Расчет припусков. Методы определения припусков.
В.1Технология маш и приб строения – наука, занимающаяся изучением закономерностей процессов изготовления машин и приборов с целью использования результатов исследования для обеспечения выпуска машин и приборов заданного кол-ва при наимэкономич затратах. Машина – механизм, осуществляющая целесообразное движение для преобразования энергии. Изделие – предмет, подлежащий изготовлению на предприятии. Сборочная единица – часть изделия, которая собирается отдельно и в дальнейшем участвует в сборке как одно целое. Производственный процесс – совокупность всех действий людей и орудий производства, необходимых на данном предприятии для изготовления или ремонта выпускаемых изделий. Структура произв процесса:1)Подготовка и обслуживание средств производства. 2)Получение материалов, полуфабрикатов и их хранение. 3)Различные виды обработки. 4)Сборка изделий. 5)Транспортировка. 6)Контроль качества на всех стадиях производства. 7)Окраска, отделка, упаковка готовой продукции. Технологич процесс – часть произв процесса, содержащая целенаправленные действия по изменению и определению состояния предмета труда (единичный, типовой, групповой, маршрутный, операционный). Структура технология проц:1)Технологич операция (законченная часть технология процесса, сверление отверстия, нарезание резьбы). 2)Установы (выполнение операции при неизменном положении образца: обтачивание вала с двух сторон). 3)Позиция (обработка на многошпиндельных автоматах и полуавтоматах при вращении стола, приводящего деталь к разным инструментам).4)Переходы (Технологический – токарная операция, переход1 – подрезка торца, переход2 – точение канатки, переход3 – нарезка резьбы; Вспомогат – закрепление заготовки, смена инструмента). 5)Ходы (Рабочий – однократное перемещение инструмента относительно заготовки, сопровождается изменением формы, размера; Вспомогат – однократное перемещение инструмента относит заготовки, необходимого для подготовки рабочего хода). 6)Приём (установка детали, её закрепление и снятие, управление станком). В.2Стадии технической подготовки производства: 1)Конструкторская подготовка к производству (создание новых изделий с высокими параметрами качества в заданные сроки с наименьшими затратами). Этапы:1)Техническое задание (область применения изделия, основные требования, технические характеристики, показатели качества). 2)Техническое предложение (при разработке приложения целесообразно создавать изделия на основе анализа технического задания заказчика, производится оценка всех возможных вариантов создания изделия). 3)Эскизный проект (разработка первоклассного варианта будущей конструкции изделия). 4)Технический проект (разработка окончательного технического решения, выполняются расчёты на прочность, жёсткость). 5)Рабочий проект (разработка чертежей сборочных единиц, уточнение спецификаций). 2)Технологическая подготовка производства (разработка оптимального технологич процесса, который бы обеспечивал изготовление изделий заданного качества с мин затратами). 3)Календарное планирование (процесс изготовления изделия а установленные сроки при заданном объёме выпуска и затрат). В.3Тип производства – классификационная категория производства, выделяемая по признаку широты номенклатуры, регулярности, стабильности и объёма выпуска изделия. Типы производства: 1)Единичное производство (характеризуется широкой номенклатурой и малым объёмом выпуска одинаковых изготавливаемых изделий. Отсутствует подробная технологическая документация, операционные карты не разрабатываются, на рабочих местах обрабатываются разные заготовки деталей, исп универсальные станки, оборудования размещаются группами по видам станков, исп рабочими высокой квалификации). 2)Серийное: мелкосерийное, среднесерийное, крупносерийное (характериз ограниченной номенклатурой изделий и сравнительно большой объём выпуска. Изделия изготавливаются сериями, операции закреплены за определённым рабочим местом, технологич процесс построен по принципу разделения операций, исп универсальное и специализир оборудование, исп рабочие ср квалификации). 3)Массовое (характеризуется узкой номенклатурой и большим объёмом выпуска изделий. На рабочем месте выполняется постоянно 1операция, оборудование расположено в порядке выполнения операции, применяют высокопроизводительное специализированное оборудования, широко используется устройство для транспортировки заготовок вдоль поточной линии, низкая квалификация рабочих). На линии непрерывного поточного производства заготовки или сборочные узлы выпускаются через определённый промежуток времени – такт выпуска. В.4 Изделие – предмет производства, подлежащий изготовлению на предприятии. В зависимости от назначения делят на изделия основного и вспомогательного производства. Основного произв: изделия, предназначены для реализации. Вспомогат: изделия, предназначены для нужд предприятия. Изделия могут быть не специфицированными (не имеют составных частей) и специфицированные (2 и более частей). Виды изделий: 1)Деталь – изделие, изготовленное из однородного материала без применения сборочных операций (балка). 2)Сборочная единица (узел) – часть изделия, которая собирается отдельно и в дальнейшем участвует в сборке как одно целое. 3)Комплекс – 2 и более специфицированных изделия, не соединённых на предприятии сборочными операциями, но предназначены для выполнения взаимосвязи. 4)Комплект – 2 и более изделия не соединённых на предприятии сборочными операциями, представляет собой набор изделий, имеющих общее эксплуатационное назначение вспомогательного характера. Качество – совокупность свойств, обуславливающих её способность удовлетворять определённым потребностям в соответствии с назначением. Характеристики: работоспособность, надёжность, безотказность, долговечность, трудоёмкость. В.5 Точность изготовления детали – степень её соответствия всем требованиям рабочего чертежа, технич условиям. Погрешность изготовления – отклонение параметров реальной детали от заданных номинальных значениях. Допуск – разность предельных отклонений рассматриваемого параметра. Методы достижения точности: 1)Метод пробных ходов и замеров (устанавливается заготовка, режущим инструментом с участка заготовки снимается пробная стружка, после этого станок останавливается, делается пробный замер полученного размера, определяют величину его отклонения от чертежа и вносят изменения, затем вновь делают пробный ход, пробный замер и при необходимости вносят поправку. Т.о. устанавливают правильное положение инструментов относительно заготовке.После этого идёт обработка заготовки по всей её длине). 2)Метод автоматического получения размеров на построенных станках (станок настраивают т.о., чтобы требуемая точность достигалась автоматически, независимо от внимания и квалификации рабочего, например, при фрезеровании. Столб фрезеровального станка устроен так, чтобы были выдержены необходимые размеры. Такую настройку ведут методом пробных ходов и замеров, затем обрабатывают всю партию деталей без замеров. Точность размеров сохраняется одинаковой для всех заготовок). В.6 Виды погрешностей: 1)Систематические постоянные (погрешности, которые при обработке партий постоянны. Возникновение погрешности в следствии режущего инструмента, в результате погрешность настройки станка). 2)Систематические переменные (погрешности, которые в процессе обработки закономерно изменяются по времени, т.е. в зависимости от количества изготавливаемых изделий. Это погрешности, вызванные износом режущего инструмента и тепловые деформации изделия в период работы станка). 3)Случайная (погрешность, которая для заготовок данной партии имеет разные значения, причёт появление предсказать невозможно. Это изменение размера заготовки в результате колебаний припуска или неравномерная твёрдость поверхности). В.7В результате возникновения случайных погрешностей истинный размер каждой детали является случайной величиной, т.е. может иметь рассеивание. Причины, порождающие рассеивание размеров: 1)Вид обработки. 2)Погрешность установки. 3)Погрешность настройки. 4)Износ режущего инструмента. 5)Колебания температуры. 6)Прочие случайные погрешности. Общее рассеивание размеров детали: Общая погрешность обработки: В.8 Жёсткость технологической системы – способность этой системы оказывать сопротивление действию деформации. При обработке резанием жёсткость технологической системы принято выражать отношением радиальной составляющей силы резания суммарному смещению лезвия режущего инструмента, относит обрабатываемой поверхности: j=Py/y Податливость технологической системы – способность этой системы упруго деформироваться под воздействием внешних сил. Величина обратна жёсткости. 𝝎=1/j=y/Py В.9 Пути повышения жёсткости технологической системы: 1)Увеличение собственной жёсткости отдельных частей технологической системы за счёт правильного выбора из размеров, формы, материала. 2)Увеличение контактной жёсткости за счёт уменьшения шероховатости и волнистости сопрягаемых поверхностей. 3)Уменьшение общего числа звеньев технологической системы (податливость технологичсист определяется суммой податливостей, составляющей звенья). 4)Применение дополнительных регулируемых и самоустанавливающихся опор. В.10 В результате проведённых за последние годы исследований жёсткости станков, установлены фактические значения жёсткости и податливости. Методы оценки жёсткости: 1)Статический (жёсткость станка и отдельных узлов определяется при их нагружении статическими силами с помощью динамометра, а индикаторами измеряют сжатие узлов станка. При испытании дают ряд нагрузок, возрастающих от 0 до некоторого значения и по ним строят зависимость у=f(Py). Затем проводят разгрузку и строят разгрузочную кривую. Данные не точны. Это приводит при расчётах к занижению погрешностей обработки. Это объясняется тем, что на неработающем станке не учитываются толчки и вибрации, которые увеличивают деформацию системы, что снижает жёсткость). 2)Производственный (даёт более точные значении жёсткости. На станке обрабатывают заготовку, имеющую ступени при токарной обработке. Эти ступени принимаются в расчётах за исходную погрешность заготовки △исх.з. После обработки исх заготовки за 1раб ход на обработанной поверхности остаётся уступ, копирующий в уменьшенном виде погрешность этой заготовки и представляющий собой погрешность △обр.з. По величине уточнения ε=△исх.з/△обр.зопределяют жёсткость станка при его работе: В.11 Размерные цепи – совокупность размеров, расположенных по замкнутому контуру, и определяющих взаимное расположение поверхностей, осей поверхностей, одной или нескольких деталей сборочного соединения. Звенья – все размеры деталей, составляющие размерную цепь. Звенья, входящие в одну размерную цепь, обозначаются большой буквой с индексом. Для анализа размерной цепи строят схему. Линию 0-0 принимают за базу – начало отсчёта. Одно из направлений (слева направо) считают положительным, а противоположное – отрицательным. Учитывая это, пишут уравнение размерной цепи. Замыкающее звено – звено размерной цепи, получающееся при её построении. В одной размерной цепи может быть 1 замыкающее звено. Составляющие звенья – звенья, кроме замыкающего. Делятся на увеличивающие и уменьшающие. Увеличивающее звено – звено, с увеличение которого увеличивается замыкающее звено. Уменьшающее звено – звено, с увеличением которого уменьшается замыкающее звено. Схему размерной цепи можно строить, откладывая только номинальные размеры звеньев. Алгебраическая сумма номинальных размеров =0. Размерные цепи в зависимости от расположения звеньев делятся на: 1)Линейные (все размеры паралл между собой). 2)Плоские (звенья находятся в одной или нескольких паралл плоскостях, проецируются на 1 плоскость). 3)Пространственные (состоят из элементов, лежат не в паралл плоскостях, проецируются на 3 плоскости). В.12 При расчёте размерных цепей решают прямую и обратную задачу. Прямая задача: по заданным параметрам замыкающего звена определяют параметры составляющих звеньев. При этом по известным предельным отклонениям и допуску замыкающего звена находят исходные рассчитываемые допуски и предельные отклонения размеров составляющих звеньев. Обратная задача: по известным параметрам составляющих звеньев определяем параметры замыкающего звена. При этом по известным номинальным размерам и их предельным отклонениям, допускам составляющих звеньев находим тожсамое для замыкающего звена. В.13 В процессе изготовления машины возникают задачи соединения с требуемой точностью 2-х или большего кол-ва деталей. Такие же задачи возникают и при обработке заготовленных деталей в разных технологических системах, когда заготовку надо установить с заданной точностью на столе станка или в приспособлении. При этом положение любой точки обрабатываемой заготовки, если её рассмотреть в системе 3-х взаимно перпендикулярных осей, может быть описан 6-ю координатами: 3-мя линейными хуz и 3-мя углами поворота относит этих осей. Вопросы, связанные с обеспечением требуемого положения заготовок при их обработке на станках рассматривают в теории базирования. База–поверхность, сочетание поверхностей, линии и точки заготовки, детали, используемые для базирования. Известно, что для полного исключения подвижности твердого тела в пространстве необходимо лишить его шести степеней свободы: трех поступательных перемещений вдоль осей координат и трех вращений вокруг указанных осей.Поэтому многие задачи связанные с расчетом точности при базировании и установке возможно решать теоретически посредством наложения "связей". Под связями подразумеваются ограничения позиционного (геометрического) или кинематического характера, накладываемые на движение точек рассматриваемого тела (заготовки или детали). В технологии машиностроения позиционные связи предполагаются двухсторонними, т. е. лишающими тело возможности перемещения в обе стороны в направлении действия связи. Эти связи не зависят от времени и поэтому их считают стационарными и позиционными. В.14База – поверхность, сочетание поверхностей, линии и точки заготовки, детали, используемые для базирования. Классификация баз: 1)Технологические (установочные: основная, вспомогательная и измерительные). 2)Сборочные. 3)Конструктивные. Сборочная база – поверхность, которая определяет положение детали относительно др деталей в собранном узле или машине. Конструктивная база – совокупность поверхностей, линий, точек, от которых задаются размеры и положение др деталей при разработке конструкций. Установочная база – поверхности детали, которыми она устанавливается для обработки в определённом положении относительно станка или приспособления и режущего инструмента. Могут исп обработанные и необработанные поверхности. Бывает основной и вспомогательной. Основная установочная база – поверхность детали, которая служит для установки детали при обработке и сопрягается с другой деталью в совместно работающей собранной машине или оказывает влияние на работу данной детали в машине. Вспомогательная установочная база – поверхность детали, которая служит для её обработки и установки, не сопрягается с др деталью, совместно работающей в собранной работе и оказывает влияние на работу данной детали в машине. Измерительная база – поверхность, от которой при изменении производится непосредственный отсчёт разметов. В.161.Принцип совмещения баз. При назначении технологических баз для обеспечения более точной обработки необходимо совмещать измерительные и технологические базы в том числе использовать эти поверхности не только при обработки но и при сборки. 2.Принцип постоянства баз. При разработке технологических процессов необходимо стремиться к тому, чтобы одна и также поверхность (по возможности) была использована в качестве базы. Исключение составляют черновые базы (например, изготовление центровых отверстий). 3.Принцип последовательной смены баз. Если не удается разработать ТП (выполняемый при одной установке заготовки), тогда в качестве следующей базы необходимо использовать поверхность (ранее уже обработанную) точность которой должна быть выше. В.19Шероховатость поверхности – совокупность неровности с относительно малыми шагами на базовой длине. Волнистость поверхности – совокупность периодически чередующихся неровностей, у которых расстояния между смежными возвышенностями или впадинами превышает базовую длину. Разграничителем понятий шероховатости и волнистости явл отношение шага к высоте неровности. Для шероховатых пов-стей: Н<50, для волнистых: Н=50..1000. Нормирование и количественная оценка шероховатости пов-сти производится с помощью 3-х высотных параметров, 2-х шаговых параметров, параметра относительной длины профиля. Наибольшая высота неровностей Rmax– средняя величина шагов неровности профиля в пределах базовой длины. Средний шаг неровностей Sm – средняя величина шагов неровностей профиля в пределах базовой длины. Средний шаг в выступе профиляS – среднее значение шагов местных выступов профиля находится в пределах базовых элементов. Относительная опорная длина профиля tp – отношение опорной длины профиля к базовой длине
|
|
|
|
|
|
|
|
Классификация припусков.
Припуском называют слой материала, удаленный в процессе механической обработки заготовки для достижения требуемой точности и качества обрабатываемой поверхности.
Различают припуски промежуточные (Zi) и общие (Zобщ).
Промежуточный припуск — слой металла, который должен быть удален во время данной операции или данного перехода. Промежуточный припуск определяют как разность размеров заготовки, полученных на выполненном и предшествующем переходах.. При этом промежуточные припуски для наружных и внутренних поверхностей вращения (рис. 8.1) рассчитываются по следующим формулам:
А) 2Zi=di-1-diБ) 2Zi=di-di-1
где Zi— припуск на сторону; d- диаметр; i-1 – индекс для предшествующего перехода;i – индекс для выполняемого перехода.
Припуски могут быть несимметричными (на одну сторону) при изготовлении призматических деталей, и симметричные (на обе стороны) чаще всего на диаметр при обработке тел вращения.
Общий припуск определяют как разность размеров заготовки и готовой детали. Он равен сумме промежуточных припусков по всему технологическому маршруту механической обработки данной поверхности.
Общий припуск на обработку зависит от ряда факторов: масштаба (типа) производства, размеров и конструктивных форм заготовки, ее свойств, материала, вида (поковка, отливка и т.д.), жесткости, толщины дефектного поверхностного слоя, состояния оборудования, на котором ведут обработку.
Следует назначать оптимальные припуски с учетом конкретных условий обработки. Завышенные припуски приводят к излишнему расходу материала, возрастанию трудоемкости механической обработки, повышению эксплуатационных расходов станочной обработки (расход инструмента, электроэнергии и т.д.). Недостаточные припуски могут препятствовать исправлению погрешностей от предшествующей обработки и получению необходимой точности и шероховатости обработанной поверхности на выполняемой операции. Поэтому выбор общих и операционных припусков и допусков имеет большое технико-экономическое значение.
Правильно выбранный припуск обеспечивает устойчивую работу оборудования при достижении высокого качества и минимальную себестоимость продукции.
Расчет припусков. Методы определения припусков.
В машиностроении применяют 2 метода определения припусков: опытно-статический, расчетно-статический.
При использовании опытно-статического метода общие промежуточные припуски назначаю по таблицам, которые составлены на основании обобщения и систематизации экспериментальных результатов исследований промышленных предприятий. Основное преимущество этого метода можно считать экономию времени на определение припуска. Он позволяет определить размеры заготовок до разработки ТП. Недостатки: припуски назначаются без учета конкретных условий построения ТП, общие припуски назначают без учета схемы установки заготовки и погрешностей, предшествующей обработки.
Расчетно-аналитический метод базируется на анализе факторов, влияющих на припуски предшествующей и выполняемой операции ТП обработки поверхности. Метод предусматривает расчет межоперационных припусков, т.е. припусков по всем последовательно выполняемым технологическим операциям обработки данных поверхности заготовки, их суммируют для определения общего припуска на обработку поверхности и расчет промежуточных разметов, определяющих положение поверхности и размеры заготовки. Расчетной величиной является минимальный промежуточный припуск, достаточный для устранения на выполняемой операции погрешностей обработки и дефектов поверхностного слоя, полученных на пред
шествующей операции, а также компенсации погрешностей, возникающих на выполняемой операции.
При расчете минимального промежуточного припуска учитывают:
- шероховатость поверхности, подученную на предшествующем переходе;
- состояние и толщину поверхностного слоя материала заготовки, снимаемого в результате выполнения предшествующего перехода;
-пространственные отклонения расположения обрабатываемой поверхности относительно баз заготовки;
-погрешность установки при выполнении данного перехода.
Дата добавления: 2018-05-12; просмотров: 509; Мы поможем в написании вашей работы! |
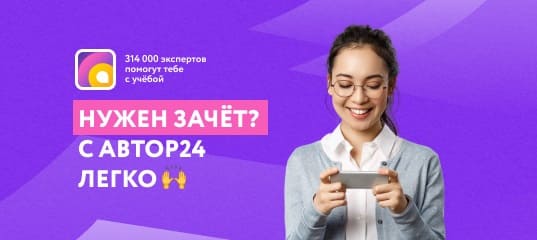
Мы поможем в написании ваших работ!