Расчет количества печей в ферросплавном цехе
МИНИСТЕРСТВО ОБРАЗОВАНИЯ И НАУКИ РЕСПУБЛИКИ КАЗАХСТАН
АКТЮБИНСКИЙ ГОСУДАРСТВЕННЫЙУНИВЕРСИТЕТ
им. К.ЖУБАНОВА
Технический факультет
Кафедра «Металлургия»
Специальность- 050709 Металлургия
Курсовая проект
По дисциплине: «Основы проектирования и проектирование металлургических объектов»
Выполнил: студент группы Мр – 4
Әділ Ә. Б.
Принял: к.т.н., доцент
Кузбаков Ж.И.
Актобе 2016
Содержание
I. Введение…………………………………………………………………………3
|
|
II. Основная часть:
1. Расчет количества печей в ферросплавном цехе…………………….4
2. Отделение шихтоподготовки …………………………………………7
2.1. Расчет шихтоподготовительных складов ……………………….10
Плавильный корпус:
3.1 . Печной пролет ………………………………………………………13
3.2. Разливочный пролет ..………………………………………………14
3.2.1. Расчет оборудования разливочного пролета ……………………15
4. Склад готовой продукции ……………………………………………17
![]() |
III. Вывод ………………………………………………………………………18
IV. Список используемой литературы ………………………………………19
|
|
![]() |
I. Введение
Производственный процесс в ферросплавном цехе включает три последовательные стадии: подготовки шихтовых материалов, плавки подготовленной шихты в электропечах и разделки готового сплава. В соответствии с этим современный ферросплавный цех состоит из отделения шихтоподготовки, плавильного корпуса и склада готовой продукции.
Отделение шихтоподготовки предназначено для бесперебойной работы ферросплавных печей запаса шихтовых материалов, шлакообразующих, огнеупорных и других материалов, с тем, чтобы по мере надобности можно было обеспечить их беспрепятственную и своевременную подачу в плавильный корпус.
Для механизации погрузочно-разгрузочных работ мостовые краны оборудуют магнитными плитами и грейферами, кроме того, широко используют контейнеры. Все поступающие и отгружаемые материалы обязательно взвешивают на стационарных и крановых весах, а также на весах раздаточных тележек. Запас материалов в шихтовом отделении определяется на основе нормативов с учетом возможности оперативной доставки.
Плавильный корпус ферросплавного цеха в свою очередь делится на печной, разливочный, трансформаторный, шихтовый и остывочный пролет.
|
|
Число ферросплавных печей в печном пролете цеха определяют с учетом годовой программы производства, емкости ферросплавных печей, их производительности, сортамента выплавляемых марок высокоуглеродистого феррохрома и массы слитков, которые могут быть далее с легкостью раздроблены.
Ферросплавные печи оборудуют как средствами для отсоса из рабочего пространства отходящих газов, так и защитными от избыточного шума устройствами. В ряде цехов загрузку шлакообразующих, восстановителей и руды осуществляют через загрузочные желоба расположенные в своде. На рабочей площадке у плавильных печей также располагают другое оборудование.
В торцах печного пролета отводят участки для стеллажей электродов и огнеупорных кирпичей. Здесь же выделяют площадь для выполнения ремонта охладительной аппаратуры, электрододержателей и другого оборудования.
Разливочный пролет предназначен для приема и разливки готового сплава и удаления шлака. С ростом мощности ферросплавных печей объемно-планировачные решения здания плавильного корпуса совершенствовались по пути сокращения числа пролетов за счет выноса шихтового и разливочного пролетов за пределы здания и ликвидации остывочного пролета.
|
|
Расчет количества печей в ферросплавном цехе
Необходимое количество ферросплавных электропечей в проектируемом цехе определяется заданным объемом производства ферросплавов и установленной мощностью выбранной печи и рассчитывается по формуле
Годовая производительность ферросплавной электропечи определяется из выражения
Суточная производительность ферросплавной электропечи непрерывного и периодического действия зависит от установленной мощности печного трансформатора и типа выплавляемого сплава. Она рассчитывается по единой формуле
Обычно при расчетах суточной производительности ферросплавных печей практикуется замена коэффициента Ки на произведение трех составляющих его коэффициентов: загрузки трансформатора по мощности ; использования трансформатора во времени
;учитывающего колебания напряжения в питающей сети
. Рекомендуемые нормами технологического проектирования числовые значения коэффициентов
,
,
, а также для печей, выплавляющих различные сплавы, сведены в таблице. Следует, однако, иметь в виду, что в соответствии новыми требованиями к энергосистемам все потребители должны иметь cos
= 0,92-0,96, что обеспечивается при оснащении ферросплавных электропечей установками продольно-емкостной компенсации реактивной мощности (УПК). Удельный расход электроэнергии при выплавке данного сплава определяется по лучшим результатам работы освоенных аналогичных печей.
Фактическое время работы печи за год вычисляется путем вычитания из календарного времени длительности холодных
и горячих
простоев печи:
Здесь номинальное время работы печи, сутки.
Нормативные значения номинального времени для различных сплавов и печей представлены в таблице. Длительность горячих простоев колеблется в пределах 0,5-1,5% от календарного времени (365 суток), при этом, максимальное значение принимают для рафинировочных печей. Полученное расчетное число печей в цехе округляют до большого целого числа. При окончательном выборе количества печей в ферросплавном цехе следует учитывать, что это число должно быть кратно двум и не превышать восьми. Число печей, кратное двум, выбирают из соображений удобства разливки сплава двух печей на общей разливочной машине и снабжения шихтой двух печей с помощью одного тракта шихтоподачи.
Если расчетное число печей в цехе превышает восемь, то следует устанавливать печи большей мощности или строить два цеха вместо одного.
Таблица 4. Коэффициенты для расчета производительности рудовосстановительных и рафинировочных электропечей
Вид ферросплавов | W, МВА | Тип электропечи | ![]() | ![]() | ![]() | ![]() |
Феррохром высокоуглеродистый | 16,5-33 | Закрытая рудовосстановительная с УПК | 0,92 | 0,96 | 0,96 | 0,99 |
Таблица 5. Нормативы номинального времени ферросплавных электропечей
Вид сплава | Номинальная мощность трансформатора, МВА | Режим работы печи | Число номинальных суток работы в году |
Феррохром высокоуглеродистый | 16,5-33 | закрытый | 355-350 |
Для выплавки углеродистого феррохрома используют электропечи с мощностью 16,5 / 21 / 24 / 33 МВА. Рассмотрим несколько вариантов:
1. Суточная производительность одной ферросплавной печи с мощностью трансформатора 16,5 МВА
Годовая производительность одной ферросплавной печи
Необходимое количество ферросплавных печей
2. Суточная производительность одной ферросплавной печи с мощностью трансформатора 21 МВА
Годовая производительность одной ферросплавной печи
Необходимое количество ферросплавных печей
3. Суточная производительность одной ферросплавной печи с мощностью трансформатора 24 МВА
Годовая производительность одной ферросплавной печи
Необходимое количество ферросплавных печей
.
4. Суточная производительность одной ферросплавной печи с мощностью трансформатора 33 МВА
Годовая производительность одной ферросплавной печи
Необходимое количество ферросплавных печей
.
Производительность в 140000 тонн в год можно обеспечить 4 печами с мощностью трансформатора 16,5 МВА или 2 печами с мощностью трансформатора 33 МВА . Из двух этих вариантов берем 2 печа с мощностью трансформатора 33МВА, так как он является наиболее эффективным.
2. Отделение шихтоподготовки
Отделение шихтоподготовки ферросплавного цеха предназначено для хранения, подготовки и дозирования шихтовых материалов. На ферросплавных заводах используют два различных варианта проектных решений шихтового хозяйства. На старых заводах каждый цех имеет свой собственный закрытый склад шихты, на открытом заводском складе обычно хранятся лишь те материалы, которые необходимы для работы нескольких цехов. Новые заводы отличаются централизованным хранением, подготовкой и распределением материалов по цехам.
Шихтовое хозяйство современного ферросплавного цеха, оборудованного мощными рудовосстановительными печами с централизованным обеспечением шихтой, включает напольный открытый склад сырых материалов (ССМ), корпус вагоноопрокидывателей (ВО), закрытый склад, корпус подготовки материалов (КПМ), корпус шихтовых бункеров (КШЮ) с подготовленными материалами, дозировочные отделения (ДО) или дозировочные пункты (ДП), которые могут быть совмещены с КПМ или КШБ.
В шихтовом хозяйстве цеха для производства марганцевых и хромистых ферросплавов может быть предусмотрена соответствующая агломерационная (или брикетировочная) фабрика и цех обжига извести.
Напольный открытый склад сырых материалов служит для создания на заводе необходимого запаса сырых материалов, поставляемых из отдаленных районов, а также ведущих рудных материалов, суточный расход которых значителен. Материалы на этом складе хранятся в штабелях, разгружаются из вагонов козловыми грейферными кранами и в дальнейшем подаются железнодорожным транспортом через корпус ВО или по конвейерным галереям в ССМ.
При проектировании современных ферросплавных цехов для хранения шихтовых материалов предусматривается три типа складов: закрытый грейферный с железнодорожной колеей, проходящей посередине склада; закрытый безкрановый ангарного типа с конвейерной подачей и выдачей материалов; открытый с конвейерной подачей сырых материалов и мостовым грейферным перегружателем, который принимает, штабелирует и выдает материалы на подготовку.
Корпус ВО представляет собой здание ангарного типа с двумя сквозными железнодорожными путями, На каждом из которых установлен роторный стационарный ВО. С помощью ВО материал из вагона выгружается в подземные бункера, оборудованные тарельчатыми питателями, и далее конвейерами большой производительности, направляется на ССМ. В корпусе ССМ крупных ферросплавных цехов обычно не имеется железнодорожного въезда, а склад оборудован грейферными кранами, с помощью которых материал подается в КПМ.
В КПМ установлено необходимое сушильное, дробильное и классифицирующее оборудование, тип и количество которого определяется видами применяемых шихтовых материалов. Для дробления кокса используют четырехвалковые дробилки 13Д 900/700 с диаметром валков 900 мм, разгрузочной щелью 0-50 мм, производительностью 35 т/ч; кварцита-конусные дробилки ККД-500 с разгрузочной щелью 75мм, производительность 150
; стружки-стружкодробилки СМ-2 с разгрузочной щелью 25 мм, производительностью 1,5-5 т/ч. Для сортировки кокса применяют вибрационный грохот ГВР-1 производительностью 300 т/ч. Транспортные пути восстановителя и рудного материала во избежания их преждевременного перемешивания из-за просыпи во время разрыва ленты не должны пересекаться. При объединенном шихтовом хозяйстве подготовленные шихтовые материалы из КПМ поступают на центральный распределительный пункт (ЦРП), Где с помощью реверсивных конвейеров и системы передаточных конвейеров распределяются по ДО плавильных цехов.
На ферросплавных заводах применяется порционное и непрерывное дозирование шихты. При порционном дозировании используют порционные весовые автоматы и вращающиеся барабанные смесители.
На складе шихты, подготовленные шихтовые материалы загружают в отдельные для каждой печи дозировочные установки, оборудованные автодозаторами. Затем компоненты, образующие калошу шихты, выгружают в конвейер или в скиповый подъемник и транспортируют в плавильный корпус цеха к печам. При проектировании новых цехов намечают дозировочные узлы вынести из помещения склада шихты, а подготовленную шихту подавать в их бункера по конвейерам непосредственно из отделений подготовки. В дозировочных узлах установлены автодозаторы непрерывного действия, работающие с заданной производительностью. Шихтовые материалы выдаются при этом одновременно, что обеспечивает их смешение. При непрерывном дозировании составляющие шихты выдаются ленточными автоматическими дозаторами непрерывного действия, работающими с заданной производительностью. Для непрерывного дозирования используют дозаторы типа ДН-23 производительностью 65 т/ч (для кокса), 100 (для кварцита), 125 т/ч (для стружки). При одновременном дозировании заданное соотношение производительностей всех работающих дозаторов, соответствующее требуемому соотношению навесок компонентов в калоше шихты, соблюдается постоянным с помощью электронного регулятора соотношения.
Регулятор соотношения управляет группой работающих дозаторов по выходному сигналу ведущего дозатора. При любом мгновенном отклонении производительности ведущего дозатора регулятор соотношения пропорционально изменяет производительность остальных дозаторов.Все компоненты шихты выдаются на движущуюся конвейерную ленту и направляются в приемные бункера печей. На ленте компоненты шихты, дозируемые одновременно в заданном соотношении, располагаются в виде слоя смешанных материалов.
В приемных бункерах печей шихта представляет собой достаточно однородную смесь с требуемым соотношением компонентов шихты.
В случае небольших и средних грузопотоков шихты все печи плавильного
корпуса обслуживается одной линией шихтоподачи; при больших грузопотоках
такая линия обеспечивает шихтой каждые две печи. Применяются три варианта подачи сдозированной шихты в печные бункера: кольцевой, линейной, скиповой.
При кольцевой и скиповой подачах шихты отделение шихтоподготовки расположено параллельно плавильному корпусу, а при линейной - в одну линию с плавильным корпусом. В последнем случае непрерывно дозируемые шихтовые материалы поступают сначала на горизонтальный конвейер, затем наклонным конвейером подаются на шихтовую площадку плавильного корпуса, перегружаются на расположенный вдоль цеха конвейер, с которого с помощью плужковых сбрасывателей или сбрасывающих тележек направляются в печные бункера.
Кольцевой способ подачи шихты позволяет уменьшить длину конвейерных лент, число перевалок и потери шихтовых материалов, а также снизить на 13-15% капитальные затраты на строительство цеха. Подготовленные шихтовые материалы транспортируются грейферными кранами в бункера готовой шихты. С помощью непрерывных дозаторов заданное количество различных шихтовых материалов подается на горизонтальный конвейер, затем по наклонному в печные карманы. Одна группа бункеров готовой шихты обслуживает одновременно две печи.
При скиповой подаче компоненты шихты дозируются в отделении шихтоподготовки, а шихта в плавильный корпус передается скиповым подъемником. При этом обеспечивается автоматическая подача шихты в печные карманы. Каждая печь обслуживается отдельной группой бункеров готовой шихты.
Себестоимость хранения, подготовки, дозировки и транспортировки шихтовых материалов в печные карманы при скиповой подаче меньше, чем при конвейерной. При движении шихты по конвейерному тракту за счет истирания образуется дополнительно 310% коксовой мелочи фракции менее 5 мм. За счет налипания на ленту промасленной стружки и кокса их потери увеличиваются на 4,5% и 3% соответственно.
В современных цехах с мощными рудовосстановительными печами применяются в основном конвейерная подача сыпучих материалов. При этом в связи с малым уклоном конвейерных лент (17%) и большой высотой цеха, галереи подачи сыпучих материалов занимают значительные площади.
![]() |
Дата добавления: 2018-04-05; просмотров: 673; Мы поможем в написании вашей работы! |
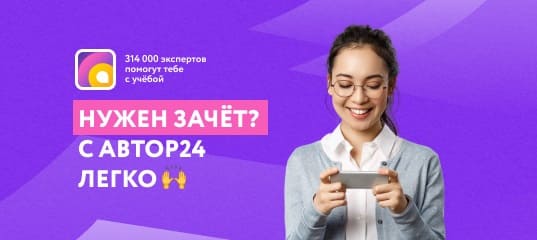
Мы поможем в написании ваших работ!