Визуальный контроль в строительстве
Введение.
Неразрушающий контроль – это контроль надежности основных рабочих свойств и параметров объекта или отдельных его элементов/узлов, не требующий выведения объекта из работы либо его демонтажа.
К средствам неразрушающего контроля относят контрольно-измерительную аппаратуру, в которой для получения информации о качестве исследуемых веществ, материалов и объектов используются физические поля, проникающие излучения и вещества.
Дефект – это каждое несоответствие продукции требованиям, установленным нормативной документацией.
Существует 9 видов неразрушающего контроля:
Магнитный – вид неразрушающего контроля основан на регистрации магнитных полей рассеяния дефектов или магнитных свойств контролируемого объекта. Его применяют для контроля объектов из ферромагнитных материалов. Процесс намагничивания и перемагничивания ферромагнитного материала сопровождается гистерезисными явлениями. Свойства, которые требуется контролировать (химический состав, структура, наличие несплошностей и др.), обычно связаны с параметрами процесса намагничивания и петлей гистерезиса, измеряя которые можно сделать вывод о наличии тех или иных отклонений от заданных параметров изделия.
Электрический – вид неразрушающего контроля основан на регистрации электрических полей и электрических параметров контролируемого объекта (собственно электрический метод) или полей, возникающих в контролируемом объекте в результате внешнего воздействия (термоэлектрический и трибоэлектрический методы). Первичными информативными параметрами являются электрические емкость или потенциал.
|
|
Вихретоковый – вид неразрушающего контроля основан на регистрации изменения взаимодействия собственного электромагнитного поля катушки с электромагнитным полем вихревых токов, наводимых этой катушкой в контролируемом объекте. Интенсивность и распределение вихревых токов в объекте зависят от его геометрических размеров, электрических и магнитных свойств материала, от наличия в материале нарушений сплошности, взаимного расположения преобразователя и объекта. Вихретоковый вид неразрушающего контроля в различных вариантах применяют с целью обнаружения поверхностных и подповерхностных дефектов сплошности, контроля геометрических размеров, химсостава, структуры, внутренних напряжений только электропроводящих материалов.
Радиоволновой – вид неразрушающего контроля основан на регистрации изменений параметров электромагнитных колебаний, взаимодействующих с контролируемым объектом. Обычно применяют волны сверхвысокочастотного (СВЧ) диапазона длиной 1 – 100 мм и контролируют изделия из материала, где радиоволны не очень сильно затухают: диэлектрики (пластмассы, керамика, стекловолокно), магнитодиэлектрики (ферриты), полупроводники, тонкостенные металлические объекты.
|
|
Тепловой – вид неразрушающего контроля основан на регистрации тепловых полей, температуры или теплового контраста контролируемого объекта. Он применим к объектам из любых материалов. Наиболее эффективным средством бесконтактного наблюдения, регистрации температурных полей и тепловых потоков является сканирующий тепловизор.
Визуально-оптический – вид неразрушающего контроля основан на взаимодействии светового злучения с контролируемым объектом. Применение инструментов (визуально-оптический контроль) типа луп, микроскопов, эндоскопов для осмотра внутренних полостей, проекционных устройств для контроля формы изделий, спроецированных в увеличенном виде на экран, значительно расширяет возможности оптического метода. Чаще всего оптические методы широко применяют для контроля прозрачных объектов. В них обнаруживают макро- и микродефекты, структурные неоднородности, внутренние напряжения (по вращению плоскости поляризации). Использование гибких световодов, лазеров, оптической голографии, телевизионной техники расширяет область применения оптических методов и повышает точность измерения.
|
|
Радиационный – вид неразрушающего контроля основан на взаимодействии проникающего ионизирующего излучения с контролируемым объектом. В зависимости от природы ионизирующего излучения вид контроля подразделяют на подвиды: рентгеновский, гамма-, бета- (поток электронов), нейтронный методы контроля. Этот вид неразрушающего контроля пригоден для любых материалов. Основным способом радиационного (рентгеновского и гамма) контроля является метод прохождения. Имеются хорошие результаты по использованию обратно рассеянного излучения фотонов с целью рентгеновского контроля при одностороннем доступе к объекту.
Акустический – вид неразрушающего контроля основан на регистрации параметров упругих колебаний, возбужденных в контролируемом объекте. Этот вид контроля применим ко всем материалам, достаточно хорошо проводящим акустические волны: металлам, пластмассам, керамике, бетоны и т.д. Наибольшее распространение нашел ультразвуковой метод, который наряду с дефектоскопией позволяет обнаруживать неоднородности структуры, определять механические характеристики материалов, анализировать напряженное состояние и решать широкий огромный круг производственных проблем контроля и диагностики. Кроме ультразвукового существуют метод акустической эмиссии, вибрационный метод контроля и другие.
|
|
Проникающими веществами – (контроль проникающими веществами) основан на капиллярном проникновении индикаторных жидкостей в полости поверхностных дефектов и регистрации индикаторного рисунка (цветного, люминесцентного, контрастного). Применяют для обнаружения невидимых и слабовидимых невооруженным глазом поверхностных дефектов.
Визуальный контроль в строительстве
2.1 Физические основы визуального контроля
Визуальный контроль – это единственный вид неразрушающего контроля, который может быть выполнен без какого-либо оборудования с использованием простейших измерительных средств.
Физические основы визуального контроля.
Основой визуального контроля являются законы оптики.
1. Закон прямолинейного распространения света. В однородной среде свет распространяется прямолинейно. Это вытекает из того, что непрозрачные предметы при освещении их источниками света дают тени с резко очерченными границами. Закон прямолинейного распространения света является приближенным, так как при прохождении света через очень малые отверстия наблюдаются отклонения от прямолинейности. Чем меньше отверстие, тем больше отклонение.
2. Закон независимости световых лучей. Независимость световых лучей заключается в том, что они при пересечении не возмущают друг друга, так как пересечение лучей не мешает каждому из них распространяться независимо друг от друга. Следует заметить, что независимость сохраняется в том случае, когда интенсивность света сравнительно невелика. При интенсивностях света, полученных лазером, независимость не наблюдается.
3. Закон отражения. При прохождении света через границу двух прозрачных веществ падающий луч разделяется на два: отраженный и преломленный. Направления этих лучей определяются законами отражения и преломления (рисунок 1). Закон отражения гласит, что отраженный луч лежит в одной плоскости с падающим лучом и нормалью, восстановленной в точке падения. Угол падения равен углу отражения.
4. Закон преломления. Согласно данному закону, преломленный луч лежит в одной плоскости с нормалью, восстановленной в точке падения. От- ношение синуса угла падения к синусу угла преломления есть величина по- стоянная для данных веществ. Виды измерений и погрешностей.
Рисунок 1 –Закон отражения и преломления
Оба эти закона выражаются формулой
(1)
где С1, С2 – скорости света, соответственно, в первой и второй средах.
Поскольку у первых двух частей равенства (1) знаменатели одинаковы (падающий и отраженный свет распространяется в одной и той же среде), то одинаковы и числители, значит, углы падения α и отражения β равны. Из равенства первой и третьей частей следует
Основным оптическим инструментом является глаз. Оптическая система глаза состоит из роговицы, жидкости передней камеры, хрусталика и стекловидного тела.
Рисунок – Схема глаза
Сила, или рефракция, глаза зависит от величины радиусов кривизны преломляющих поверхностей, расстояний между ними, показателя преломления роговицы, хрусталика, водянистой влаги и стекловидного тела. Все эти величины для разных глаз имеют разные значения. Нормальная зрительная работоспособность глаза зависит от состояния светочувствительного и двигательного аппарата. Зрительное утомление может наступить при расстройстве функций одного или обоих аппаратов. Утомление двигательного аппарата глаза может быть следствием необходимости часто переводить взгляд с одного предмета на другие, неодинаково удаленные, а также следить за движущимися объектами. При неудовлетворительном распределении яркости в освещенном пространстве и шуме в помещении возникает явление дискомфорта – ощущение неудобства или напряженности. Так, при яркости больше 1 500 кд/м2 зрачок глаза максимально сужен и глаз быстро утомляется. При пониженном освещении зрачок расширяется и наступает быстрое утомление за счет изменения световой чувствительности зрительного анализатора. Эта способность называется адаптацией. Адаптация бывает световая и темновая. Способность глаза раздельно воспринимать близко расположенные друг к другу точки, линии или другие фигуры называется разрешающей. Способность глаза замечать мелкие пред- меты и различать их форму называется остротой зрения. Способность глаза приспосабливаться к четкому видению различно удаленных объектов называется аккомофецией.
Электромагнитная волна несет c собой энергию. В белом свете глазом воспринимается весь интервал электромагнитных волн. Действие света на глаз (т.е. световые ощущения) в сильной степени зависит от длины волны. Чувствительность среднего нормального глаза к излучению разной длины волны дается так называемой кривой видности. Человеческий глаз наиболее чувствителен к излучению с длиной волны 0,555 мкм. Функция видности для этой длины волны принята равной 1. При том же потоке энергии оцениваемая зрительно интенсивность света для других длин волн оказывается меньше. Для характеристики интенсивности света с учетом его способности вызывать зрительное ощущение введена величина, называемая световым потоком. Световой поток – это поток лучистой энергии, оцениваемый по зрительному ощущению. Единица измерения – люмен (лм):
где «кд» – кандела (единица силы излучения света, от англ. candle – свеча); «рад» – радианы (единица измерения угла расхождения светового потока).
Степень освещенности некоторой поверхности падающим на нее све- товым потоком характеризуется величиной, называемой освещенностью. Единица освещенности – люкс (лк):
То есть 1 лк – это световой поток в 1 лм, равномерно распределенный по поверхности в 1 м. Освещенность рабочего места при визуальном контроле – важная величина, она должна быть не менее 500 лк. Рабочую поверхность на стационарном рабочем месте целесообразно покрывать светлым пластиком, при этом наиболее благоприятным является полуотраженное освещение. При выборе освещенности на рабочем месте учитывают: наименьший размер дефекта, который требуется обнаружить, и контраст дефекта на поверхности объекта контроля. Расстояние наилучшего зрения от нормального невооруженного глаза до объекта контроля считается 250 мм.
2.2 Виды измерений и погрешностей
Измерение – это нахождение значения физической величины опытным путем с помощью специальных технических средств. Средство измерений – это техническое средство, предназначенное для измерений, имеющее нормированные метрологические характеристики, воспроизводящие и (или) хранящие единицу физической величины, размер которой принимается неизменным в пределах установленной погрешности в течение известного интервала времени
По метрологическому назначению средства измерений подразделяются:
– на рабочие средства измерений физических величин (они являются самыми многочисленными);
– метрологические средства измерений, предназначенные для обеспечения единства измерений в стране. Единство измерений – это состояние измерений, при котором результаты измерений выражены в узаконенных единицах и погрешности известны с заданной вероятностью.
Средства измерений классифицируют:
1) по конструктивному исполнению – на меры, измерительные приборы, измерительные установки, измерительные системы, измерительные комплексы;
2) по уровню автоматизации – на неавтоматические, автоматизированные и автоматические; 3) по уровню стандартизации – на стандартизованные и нестандартизируемые; 4) по отношению к измеряемой физической величине – на основные и вспомогательные
Меры – это средства измерения, предназначенные для воспроизведения и (или) хранения физической величины одного или нескольких заданных размеров, значения которых выражены в установленных единицах измерения и известны с необходимой точностью.
Различают несколько видов измерений.
Прямое измерение – это измерение, при котором значение измеряемой
величины определяют непосредственно по результату измерения, например,
измерение глубины линейкой глубиномера штангенциркуля ЩЦ-1.
Косвенное измерение – это измерение, при котором искомое значение величины определяют пересчетом результатов прямых измерений величин, связанных с искомой величиной известной зависимостью.
Например, требуется измерить расстояние L между центрами двух отверстий с помощью штангенциркуля.
Рисунок –Косвенно измерение штангенциркулем дистанции между центрами отвертстий
Прямым измерением с помощью циркуля это сделать практически невозможно, следовательно, воспользуемся косвенным измерением. Сначала выполним прямые измерения величин d1, d2, Lmax губками для внутренних измерений, а затем рассчитаем искомую величину по формуле
L = Lmax – 0,5(d1 + d2) .
Контактное измерение – это измерение, при котором воспринимающее устройство средства измерений имеет механический контакт с поверхностью объекта, например, измерение с помощью штангенциркуля, микрометра, индикатора и т.д.
Бесконтактное измерение – это измерение, при котором воспринимающее устройство средства измерений не имеет механического контакта с поверхностью измеряемого объекта, например, измерение элементов резьбы с помощью микрометрического микроскопа.
Методами измеренийпринято называть совокупность приемов и принципов использования средств измерений. Наиболее распространены следующие методы:
1. Метод непосредственной оценки. При этом методе величину измеряемого объекта определяют непосредственно по размерному устройству, имеющемуся в конструкции применяемого средства измерений. Например, при измерении диаметра вала с помощью штангенциркуля величина диаметра, воспринятая губками, непосредственно сопоставляется со шкалой штанги, обладающей точным размером и включенной в конструкцию штангенциркуля.
2. Метод сравнения с мерой. Это метод, при котором величина измеряемого объекта сопоставляется с величиной, воспроизводимой мерой или величиной образцовой детали, которые не входят в конструкцию применяемого средства измерений. Например, измерение диаметра вала (30 мм) с помощью индикатора цифрового типа методом сравнения с концевой мерой длиной 30 мм на стойке со столиком. В этом случае величина диаметра вала сопоставляется с помощью индикатора с величиной концевой меры длины, которая не входит в конструкцию индикатора.
При выполнении измерения неизбежно возникают погрешностиразличной величины.
Погрешность измерения – это отклонение результата измерения Lu от действительного значения измеряемой величины Lg, определяемое по формуле
Δ = Lu – Lg.
Погрешности делят на группы:
– систематические (постоянно или закономерно изменяющиеся при повторных измерениях одной и той же величины);
– случайные (изменяющиеся случайным образом при повторных измерениях одной и той же величины).
На суммарную погрешность измерения наиболее существенно влияют
следующие составляющие:
1) инструментальная погрешность;
2) погрешность, вносимая в процесс мерами или образцами;
3) погрешность, возникающая от измерительного усилия при контактном измерении;
4) погрешности, возникающие из-за термического расширения или сжатия объекта контроля или средства измерений при отклонениях температуры в процессе измерения;
5) субъективные погрешности, связанные с человеком, выполняющим процесс измерения.
От правильности выполнения измерения значительно зависит качество продукции, поэтому рассмотрим подробнее составляющие погрешности измерения.
Инструментальная погрешность – это разность между показанием средства измерений и действительным размером измеряемого объекта.
Так как эта погрешность вносит самый большой вклад в погрешность измерения, за всеми средствами измерений проводится контроль как после их изготовления или ремонта, так и во время их эксплуатации. Такой контроль принято называть поверкой средств измерений. При проведении поверки определяют работоспособность поверяемого средства и его инструментальную погрешность, выясняя, находится ли она в пределах нормы, установленной для данного средства измерений.
Выполняют поверку специальные органы метрологической службы – измерительные лаборатории и их поверочные пункты.
Если в результате поверки данное средство измерений годное, то составляется официальный документ о положительных результатах поверки (аттестат) и (или) проводится его клеймение; если же средство измерений не годное, то оно изымается из применения. Свидетельство годного средства измерений хранится до даты следующей поверки. Если срок прошел и очередную поверку не произвели, то при контроле метрологическим органом данное средство измерений объявляется незаконным, а его аттестат недействительным.
Погрешности мер или образцов, используемых при установке средства измерений на размер со своими знаками, входят в погрешность каждого измерения. Чем выше точность изготовления объекта измерения, т.е. чем меньше допуск, тем опаснее отклонение меры, используемой при установке средств измерения.
Погрешность, появляющаяся от измерительного усилия при контактном измерении, зависит от деформаций, возникающих на поверхности объекта измерения. Чем больше деформации, тем больше погрешности измерения.
Погрешность, возникающая из-за термического расширения (сжатия) объекта измерения и средства измерений зависит от температуры помещения, где производятся измерения. Нормальной считается температура +20 С.
Отклонения от нормальной температуры приводят к тепловому расширению или сжатию измеряемой детали и средства измерений, а следовательно, к увеличению погрешности измерения.
Субъективные погрешности, связанные с человеком, выполняющим измерения, можно разделить на 3 группы:
– ошибки при действиях: неточное совмещение шкалы с измеряемым размером; ошибки подбора концевых мер длины (КМД) в блок, ошибки установки на нуль, ошибки при закреплении средства измерений в установленном положении; при контакте чувствительного элемента средства измерений с поверхностью объекта (возможно завышение или занижение измерительного усилия);
– ошибки при наблюдении: ошибки отсчета при оценке точности совпадения стрелки или штриха нониуса с делением шкалы и его знаком;
– профессиональные субъективные погрешности – это ошибки исполнителя, вызванные его недостаточной квалификацией.
2.3 Оборудование для визуального контроля.
Комплект оборудования для ВИК может включать в себя (например):
Рисунок – Стандартный комплект ВИК
- Нормативный документ РД 03-606-03;
- Фонарик карманный;
- Маркер по металлу;
- Лупа с подсветкой;
- Рулетка измерительная 200 см;
- Линейка измерительная 30 см;
- Штангенциркуль;
- Универсальный шаблон сварщика УШС-2;
- Универсальный шаблон сварщика УШС-3;
- Угольник поверочный;
- Набор щупов;
- Измерительная лупа
Сумка упаковочная.
Лупы и микроскопы. Для контроля близко расположенных деталей (находящихся на расстоянии не более 250 мм от глаз контролера) используют лупы и микроскопы различного типа.
Лупы и микроскопы позволяют обнаруживать трещины различного происхождения, поверхностные коррозионные и эрозионные повреждения, забоины, открытые раковины, язвы, поры, выкрашивание материала деталей, риски, надиры трущихся поверхностей и другие поверхностные дефекты деталей, а также различные дефекты лакокрасочных и гальванических покрытий. При анализе характера дефектов эти приборы позволяют отличать усталостные трещины от хрупких, трещины - от рисок, примятых заусенцев, сколов окисной пленки, нитевидных загрязнений (волокон ветоши, щетины от кистей) и т.д.
Обычно осмотр деталей проводят с помощью луп с фокусным рас-стоянием от 125 до 12,5 мм и увеличением соответственно от 2 до 20х. Из-за существенного снижения поля зрения и глубины резкости при больших увеличениях для осмотра деталей в цеховых условиях в основном применяют микроскопы с увеличением от 8 до 40-50х.
Увеличение изображения микроскопом, используемым для осмотра деталей, несколько превышает увеличение лупой. Однако, даже при использовании микроскопа и лупы с равным увеличением, эффективность применения микроскопа из-за высокого качества изображения и надежного обнаружения дефектов выше. Применяемые для контроля деталей микроскопы дают прямое стереоскопическое изображение контролируемой поверхности, что облегчает поиск дефектов. Область применения микроскопов ограничена, как правило, заводскими условиями.
Достоинством микроскопов является их относительно большое рабочее расстояние, позволяющее использовать их для осмотра различных углублений и пазов на деталях. Например, рабочее расстояние лупы 20х составляет 10 мм, а микроскопа МБС-02 (рисунок 2) - 64 мм при любом уве-личении.
Рисунок – Микроскоп МБС-02
Универсальные шаблоны сварщика. Простейшие устройства, предназначенные для контроля внешних характеристик сварного соединения.
УШС-2 предназначен для контроля катетов угловых швов в диапазоне 4-14мм (рисунок 3). Контроль проводится ступенчатым методом определения до минимального зазора.
Рисунок – УШС-2
УШС-2 состоит из 3-х лепестков и 1 соединительного кольца. Каждый из лепестков имеет точно выполненные выточки определенного катета. Для удобства контроля рядом с каждой выточкой выбит размер соответствующего радиусу катета шва. Контроль катета сварного шва производиться путем последовательного соприкосновения (подбора) лепестков с соединенными сваркой деталями. Размер считается установленным, если длинная сторона лепестка и перемычка между катетами лепестка прилегают к деталям без видимого зазора, а зазор между дугами лепестка и шва является минимальным. При несовпадении ни с одной ступенью размеров в указанном диапазоне значение катета определяется эмпирическим путем.
УШС-3 предназначен для измерения контролируемых параметров труб, контроля качества сборки стыков соединений труб, а также для измерения параметров сварного шва при его контроле.
Рисунок – УШС-3
Шаблон УШС-3 состоит из основания 1, соединенного осью 4 с движком 2 и закрепленного на движке указателем 3.
Контроль производится следующим образом:
1. Контроль глубины раковин, глубины забоин, превышение кромок глубины разделки стыка до корневого слоя и высоту усиления шва производят при установке шаблона поверхностью А на изделие, затем поворотом движка 2 вокруг оси 4 ввести указатель 3 в соприкосновение с измеряемой поверхностью. Результат считывается против риски К по шкале Г.
2. Контроль зазора производится введением движка 2 его клиновой частью в контролируемый зазор. По шкале И, нанесенной на движке, считывается результат.
3. Контроль притупления шва, ширины шва производить при помощи шкалы Е , пользуясь ею как измерительной линейкой.
Рисунок – Основные измерительные элементы УШС-3
4. Контроль углов скоса кромок производится при установке шаблона поверхностью Б на образующую изделия. Затем, поворотом движка 2 совместить без зазора его поверхность В с измеряемой поверхностью. Результат считывается по шкале Д против поверхности движка В.
5. Определение диаметров проволоки производится с помощью пазов Ж.
Кроме указанных выше существует большое количество других шаблонов. Принцип их применения аналогичен применению шаблонов УШС-2 и УШС-3. Например, шаблон Красовского.
Рисунок – Шаблон Красовского
Шаблон Красовского служит для контроля тавровых и нахлесточных сварных соединений, стыковых сварных соединений, измерения зазора между кромками. Схемы его применения приведены на рисунке.
Рисунок – Схемы применения шаблона Красовского
Инструменты, позволяющие провести измерение отдельных параметров сварного соединения. Устройство штангенциркуля должно быть известно читателям настоящего пособия. Механический штангенинструмент представляет собой две измерительные поверхности, между которыми устанавливается размер, одна из которых составляет единое целое с линейкой (штангой), а другая соединена с двигающейся по линейке рамкой. На линейке находится через 1 мм деления, на рамке устанавливается или гравируется нониус. Наиболее распространенный штангенинструмент - штангенциркуль. Внешний вид различных штангенциркулей представлен на рисунке.
К этому же виду инструментов можно отнести и шаблон Ушерова-Маршака, предназначенный для измерения скоса кромок при подготовке свариваемых соединений деталей, измерения высоты катета углового шва, измерения высоты валика усиления, измерения выпуклости корня шва стыкового сварного соединения, измерения зазора в соединении при подготовке деталей к сварке.
Рисунок – Виды штангенциркулей
1– с круговым индикатором; 2 – электронный; 3 –механический с нониусом
Рисунок – Разные виды шаблона Ушерова-Маршака
Схемы применения шаблона Ушерова-Маршака представлены на рисунке.
Рисунок – Применение шаблона Ушерова-Маршака
При проведении измерений допустимая погрешность должна быть в диапазоне, указанном в таблице 1.
Таблица 1 - Допустимая погрешность измерений при измерительном контроле
Для расширения возможностей метода НК ВИК все чаще находят применение различные эндоскопы – смотровые приборы, построенные на базе волоконной или линзовой оптики и современные видеоэндоскопы, имеющие на торце щупа микровидеокамеру с подсветкой.
Рисунок – Современный видеоэндоскоп
Применение различных эндоскопов позволяет увидеть те области конструкции, узлов и деталей машин, которые невозможно увидеть человеческим глазом из-за невозможности проникновения к данной области.
ВИК, по определению, предусматривает ручные технологии контроля. В последнее время на рынке стало появляться оборудование, позволяющее автоматизировать процесс контроля, снизить влияние человеческого фактора. Одним из таких устройств является система для контроля сварного шва, представленная на рисунке.
Рисунок – Лазерный сканер для контроля сварных швов
Система снабжена лазерным сканером и камерой высокого разрешения, позволяющим получать качественное трехмерное изображение шва. После создания трехмерной цифровой модели сварного шва производится автоматическое сравнивнение со встроенными шаблонами, основанными на конкретных нормативных документах. Признание сварного шва годным к эксплуатации происходит в режиме реального времени.
На экране устройства отображается как фотография сварного шва, так и разнообразная информация, позволяющая классифицировать сварной шов, определить вид и геометрические параметры дефекта, сделать вывод о допустимости к эксплуатации изделия с данным дефектом.
Рисунок – Информация, отображаемая на экране лазерного сканера
2.4 Процедура визуального контроля.
Процедура визуального контроля осуществляется в соответствии с РД 6–303–6.
Дата добавления: 2018-04-05; просмотров: 1596; Мы поможем в написании вашей работы! |
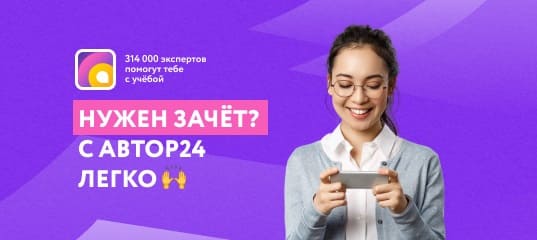
Мы поможем в написании ваших работ!