ТЕХНОЛОГИЧЕСКИЙ ПРОЦЕСС КАПИТАЛЬНОГО РЕМОНТА СТАНКА МОДЕЛИ 2431С
Износ оборудования в процессе его эксплуатации и нерациональная организация технического обслуживания и ремонта приводят к увеличению простоев в ремонте, к ухудшению качества обработки и рост брака, а также к увеличению затрат на ремонт.
О значении улучшения организации хранения и ремонта оборудования свидетельствуют следующие показатели: годовые затраты на ремонт и техническое обслуживание оборудования на предприятиях составляют 10-25% его первоначальной стоимости, а их доля в себестоимости продукции достигает 6-8%.
Количество ремонтников колеблется в пределах 20-30% от общего количества вспомогательных рабочих.
Капитальный ремонт станка модели 2431С проводится в соответствии с едиными требованиями, указанными в специальном документе - типовом технологическом процессе. В нем указаны нормы и правила ремонта, способы и методы его осуществления. Проведенные работы также фиксируются. Для этого существует дефектная ведомость. К ее составлению приступают через два-три месяца после осмотра оборудования. Этот документ становится своеобразным ориентиром для представителя ремонтной службы, так как позволяет ознакомиться с проблемами, которые необходимо устранить.
Во время ремонта необходимо соблюдать определенную последовательность действий и исключить резкие движения, так как они могут привести к ударам и возникновению новых деформаций. Вполне возможно, что в результате подобных действий оборудование придется не восстанавливать, а обновлять, что приведет к лишним затратам и увеличению срока простоя.
|
|
Для разборочных процедур на заводе или в ремонтном цехе должно быть оборудовано специальное место, освобожденное от посторонних предметов. Здесь и ведутся ремонтные работы. Ремонт сверлильного станка начинается с его подготовки – снятия вспомогательных деталей, таких как: дверцы, кожухи, щитки. После снятия детали прочищают и моют. Это позволяет обновить внешний вид оборудования и обеспечить быструю наладку, так как с пыльными деталями работать не только неприятно, но и затруднительно. Под слоем грязи может расположиться трещина, не заметив которую механик так и не справится с поставленной задачей. Начинать разборку следует с узлов и механизмов, а не с конкретных деталей. Это приведет к ненужным обвалам и спровоцирует деформацию всего оборудования. Поэтому сначала снимают рукава, упоры, шпиндели, колонны, стол, а уже затем приступают к осмотру внутренних составляющих.
При осмотре снятых деталей и выявлении дефектов, их отправляют для дальнейшего рассмотрения и исправления повреждений. Отдельнорассматривают и очищают каждую деталь, при необходимости ремонтируют стол. После осмотра всех частей и выявления их недостатков, а также их устранения, детали начинают собирать, соблюдая правильное расположение узлов. Затем заливают масло и обкатывают оборудование. В процессе обкатывания станок испытывают на точность и малейшие дефекты в работе. Если все сделано правильно, то не возникает никаких посторонних шумов, деталь обрабатывается качественно без царапин, масло не протекает и т.д. Тогда мастер составляет акт приема оборудования, и оно вступает в эксплуатацию.
|
|
Наиболее подверженной различным изменениям деталью сверлильного станка является станина. Поэтому в процессе ремонта ей уделяется повышенное внимание. Пред разборкой следует не только ознакомиться с документацией, но и опросить рабочий персонал, который обслуживал данное оборудование. В процессе устного разговора выявляется гораздо больше полезной информации, чем в дефектной ведомости.
Ремонт станины, как и любой другой части станка, начинают с разбора отдельных деталей, который проводят с помощью специальных инструментов. Детали станка являются объемными, поэтому в цехе должен быть кран или передвижное устройство. Для более детального осмотра станка используют линейки, уровни, индикаторы, микрометры, угольники, микроскопы, глубиномеры. Индикаторы на инструментах позволяют установить наличие отклонений от нормы при работе станка, поэтому для изучения труднодоступных мест и сложных соединений оборудование с индикатором становится незаменимо. При осуществлении ремонта мастеру иногда требуется и специальные приспособления, которые разрабатываются для конкретной модели машины. Такая необходимость возникает, когда в процессе использования обычных инструментов работник может получить травму или может возникнуть угроза его жизни.
|
|
Поступивший в ремонт станок подвергается проверке на точность по ГОСТу 6744—67. Результаты проверок заносят в ведомость дефектов.
Перед разборкой необходимо снять электрическую проводку и электродвигатель, кожухи и щитки, а также удалить арматуру системы охлаждения.
При разборке рационально придерживаться следующего порядка демонтажа: оптико-механическая система и окуляр; коробка скоростей и шпиндельный узел со шпинделем; блок направляющих и стойка; привод продольного и поперечного перемещения стола; стол и каретка; станина.
|
|
Рассмотрим последовательность разборки оптико-механической системы станка модели 2431С.
1. Открепляют прижимные планки, снимают опорный вал прижимных планок, а также ленты зажима стола и каретки с двух сторон.
2. Снимают левый кулачок, ограничивающий ход стола вправо (расположен с задней стороны станины). Во избежание поломки узла подсветки шкалы, стол необходимо сместить в сторону так, чтобы рейка вышла из зацепления с зубчатым колесом, обеспечивая допуск к шкале (зеркальному валику) продольного перемещения.
3. Открепляют и снимают лимб с фланцем.
4. Снимают зеркальный валик с защитным кожухом, поддерживая его, чтобы избежать ударов и царапин. Зеркальный валик из кожуха следует извлекать с большой осторожностью. Для этого валик через щель кожуха необходимо обернуть куском мягкой, гладкой и совершенно чистой бумаги так, чтобы она служила прокладкой между валиком и кожухом, исключая их соприкосновение.
5. Открепляют и снимают шторы, защищающие направляющие каретки. Отворачивают гайку, снимают лимб и фланец шкалы поперечного перемещения, вынимают валик крепления прижимных планок каретки.
6. Снимают зеркальный валик (поперечного перемещения) с защитным кожухом, соблюдая предосторожности, как при демонтаже валика.
7. В присутствии электрика снимают объективы с лампами освещения поперечной и продольной шкал (зеркальных валиков). Открепляют провод и трубу подсветки поперечной шкалы, выдвигают на 500 мм и снимают объектив со встроенным узлом подсветки.
8. Вывертывают регулировочный винт, отвертывают крепление и снимают колпачок. Поддерживая рукой узел подсветки шкалы. Продольного перемещения, отворачивают цилиндрическую гайку и вынимают узел.
9. Снимают крышку с коробки привода столаи каретки открепляют и снимают два окуляра.
Ремонт и юстировка оптико-механической и оптической системы отсчета координат производится специализированными бригадами на специальных предприятиях.
Ремонт направляющих станины
При ремонте станины восстанавливают: прямолинейность направляющих 1, 4, 5 и 8 (рис. 6.1), допуская отклонение не более 0,005 мм на длине 1000 мм\ взаимную не параллельность поверхностей 4 и 5 — не более 0,005 мм на длине 1000 мм; извернутость в направляющих 1 и 8 — не более 0,005 мм на длине 1000 мм;не параллельность направляющих 1 и 8 к поверхности 9 (для стойки) по направлениям г—г и е—е, д—д и ж—ж — не более 0,01 мм на длине 1000 мм.
Практика эксплуатации этих станков показала, что направляющие 4 и 5 изнашиваются незначительно (0,01—0,03 мм), а износ накладных каленых направляющих — планок 1 и 8 — составляет менее 0,01 мм. Поэтому поверхности 4 и 5 рационально ремонтировать шабрением, а направляющие 7 и 8 — доводкой чугунными притирами.
Однако при аварийных случаях, когда из-за плохого межремонтного обслуживания между телами качения (направляющих) накапливается грязь, появляется заедание отдельных роликов, возникает трение скольжения. При этом на роликах образуются грани, а на сопрягаемых поверхностях направляющих появляется повышенный износ. В таких случаях направляющие снимают и шлифуют на плоскошлифовальном станке, добиваясь непрямо- линейности, не параллельности и разно высотности не более 0,01 мм, а сопрягаемые поверхности 2 и 7 станины шабрят, добиваясь их прямолинейности и параллельности к поверхности 9. Затем после установки накладных направляющих на место их дополнительно доводят притирами. Поверхности 3 и 6 являются базовыми, от которых ведут ремонт всех других поверхностей.
В случае прямолинейности поверхностей 7, 3, 6 и 8, их взаимной параллельности и допустимой извернутостии однако не параллельности их к поверхности9 последнюю целесообразно шабрить, выверяя на параллельность к вышеуказанным поверхностям.
Рисунок 6.1 - Станина станка 2431С
а—общий вид; б и в — схемы проверки точности направляющих.
Ремонт стола
Ремонт стола включает работы по восстановлению плоскостности зеркала 1 (рис. 6.2), прямолинейности накладных направляющих 2 и 5 и параллельности их зеркалу 1 с точностью 0,005 мм на длине 1000 мм, прямолинейности поверхности 4, точности контакта ее с сопрягаемой поверхностью каретки, параллельности поверхности 4 к стенкам Т-образных пазов и базовой поверхности 6 с точностью 0,005 мм на длине 1000 мм.Поверхность 1 рационально восстанавливать финишным строганием, поверхности 2 и 5 - чугунными притирами, поверхность 4 - шабрением по поверочной линейке и сопрягаемой поверхности каретки, а клиновую поверхность 3- шабрением по поверочной линейке.
Ремонт целесообразно начинать с поверхности 1, так как при этом снимают напряжении (вследствие паклена), которые возникли в процессе эксплуатации, а завершать ремонтом поверхностей 2, 4 и 5, сопрягаемых с кареткой, площадь которых значительно меньше зеркала 1.
При отсутствии возможности строгания эту поверхность следует ремонтировать шабрением.
Рисунок 6.2 -Схема ремонт стола.
Ремонт направляющих каретки
При ремонте каретки (рис. 6.3, а) необходимо восстановить: прямолинейность поверхностей 2, 3, 4, 5, 7, 8, 9 я 10 и параллельность поверхностей 2 и 5 к поверхностям 7 и 10 по направлениям в—в и д—д,допуская отклонения до 0,005 мм на длине 1000 мм; отклонения от параллельности поверхностей 3 и 4 — 0,005 мм на длине 1000 мм и от перпендикулярности поверхностей 4 и 9 по направлениям г-ги е-е - 0,005 мм на длине 1000 мм.
Поверхности 2, 5, 7 и 10 накладных направляющих, как правило, изнашиваются незначительно (не менее 0,01—0,02 мм) и поэтому рационально их ремонтировать без снятия с места с помощью чугунных притиров (рис. 6.3, в). Чистота поверхностей должна быть V10.
При больших износах планки снимают, шлифуют, затем устанавливают на место, шабрят поверхности 1, 6, 11 и12 каретки и доводят притирами (рис. 6.3, в).
Поверхности 3 и 9 целесообразно ремонтировать шабрением, добиваясь высокой точности сопряжения с поверхностью 5 (рис. 6.1) станины и поверхностью 3 (рис. 6.2) стола. Количество пятен при проверке по бликам — 20—25 на площади 25x25 мм. Контактирование этих поверхностей осуществить после установки на сопряженные поверхности планок станины и стола сепараторов с исправными роликами.
Ремонт направляющих каретки экономически целесообразно начинать с больших поверхностей, сопрягаемых с направляющими стола, а окончательную выверку осуществлять за счет меньших поверхностей, сопрягаемых со станиной. При этом приходится снимать значительно меньше металла, на что затрачивается намного меньше времени.
Рисунок 6.3 - Направляющие каретки
а — общий вид каретки; б — схема проверки направляющих; в — схема притира поверхностей.
Дата добавления: 2018-04-15; просмотров: 866; Мы поможем в написании вашей работы! |
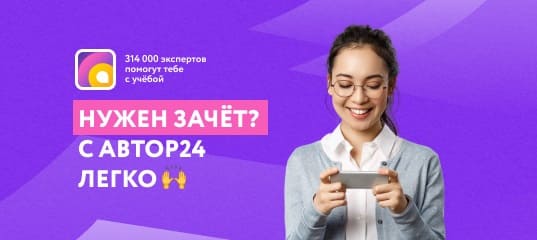
Мы поможем в написании ваших работ!