Выбор и обоснование технологической схемы производства
Поточно-агрегатная технология является более гибкой и маневренной в отношении использования технологического оборудования. При этом можно изготовлять изделия широкой номенклатуры с меньшими капитальными затратами по сравнению с конвейерной технологией. Эта технология, основанная на применении передвижных агрегатов, позволяет обрабатывать изделие за несколько проходов, что гарантирует высокое качество изделий особенно сложной конфигурации и многослойных (стеновых панелей, кровли), и позволяет производить замену устаревшего оборудования без значительной переделки линии.
По сравнению с изготовлением изделий в горизонтальном положении, кассетный способ имеет ряд преимуществ:
- при изготовлении изделий в кассетных формах, представляется возможным получать изделия с высокой точностью размеров и хорошим качеством их поверхностей, что весьма затруднительно для крупнопанельных изделий, изготовляемых в горизонтальных формах;
- ввиду того, что отформованные в кассетных установках изделия имеют не более 6% открытой поверхности, т.е. основная масса бетона находится в замкнутом пространстве, можно обеспечить более жесткий режим тепловой обработки по сравнению с пропариванием изделий в горизонтальных формах и, тем самым ускорить набор прочности бетона;
- возможность подъема температуры с большой скоростью (60-70 0С/час);
- поскольку изготовление, транспортировка и хранение стеновых панелей производится в вертикальном положении, можно транспортировать изделия с распалубочной прочностью (около 50% от проектной). В этом случае твердение бетона до отпускной прочности может протекать в специальных камерах дозревания или на промежуточных теплых складах, где одновременно может быть организована отделка и комплектация изделий.
|
|
Кассетный способ производства железобетонных изделий по сравнению с другими обеспечивает более высокую производительность труда при изготовлении и отделке изделий, требует меньшего расхода пара и электроэнергии.Однако кассетный способ формования изделий имеет и существенные недостатки, устранить которые можно только путем дальнейшего совершенствования технологического процесса. Например, для кассетного способа производства железобетонных изделий требуются пластичные бетонные смеси, что приводит не только к большому перерасходу цемента, но и к появлению в готовых изделиях большого количества усадочных трещин. Кроме того, удельная металлоемкость форм и оборудования значительно выше, чем при агрегатном - поточном способе. К недостаткам кассетного способа следует отнести недостаток контактного обогрева в кассетах, обусловленный особенностями теплообмена, связанного с конденсацией пара в тепловых отсеках, а также большие затраты ручного труда.
|
|
3.2.Описание технологической схемы производства панелей внутренних стен.
Цемент поступает на завод железнодорожным транспортом.
Песок и щебень поступают автомобильным и железнодорожным транспортом.
Металл поступают автомобильным транспортом.
Для разгрузки песка и щебня имеются два поста, оборудованные вагоновибраторами, бурорыхлительными машинами и плужками для сдвига материала с платформы. Завод снабжен закрытым эстакадно-полубункерным складом заполнителей. Покрытие склада выполнено из волнистых асбестоцементных листов по сборному железобетонному каркасу.
Выдача заполнителей со склада производится через устроенные в перекрытии подштабельной галереи течки и лотковые вибраторы-питатели на горизонтальный конвейер подштабельной галереи, а затем с помощью наклонного конвейера в бетоносмесительный цех.
Цемент из вагонов пневмотранспортёром подается в силосные банки.
Склад оборудован пневматическим разгрузчиком цемента, сдвоенным приемным бункером с пневматическими подъемниками цемента для транспортирования его в верхний аэрожелоб и силосы, донными разгружателями, нижними аэрожелобами и пневматическим винтовым насосом для транспортирования цемента в бункер БСУ.
|
|
Транспортирование материала в бетоносмесительное отделение.
Со склада инертных материалов песок и щебень по наклонной галерее ленточными транспортерами подается в бункерное отделение бетоносмесительного узла. Цемент с помощью пневмотранспортера поступает в бетоносмесительное отделение.
Бетоносмесительный узел
Приготовление бетонной смеси осуществляется в БСУ с вертикальной схемой приготовления бетонной смеси. БСУ размещается с продольной стороны формовочного пролета.
Дозирование компонентов.
Приготовление бетонных смесей - важное звено технологической схемы производства железобетонных изделий. От работы бетоносмесительного узла зависят расход цемента, качество и себестоимость продукции, а также экологические условия внутри и вокруг цеха.
Приготовление бетонной смеси сводится к дозированию и смешиванию составляющих материалов. От точности дозирования зависят соответствие фактического состава к заданному, а также постоянство этого состава от замеса к замесу. По существующим нормам допускаемые отклонения при дозировании материалов на замес не должны превышать ±1% по массе для цемента и воды и ± 2% для заполнителей. Для поддержания количества воды в смеси на заданном уровне необходимо помимо обеспечения точности дозирования воды на замес также систематически осуществлять корректировку назначенной дозы воды в соответствии с изменяющейся влажностью заполнителей.
|
|
На данном заводе весовое дозирование составляющих материалов осуществляется в бетоносмесительном узле, который оснащен автоматизированной системой управления ЦИКЛ - БС. Для сокращения потерь цемента пульт управления выведен за пределы дозаторного управления, для снижения запыленности разгрузка осуществляется пневмотранспортом. Автоматизированная система управления не только обеспечивает необходимую точность, но и позволяют сократить длительность дозирования всех компонентов на замес до 30 - 40 сек., а также сократить численность обслуживающего персонала. В автоматических дозирующих установках весь цикл дозирования материалов, включая выдачу их в бетоносмесители, производится по заданной программе без участия оператора.
Рекомендуется следующий порядок подачи составляющих в бетоносмеситель: а) щебень, вода, б) песок, цемент.
В процессе приготовления бетонной смеси используется омагниченная с помощью магнитотронов вода. Магнитотрон - это стальная труба внутри, которой вмонтирован сильный магнит. Само устройство включено в систему подачи воды — весовой дозатор. Сущность омагничивания жидкой среды заключается в пропускании ее через магнитотрон, в котором создаются магнитные поля. Это ведет к изменению структуры, физико-механических свойств воды и характера взаимодействия молекул воды друг с другом. Омагниченная вода придает бетонной смеси большую подвижность, что позволяет отказаться от суперпластификатора и, при этом, экономится цемент на 10 %. Необходимо отметить, что омагниченная вода- это экологически чистый безопасный продукт, что нельзя сказать о суперпластификаторе.
Перемешивание компонентов
Так как бетонная смесь подвижная, перемешивание компонентов бетонной смеси осуществляется в бетоносмесителе гравитационного действия. Принцип работы бетоносмесителя гравитационного действия - смешивание при свободном падении материалов в смесителе в результате многократного подъема и падения с некоторой высоты частиц смешиваемых материалов и погружением их, при этом, в основную массу смеси.
Подвижность получаемой бетонной смеси 15 см - ПЗ (в соответствии с ГОСТ 7473-94). Время перемешивания материалов - не менее трех минут.
Арматурный цех
Арматурный цех обеспечивает готовыми арматурными изделиями (сетками, каркасами и монтажными петлями) формовочный цех завода. Цех оборудован высокопроизводительными машинами для изготовления больших сеток, гибочными станками для изготовления монтажных петель. Небольшие плоские каркасы изготавливают на аппаратах точечной сварки. В специальных кондукторах - манипуляторах собирают объемные каркасы для армирования стеновых панелей.
Для изготовления арматурных каркасов и сеток применяется горячекатаная сталь классов А –I, А –Ш по ГОСТ 5781-82 и обыкновенная холоднотянутая проволока класса В -1 или Вр -1по ГОСТ 6727 - 80.
Готовые изделия из арматурного цеха доставляются в формовочный цех к местам укладки их в формы.
Формовочный цех
Формование внутренних стеновых панелей с готовыми электроканалами производится в кассетных формах.
Отличительной особенностью этого способа является вертикальное расположение форм и формуемого изделия. Кассетная установка состоит из спаренных отсеков с разделительными стенками между ними и из паровых рубашек через каждые два отсека.
Подготовка кассетных форм
Подготовка кассетных форм к бетонированию производится после распалубки и извлечения всех готовых изделий. Продолжительность распалубки, включая разборку кассеты и извлечение изделий, составляет не более 30 мин. Она начинается с профилактической очистки разделительных стенок щетками портальной установки, в то время, как тщательная механическая обработка производится через 30 - 50 оборотов кассетной установки.
На очищенные поверхности наносится эмульсионный состав ОЭ - 2, который готовится в установке СМЖ-18А и ею же наносится. В смазке ОЭ -2 масляной составляющей является эмульсол марки ЭКС-А. Смазка готовится на омагниченной воде. Омагничивание жидкой среды разжижает смазку, позволяет ее наносить тонким слоем, что снижает расход эмульсола до 20%. Состав смазки: ЭКС-А-50%, известковая вода — 50%.
Установка арматурных каркасов и закладных деталей
В очищенную и смазанную кассетную установку устанавливают в проектное положение арматуру и полихлорвиниловые трубки электроканалов. Продолжительность подготовки кассеты (чистка и смазка, установка арматуры и закладных деталей, сборка кассеты) составляет не более 40 мин.
Укладка бетонной смеси
Бетонная смесь системой ленточных конвейеров подается в бетонораздатчик СМЖ -306А, который предназначен для подачи и укладки бетонной смеси в отсеки кассетных установок. Благодаря тому, что бетонная смесь очень подвижная (осадка конуса около 15 см), она легко заполняет рабочие отсеки.
Уплотнение бетонной смеси
Уплотнение бетонной смеси осуществляется путем вибрирования разделительных стенок кассеты специальными навесными вибраторами. В качестве вибровозбудителей использованы вибраторы С-414 мощностью 0,8 кВт.
После уплотнения бетонной смеси верхнюю поверхность отформованных изделий заглаживают, а затем, покрывают крышками с целью предотвращения интенсивного испарения влаги и экономии тепла.
Кассетную форму следует заполнять не более чем, в 3-4 приема с вибрационной проработкой каждого слоя. При этом следят, чтобы укладка бетонной смеси производилась горизонтальными слоями, а в двух смежных отсеках разница в уровнях слоев не превышала 0,5 м.
Продолжительность укладки и уплотнения бетонной смеси составляет не более 50мин.
Предварительная выдержка изделий
Подъем температуры является наиболее ответственным этапом тепловой обработки, так как возможные нарушения в структуре бетона протекают именно на этой стадии тепловой обработки. Величина и характер структурных нарушений за висят от достигнутой бетоном к началу тепловой обработки прочности, от скорости подъема температуры среды в камере и ряда других факторов, способствующих или препятствующих развитию деструктивных процессов.
Предварительное выдерживание сформованных изделий перед тепловой обработкой имеет целью обеспечить бетону ту минимальную необходимую начальную (критическую) прочность бетона, при которой он может воспринимать тепловое воздействие при принятом режиме без нарушения его структуры. Оптимальное время выдерживания зависит от вида и марки цемента, начального водосодержания бетонной смеси, В/Ц, температуры среды; оно должно составлять в среднем 2-4 часа. Время предварительной выдержки изделий принимаем - 2 часа.
Тепловая обработка изделий
Режим тепловой обработки следующий:
1. Подъем температуры до 80°С - 3 часа.
2. Изотермическая выдержка - 3 часа.
3. Период остывания (термосное выдерживание) бетона - 2 часа.
Распалубка изделий
Распалубку изделий осуществляют распалубочной машиной СМЖ- 3301Б путем последовательного перемещения разделительных стенок кассетной формы.
Подготовка к отделке изделий
После этого, изделие поступает на стенд доводки. Для ремонта сколов бетона, затирки раковин и восстановления бетонного «зуба» применяется раствор следующего состава: цемент — 1 часть, песок - 3 части, эмульсия ПВА — 0,5% от массы сухих составляющих.
Отделка изделий
Из растворомешалки отделочный раствор подается в питатели, из которых по трубопроводам в емкость отделочной машины.
Для отделки внутренних стеновых панелей применяется отделочный раствор следующего состава: известковое тесто - 1 часть;
перлитовый песок (фракций до 2,5 мм).
Кондиционную стеновую панель без сколов и вырвов с закрытыми отверстиями электроканалов мостовым краном погружают на всю высоту в металлическую ванну, наполненную известково-перлитовым раствором.
Включается в работу системы механических шпателей, с двух сторон резиновые шпатели прижимаются к поверхности изделия и, по мере его подъема из ванны втирают отделочный раствор в раковины и поры на поверхности изделия.
Продолжительность отделки одного изделия составляет 5-6 минут.
Готовое изделие доводится вручную, маркируется и направляется на промежуточный цеховой склад. Далее готовые изделия транспортируются на склад самоходной тележкой СМЖ -151.
Склад готовой продукции
Хранение готовых железобетонных изделий предусмотрено в открытых штабелях открытого склада, снабженного четырьмя мостовыми кранами с траверсами, маркой МК-5, грузоподъемностью 5 т. Склад двухпролётный, ширина каждого пролета 18м и длина 100 м.
Дата добавления: 2018-04-05; просмотров: 424; Мы поможем в написании вашей работы! |
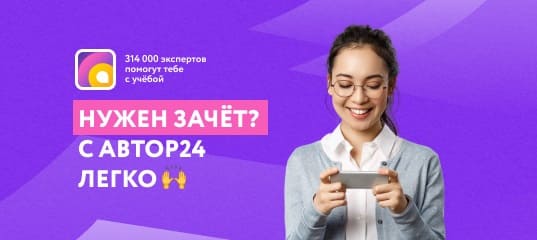
Мы поможем в написании ваших работ!