Наращивание цементного кольца за обсадной колонной
1) параметры глинистого и цементного растворов, использованных при первичном цементировании;
2) наличие и интенсивность поглощения в процессе бурения скважины;
Останавливают скважину и определяют динамику восстановления давления в межколонном пространстве.
Производят глушение скважины.
Шаблонируют эксплуатационную колонну до глубины на 100—200 м ниже расположения цементного кольца за обсадной колонной.
Устанавливают цементный мост над интервалом перфорации и по истечении срока ОЗЦ проверяют прочность цементного моста при разгрузке НКТ с промывкой.
При наличии зон поглощений проводят изоляционные работы для снижения их интенсивности.
Выбирают тип тампонажного материала в зависимости от интенсивности поглощения с учетом геолого-технических и температурных условий. В скважинах, в которых возможен гидроразрыв пласта, следует использовать облегченные тампонажные растворы.
При прямом тампонировании через специальные отверстия на заданной глубине в обсадной колонне простреливают отверстия, промывают скважину до полного удаления остаточного объема старого бурового раствора, закачивают расчетный объем тампонажного раствора, поднимают НКТ на 50-100 м и оставляют скважину на ОЗЦ. Определяют верхнюю границу цементного кольца за обсадной колонной. Разбуривают цементный стакан в обсадной колонне и проверяют ее на герметичность.
|
|
Обратное тампонирование применяют в случаях, когда над наращиваемым цементным кольцом находится интенсивно поглощающий пласт. Тампонажный раствор с закупоривающими наполнителями закачивают в заколонное пространство с устья.
Комбинированное тампонирование применяют в случаях, когда перед прямым тампонированием не удается восстановить циркуляцию из-за наличия в разрезе одной или нескольких зон поглощений. Первую порцию тампонажного раствора закачивают прямым способом через отверстия, а вторую — обратным.
В случае если установлена негерметичность обсадной колонны в интервале спецотверстий, производят дальнейшие работы по ликвидации негерметичности с применением стальных гофрированных пластырей.
Устранение негерметичности обсадной колонны
Тампонирование
Работы по устранению негерметичности обсадных колонн включают изоляцию сквозных дефектов обсадных труб и повторную герметизацию их соединительных узлов (резьбовые соединения, стыковочные устройства, муфты ступенчатого цементирования)
· Останавливают и глушат скважину.
· Проводят исследования скважины.
· Проводят обследование обсадной колонны.
· Выбирают технологическую схему проведения операции, тип и объем тампонажного материала.
|
|
· Ликвидацию каналов негерметичности соединительных узлов производят тампонированием под давлением.
· В случае достоверной информации о негерметичности резьбового соединения используют метод установки металлического пластыря.
Тампонирование негерметичных резьбовых соединений обсадных колонн.
· В качестве тампонирующих материалов используют фильтрующие полимерные составы, образующие газонепроницаемый тампонажный камень или гель.
· Использование цементных растворов для работ указанных выше запрещается.
В случае если в скважине межколонных проявлений не наблюдалось, а негерметичность выявлена при гидроиспытании, башмак НКТ устанавливают на 5—10 м выше искусственного забоя или цементного моста, расположенного над интервалом перфорации. В качестве тампонирующего материала используют гелеобразующие составы.
При не установленном интервале негерметичности обсадной колонны применяют метод тампонирования под давлением с непрерывной (или остановками) прокачкой тампонирующей смеси по затрубному пространству.
В случае, если в процессе эксплуатации наблюдались межколонные проявления, после отключения интервала перфорации башмак НКТ устанавливают на 200-300 м выше нижней границы предполагаемого интервала негерметичности.
|
|
В случае если величина межколонного давления больше 4 МПа, в качестве тампонирующих материалов допускается использование отверждающихся составов.
В фонтанирующих скважинах допускается применение извлекаемого полимерного состава.
Изоляцию сквозных дефектов обсадных колонн осуществляют, если:
· замена дефектной части колонны или перекрытие ее трубами меньшего диаметра технически невозможны;
· зона нарушения обсадной колонны расположена более чем на 500 м выше интервала перфорации. В этом случае устанавливают дополнительный цементный мост высотой не менее 5 м в интервале на 20—30 м ниже дефекта.
При наличии в колонне нескольких дефектов тампонирование каждого дефекта производят последовательно сверху вниз, предварительно установив под очередным нарушением на расстоянии от 20 до 30 м разделительный мост высотой не менее 5 м.
· При приемистости дефекта колонны более 3 м3/(ч • МПа) предварительно проводят работы по снижению интенсивности поглощения.
· При приемистости 0,5 м3/(ч • МПа) в качестве тампонажного материала используют полимерные материалы.
|
|
При тампонировании под давлением лишний объем тампонажного раствора из зоны дефекта не удаляют.
На период отверждения тампонажного материала скважину оставляют под избыточным давлением от 40 до 60% от достигнутого при продавливании тампонажного раствора.
Определяют местоположение установленного моста и разбуривают его, оставляя толщиной не менее 3 м над дефектом.
Перекрытие дефекта обсадной колонны трубами меньшего диаметра производят в случаях, если:
· замена дефектной части обсадной колонны технически невозможна;
· метод тампонирования не обеспечивает необходимой герметичности обсадной колонны;
· обсадная колонна имеет несколько дефектов, устранение которых технически невозможно или экономически нецелесообразно;
· по условиям эксплуатации скважины допускается уменьшение проходного сечения колонны.
Оценка качества работы:
· При испытании отремонтированного интервала газом межколонные проявления должны отсутствовать;
· качество РИР без отключения перфорированной зоны оценивают по результатам изменения межколонного давления при освоении и эксплуатации скважины;
· при определении показателя долговечности (среднего срока службы изолирующего тампона) устанавливают ежемесячный контроль за эксплуатацией скважин.
Установка стальных пластырей
В современной отечественной и зарубежной нефтедобывающей отрасли одним из эффективных методов ремонта скважин является установка стальных гофрированных пластырей на дефект обсадных колонн с использованием специальных транспортных устройств.
В отечественной практике известны устройства типа ДОРН – 1, ДОРН – 2, которые обеспечивают транспортировку и установку стальных пластырей на дефект в обсадных колоннах. В настоящее время создано и испытано устройство ДОРН – 3М, которое имеет принципиальное отличие от предыдущих конструкций. Установка стального пластыря производится по схеме сверху вниз. Это отличие позволяет следующее:
· исключить попадание твердых частиц между колонной и пластырем в процессе установки, следовательно повышается коэффициент успешности ремонта.
· Использовать пластыри с нулевыми и отрицательными периметрами.
· Устанавливать пластырь без осевых (растягивающих) нагрузок на инструмент
· Не применять левые переводники
· Работать с минимально необходимым давлением жидкости в системе, а значит, и минимальной радиальной нагрузкой на дорнирующую головку при проходах ее в пластыре, что обеспечивает благоприятные условия ремонта скважин
· Ликвидировать незначительные смятия обсадной колонны. В этом случае необходимо работать только дорнирующей головкой без пластыря.
Применять данное устройство для ремонта обсадных колонн предпочтительно на глубине 1000 м и более.
На рисунке 3.10.1 показано устройство для транспортировки и установки стального пластыря ДОРН – 3М
Рис 3.10.1
Устройство состоит из пяти отдельных узлов: циркуляционного клапана 9, силового цилиндра 10, подвижной дорнирующей головки 1, связующей полой штанги 2 и основного нижнего упора 6. Пластырь 3 монтируется на штангу 2 между дорнирующей головкой 1и основным нижним упором 6. Силовой цилиндр 10выполнен из трех рабочих и одного холостого цилиндров, поршней, соединенных между собой штоками и регулируемого упора. Дорнирующая головка 1 включает в себя полый стержень с радиальным отверстием, составной корпус с отверстием, камерами и уплотнительными элементами, конусный пуасон, калибрующие сектора, кожух, самоуплотняющуюся манжету, обоймы, гайки, переводники.
Связующая полая штанга 2 состоит из стержня 8, на котором размещены промежуточные упоры пластыря 7.
Основной нижний упор 6 выполнен в виде конуса с пазами, в которых на шарнирах с пружинными лепестками расположены упорные пластины пластыря, при этом в рабочем состоянии они занимают положение перпендикулярное к образующим пластыря, контактируя одним концом с его торцом, другим с уступами пазов в корпусе, а в транспортном состоянии заподлицо в пазах корпуса – пуасона.
Такая конструкция упора позволяет в случае аварийной ситуации извлечь устройство без оставления его элементов в скважине, продолжить без подъема на поверхность расширение и калибровку пластыря до полного сопряжения его со стенкой обсадной трубы или после устранения неполадок опустить в скважину для качественного завершения операции.
Циркуляционный клапан 9состоит из корпуса , переходника, фильтров, сбивного пальца, шара.
В устройстве могут быть использованы и клапаны других типов, которые обеспечивают заполнение жидкостью труб при спуске и сливе ее при подъеме.
Дорнирующая головка снабжена стопорным срезным штифтом, предупреждающее преждевременное расширение пластыря при спуске его в скважину. Устройство комплектуется стержнем (ломиком) диаметром 25мм, длиной 2 метра для открытия отверстия в циркуляционном клапане 9 перед подъемом инструмента.
Принцип работы устройства
Для спуска в скважину устройство в сборе с пластырем комплектуется из двух частей: первая включает в себя дорнирующую головку 1, полую штангу 2, упор 6, пластырь 3; вторая – циркуляционный клапан 9, силовой цилиндр 10.
Первая часть опускается в скважину и соединяется со второй над устьем через переводник, а дорнирующая головка 1 фиксируется от осевого перемещения регулируемым упором силового цилиндра 10. Устройство в сборе с пластырем опускается в скважину так, чтобы середина пластыря 3 была ориентирована на дефект 4 обсадной колонны 5 (рис 3.10.1 а). Если длина пластыря более допустимой высоты подъема агрегатом, то пластырь в сборе со штангой спускают в скважину по частям и сваривают их над устьем по соответствующей технологии. Расширение пластыря 3 до сопряжения с внутренней стенкой обсадной колонны 5 для перекрытия нарушения 4 осуществляется продавливанием дорнирующей головки 1 через пластырь силовым цилиндром 10, при этом предварительное расширение пластыря обеспечивается конусным пуансоном дорнирующей головки, а окончательное, до полного контакта с обсадной колонной – калибрующими секторами дорнирующей головки (рис 3.10.1 б).
Заход калибрующих секторов в пластырь на отрезке L1 осуществляется без избыточного давления жидкости в головке. После захода калибрующих секторов в пластырь жидкость поступает в камеру, а затем в полость самоуплотняющейся манжеты, что обеспечивает радиальный ход калибрующих секторов. Рабочее избыточное давление жидкости на калибрующие сектора поддерживается на отрезке L2 – хода дорнирующей головки под давлением. После первого шагового рабочего хода L = L1 + L2 давление дорнирующей головки надо снизить до «0» и инструмент осадить вниз (зарядить) на величину хода головки – 1500 мм. В это время первый промежуточный упор 7 выходит из пластыря и удерживает его от сдвига. Затем вновь создают рабочее давление в системе и процесс продавливания дорнирующей головки в пластыре повторяется на величину ее рабочего хода. Таким образом, продавливание дорнирующей головки повторяется циклами до выхода ее из пластыря. При этом оставшийся нерасширенным нижний участок пластыря после выхода из него последнего
промежуточного упора расширяется головкой с частичным использованием веса инструмента. При недостаточном весе его для продавливания головки давление в системе может быть снижено (при необходимости до 0). В этом случае работают только конусным пуансоном дорнирующей головки.
Устройство (рис 3.10.1 в)позволяет осуществлять повторные проходы установленного пластыря дорнирующей головкой с давлением, используя частично вес инструмента по технологии работы сверху вниз или снизу вверх. При этом осевая нагрузка на инструмент значительно (30 – 70%) снижается по сравнению с нагрузкой полученной в первоначальном проходе.
В случае невозможности протянуть дорнирующую головку через пластырь вниз (недостаточный вес инструмента, не сработал промежуточный упор и тд) продолжение операции по установке пластыря в обсадной трубе обеспечивается наличием в устройстве конусного упора, который своим конусом – пуансоном при подъеме инструмента расширяет оставшуюся часть пластыря снизу вверх. При этом давление в системе снимается. Затем под давлением производится протягивание дорнирующей головки через пластырь сверху вниз весом инструмента. Если калибровка не удалась из –за недостатка давления в системе, то устройство извлекается на поверхность , устраняются неполадки и операция по установке повторяется.
Заполнение жидкостью труб и устройства при спуске в скважину и слив жидкости при подъеме осуществляется через циркуляционный клапан 9.
Перед подъемом устройства на поверхность в циркуляционный клапан опускается стержень (ломик) который срезает сбивной палец и открывает отверстие для слива жидкости.
В 80-х годах в целях восстановления герметичности колонн были разработаны стальные профильные перекрыватели с диаметрами 146 и 168мм. Перекрыватели представляют собой профильную двухканальную трубу с цилиндрическими концами, в которых с одной стороны крепится башмак, а с другой – устройство для спуска перекрывателя в скважину. Профильная труба имеет длину 8 – 10 метров, толщину стенки 5мм и изготавливается из стали марки 10.
Башмак, профильная труба и устройство для спуска перекрывателя в скважину образуют гидравлическую камеру. В эту камеру через НКТ закачивается жидкость и создается давление до 16 – 18 МПа, под действием которого профильная часть перекрывателя выправляется и плотно прижимается к стенкам колонны (рис 3.10.2).
Перед тем как спустить перекрыватель с устройством, в колонну в интервале нарушения герметичности прорабатывают гидромеханическим расширителем. Шаблонируют колонну и НКТ. Перекрыватель спускают в скважину и устанавливают напротив места нарушения.
В колонну НКТ сбрасывают шар и закачивают жидкость. Когда шар садится в седло происходит увеличение давления, под действием которого перекрыватель выпрямляется и плотно прижимается к внутренней стенки колонны. Затем колонну НКТ отсоединяют от перекрывателя и поднимают, на бурильных трубах спускают развальцеватель, создают через него циркуляцию и вращая колонну бур труб ротором развальцовывают концы и недожимы перекрывателя, а так же разрушают башмак. При этом паста нанесенная на наружную поверхность профильной трубы уплотняется и достигается герметичность э/колонны.
Дата добавления: 2018-05-09; просмотров: 1147; Мы поможем в написании вашей работы! |
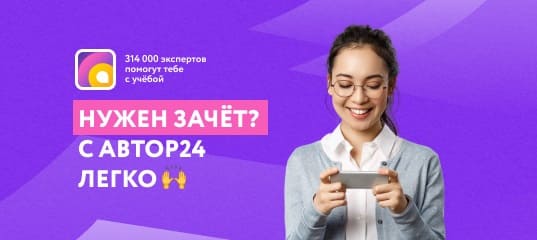
Мы поможем в написании ваших работ!