Мундштук; 2 — электродная проволока; 3 — горелка; 4 — наконечник; 5 — сопло горелки; 6 — электрическая дуга; 7 — сварочная ванна; 8 — наплавленный металл; 9-наплавляемая деталь
3) К достоинствам способа относятся -меньший нагрев деталей; возможность наплавки при любом пространственном положении детали; более высокую по площади покрытия производительность процесса (на 20... 30 %); возможность наплавки деталей диаметром менее 50 мм; отсутствие трудоемкой операции по отделению шлаковой корки, а к недостаткам— повышенное разбрызгивание металла (5... 10%), необходимость применения легированной проволоки для получения наплавленного металла с требуемыми свойствами, открытое световое излучение дуги, требующее защиты сварщика.
4) Наибольшее распространение при сварке в среде СО2 нашли электродные проволоки Св-08ГС, СВ-10ГС, Св-08Г2С, Св-18ХГС и др.
Кроме проволок сплошного сечения, часто используются порошковые проволоки типа ПП-АН4, ПП-АН5, ПП-АН8, ПП-3Х2В8Т и др.
Вопрос 22
Поясните сущность вибродуговой наплавки. 2)Поясните принцип работы схемы Клековкина. 3)Перечислите параметры вибродуговой наплавки. 4)Выделите основные преимущества и недостатки вибродуговой наплавки.
1) Сущность вибродуговой наплавки- используют для восстановления деталей диаметром менее 50 мм. С целью уменьшения нагрева и деформации наплавляемой детали было предложено, во-первых, обеспечить вибрирование электрода, что позволяет снизить напряжение дуги U, во-вторых, для охлаждения детали осуществлять процесс наплавки в жидкости, а не в воздухе под флюсом .(Этот способ обычно используется для наплавки деталей типа тел вращения диаметром от 5 - 10 мм и более)
|
|
2) Схема установки Клековкина
Процесс вибродуговой наплавки протекает в следующей последовательности :
1) сначала электрод касается детали и так как напряжение холостого хода трансформатора питания понижено до Uхх = 12 ... 18 В, то электрическая дуга не загорается, а напряжение падает до нуля, но ток короткого замыкания Iк.з возрастает до максимума, что определяется параметрами электрического дросселя L и резистора R;
2) от Iк.з оплавляется конец электрода и он отрывается от детали, оставляя на ней каплю металла; 3) при отрыве электрода в катушке L возникает ЭДС самоиндукции, которая складывается c напряжением источника питания Uхх и данной добавки хватает для возбуждения сварочной дуги, горящей до следующего касания электродом детали.
Т. е. В процессе вибраций наблюдаются короткие замыкания вследствие прикасания электродной проволоки к наплавляемому изделию (основному металлу), а во время отрыва проволоки возникает большая сила ток и загорается электрическая дуга.
3) Параметры вибродуговой наплавки: 1) напряжение питания Uхх = 12 ... 18 В; 2) сварочный ток I = 100 ... 120 А; 3) шаг наплавки s = 2,0 ... 2,5 мм/об; 4) частота вращения детали n= 4 ... 10 об/мин; 5) скорость подачи электродной проволоки v = 1,0 ... 1,6 м/мин.
|
|
4) Главным преимуществом данного методаявляется отсутствие нагрева, а значит и коробления детали, к тому же имеет место закалка наплавленного слоя до HRC 64, что исключает дополнительную термообработку, вoзмoжнoсть пoлучaть нaплaвленный слoй без пoр и трещин; минимaльнaя дефoрмaция детaли.
Недостатком вибродуговой наплавкиявляется снижение до 40 % усталостной прочности sr из-за действия внутренних напряжений. Поэтому с особой осторожностью надо рекомендовать этот метод для деталей, работающих при знакопеременных нагрузках, сравнительно низкий коэффициент наплавки и невысокая производительность наплавки.
Вопрос 23
Поясните сущность процесса газовой сварки и наплавки. 2.Перечислите основные виды горючего газа, применяемого при газовой сварке и наплавке. 3.Охарактеризуйте типы пламени горелки в зависимости от соотношения кислорода и ацетилена.4. Выделите основные преимущества и недостатки газовой сварки и наплавки.
1) Сущность процессагазовой сварки и наплавки – это расплавление свариваемого и присадочного металла пламенем, которое образуется при сгорании горючего газа в смеси с кислородом
|
|
2) В качестве горючего может применяться:
1) природный газ метан CH4, имеющий максимальную температуру горения tmax = 2000° С;
2) сжиженный газ пропан C2H6 c tmax = 2600° C;
3) ацетилен C2H2 с tmax = 3300° C.
Наиболее часто применяется последний, то есть ацетилен.
3) В зависимости от соотношения кислорода и ацетилена различают пламя горелки:
1) нормальное при соотношении O2 / C2H2 = 1 , имеющее максимальную температуру t = 3100° С (применяют для сварки и наплавки мало и среднеуглеродистых сталей, алюминиевых сплавов, бронзы и меди);
2) науглероживающеепри соотношении O2 / C2H2 = 0,8 , имеющее максимальную температуру t = 2700° С (применяют для сварки и наплавки чугуна и припаивания твёрдосплавных пластин);
3) окислительноепри соотношении O2 / C2H2 = 1,4 , имеющее максимальную температуру t = 3300° С (применяют для резки стали и сварки латуни).
4) К преимуществам газовой сварки относятся: простота способа, несложность оборудования, отсутствие источника электрической энергии.
К недостаткам газовой сварки относятся: меньшая производительность, сложность механизации, большая зона нагрева и более низкие механические свойства сварных соединений, чем при дуговой сварке.
|
|
Вопрос 24
Поясните сущность процесса газотермического напыления. 2.Перечислите виды газотермического напыления. 3.Опишите основные технологические операции процесса газотермического напыления. 4.Выделите основные преимущества и недостатки газотермического напыления.
1) Газотермическое напыление (металлизация) - это процесс нанесения на поверхность детали расплавленного мелкодисперсного металла с целью изменения её размеров и свойств, т. е. заключается в нагреве исходного материала покрытия до жидкого или пластичного состояния и его распылении газовой струей. Газотермическое напыление используется для получения износостойких, коррозионно-стойких, жаропрочных, теплоизоляционных покрытий.
2) Виды газотермического напыления:
1) газо-плазменное;
2) электродуговое;
3) высокочастотное;
4) плазменное и др.
При газо-плазменном напылении электродная проволока плавится в кислородно-ацетиленовом пламени. Распыление металла и его нанесение на поверхность осуществляется струёй сжатого воздуха. При электродуговом напылениипроцесс расплавления металла идёт за счёт горения электрической дуги между двумя электродами. Распыление осуществляется аналогично, то есть струёй воздуха. При высокочастотном напылении вместо проволоки используются стержни из углеродистой или легированной стали, которые располагают в высокочастотном индукторе, где они плавятся токами высокой частоты и затем распыляются сжатым воздухом. Плазменная металлизация по сравнению с другими способами имеет более высокие температуру и мощность
3) Основные технологические операции процесса газотермического напыления:
1)Механическая обработка (для устранения дефектов, придания правильной формы);
2)Обезжирование органическими растворителями, моющими средствами; 3)Струйная обработка с целью придания нужной шероховатости;
4)Процесс напыления(производится в течении 10-15 мин);
5)Окончательная механическая обработка(на шлифовальных и токарных станках); 6)Контроль качества покрытий.
4) Недостатками данного методаявляются: 1) относительно слабое механическое сцепление корки с основной поверхностью; 2) немонолитный, то есть пористый, состав покрытия; 3) необходимость особых методов подготовки поверхности.
Достоинства метода: 1) высокая производительность; 2) незначительный нагрев детали - до 200° С; 3) возможность нанесения слоя толщиной от 0,1 до 10 мм; 4) относительная простота процесса и оборудования.
Недостатками способа высокочастотного напыления являются: 1) высокая стоимость генератора ТВЧ; 2) меньшая производительность по сравнению с ранее рассмотренными способами. Главное достоинство метода - лучше качество покрытия за счёт меньшего выгорания легирующих элементов и меньшего количества окислов в зоне расплавления.
Вопрос 25
Поясните сущность и назначение пайки.2. Перечислите основные технологические требования, предъявляемые к припоям и флюсам. 3.Опишите технологический процесс паяния. 4.Выделите основные преимущества и недостатки пайки.
1) Пайкой (паянием) называют процесс получения неразъемного соединения металлов, находящихся в твердом состоянии, при помощи расплавленного вспомогательного (промежуточного) металла или сплава, имеющего температуру плавления ниже, чем соединяемые металлы.
При ремонте автомобилей пайку применяют для устранения трещин и пробоин в радиаторах, топливных и масляных баках и трубопроводах, приборах электрооборудования, кабин, оперения и т.д.
2) Металл или сплав, при помощи которого ведется пайка, называется припоем. По температуре плавления припоев процессы пайки делятся на два основных вида: пайка легкоплавкими (мягкими) припоями и пайка тугоплавкими (твердыми) припоями. К легкоплавким относятся припои, температура плавления ниже 450°С, а к тугоплавким — припои, температура плавления которых выше 450 °С.
К припоям предъявляются основные технологические требования: высокая жидкотекучесть и хорошая смачиваемость соединяемых поверхностей; устойчивость к коррозии; достаточная прочность и пластичность; температура плавления ниже, чем у соединяемых металлов.
3)Технологический процесс паяния состоит из следующих операций: 1)механической (шабером, напильником, шлифовальной шкуркой или химической очистки; 2) покрытия флюсом; 3)нагревания (паяльником, паяльной лампой и другим способом); 4)предварительного облуживания припоем (паяльником, или натиранием, или погружением в припой). Предварительное лужение имеет весьма важное значение, так как в этом случае достигаются повышенные прочность и плотность спая. В случае невозможности предварительного лужения паяние ведут и по чистой поверхности, но результаты будут более низкими.
4)Преимущества: простота технологического процесса и применяемого оборудования; высокая производительность процесса; сохранение точной формы, размеров и химического состава деталей (а при пайке легкоплавкими припоями - сохранение структуры и механических свойств металла); простота и легкость последующей обработки, особенно после пайки тугоплавкими припоями; небольшой нагрев деталей (особенно при низкотемпературной пайке); возможность соединения деталей, изготовленных из разнородных металлов; достаточно высокая прочность соединения деталей; низкая себестоимость восстановления детали.
Основной недостаток пайки - некоторое снижение прочности соединения деталей по сравнению со сваркой.
Вопрос 26
Перечислите виды электрохимического способа для восстановления деталей и их упрочнения; для защиты от коррозии; для улучшения электропроводности. 2.Изобразите схему и объясните процесс электролиза электрохимического способа восстановления.3. Перечислите основные операции, которые проводят перед электрохимическими способами восстановления.4.Выделите особенность получения одинаковой толщины покрытия по всей поверхности детали.
1) Для восстановления деталей машин и их упрочнения применяют:
1) хромирование; 2) железнение; 3) никелирование.
Для защиты деталей от коррозии применяют:
1) цинкование; 2) кадмирование; 3) оксидирование; 4) фосфатирование; 5) азотирование; 6) цианирование; 7) грунтование и покраску.
Для улучшения электропроводности и условия пайки применяют:
1) меднение; 2) лужение; 3) серебрение.
2)
Катодом при гальванопокрытии является восстанавливаемая деталь. Анод может быть нерастворимый.Тогда его выполняют в виде свинцовой пластины. Либо применяют анод растворимый. В последнем случае его делают из металла, который наносится на восстанавливаемую деталь. При прохождении тока через электролит на катоде разряжаются положительно заряженные ионы, выделяется металл и водород H2. На аноде происходит разряд отрицательно заряженных ионов и выделяется кислород O2.То есть над электролитической ванной имеется гремучая смесь водорода и кислорода. Поэтому при проведении процесса электролиза и некоторое время после окончания его необходима интенсивная вентиляция в помещении где находится ванна и строгое соблюдение противопожарных мероприятий.
При использовании растворимого анода его металл переходит в раствор в виде ионов взамен осевших на катоде. При нерастворимом аноде в процессе электролиза концентрация соли в электролите уменьшается, то есть он истощается. Поэтому приходится периодически корректировать состав электролита путём добавления соли.
3) При гальванопокрытии осуществляют следующие операции:
1) механическую обработку поверхностей, подлежащих наращиванию, для придания им точной формы;2) очистку деталей от окислов;3) предварительное обезжиривание;4) изоляцию поверхностей, не подлежащих гальванопластике;5) крепление деталей на подвесках ванны;6) окончательное обезжиривание;7) активацию (анодную или химическую);8) собственно гальванопокрытие;9) последующую промывку.
4)Следует учитывать тот факт, что после электролиза толщина покрытия не везде одинакова. Она зависит от плотности электрического поля, которая в свою очередь больше на выступах и углах восстанавливаемой детали. Поэтому для обеспечения одинаковой толщины покрытия по всей поверхности детали увеличивают так называемую рассеивающую способность электролита.Для этого в него вводят специальные добавки, уменьшают катодную плотность тока Dк , повышают температуру электролита и применяют перемешивание его. Иногда для этой же цели используют фигурные аноды, копирующие форму восстанавливаемой детали, а также дополнительные катоды и токонепроводящие экраны.
Каждый электролит имеет свою так называемую кроющую способность. Это свойство, характеризующее способность нанесения покрытия в углублениях восстанавливаемой детали. С увеличением концентрации соли в электролите его кроющая способность увеличивается.
Вопрос 27
Поясните назначения хромирования. 2)Перечислите типы электролитов, используемых для хромировании. 3)Охарактеризуйте виды хромовых корок и параметры, влияющие на их качество.4) Выделите основные преимущества и недостатки хромирования.
1) Хромирование применяют в ремонтном производстве для компенсации износа деталей, а также для их упрочнения и улучшения антикоррозионных свойств. Электролитический хром обладает высокими твёрдостью, износостойкостью, малым коэффициентом трения скольжения, хорошей коррозионной стойкостью и теплопроводностью, прочным сцеплением с основным металлом.
2) Для хромирования применяют три типа электролитов:
1) сернокислый;
2) саморегулирующийся;
Тетрохроматный.
По концентрации бывают:
Электролит низкой концентрации имеет самый высокий выход по току, хорошую рассеивающую способность и обеспечивает твёрдые и износостойкие корки. Этот электролит применяют для восстановления деталей с повышенными требованиями износостойкости.Электролит высокой концентрации имеет плохую рассеивающую способность и малый выход по току, но хорошую кроющую способность. Он более устойчив в работе и обеспечивает блестящие корки, то есть его применяют для получения защитно-декоративных покрытий.Электролит средней концентрации по своим свойствам занимает промежуточное положение.
3) Качества хромовых покрытий зависят не только от состава электролита, но и других параметров режима процесса, а именно: 1) катодной плотности тока Dк , А/дм2; 2) температуры электролитаtэл°.Изменяя эти параметры, в электролите любой концентрации можно получить три вида корок:
1) матовые (серые) ;
2) блестящие ;
Молочные .
Матовые корки отличаются высокой твёрдостью (9000 ... 12000 МПа). Они весьма хрупки. Имеют низкую износостойкость из-за очень плохой смачиваемости маслом. У данных покрытий образуется густая сетка мелких и неглубоких микротрещин. Отсюда и их название - серые или матовые.
Блестящие корки имеют твёрдость 6000 ... 9000 МПа, высокую износостойкость и повышенную хрупкость. Сеть микротрещин более разреженная, что определило их внешний вид и название.
Молочные корки имеют твёрдость 4000 ... 6000 МПа, высокую вязкость и износостойкость. Трещины отсутствуют.
В ремонтном производстве чаще всего получают блестящие и молочные хромовые покрытия деталей. Изменяя режим процесса, то есть силу тока, температуру и состав электролита, можно программировать свойства покрытия.
4) Недостатками хромирования являются: 1) низкий выход по току (a < 16 %); 2) малая производительность (до 0,03 мм/ч); 3) сравнительно небольшая максимальная толщина корки (до 0,4 мм), так как более толстая обладает плохими механическими свойствами; 4) высокая агрессивность и ядовитость хромовых электролитов; 5) снижение предела выносливости детали (до 20 %); 6) плохая смачиваемость маслом электролитического хрома.
Преимуществa---высокая твёрдость поверхности, износостойкость, малый коэффициент трения скольжения, хорошая коррозионная стойкость и теплопроводность, прочное сцеплением с основным металлом. Хром обладает очень высокой отражательной способностью и большей стойкостью против окисления.
Вопрос 28
Поясните назначение железнения. 2.Перечислите типы электролитов, используемых для железнения.3. Опишите технологический процесс железнения. 4.Назовите основные преимущества и недостатки железнения.
1) В ремонтном производстве железнениеприменяется для компенсации износа (т.е. используют как средство наращивания металла на изношенную поверхность стальных и чугунных деталей при восстановлении их размеров.)
Также может использоваться для исправления брака и упрочнения поверхностей деталейиз малоуглеродистых сталей без их термообработки.
2) По своему составу электролиты для железнения делятна три типа:
1) хлористые;
2) сернокислые;
3)сульфатно-хлористые или смешанные.
При железнении свойства покрытия зависят от состава электролита и параметров режима осаждения металла.
В ремонтном производстве наиболее часто применяют хлористые электролиты, так как сернокислые не обеспечивают высокой производительности процесса и качества корки. Однако сернокислые менее агрессивны и более стойки к окислению.
В зависимости от теплового режима различают горячие электролиты (температура 60 ... 90° С) и холодные, которые не подогревают. Первые более производительны, так позволяют повышать катодную плотность тока Dк.
3) Типовой технологический процесс железнения имеет следующие этапы:
1) очистка деталей от грязи и масла;
2) механическая обработка;
3) промывка в бензине;
4) сушка;
5)изоляция не покрываемых поверхностей;
6) монтаж деталей на подвеске;
7) обезжиривание;
8) промывка горячей водой (70 ... 80° С);
9) промывка холодной водой (10° С);
10) анодное травление в электролите железнения;
11) промывка холодной водой;
12) анодная обработка в 30 % растворе H2SO4(серной кислоты);
13) промывка холодной водой;
14) промывка-прогрев тёплой водой (50 ... 60° С);
15) железнение;16) промывка горячей водой (70 ... 80° С);
17) нейтрализация;
18) промывка горячей водой (70 ... 80° С);
19) демонтаж деталей с подвесок;
20) контроль качества железнения;
21) механическая обработка;
22) консервация деталей.
При железнении следует поддерживать строго определённую кислотность
(pH )электролита. При уменьшении pH ухудшается сцепление корки, а при увеличении pH снижается выход по току.
4) Достоинства процесса железнения: 1) расходные материалы сравнительно дёшевы и недефицитны; 2) высокий выход по току a = 85 ... 95 %; 3) высокая производительность, то есть скорость осаждения составляет 0,2 ... 0,5 мм/ч; 4) толщина твёрдого покрытия может доходить до 3 мм; 5) имеется возможность в широких пределах регулировать свойства корки, например, микротвёрдость от 1600 до 7800 МПа; 6) высокая износостойкость корки, приближающаяся к закалённой стали; 7) в случае необходимости корки после железнения хорошо хромируются; Недостатки: сцепление металла детали с нанесенным металлом значительно хуже, чем при хромировании. Твердость нанесенного слоя составляет всего лишь НВ 170—200. Следовательно, детали машин, восстановленные таким способом, имеют низкую износостойкость. Для ее повышения необходимо нанесенный слой металла подвергать химико-термической обработке, например цементации с последующей закалкой и отпуском. После железнения предел выносливости детали снижается на 10 ... 30%.
Вопрос 29
Перечислите виды электрохимического способа для защиты от коррозии и декоративной отделки. 2Назовите виды электролитов, используемых для цинкования. 3Выделите способы никелирования и объясните их сущность. 4Опишите особенность технологического процесса меднения.
1) Покрытие деталей никелем проводят чаще всего для защиты от коррозии и в качестве декоративной отделки. Редко данные корки наносят с целью компенсации износа. Цинкованиеприменяется для защиты стальных и чугунных деталей от коррозии. Также для защиты от коррозии применяют: кадмирование; оксидирование; фосфатирование; азотирование; цианирование; грунтование и покраску.
2)Для цинкования используют
Кислые,
Цианистые,
Цинкатные
Аммиакатные электролиты.
3) Существует два способа никелирования- электролитический и химический.
Электролитическое никелирование используется как для защитно-декоративного покрытия, так и в качестве подслоя перед меднением или хромированием. Чаще всего применяют сернокислые электролиты, где основным компонентом является сернокислый никель NiSO4. Также используют сульфатно-хлористые электролиты, в которые входит хлористый никель NiCl, фтор-боратные и сульфоматные электролиты.
При электролитическом никелировании используют растворимые никелевые аноды марок НПА1, НПА2 и НПАН. Все электролиты для никелирования весьма чувствительны к посторонним примесям, которые могут попадать в раствор из анодов и материалов подвесок. Поэтому электролит подвергают постоянной фильтрации. Чем больше кислотность и температура раствора (электролита), тем при большей плотности тока и с большей скоростью можно вести процесс никелирования.
При химическом никелировании деталь погружают в нагретый до 85 ... 95° С раствор и выдерживают в нём без применения электрического тока. Осаждение никеля происходит за счёт его восстановления из водного раствора солей никеля с помощью восстановителя - гипофосфата натрия. Такое покрытие является гладким и твёрдым, так как оно есть сплав никеля с фосфором. После термообработки (нагрев до 400° С) твёрдость корки возрастает в 2 раза, то есть примерно до 10000 МПа.
4) Данный технологический процесс, во-первых, позволяет предохранить стальные детали от спекания при действии высоких температур. Поэтому меднению подвергают болты и гайки, крепящие выпускные коллекторы ДВС, штуцеры тормозных цилиндров самоходных машин и т.п. Во-вторых, меднение применяется для защиты поверхностей от науглероживания при цементации. В-третьих, - в качестве приработочного слоя в ответственных парах трения, например, в паре “поршневое кольцо - цилиндр двигателя”. В-четвёртых, слой меди наносится на поверхности деталей перед их пайкой. Также покрытие меди применяется в качестве подслоя перед никелированием или хромированием, что улучшает сцепление последних. Для меднения применяют кислые и щелочные электролиты.
Вопрос 30
1.Опишите назначение герметиков и клеев в ремонтном производстве. 2.Перечислите основные преимущества и недостатки ремонта деталей клеями. 3.Приведите примеры клеев, используемых при ремонтном производстве. 4.Обоснуйте необходимость использования холодной молекулярной сварки.
1 Герметики применяют для уплотнения стыков между сопрягаемыми деталями, для укрепления резьбовых соединений, для заделки трещин, склеивания и других целей.
Клеевые технологии нашли широкое применение в ремонтном производстве. С помощью клеев герметизируют трещины длиной до 150 мм, заделывают пробоины площадью до 3 см2, устраняют течи, сколы и другие дефекты. Клеями ремонтируют не только корпусные детали, но и рамные конструкции, а также кузовные панели, восстанавливают изношенные поверхности как плоские, так и цилиндрические.
2 Ремонт с помощью клеев имеет следующие преимущества перед сваркой, пайкой и т.п. методами: 1) возможность соединения разнородных материалов, например, пластик с металлом; 2) отсутствие внутренних термических напряжений; 3) отсутствие короблений; 4) не изменяются свойства соединяемых материалов; 5) высокая герметичность соединений; 6) простота технологического процесса, что обуславливает низкую себестоимость.
Основной недостаток эпоксидных клеев - токсичность до затвердевания , большинство клеев имеют низкую теплостойкость. Недостатком клеевых соединений является также их относительно невысокая прочность при неравномерном отрыве и необходимость во многих случаях производить нагревание при склеивании. Еще к некоторым видам можно отнести такой недостаток, как сравнительно недолгий срок хранения клея и очень длительный период отверждения.
3 Наиболее широко применяются эпоксидные клеи. Это связано с их высокой прочностью, химической нейтральностью, малой усадкой при затвердевании. Армирование эпоксидных смол стекловолокном и иными материалами ещё в большей степени расширяет их диапазон применения.При ремонте также широко применяют акриловые, цианакриловые и силиконовые клеи. Причём, два последних являются быстро затвердевающими.
Лучший импортный клей-герметик Silicon AP фирмы MOLIKOTEAP. Он обеспечивает прочное соединение и герметичность стыка в диапазоне температур -50 ... +220° С.
4 Холодная молекулярная сварка (ХМС), где сварочный шов формируется без нагрева материалов, а с помощью специальных композитных веществ, например, РЕКОМ, ПЛАСТМЕТАЛЛ и др. эти материалы представляют собой смеси из порошков никеля, хрома, цинка, других металлов и полимеров называемых олигомерами.
С помощью ХМС можно получать высокопрочные соединения деталей из разных материалов, восстанавливать размеры и форму изношенных деталей, наносить на рабочие поверхности деталей износостойкие самосмазывающиеся покрытия, устранять трещины и сколы. При этом не требуется термическая и механическая обработка, не выделяются токсичные вещества. Работы могут производиться в полевых условиях.
Композит для ХМС готовят непосредственно перед применением также как и эпоксидные клеи. При этом смешивают два или более компонентов.
Например, весьма прост и эффективен метод ХМС для восстановления сорванной резьбы в корпусной детали. Так поверхность резьбы нового болта покрывают специальной разделительной жидкостью для недопущения сцепления его с композитом. Затем сверху наносят слой ХМС и болт вворачивают в повреждённое резьбовое отверстие.
Аналогично восстанавливают шпоночные и другие соединения.
Вопрос 31
Дата добавления: 2018-05-02; просмотров: 235; Мы поможем в написании вашей работы! |
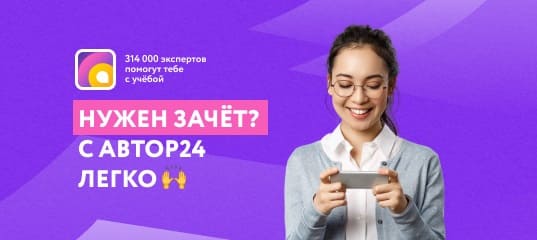
Мы поможем в написании ваших работ!