Ультразвуковой контроль в строительстве
5.1 Физические основы ультразвукового контроля.
Выявление скрытых дефектов основано на распространении упругих волн и их изменении при наличии дефектов. Ультразвуковые колебания так же, как и звуковые, представляют собой механические колебания частиц упругой среды. Ультразвуковыми называются упругие колебания, частота которых больше 20 кГц, то есть выше частоты слышимого человеком звука. Упругие колебания могут быть возбуждены в газообразной, жидкой и твердой средах. Колебательное движение возбужденных частиц благодаря наличию упругих связей вызывает ультразвуковые волны.
Для получения ультразвука частот (1 – 5 мГц) применяют пьезоэлектрические, магнито-стрикционные, электромагнитно-акустические и другие преобразователи. Наибольшее распространение получили пьезоэлектрические преобразователи (ПЭП), в которых активными являются пьезоэлементы, изготовленные из монокристалла кварца или пьезокерамических материалов — титаната бария, цирконат титаната свинца и др. Для изготовления преобразователей (вставок, резонаторов) рельсовых дефектоскопов чаще всего используют ПЭП из цирконат титаната свинца марки 19 (ЦТС-19). На плоские поверхности пьезоэлементов наносят тонкие слои серебра, служащие электродами. При подведении к электродам знакопеременного электрического напряжения пьезоэлемент совершает вынужденные механические колебания (растягивается и сжимается, как это показано на рис. 10.6) с частотой подаваемого электрического напряжения. Данное явление называется обратным пьезоэффектом.
|
|
а)
б)
Рис. 10.6. Иллюстрация обратного пьезоэффекта
Конструкция пьезоэлемента представляет собой некую электрическую емкость, изменяющуюся при изменении размеров элемента. Таким образом можно изменять электрические параметры датчика, что формирует высокочастотные (ультразвуковые) импульсы, необходимые для работы ультразвуковых дефектоскопов.
При воздействии на пьезоэлемент упругих механических колебаний на его электродах возникает знакопеременное электрическое напряжение, величина которого пропорциональна прилагаемому к пьезоэлементу усилию (рис. 10.7). Это явление носит название прямого пьезоэффекта.
Рис. 10.7. Прямой пьезоэффект
5.2 Ультразвуковая дефектоскопия и толщинометрия.
Различают две группы акустических методов неразрушающего контроля: ультразвуковая дефектоскопия и структуроскопия, основанные на исследовании процесса распространения ультразвуковых упругих колебаний, специально вводимых в контролируемый объект; акустической эмиссии, основанной на исследовании упругих волн, возникающих в контролируемом объекте в момент образования или развития в нем несплошностей. Для излучения и регистрации упругих колебаний применяют электроакустичес-кие или электромагнитоакустические преобразователи. В практике контроля металлических конструкций используют теневой, зеркально-теневой и эхо-импульсный методы ультразвуковой дефектоскопии и метод ультразвукового структурного анализа. При ультразвуковой дефектоскопии признаком обнаружения дефекта служит:
|
|
для теневого метода – уменьшение интенсивности (амплитуды) ультразвуковой волны, прошедшей через объект от излучающего (И) преобразователя к приемному (П);
для зеркально-теневого – уменьшение интенсивности (амплитуды) ультразвуковой волны, отраженной от противоположной (донной) поверхности объекта (уменьшение донного сигнала);
для эхо-метода – прием преобразователем волны, отраженной от дефекта (прием эхо-сигнала).
При ультразвуковом структурном анализе признак обнаружения дефекта – превышение ослабления ультразвуковой волны, прошедшей через контролируемый объект, над соответствующим ослаблением в контрольном образце.
В практике контроля рельсов получили распространение теневой, зеркально-теневой и эхо-методы ультразвуковой дефектоскопии.
|
|
5.3 Измерение прочности и глубины трещин
Основной показатель, по которому характеризуется бетон, – прочность на сжатие. Принцип определения прочности бетона ультразвуковым методом базируется на наличии функциональной связи между скоростью распространения ультразвуковых колебаний и прочностью бетона.
Ультразвуковой метод применяют для определения прочности бетона классов В7,5–В35 (марок М100–М400) на сжатие.
Прочность бетона в конструкциях определяют экспериментально по установленным градуировочным зависимостям "скорости распространения ультразвука – прочность бетона V = f(R)" или "время распространения ультразвука t – прочность бетона t = f(R)". Степень точности метода зависит от тщательности построения тарировочного графика.
Тарировочный график строится по данным прозвучивания и прочностных испытаний контрольных кубиков, приготовленных из бетона того же состава, по той же технологии, при том же режиме твердения, что и изделия или конструкции, подлежащие испытанию. При построении тарировочного графика следует руководствоваться указаниями ГОСТ 17624-87.
Для определения прочности бетона ультразвуковым методом применяются приборы: «Пульсар-1.2», «УКБ-1», «УКБ-1М», «УК-16П», «Бетон-22» и др..
|
|
Ультразвуковые измерения в бетоне проводят способами сквозного или поверхностного прозвучивания. Схема испытаний бетона приведена на рисунке 1.1.
а – схема испытания способом сквозного прозвучивания; б – то же поверхностного прозвучивания; УП – ультразвуковые преобразователи
Рисунок 1.1 – Способы ультразвукового прозвучивания бетона
При измерении времени распространения ультразвука способом сквозного прозвучивания ультразвуковые преобразователи устанавливают с противоположных сторон образца или конструкции.
Скорость ультразвука n, м/с, вычисляют по формуле:
, (1.1)
где t – время распространения ультразвука, мкс;
l – расстояние между центрами установки преобразователей (база прозвучивания), мм.
При измерении времени распространения ультразвука способом поверхностного прозвучивания ультразвуковые преобразователи устанавливают на одной стороне образца или конструкции по схеме, приведенной на рисунке 1.1.
Число измерений времени распространения ультразвука в каждом образце должно быть следующим: при сквозном прозвучивании – 3, при поверхностном – 4.
Отклонение отдельного результата измерения времени распространения ультразвука в каждом образце от среднего арифметического значения результатов измерений для данного образца не должно превышать 2 %.
Измерение времени распространения ультразвука и определение прочности бетона производятся в соответствии с указаниями паспорта (технического условия применения) данного типа прибора и ГОСТ 17624-87.
На практике нередки случаи, когда возникает необходимость определения прочности бетона эксплуатируемых конструкций при отсутствии или невозможности построения градуировочной таблицы. В этом случае определение прочности бетона проводят в зонах конструкций, изготовленных из бетона на одном виде крупного заполнителя (конструкции одной партии). Скорость распространения ультразвука n определяют не менее чем в 10 участках обследуемой зоны конструкций, по которым определяют среднее значение n. Далее намечают участки, в которых скорость распространения ультразвука имеет максимальное nmax и минимальное nmin значения, а также участок, где скорость имеет величину nn наиболее приближенную к значению n, а затем выбуривают из каждого намеченного участка не менее чем по два керна, по которым определяют значения прочности в этих участках: Rмакс, Rмин, Rф соответственно. Прочность бетона Rн находят по формуле:
, (1.2)
, (1.3)
где x – скорость (время) распространения ультразвука;
Rн – прочность определенная по уравнению,
Rмин, Rмакс – минимальное и максимальное значения прочности по испытанным сериям образцов, МПа.
Коэффициенты а1 и a0 вычисляют по формулам:
; (1.4)
; (1.5)
; (1.6)
; (1.7)
, (1.8)
где – средняя прочность бетонов, испытанных при установлении градуировочной зависимости, МПа;
N – число серий образцов, испытанных при установлении градуировочной зависимости;
Rjф, xj – единичные значения прочности и скорости (времени) распространения ультразвука для j-й серии образцов.
При определении прочности бетона по образцам, отобранным из конструкции, следует руководствоваться указаниями ГОСТ 28570-90.
Для бетонов классов прочности выше В25 прочность бетона в эксплуатируемых конструкциях может быть оценена также сравнительным методом, принимая в основу характеристики конструкции с наибольшей прочностью.
Такие конструкции, как балки, ригели, колонны, должны прозвучиваться в поперечном направлении, плита – по наименьшему размеру (ширине или толщине), а ребристая плита – по толщине ребра.
При тщательном проведении испытаний этот метод дает наиболее достоверные сведения о прочности бетона в существующих конструкциях. Недостатком его является большая трудоемкость работ по отбору и испытанию образцов.
Выявление дефектов и анализ трещин в железобетонных конструкциях
Значение раскрытия трещин при обследовании измеряется с помощью специальных оптических приборов — трубки Бриннеля, отсчетного микроскопа МПБ-2 (с 24-кратным увеличением), градуированных луп Польди, визирных луп, щупов.
Глубина трещин определяется с помощью щупов или ультразвуковых приборов, например, УКБ-1М и типа "Бетон".
При применении ультразвукового метода глубина трещины устанавливается по изменению времени распространения ультразвука как при сквозном прозвучивании, так и методом продольного профилирования при условии, что плоскость трещинообразования перпендикулярна линии прозвучивания. Глубина трещин (рис. 1.13) определяется из соотношений:
,
,
где h – глубина трещин, см;
V – скорость распространения ультразвука на участке бетона без трещин, см/мкс;
te – время распространения ультразвука на участке бетона с трещиной, мкс;
ta – время распространения ультразвука на участке бетона без трещины, мкс;
l – база прозвучивания для обоих участков, см.
Определение глубины трещин в конструкции:
1 – излучатель; 2 – приемник
Дата добавления: 2018-04-05; просмотров: 1422; Мы поможем в написании вашей работы! |
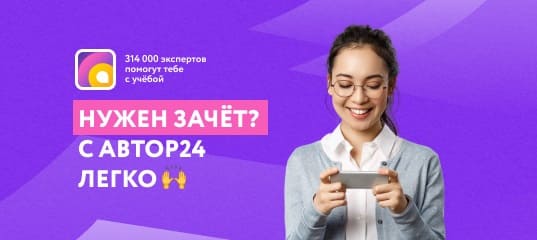
Мы поможем в написании ваших работ!