания заготовке изогнутой формы по заданному контуру. Этой операцией получают угольники, скобы, крючки, кронштейны и т.п. Гибка сопровождается искажением первоначальной формы поперечного сечения заготовки и уменьшением его площади в зоне изгиба, называемым утяжкой. Оборудование для ковки выбирают в зависимости от режима ковки данного металла или сплава, массы поковки и ее конфигурации. Необходимую мощность оборудования обычно определяют по приближенным формулам или справочным таблицам. Ковку выполняют на ковочных молотах и ковочных гидравлических прессах. Молоты - машины динамического, ударного действия. Продолжительность деформации на них составляет тысячные доли секунды. Металл деформируется за счет энергии, накопленной подвижными (падающими) частями молота к моменту их соударения с заготовкой. Гидравлические прессы – машины статического действия; продолжительность деформации на них может составлять от единицы до десятков секунд. Металл деформируется приложением силы, создаваемой с помощью жидкости (водяной эмульсии или минерального масла), подаваемой в рабочий цилиндр пресса.
|
|
|
|
Классификация видов сварки.
СВАРКА - получение неразъемных соединений посредством установления межатомных связей между соединяемыми частями при их нагревании и (или) пластическом деформировании
|
|
Сварное соединение – неразъемное соединение, выполненное сваркой.
Электрическая дуга (сварочная дуга) - мощный устойчивый электрический разряд в газовой среде, образованной между электродами, либо между электродами и изделием. Сварочная дуга характеризуется выделением большого количества тепловой энергии и сильным световым эффектом. Она является концентрированным источником теплоты и применяется для расплавления основного и присадочного материалов.
Электрод — металлический или неметаллический стержень, предназначенный для подвода тока к сварочной дуге.
Основной металл- металл подвергающихся сварке соединяемых частей.
Присадочный металл - металл для введения в сварочную ванну в дополнение к расплавленному основному металлу.
ПОЛУЧЕНИЕ СВАРНОГО СОЕДИНЕНИЯ
Для получения сварного соединения необходимо выполнить следующие основные условия:
1. Зачистить соединяемыми поверхностями, т.е. освободить связи поверхностных атомов от атомов кислорода, водорода и азота, находящихся в атмосфере.
2. Активировать поверхностные атомы, т.е. сообщить им дополнительную энергию (энергию активации).
3. Сблизить соединяемые поверхности на расстояния, при которых между ними возможно атомно-молекулярное взаимодействие (для металлов эти расстояния сопоставимы с параметрами кристаллической решетки ~ 4·10-10м).
Сближению поверхностей до нужного расстояния препятствуют неровности поверхности, а также находящиеся на ней загрязнения и оксидные пленки. Для преодоления их влияния необходимо затратить энергию, которая при сварке передается свариваемым поверхностям двумя физическими процессами: нагревом и (или) давлением.
КЛАССИФИКАЦИЯ СВАРКИ
Сварка классифицируется по физическим, техническим и технологическим признакам.
I. Классификация сварки по физическим признакам.
1. В зависимости от агрегатного состояния вещества в зоне сварки различают:
1.1. Сварка плавлением - сварка, осуществляемая оплавлением сопрягаемых поверхностей без приложения внешней силы, при которой обычно, но не обязательно, добавляется расплавленный присадочный металл. Выполняется при температурах равных, или выше температуры плавления свариваемого металла. Сопровождается расплавлением свариваемых поверхностей.
1.2. Сварка давлением - сварка, осуществляемая приложением внешней силы и сопровождаемая пластическим деформированием сопрягаемых поверхностей, обычно без присадочного металла. Выполняется без нагрева или с нагревом до температур ниже температуры плавления свариваемого металла.
Без нагрева свариваются высокопластичные металлы (например:Cu; Al; Pb). Материалы, имеющие пониженную пластичность(например: сталь) нагреваются, с целью ее повышения, до температур термопластичного состояния (1000 1200 0 С ).
2. В зависимости от формы дополнительной энергии определяется класс сварки.
В зависимости от формы вводимой дополнительной энергии (энергии активации), используемой для образования сварного соединения, сварочные процессы делятся на 3 класса:
2.1. Термический класс - дополнительная энергия вводится в виде теплоты.
К этому классу относится сварка плавлением.
2.2. Термомеханический класс - дополнительная энергия вводится в виде теплоты и упруго-пластической деформации.
2.3. Механический класс - дополнительная энергия вводится только в виде упруго-пластических деформаций.
К термомеханическому и механическому классам относится сварка давлением.
3. В зависимости от энергоносителя определяется вид сварки.
Энергоноситель - физическое явление, при котором образуется необходимая для сварки энергия в результате передачи или в результате превращения внутри детали(ей).
В зависимости от используемого при сварке энергоносителя различают следующие виды сварки: 3.1. Энергоноситель - электрическая дуга.
Дуговая сварка - сварка плавлением, при которой нагрев осуществляется электрической дугой.
К этим видам сварки относятся: ручная дуговая сварка плавящимся покрытым электродом, дуговая сварка под флюсом, дуговая сварка в защитном газе плавящимся и неплавящимся электродом, дуговая сварка самозащитной порошковой проволокой, плазменная сварка.
3.2. Энергоноситель – газ
Газовая сварка - сварка плавлением, при которой для нагрева используется теплота горения горючего газа или смеси горючих газов и кислорода.
К этим видам сварки относится, например, ацетиленокислородная сварка, газопрессовая сварка.
3.3. Энергоноситель – излучение
К этим видам сварки относятся: лазерная сварка, электронно-лучевая сварка.
3.4. Энергоноситель - электрический ток
Электрошлаковая сварка - сварка плавлением, при которой используют теплоту, выделяющуюся в вылете плавящегося электрода или электродов и в токопроводящей шлаковой ванне при прохождении тока. При этом металлическая ванна и шлаковая ванна удерживаются охлаждаемыми ползунами, перемещающимися вверх по мере выполнения шва
Контактная сварка - сварка давлением, при которой нагрев, необходимый для сварки, создается электрическим током, проходящим через зону сварки.
Зона сварки - зона детали или деталей, где сварка выполняется или выполнена.
К этим видам сварки относятся: точечная контактная сварка, стыковая контактная сварка, шовная контактная сварка, конденсаторная сварка, высокочастотная контактная сварка, индукционная сварка.
3.5. Энергоноситель - движение массы
К этим видам сварки относятся: холодная сварка, ударная сварка (сварка взрывом), сварка трением, ультразвуковая сварка.
3.5. Прочие источники энергии
К этим видам сварки относятся: диффузионная сварка, сварка прокаткой
II. Классификация сварки по техническим признакам.
1. В зависимости от способа защиты зоны сварки сварного соединения или всего изделия от влияния атмосферы различают:
1.1. Без защиты (например: лазерная сварка в воздухе)
1.2. С газошлаковой защитой (например: ручная дуговая сварка плавящимся покрытым электродом, дуговая сварка под флюсом)
1.3. Со шлаковой защитой (например: электрошлаковая сварка)
1.4. С газовой защитой (например: сварка в защитных газах)
1.5. С вакуумной защитой (например: электронно-лучевая сварка)
2. В зависимости от непрерывности процесса сварки различают:
2.1. Сварка в непрерывном режиме
2.2. Сварка в импульсном режиме
2.3. Сварка в импульсно-периодическом режиме
3. В зависимости от степени механизации различают:
3.1. Ручная сварка - сварка, при которой электрододержатель, ручной сварочный пистолет или горелка управляются вручную.
3.2. Частично механизированная сварка - ручная сварка, при которой подача проволоки механизирована
3.3. Полностью механизированная сварка - сварка, при которой все главные операции (исключая погрузку-разгрузку деталей) механизированы
3.4. Автоматическая сварка - сварка, при которой все операции механизированы
III. Классификация сварки по технологическим признакам.
Технологические признаки классификации устанавливаются для каждого вида сварки отдельно. Например, вид дуговой сварки может быть классифицирован по следующим признакам:
род тока; полярность сварочного тока; вид сварочной дуги; вид электрода; степень механизации.
Технические и технологические признаки определяют способ сварки.
Технические и технологические признаки сварки
Признаки способа сварки
Род тока:
Постоянный (рис. 1С)
Переменный (рис. 1С)
Полярность постоянного сварочного тока
Прямая (рис. 2С)
Обратная (рис. 3С)
Вид сварочной дуги
Дуга прямого действия (рис. 5С, а;б).
Дуга косвенного действия (рис. 5С, в).
Трехфазная дуга (рис. 5С, г).
Вид электрода
Плавящийся электрод (рис. 5С, а)
Неплавящийся электрод с использованием присадочного материала (с присадкой) (рис. 5С, б) и без него (без присадки)
Покрытый электрод - плавящийся электрод для дуговой сварки, имеющий на поверхности покрытие, адгезионно связанное с металлом электрода .
Электродная проволока - сварочная проволока для использования в качестве плавящегося электрода.
Степень механизации
Ручная сварка - сварка, выполняемая вручную
Механизированная сварка - сварка, при которой подача плавящегося электрода или присадочного металла, или относительное перемещение дуги и изделия выполняются с помощью механизмов.
Автоматическая сварка - сварка, при которой возбуждение дуги, подача плавящегося электрода или присадочного металла и относительное перемещение дуги и изделия осуществляются механизмами без непосредственного участия человека, в том числе и по заданной программе
Сварка на переменном токе и постоянном токе прямой и обратной полярности.
В зависимости от рода тока различают сварку на переменном токе и сварку на постоянном токе
Рис. 1С Схема сварки на переменном и постоянном токе
Сварка на переменном токе ( ~ );
Сварка на постоянном токе ( — ).
При сварке на постоянном токе дуга горит устойчивее, чем на переменном.
При сварке на постоянном токе различают сварку на прямой и обратной полярности
Рис. 2С Схема сварки на постоянном токе прямой полярности
Прямая полярность - полярность, при которой электрод присоединяется к отрицательному полюсу источника питания дуги, а объект сварки - к положительному.
Рис. 3С Схема сварки на постоянном токе обратной полярности
Обратная полярность - полярность, при которой электрод присоединяется к положительному полюсу источника питания дуги, а объект сварки - к отрицательному.
Влияние рода тока и полярности на глубину проплавления основного металла (рис. 4С)
Рис. 4С. Влияние рода тока и полярности на глубину проплавления основного металла
h – глубина проплавления основного металла
Глубина проплавления - наибольшая глубина расплавления основного металла в сечении шва или наплавленного валика.
При сварке на постоянном токе прямой полярности глубина проплавления h минимальна.
При сварке на постоянном токе обратной полярности глубина проплавления h на 40- 50% больше, чем на постоянном токе прямой полярности. При сварке на переменном токе глубина проплавления h на 15 - 20% меньше, чем при сварке на постоянном токе обратной полярности.
Сварка плавящимся и неплавящимся электродом.
Сварка дугой прямого и косвенного действия, сварка трехфазной дугой.
а
Дуга прямого действия – дуга 2, при которой объект сварки 3 включен в цепь сварочного тока.
Сварка плавящимся электродом (электрод расходуется в процессе сварки). При сварке плавящимся электродом формирование сварного шва происходит с участием как основного, так и электродного металла.
Плавящийся электрод для дуговой сварки - металлический электрод, включаемый в цепь сварочного тока для подвода его к сварочной дуге, расплавляющийся при сварке и служащий присадочным металлом.
Сварной шов - участок сварного соединения, образовавшийся в результате кристаллизации расплавленного металла или в результате пластической деформации при сварке давлением или сочетания кристаллизации и деформации.
б
Дуга прямого действия – дуга 2, при которой объект сварки 3 включен в цепь сварочного тока.
Сварка неплавящимся электродом (электрод не расходуется в процессе сварки) с использованием присадочного металла (6) и без него (с присадкой и без присадки).
Неплавящийся электрод для дуговой сварки - деталь из электропроводного материала, включаемая в цепь сварочного тока для подвода его к сварочной дуге и не расплавляющаяся при сварке.
При сварке неплавящимся электродом без присадки формирование сварного шва происходит только при участии основного металла. При сварке неплавящимся электродом с присадкой формирование сварного шва происходит с участием основного металла и материала присадки.
в
Дуга косвенного действия – дуга 4 горит между двумя электродами 1, а свариваемое изделие 3 не включено в сварочную цепь (используется при сварке неэлектропроводных материалов, а также при необходимости уменьшить глубину проплавления основного металла, например, при наплавке)
г
Трехфазная дуга - сварочная дуга, получающая питание от трехфазной силовой сети.
Трехфазная дуга 5 горит между двумя электродами 1, а также между каждым электродом и основным металлом 3.
Трехфазная дуга для сварки изделий значительных толщин имеет преимущества по сравнению с однофазной дугой. Производительность сварки трехфазной дугой в 2— 2,5 раза выше, чем производительность сварки однофазной дугой.
Рис. 5С Виды сварочной дуги и схемы сварки плавящимся и неплавящимся электродом:
а –дуга прямого действия (сварка плавящимся электродом); б –дуга косвенного действия; в –трехфазная дуга; г – дуга прямого действия (сварка неплавящимся электродом с присадкой); 1 – электрод; 2 – дуга прямого действия; 3 – основной (свариваемый) металл; 4 – дуга косвенного действия; 5 – трехфазная дуга; 6 – присадочный материал (присадка).
Дата добавления: 2018-05-12; просмотров: 879; Мы поможем в написании вашей работы! |
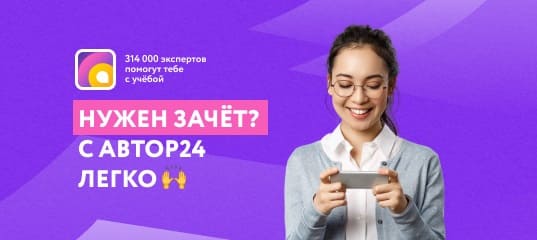
Мы поможем в написании ваших работ!