Определение свариваемости материала сварной конструкции
Необходима критическая оценка соответствия материала назначению изделия и условиям его работы. При наличии оснований, подтвержденных расчетами или другими доводами, принимается вариант материала изделия.
Указать требования стандартов или ТУ на материалы, механические и физико-химические свойства выбранного материала.
Таблица 1.6.1 Химический состав стали
Марка стали | ГОСТ | Содержание элементов, % | |||||||
C | Mn | Si | Cr | Ni | Mo | V | Cu | ||
Таблица 1.6.2 Механические свойства стали
Марка стали | ГОСТ | Временное сопротивле-ние разрыву, σв МПа | Предел текуче-сти,σ0,2 МПа | Относи-тельное удлине-ние, % | Ударная вязкость, мДж/м2 |
Для определения свариваемости стали рассчитываем эквивалентное содержание углерода
Сэ = Сх +Ср, (1.6.1.)
где
Сх химический эквивалент углерода;
Ср размерный коэффициент углерода.
Сх = С+ +
+
+
+
+
+
+
, (1.6.2.)
где C, Mn, Ni, Cr, Mo, V, Cu, Р - %-ое содержание компонентов в стали.
С учетом толщины металла поправка к эквиваленту углерода рассчитывается по формуле:
Cр = 0,005· S· Сх, (1.6.3.)
|
|
где Ср – поправка к эквиваленту углерода;
S – толщина свариваемого металла;
Сх – эквивалент углерода;
0,005 – коэффициент толщины.
По значению эквивалентного содержания углерода определить группу свариваемости стали
при
Сэ до 0,25 включительно свариваемость хорошая;
Сэ свыше 0,25 до 0,35 включительно свариваемость удовлетворительная;
Сэ свыше 0,35 до 0,45 включительно свариваемость ограниченная;
Сэ свыше 0,45 свариваемость плохая.
В зависимости от группы свариваемости стали дать предложения по технологии сварки каждой марки стали.
При необходимости определить температуру предварительного подогрева по формуле
Тп = 350*
Выбор и обоснование методов сборки и сварки
Сборку сварных конструкций вединичном и мелкосерийном производстве можно производить по разметке с применением простейших универсальных приспособлений (струбцин, скоб с клиньями), с последующей прихваткой с использованием того же способа сварки, что и при выполнении сварных швов.
В условиях серийного производства сборка под сварку производится на универсальных плитах с пазами, снабжёнными упорами, фиксаторами с различными зажимами. На универсальных плитах сборку следует вести только в тех случаях, когда в проекте заданы однотипные, но различные по габаритам сварные конструкции. При помощи шаблонов можно собрать простые сварные конструкции.
|
|
В условиях серийного и массового производства сборку под сварку следует производить на специальных сборочных стендах или в специальных сборочно-сварочных приспособлениях, которые обеспечивают требуемое взаимное расположение входящих в сварную конструкцию деталей и точность сборки изготавливаемой сварной конструкции в соответствии с требованиями чертежа и технических условий на сборку.
Кроме того, сборочные приспособления обеспечивают сокращение длительности сборки и повышение производительности труда, облегчение условий труда, повышение точности работ и улучшение качества готовой сварной конструкции.
Собираемые под сварку детали крепятся в приспособлениях и на стендах с помощью различного рода винтовых, ручных, пневматических и других зажимов.
При установлении последовательности сборочных операций необходимо руководствоваться следующим.
1. Выполняемая сборочная операция не должна затруднять осуществление последующей операции.
|
|
2. Размеры поступающих на сборку деталей и подготовка их кромок под сварку должны быть тщательно проверены.
3. Выполнение дополнительных работ, в случае надобности, по пригонке деталей в целях точного соблюдения запроектированных зазоров, перекрытий и взаимного расположения их согласно чертежу должно осуществляться легко и быстро.
4. Обеспечение соответствующими инструментами и приспособлениями, облегчающими правильность установки деталей и закрепление их в требуемом положении.
По характеру сборочно-сварочных работ при изготовлении конструкций сборка делится на:
- сборку всей конструкции,
- сборку узлов (узловая сборка)
- монтажную сборку.
Собирать всю конструкцию на прихватках не рекомендуется даже при изготовлении ее с применением ручной сварки. Она может быть допущена только при изготовлении простейших сварных конструкций, составляемых из небольшого количества деталей.
Недостатки сборки всей конструкции следующие:
1. Невозможность применения механизированных методов сварки для многих швов, находящихся в различных положениях в пространстве (горизонтальные, вертикальные и потолочные) и находящихся в труднодоступных местах.
|
|
2. Громоздкая и трудоемкая кантовка тяжеловесных конструкций и конструкций с большими габаритными размерами.
3. Неудобное положение сварщика при выполнении швов в труднодоступных местах, что снижает производительность и понижает качество сварных швов.
4. Высокие остаточные напряжения, которые образуются из-за невозможности осуществления свободной усадки швов и которые иногда могут привести к образованию трещин и даже к самопроизвольному разрушению конструкций в цехах после окончания сварочных работ.
5. Накапливание остаточных деформаций, которые могут достигнуть такой величины, что правка станет невозможной и конструкция будет забракована.
Наиболее целесообразными видами сборки и сварки конструкций является
сборка и сварка отдельных узлов, а затем сборка и сварка этих узлов в целую конструкцию в цехах или на монтаже. Узловая сборка и сварка дают возможность механизировать сборочно-сварочные операции, повысить качество сборочно-сварочных работ и производительность труда.
Преимущества узловой сборки:
1) возможность автоматизации сварочных работ, так как швы более доступны и кантовка узла значительно легче, чем кантовка всей конструкции;
2) детали свариваются в свободном состоянии и остаточные напряжения от поперечной усадки незначительны;
3) возможность создания поточных линий производства;
4) технологические недостатки сборочно-сварочных работ (деформации, напряжения и др.) могут быть легко исправлены в отдельных узлах и не создавать накопления этих недостатков в целой конструкции;
5) возможность механизации сборочных операций и поднятия культуры производства на более высокую ступень.
Выбор того или иного способа сварки зависят от следующих факторов:
- толщины свариваемого материала;
- протяжённости сварных швов;
- требований к качеству выпускаемой продукции;
- химического состава металла;
- предусматриваемой производительности;
- себестоимости 1 кг наплавленного металла;
Среди способов электродуговой сварки наиболее употребляемыми являются.
- ручная дуговая сварка;
- механическая сварка в защитных газах;
- автоматизированная сварка в защитных газах и под флюсом.
В данном разделе необходимо подробно описать особенности выбранного способа сборки, сварки, привести другие способы сборки, сварки данной сварной конструкции. Описать достоинства и недостатки этих способов сборки, сварки.
Выбор сварочных материалов
При выборе сварочных материалов следует исходить из следующих условий:
- возможности осуществлять сварку в тех положениях, в каких будет находиться во время сварки изделие;
- возможности получения плотных беспористых швов;
- возможности получения металла шва, обладающего высокой технологической прочностью,
- возможности получения металла шва, имеющего требуемую эксплуатационную прочность;
- низкой токсичности;
- экономической эффективности.
Выбор сварочных материалов производится в соответствии с принятым способом сварки.
При ручной дуговой сварке конструкционных углеродистых и легированных сталей выбор электродов производится по ГОСТ 9467-75, который предусматривает два класса электродов.
1. Первый класс - электроды для сварки углеродистых и легированных сталей, требования к которым установлены по механическим свойствам наплавленного металла и содержанию в нём серы и фосфора.
2. Второй класс регламентирует требования к электродам для сварки легированных теплоустойчивых сталей и которые классифицируются по химическим свойствам наплавленного металла шва.
3. ГОСТ 10052-75 устанавливает требования к электродам для сварки высоколегированных сталей с особыми, свойствами. Выбор электродов для сварки этих сталей производится по этому ГОСТу.
Выбор стальной проволоки для механизированных способов сварки производится по ГОСТ 2246-70, который предусматривает выпуск стальной сварочной проволоки для сварки диаметром от 0,3 до 12 мм.
Выбор флюсов для сварки производится по ГОСТ 9078-81, который предусматривает две группы флюсов:
- для сварки углеродистых низколегированных и среднелегированных сталей (АН-348А, АН-348АМ, ОСЦ-45, АН-60, АН-22, ФЦ-9, АН-64);
- для сварки высоколегированных, сталей (АН-26, АН-22, АН-30, АНФ-14, АНФ-16, АНФ-17, ФЦК-С, К-8).
В качестве защитных газов при сварке применяются инертные газы (аргон, гелий) и активные газы (углекислый газ, водород).
Аргон, предназначенный для сварки, регламентируется ГОСТ 10157-79 и в зависимости от процентного содержания аргона и назначения делится на аргон высшего, первого и второго сорта.
Гелий поставляется по ГОСТ 20461-75, который предусматривает два сорта газообразного гелия: гелий высокой чистоты (99,98% Не) и гелий технический (99,8% Не).
Углекислый газ, предназначенный для свари, соответствует ГОСТ 8050-85, который в зависимости, от содержания СО2 предусматривает двасорта сварочной углекислоты: первый сорт - с содержанием CQ2 не менее 99,5%, второй сорт - с содержанием СО2 не менее 99%.
После обоснования выбора сварочных материалов для принятых в проекте способов сварки необходимо привести в форме таблиц химический состав этих материалов, механические свойства и химический состав наплавленного металла.
1.9 Расчет режимов сварки
1.9.1. При полуавтоматической сварке в СО2 и СО2 + Ar
Сведения о стандартных типах соединений, швов и форм подготовки кромок для дуговой сварки в защитных газах приведены в ГОСТ 14771-76.
Основными параметрами режима сварки в среде СО2 и СО2 + Ar являются:
- Диаметр электродной проволоки, dэл, мм.
- Сила сварочного тока, Iсв, А.
- Напряжение на дуге, Uд, В.
- Скорость сварки, Vсв, м/ч.
- Расход защитного газа, Gсо2
Дополнительными параметрами режима являются:
- Род тока,
- Полярность при постоянном токе.
Диаметр электродной проволоки (dэл) выбирается в зависимости от толщины свариваемых деталей. При выборе диаметра электродной проволоки при сварке швов в нижнем положении следует руководствоваться данными таблицы 1.9.1.1, 1.9.1.2
Таблица 1.9.1.1 – Выбор диаметра электродной проволоки для сварки швов стыковых соединений
Толщина металла, мм | Форма подготовки кромок | Диаметр электродной проволоки, мм |
1 | 2 | 4 |
0,8-1,0 1,5-2,0 2,5-3,0 3,5-4,0 | Встык, без разделки кромок | 0,8 1,0 1,2 1,2 |
4,5-6,0 | 1,6 | |
7,0-8,0 | 1,6 | |
9,0-10,0 | 1,6 | |
11,0-12,0 | 1,6 | |
13,0-14,0 15,0-16,0 | V – образная односторонняя | 1,6 1,6 |
17,0-18,0 19,0-20,0 21,0-22,0 23,0-24,0 25,0-28,0 | V – образная двусторонняя | 2,0 2,0 2,0 3,0 3,0 |
Таблица 1.9.1.2 – Выбор диаметра электродной проволоки для сварки угловых швов
Толщина металла, мм | Форма подготовки кромок | Диаметр электрод. проволоки, мм |
0,8-1,0 1,5-2,0 3,0-4,0 |
Угловое без разделки кромок | 0,5-1,0 0,8-1,2 1,2 |
4,0-5,0 | 1,2 | |
5,0-6,0 7,0-8,0 9,0-10,0 11,0-13,0 | 1,6 1,6 1,6 1,6 | |
14,0-16,0 | 2,0 | |
17,0-20, | 2,0 | |
21,0-28,0 | 2,0 |
Сварочный ток
Iсв = hр *100 / Kп , А, (1.9.1.1.)
где
hр – расчетная глубина проплавления, мм
hр = , мм, (1.9.1.2.)
гдеh – глубина проплавления, мм ( из таблицы1.9.1.3)
n – количество проходов ( из таблицы1.4.2)
Таблица 1.9.1.3 Зависимость глубины проплавления от вида сварного шва
Вид шва | Стыковой односторонний | Стыковой двусторонний | Стыковой на подкладке | Угловой |
h | S | 0.5*S | S+1 | 0.6*Кш |
где
S – толщина свариваемого металла, мм
Кш – катет шва, мм
Минимальный катет углового шва для толщины более толстого из свариваемых элементов | |||||||
от 3 до 4 | св. 4 до 5 | св. 5 до 10 | св. 10 до 16 | св. 16 до 22 | св. 22 до 32 | св. 32 до 40 | св. 40 до 80 |
3 | 3 | 4 | 5 | 6 | 7 | 8 | 9 |
Кп - коэффициент пропорциональности (таблица1.9.1.4)
Таблица 1.9.1.4 KП –коэффициент пропорциональности
d пров | 1,2 | 1,6 | 2,0 | 3,0 | 4,0 |
KП | 1,75 | 1,55 | 1,45 | 1,35 | 1,2 |
Напряжение на дуге
U = 20 + , В (1.9.1.3.)
Скорость сварки
Vсв = , м/час (1.9.1.4.)
где
αн –коэффициент наплавки г/А*час (таблица 1.9.1.5 )
Таблица 1.9.1.5 Коэффициент наплавки
Катет, толщина металла мм | 2 | 3 | 4 | 5 | 6 |
Коэффициент наплавки, αн г/а*ч | 11,5 | 12,2 | 14,5 | 15,8 | 17,1 |
ρ– плотность металла, принятая для углеродистых и низколегированных сталей равной 7,85 г/см3;
Fр – расчетная площадь поперечного сечения наплавленного металла. см2
Fр = , (1.9.1.5.)
где
Fш –общая площадь поперечного сечения шва, см2 (из таблицы1.4.2)
n – количество проходов ( из таблицы 1.4.2)
Расход сварочных материалов при полуавтоматической сварке в СО2 и СО2 + Ar
Расход электродной проволоки
Gэ. пр = 1,1 * М ,Кг (1.9.1.6.)
где
М – масса наплавленного металла
М = Fш * ρ * L * 10-3 ,Кг
где
Fш– площадь поперечного сечения наплавленного металла см2 (таблица 1.4.2)
ρ – плотность металла, принятая для углеродистых и низколегированных сталей равной 7,85 г/см3;
L – длина шва определенного вида шва, см (Таблица 1.4.2)
Расход углекислого газа
Gсо2 =1,5* Gэ. пр,Кг (1.9.1.7.)
Результаты расчета сводят в таблицу 1.9.1.6.
Таблица № 1.9.1.6. Режимы сварки при полуавтоматической сварке в СО2 и СО2 + Ar
№п/п | Условное обозначение сварного соединения | Диаметр электрода dэ | Сварочный ток Iсв | Напряжение на дуге U | Скорость сварки Vсв | Расход электродной проволоки Gэ. пр | Расход углекислого газа Gсо2 |
1.9.2. При ручной дуговой сварке
Сведения о стандартных типах соединений, швов и форм подготовки кромок для РДС приведены в ГОСТ 5264 – 80
Параметры режима ручной дуговой сварки составляют:
- Диаметр покрытых электродов dэл;
- Сварочный ток Ic;
- Напряжение на сварочной дуге Uc;
- Количество проходов n ;
- Скорость сварки Vc;
Диаметр электрода (dэл) выбирается в зависимости от толщины свариваемых деталей.
При выборе диаметра электрода при сварке швов в нижнем положении следует руководствоваться данными таблицы 1.9.2.1, 1.9.2.2
Таблица 1.9.2.1 - Рекомендуемые диаметры электродов при сварке стыковых швов в нижнем положении, мм
Толщина свариваемых деталей | 1,5 | 2,0 | 3,0 | 4 - 5 | 6 - 8 | 9 - 12 | 13 - 15 | 16 - 20 | 21 - 24 |
Рекомендуемый диаметр электрода | 1,6 | 2,0 | 3,0 | 3 - 4 | 4,0 | 4 - 5 | 5,0 | 5 - 6 | 6 – 10 |
Таблица 1.9.2.2. - Рекомендации по выбору диаметра электрода при сварке угловых швов, мм
Катет шва, К, мм | 2 | 3 | 4 | 5 | 6-8 | 9-12 | 12-20 |
Рекомендуемый диаметр электрода, dэл, мм | 1,6-2 | 2,5-3 | 3-4 | 4,0 | 4-5 | 5,0 | 5,0 |
Примечание: толщину свариваемых деталей и катет шва необходимо выбирать с учетом количества проходов сварного шва (таблица 1.4.2). Толщину свариваемых деталей и катет шва необходимо разделить на количество проходов
Сварочный ток
Iсв = , А (1.9.2.1.)
где:
dэл – диаметр электрода, мм
J – плотность тока А/мм2 ( таблица 1.9.2.3 )
Таблица 1.9.2.3 Зависимость плотности тока от диаметра электрода и вида покрытия электрода
dэ | 3 | 4 | 5 | 6 |
J-рутиловое покрытие электродов | 14 - 20 | 11.5 - 16 | 10 – 13.5 | 9.5 – 12.5 |
J - основное покрытие электродов | 13 - 18.5 | 10 – 14.5 | 9 – 12.5 | 8.5 - 12 |
Напряжение на дуге
Uс = 20+0.04 * Iсв , В (1.9.2.2.)
Скорость сварки
Vсв = , м/час (1.9.2.3.)
где αн –коэффициент наплавки г/А*час
Таблица 1.9.2.4 зависимость коэффициента наплавки от толщины свариваемых деталей
Катет, толщина свариваемых деталей, мм | 2 | 3 | 4 | 5 | 6 |
Коэффициент наплавки, αн г/а*ч | 11,5 | 12,2 | 14,5 | 15,8 | 17,1 |
ρ– плотность металла, принятая для углеродистых и низколегированных сталей равной 7,85 г/см3;
Fр – расчетная площадь поперечного сечения наплавленного металла. см2
Fр = , (1.9.2.4.)
где
Fш –общая площадь поперечного сечения шва, см2 ( таблица 1.4.2)
n – количество проходов ( таблица 1.4.2)
Нормативный расход электродов определяется по формуле:
Н = М * Кр (1.9.2.5.)
где Кр – коэффициент расхода электродов данной марки.
Этот коэффициент учитывает потери при сварке на угар и разбрызгивание, длину огарка не более 50мм. Значение Кр для некоторых наиболее часто применяемых электродов длиной 350 и 450мм приведены в таблице ниже.
Таблица 1.9.2.5 Коэффициент расхода покрытых электродов
Коэффициент расхода электродов, Кр | Группа марок электродов | |
1,5 | І | АНО-1, АНГ-1К, ОЗС-17Н, АНО-19М, ДСК-50, АНП-6П, НИАТ-3М |
1,6 | ІІ | ОЗС-23, ВН-48, УП-1/45, АНО-5, АНО-13, АНО-19, АНО-20, ОЗС-6, АНО-10, АНО-11, АНО-30, АНО-ТМ, ВСО-50СК, ОЗС-18, ОЗС-25, УОНИ-13/55У, АНО-ТМ60, ВСФ-65, АНО-ТМ70, АНП-2, УОНИ-13/65, УОНИ-13/85 |
1,7 | ІІІ | АНО-4, АНО-6, АНО-6У, АНО-21, АНО-24, АНО-29М, АНО-32, МР-3, ОЗС-4, ОЗС-12, ОЗС-21, СМ-11, УОНИ-13/45, УОНИ-13/45, УОНИ-13/45СМ, АНО-27, АНО-25, УОНИ-13/55, УОНИ-13/55СМ, ИТС-4С, ОЗС-24 |
1,8 | ІV | ВСЦ-4, К-5А |
М – масса наплавленного металла определяется для всех видов шва кг :
М = Fш * ρ * L * 10-3 Кг (1.9.2.6.)
где
Fш – площадь поперечного сечения шва см2 (таблица 1.4.2)
ρ – плотность металла, принятая для углеродистых и низколегированных сталей равной 7,85 г/см3;
L – длина шва определенного вида шва, см (таблица 1.4.2)
Результаты расчета сводят в таблицу 1.9.2.6.
Таблица 1.9.2.6. Режимы сварки при ручной дуговой сварке
№п/п | Условное обозначение сварного соединения | Диаметр электрода dэ | Сварочный ток Iсв | Напряжение на дуге U | Скорость сварки Vсв | Расход электродов Н |
1.9.3 При сварке под флюсом
Конструктивные элементы подготовки кромок и виды сварных соединений (стыковые, угловые, тавровые, нахлесточные) для автоматической и механизированной сварки под слоем флюса регламентированы ГОСТ 8713-79.
Основными параметрами режима автоматической и механизированной сварки под слоем флюса, оказывающим влияние на размеры и форму шва, являются:
- Диаметр электродной (сварочной) проволоки, dэл, мм.
- Сила сварочного тока, Iсв, А.
- Напряжение на дуге, Uд, В.
- Скорость подачи электродной проволоки,Vп.п., м/ч.
- Скорость сварки, Vсв, м/ч.
Дополнительными параметрами режима являются:
- Род тока.
- Полярность (при постоянном токе).
- Марка флюса.
Расчет режима сварки начинают с того, что задают требуемую глубину провара при сварке которая устанавливается равной:
h = S, мм, при сварке одностороннего шва
h=0.6*S, мм при сварке двустороннего шва
где S – толщина металла, мм.
Силу сварочного тока, необходимую для получения заданной глубины проплавления основного металла, рассчитывают по формуле:
Iсв = (80-100)·h, А (1.9.3.1.)
Диаметр сварочной проволоки рассчитывают по формуле:
dэл = 2 * , мм (1.9.3.2.)
где Iсв – сила сварочного тока, А;
j – плотность тока, приближенные значения которой приведены в табл. 1.9.3.1.
Таблица 1.9.3.1 Допускаемая плотность тока в электродной проволоке при автоматической сварке стыковых швов
Диаметр электродной проволоки, мм | 6 | 5 | 4 | 3 | 2 | 1 |
Плотность тока, А/мм2 | 25-45 | 30-50 | 35-60 | 45-90 | 65-200 | 90-400 |
Напряжение на дуге
Uд = 20+0,05* , В (1.9.3.2.)
Определяют коэффициент наплавки (αН), который при сварке постоянным током обратной полярности αН = 11,6±0,4 г/А ч, а при сварке на постоянном токе прямой полярности и переменном токе по формуле:
αН = A + B * , г/А·ч, (1.9.3.3.)
где Iсв – сила сварочного тока, А;
dэл - диаметр электродной проволоки, мм;
А, В – коэффициенты, значения которых приведены в табл. 1.9.3.2.
Таблица 1.9.3.2 - Значения коэффициентов А и В
Марка флюса | Коэффициент А | Коэффициент В | ||
Постоянный ток прямой полярности | Переменный ток | Постоянный ток прямой полярности | Переменный ток | |
АН-348А АН-348 АН-348Ш | 2,3 2,8 1,4 | 7,0 7,3 6,0 | 0,065 0,095-0,120 0,081 | 0,040 0,048-0,058 0,038 |
Скорость сварки
Vсв = , м/час (1.9.3.4.)
где
αН - коэффициент наплавки , г/А·ч
j – плотность тока,
Fр – расчетная площадь поперечного сечения наплавленного металла. см2
Fр = , (1.9.3.5.)
где
Fш –общая площадь поперечного сечения шва, см2
n – количество проходов.
Скорость подачи сварочной проволоки
Vп.п= Vсв* , м/час (1.9.3.6.)
где Fэл – площадь сечения электродной проволоки
Fэл = см2 (1.9.3.7.)
Результаты расчета сводят в таблицу 1.9.3.3.
Таблица 1.9.3.3. Режимы сварки при сварке под флюсом
№п/п | Условное обозначение сварного соединения | Диаметр электродной (сварочной) проволоки dэл, мм | Сила сварочно го тока Iсв, А | Напряже ние на дуге Uд,,В | Скорость сварки Vсв,м/ч | Скорость подачи электродной проволоки Vп.п.м/ч | Род тока. Полярность | Марка флюса |
Расход сварочных материалов при сварке под флюсом
Расход электродной проволоки
Gэ. пр = 1,1 * М , Кг (1.9.3.7.)
где
М – масса наплавленного металла
М = Fш * ρ * L * 10-3 ,Кг (1.9.3.8.)
где
Fш– площадь поперечного сечения наплавленного металла см2 (таблица 1.4.2)
ρ – плотность металла, принятая для углеродистых и низколегированных сталей равной 7,85 г/см3;
L – длина шва определенного вида, см (таблица 1.4.2)
1.9.4 Расчет расхода электроэнергии
Если известна масса наплавленного металла Gэ. пр, то расход электроэнергии W, кВт·ч, можно вычислить из удельного расхода электроэнергии по формуле:
W = aэ · Gэ. пр кВт*ч (1.9.4.1.)
где aэ - удельный расход электроэнергии на 1 кг наплавленного металла, кВт·ч/кг.
Для укрупнённых расчётов величину aэ можно принимать равной:
- при сварке на переменном токе, кВт·ч/кг 3...4;
- при многопостовой сварке на постоянном токе, кВт·ч/кт 6...8;
- при автоматической и полуавтоматической сварке на постоянном токе, кВт·ч/кг 5...8.
Дата добавления: 2018-04-15; просмотров: 1413; Мы поможем в написании вашей работы! |
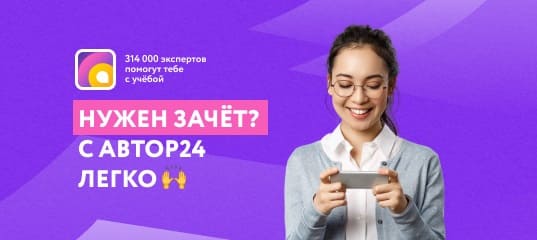
Мы поможем в написании ваших работ!