Слесарные напильники общего назначения.
Основные правила и приемы опиливания
Обычно опиливание выполняется в тисках. Заготовка закрепляется так, чтобы обрабатываемая поверхность располагалась горизонтально на 8...10 мм выше уровня губок. Если для установки используются обработанные поверхности, то, чтобы не повредить их рифленными планками, применяют нагубники.
Необходимо следить за тем, чтобы закрепление заготовки было надежным. Не следует закреплять детали краями губок — губки перекашиваются и плохо удерживают заготовку. Если на поверхности, подлежащей обработке, имеются остатки формовочной смеси, окалины, грязь, масло, ее нужно предварительно очистить металлическими щетками.
На опиливание обычно оставляется припуск до 1мм. При большем припуске следует излишний металллибо срубить, либо срезать ножовкой.
Меры по предупреждению брака. Организация рабочего места. Техника безопасности
Неплоскостность и «завалы» — результат несоблюдения правил опиливания, слабого или очень сильного зажима заготовки в тисках, что приводит к смещению или к короблению детали, неверного выбора длины напильника. Неправильная разметка, применение неисправного инструмента для измерения, неумение пользоваться им, невнимательная работа и несоблюдение правил обработки ведут к получению погрешностей размеров, формы и расположения поверхностей. При работе тупым и засаленным напильником на поверхности появляются задиры, не выдерживается требуемая шероховатость.
|
|
Нельзя работать напильниками без ручек или с расколотыми ручками. Не следует охватывать носок напильника снизу— при холостом ходе можно задеть пальцами за деталь. При чрезмерном продвижении напильника вперед ручка может удариться о край детали — хвостовик выйдет из ручки, что может стать причиной травмы.
Глава 7
Сверление
1.Сверлением называется операция по изготовлению отверстий в сплошном материале. Увеличение размера отверстия, полученного отливкой, ковкой, штамповкой или другим способом, называется рассверливанием.
Инструментом для сверления и рассверливания являются сверла различных типов и размеров, оборудованием — сверлильные станки и сверлильные ручные машины. Для обработки отверстия инструмент получает одновременно два движения: главное (движение резания) — вращательное и движение подачи — поступательное перемещение в осевом направлении. Каждая точка инструмента движется при этом по винтовой линии.
Сверло
Перовое сверло (рис. 87, а)имеет форму лопатки с хвостовиком. Его режущая часть — треугольной формы с углом при вершине
|
|
Из-за плохого отвода стружки перовые сверла применяются редко, в основном для обработки ступенчатых отверстий и при небольшом количестве изделий.
Спиральные сверла (рис. 87, б)обеспечивают хорошее удаление стружки. Они имеют две спиральные канавки, служащие для образования режущих кромок, отвода стружки и подвода охлаждающей жидкости. Канавки наклонены к оси под углом 17...30°.
Сверло состоит из рабочей части, хвостовика и шейки между ними. Шейка обеспечивает выход шлифовального круга в процессе шлифования сверла. На ней маркируется диаметр инструмента и материал, из которого изготовлена его рабочая часть.
Сверло состоит из рабочей части, хвостовика и шейки между ними. Шейка обеспечивает выход шлифовального круга в процессе шлифования сверла. На ней маркируется диаметр инструмента и материал, из которого изготовлена его рабочая часть.
Рабочая часть подразделяется на кюническую режущую и цилиндрическую направляющую. На режущей части (рис. 87, в)располагаются две режущие кромки и между ними под углом 45...55° — поперечная кромка (перемычка).
Зенкерование
Зенкерование применяется для увеличения размера просверленного отверстия (рис. 105, а), исправления погрешностей сверления, повышения точности и придания правильного положения осям отверстий, полученных отливкой и штамповкой.
|
|
Зенкерование гладких цилиндрических отверстий является обычно промежуточной операцией между сверлением и развертыванием. Оно обеспечивает получение отверстий За, 4-го классов точности и шероховатостью не более Rz = 40.
Развертывание
Развертывание — окончательная операция по обработке отверстий после сверления, зенкерования или расточки для придания им высокой точности и чистоты. При развертывании можно получить отверстие 2, 3-го классов точности и шероховатостью не грубее Ra= 1,25.
Инструмент для развертывания — развертки.
По форме обрабатываемой поверхности они подразделяются на цилиндрические и конические, по способу применения — на ручные и машинные, по способу закрепления — на хвостовые и насадные.
Глава 8
Нарезание резьбы
Нарезание резьбы - это образование винтовой поверхности на наружной или внутренней цилиндрической или конической поверхностях детали.
Нарезание винтовой поверхности на болтах, валиках и других наружных поверхностях деталей можно выполнять вручную или машинным способом. К ручным инструментам относятся: круглые разрезные и неразрезные плашки, а также четырех- и шестигранные пластинчатые плашки, клуппы для нарезания резьбы на трубах. Для крепления плашек используются плашкодержатели и клуппы. Круглая плашка используется также для машинного нарезания резьбы.
|
|
Нарезание резьбы в отверстиях выполняют метчиками вручную и машинным способом. Различают цилиндрические и конические метчики. Ручные метчики бывают одинарные, двухкомплектные и трех-комплектные. Обычно используют комплект, состоящий из трех метчиков: чернового, обозначенного одной черточкой или цифрой 1; среднего, обозначенного двумя черточками или цифрой 2; и чистового, обозначенного тремя черточками или цифрой 3 (таблица 1, рисунок 3). Имеются специальные метчики: для плашек (плашечные метчики с длинной режущей частью), для гаек, для труб, для легких сплавов, а также с конической рабочей частью. Метчиками можно нарезать резьбу в сквозных и глухих отверстиях или калибровать маточными метчиками ранее нарезанную резьбу.
Правила нарезания резьбы метчиком:
При нарезании резьбы в глубоких отверстиях, в мягких и вязких металлах (медь, алюминий, баббиты и др.) метчик необходимо периодически вывертывать из отверстия и очищать канавки от стружки.
Нарезать резьбу следует полным набором метчиков. Нарезание резьбы сразу средним метчиком без прохода черновым, а затем чистовым не ускоряет, а, наоборот, затрудняет работу; резьба в этом случае получается недоброкачественной, а метчик может сломаться. Средний и чистовой метчики вводят в отверстие без воротка и только после того, как метчик пройдет правильно по резьбе, накладывают вороток и продолжают нарезание резьбы.
Глухое отверстие под резьбу нужно делать на глубину, несколько большую, чем длина нарезаемой части, с таким расчетом, чтобы рабочая часть метчика немного вышла за пределы нарезаемой части. Если такого запаса не будет, резьба получится неполной.
В процессе нарезки необходимо тщательно следить за тем, чтобы не было перекоса метчика; для этого надо через каждые 2—3 нарезанные нитки проверять с помощью угольника положение метчика по отношению к верхней плоскости изделия. Особенно осторожно нужно нарезать резьбу в мелких и глухих отверстиях.На качество резьбы и на стойкость инструмента влияет правильный выбор смазочно-охлаждающей жидкости.
Глава 9
Клепка, пайка, лужение.
Пайка. Представляет собой процесс соединения деталей с использованием специального присадочного скрепляющего материала — припоя и вспомогательного защитного материала — флюса.
Применяются легкоплавкие и тугоплавкие припои.
Процесс пайки металлов включает подготовку изделия, паяльника к пайке и саму пайку изделия.
Подготовка изделия состоит в очистке его поверхности от грязи, жиров, окислов, коррозии, окалины.
Подготовка паяльника (рис. 3.6) включает заправку рабочей части под углом 30…40° с притуплением вершины, ее очистку от окалины и нанесение (облужение) на концевую часть припоя.
При пайке нельзя допускать недогрева и перегрева паяльника. В первом случае припой быстро остывает, образуя непрочное соединение, во втором (выше 500° С) образуется окалина и затруднено лужение рабочей части на паяльнике.
Лужение. Сущность этой слесарной операции состоит в нанесении на деталь тонкого слоя олова или сплавов олова (со свинцом, цинком, висмутом и т. д.) с целью предохранения поверхностей от коррозии и окисления, придания им необходимых свойств, например, для декоративной обработки поверхности при изготовлении художественных изделий или подготовки поверхности подшипников перед заливкой баббитом, перед пайкой. Этот слой носит название полуда.
Перед лужением поверхности деталей обрабатывают до чистого металлического блеска либо нехимическим способом (напильниками, стальной или волосяной щеткой с мокрым песком, шлифованием) либо химическим способом с целью обезжиривания (в растворе каустической соды при кипении, венской известью, бензином и др.) и травления (в растворе соляной кислоты с подогревом). Процесс лужения осуществляется двумя способами погружением в полуду (а), налитую в чистую посуду, с кусочками древесного угля (для защиты от окисления) и растиранием, путем предварительного нанесения паклей на поверхность детали хлористого цинка и последующего нанесения от прутка с подогревом припоя (в) и растирания его паклей (б). После лужения детали промывают водой и сушат.
Глава 10
Притирка и доводка
Притирка — это слесарная операция по удалению с поверхности обрабатываемой детали тончайшего слоя металла (до 0,02 мм) с целью получения высокого качества ее поверхности (плоскостности, прямолинейности, малой шероховатости) для обеспечения плотного (герметичного) или разъемного (подвижного) соединения. Режущим инструментом при притирке являются острые ребра мельчайших зерен абразивного материала. Наибольшее распространение в слесарном деле имеют следующие виды притирки поверхностей: плоских (широких и узких), цилиндрических, конических, а также криволинейных различной конфигурации. Особый вид притирки — притирка кранов с коническими пробками и клапанов в целях достижения их герметичности, когда абразивным материалом обрабатываются обе поверхности — пробки крана, клапана и их гнезд (седел).
Притирка является окончательной операцией, более точной, чем шабрение.
Доводка — это чистовая отделочная операция, позволяющая с помощью притирки обрабатывать детали с высокой точностью линейных размеров (по 5… 6 квалитетам) и геометрической формы, а также с очень малой степенью шероховатости. Путем доводки обрабатываются режущие и измерительные и проверочные инструменты, матрицы и пуансоны штампов и другие детали, к которым предъявляются высокие требования по параметрам точности размеров и геометрической формы, а также шероховатости обработанных поверхностей.
Подготовка поверхностей под доводку осуществляется теми же методами и с теми же требованиями, что и подготовка поверхностей под притирку. Параметры, достигаемые при доводке, также не отличаются от параметров точности и шероховатости, достигаемых при притирке.
Глава 11
Дата добавления: 2018-05-02; просмотров: 1272; Мы поможем в написании вашей работы! |
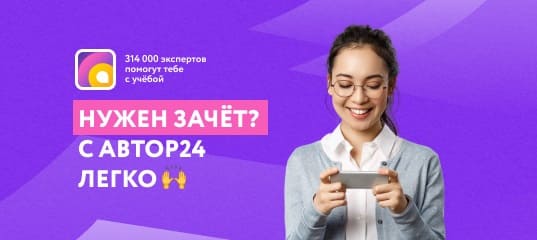
Мы поможем в написании ваших работ!