Оборудование, приборы и материалы
Министерство образования и науки Украины
Донбасская государственная машиностроительная академия
Кафедра технологии и управления производством
Методические указания
к лабораторным работам и практическим занятиям по дисциплине
"Технологические основы машиностроения"
для студентов специальностей инструментальное производство и металлорежущее оборудование
Краматорск 2003
Министерство образования и науки Украины
Донбасская государственная машиностроительная академия
Кафедра технологии и управления производством
Методические указания
к лабораторным работам и практическим занятиям по дисциплине
"Технологические основы машиностроения"
для студентов специальностей инструментальное производство и металлорежущее оборудование
Утверждено
на заседании кафедры
технологии и управления
производством
протокол №37 от 03.06.03
Краматорск 2003
УДК 621.91
Методические указания к лабораторным работам и практическим занятиям по дисциплине "Технологические основы машиностроения" для студентов специальностей ИП и МС / Сост.: А.А. Попивненко,
Ф.А. Фоменко - Краматорск: ДГМА, 2003. - с.
Содержат общие сведения, которые необходимы для выполнения лабораторных работ и практических занятий.
Составители: А. А. Попивненко, ст. препод.,
|
|
Ф.А. Фоменко, ассист.
Ответственный за С. В. Ковалевский, зав. каф.
выпуск
Лабораторная работа № 1
Исследование влияния технологических факторов на
качество поверхности обработанной детали
Цель работы – исследовать влияние подачи и радиуса скругления вершины режущего инструмента на шероховатость обработанной поверхности.
Общие сведения
Шероховатостью называется совокупность неровностей с относительно малыми шагами на определенной базовой длине. Шероховатость существенно влияет на эксплуатационные свойства деталей и зависит от разных факторов (режимов резания, параметров режущего инструмента, физико-механических свойств обрабатываемого материала, качества смазочно-охлаждающей жидкости и т. д.).
Наиболее просто высоту неровностей расчетного профиля обработанной поверхности (в случае строгания, точения, торцового фрезерования) можно определить по формуле проф. В.Л. Чебышева, что получена из совместного решения уравнения двух окружностей радиусом, который равняется радиусу скругления вершины резца, смещенных на величину подачи
(рисунок 1)
Рисунок 1 – Схема образования профиля обработанной поверхности
|
|
, (1)
где RzТ – расчетная величина неровностей, мм;
r - радиус скругления вершины резца, мм;
s - подача, мм/об.
Параметры шероховатости поверхности, регламентированы
ГОСТ 2789-73. К высотным параметрам шероховатости относятся среднее арифметическое отклонение профиля Ra, высота неровностей профиля по десяти точкам Rz.
Raопределяют по абсолютным значениям отклонений профиля y(x), (yi) в границах базовой длины:
,
(2)
где n - количество дискретно измеренных отклонений.
Rzопределяется как среднее арифметическое суммы абсолютных значений высот пяти наибольших выступов Hmax и пяти наибольших впадин Нmin в границах базовой длины
, (3)
Порядок выполнения работы
1. Определить шероховатость поверхности Ra для любого из образцов, обработанных фрезами с радиусами скругления вершины 1, 3 и 5 мм при подачах 45, 90 и 180 мм/мин и занести результаты измерений в таблицу 1. Каждый обработанный участок замерять по 3 раза. Обработка заготовок осуществлялась при вращении фрезы с частотой n = 565 мин-1 .
Таблица 1 – Результаты измерений шероховатости поверхности
S, мм/мин | r, мм | Ra1, мм | Ra2, мм | Ra3, мм | Raср, мкм | Raексп, мкм | Rzтеор, мкм |
45 90 180 | 1 | ||||||
45 90 180 | 3 | ||||||
45 90 180 | 5 |
|
|
2. Определить высоту неровностей профиля для всех соединений измеренных параметров, используя зависимость (1), а также определить величину Rz, учитывая измеренные значения Ra по зависимости Rz = 4Ra и записать в таблицу 1.
3. На основе расчетных зависимостей и исследовательских данных построить два графика зависимости неровностей профиля от величины подачи Rz = f(s) и радиуса скругления резца Rz = f(r).
Содержание отчета
1 Наименование и цель работы.
2 Схема образования шероховатости поверхности.
3 Таблица результатов измерений.
4 Графики зависимостей неровностей профиля от подачи и радиуса вершины резца.
Контрольные вопросы
1 Что называется шероховатостью поверхности, ее высотные параметры?
2 Как определяется высота неровностей профиля расчетным методом?
3 Как влияют на шероховатость поверхности подача и радиус скругления вершины режущего инструмента?
Лабораторная работа № 2
Исследование влияния погрешностей базирования
на точность обработки
|
|
Цель работы – изучить причины возникновения погрешностей базирования, способы их определения и уменьшения.
Общие сведения
Правильное базирование и закрепление заготовок при обработке оказывает существенное влияние на точность и качество обработки.
Базирование – придание заготовке или собираемому изделию требуемого положения относительно выбранной системы координат при механической обработке или сборке.
База – поверхность или выполняющее ту же функцию сочетание поверхностей, ось, точка, принадлежащее заготовке или изделию и используемая для базирования
Базы могут быть классифицированы по назначению:
- конструкторская (основная, вспомогательная);
- технологическая;
- измерительная;
по лишаемым степеням свободы:
- установочная;
- направляющая;
- опорная;
- двойная направляющая;
- двойная опорная;
по характеру проявления:
- скрытая;
- явная.
Погрешность базирования имеет место при несовмещении установочной и измерительной баз, при обработке на предварительно настроенных станках и зависит от допуска на размер и погрешности формы базовых поверхностей. Величина погрешности базирования может быть подсчитана на основании геометрических соотношений. Она является частью погрешности установки, которая определяется по формуле:
,
где – погрешность базирования;
– погрешность закрепления;
– погрешность приспособления.
Типовые схемы базирования и расчетные формулы погрешности базирования показаны в таблице 1.
Таблица 1 – Погрешности базирования при обработке в приспособлениях
Базирование | Схема установки | Формулы для расчета погрешности базирования |
В призме при обработке паза или плоскости. | ![]() | ![]() ![]() ![]() ![]() |
По центровым отверстиям: на жесткий передний центр | ![]() | ![]() ![]() |
на плавающий передний центр | ![]() | ![]() ![]() |
Содержание работы
При выполнении лабораторной работы необходимо определить погрешности базирования деталей на фрезерном станке в призмах и токарном станке в жестких центрах.
Каждое из звеньев студентов выполняет работу, осуществляя взаимный обмен местами.
Оборудование, приборы и материалы
1 Фрезерный станок, набор призм, микрометр, валики, контрольная плита.
2 Токарный станок, индикаторная стойка с индикатором, валики.
Порядок выполнения работы
1 Изучить различные схемы базирования и соответствующие им погрешности базирования (выполняется при подготовке к лабораторной работе по данным из литературных источников и таблице 1)
2 Рабочее место – фрезерный станок (данные замеров заносить в таблицу 2).
Таблица 2 – Расчет погрешности базирования детали при установке в призмах
Схема базирования |
| di | dэ | | Показания индикатора | Погрешность базирования | ||
Ci | Сэ | ![]() | ![]() | |||||
В призмах | 90° | |||||||
120° | ||||||||
Призмы выставить с выполнением условий, что эталонный валик имеет погрешность базирования .
Выполнить действия:
а) измерить микрометром диаметры валиков, выбрать dэ (dmin);
б) установить валик dэ в призму с углом 90о; настроить индикатор;
в) по диаметрам валиков di, устанавливаемым поочередно в призму с
углом , определить показания индикатора сi;
г) заменить валик и призму, повторить пп б, в.
3 Рабочее место – токарный станок (данные замеров заносить в табл. 3)
Таблица 3 – Расчет погрешности базирования детали при установке в центрах.
Схема базирования | | di | dэ | | Показания индикатора | Погрешность | ||
Ci | Сэ | ![]() | ![]() | |||||
В центрах | 60° | |||||||
Выполнить действия:
а) измерить наружный диаметр центрального отверстия, валика; определить валик с dэ (dmin);
б) установить валик c dэ в центрах токарного станка; настроить индикатор;
в) по торцам валиков с различными диаметрами di поочередно устанавливаем в центра, определить погрешность базирования с;
г) заменить валик, повторить опыты по пп.3 б, в.
Рисунок 1 – Схема формирования погрешности базирования
Дата добавления: 2018-04-05; просмотров: 369; Мы поможем в написании вашей работы! |
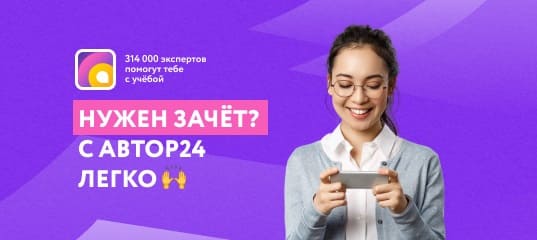
Мы поможем в написании ваших работ!