Организация взвешивания и подачи шихтовых материалов на колошник печи
Подача железорудного сырья бывает различной в зависимости от принятого способа транспортирования. При системе с механизмами периодического действия подача шихты осуществляется вагона-весами, двигающимися между бункерами и набирающими материалы в «карманы» — воронки при помощи барабанных затворов «Орра». В этом случае эстакада линейного типа с двухрядным расположением бункеров в количестве 18-32 на одну печь (число бункеров зависит от производительности печи и расстояния между осями печей цеха).
Шихта загружается последовательно в каждый карман вагона-весов по установленной программе с соблюдением строгой очередности забора из бункеров с одноименным материалом. После заполнения карманов шихта доставляется к скиповой яме (рис. 4.12) и разгружается через направляющие лотки 3 в скипы 4 или промежуточные бункера 1 с затворами, управление которых входит в общую схему автоблокировки загрузочной системы.
Рис.4.12. Схема шихтоподачи с помощью вагона-весов.
Таким образом создается резерв времени для набора материалов при наличии в запасе шихты для очередной подачи. Питание вагона-весов 2 электроэнергией осуществляется через троллеи, укрепленные на потолке подбункерного помещения.
В подбункерном помещении между бункерами отдельных печей делаются ремонтные площадки с установкой запасных вагона-весов (не менее одних на две смежные доменные печи). Под горловинами коксовых бункеров (имеющих листовые задвижки ручного привода для их перекрытия на случай ремонта бункеров) устанавливаются грохоты 5 для отсева коксовой мелочи <25 мм с одновременной загрузкой отсеянного кокса в весовую воронку 6 и далее в скипы 4.
|
|
Отсеянная мелочь <25 мм специальным малым скиповым подъемником 7 передается в сборный бункер изатем подвергается грохочению на классы 25-40, 25-10, 10-0 мм. Класс 25-40 можно задавать обратно в печь, соблюдая установленную периодичность загрузки, а фракции 25—10 (орешек) и 10-0 отгружаются соответственно для ферросплавной промышленности и агломерационного производства. В связи с холостыми пробегами и ограниченной грузоподъемностью, сложными условиями автоматизации и запыленностью при наборе материалов вагон-весы в настоящее время применяются на печах полезным объемом до 1719 м3, а на больших печах заменяются системой машин непрерывного действия, т. е. конвейерными транспортерами с дозаторами-питателями, служащими одновременно грохотами для отсева мелочи и затворами для бункеров. Такая схема может быть осуществлена при подаче материалов на колошник как скипами, так и ленточным транспортером. Примером являются эстакада и шихтоподача в подбункерном помещении печи 3200 м3 (рис. 4.13).
|
|
Рис. 4.13. Схема транспортной шихтоподачи к скипам доменной печи объемом 3200 м3
1 - грохот агломерата; 2 - конвейер агломерата; 3 - перекидной лоток;
4, 6, 10 - воронка-весы; 5 - питатель добавок; 7- конвейер добавок; 8 - скип;
9 - грохот кокса; 11 - конвейеры уборки мелочи
Схема этой шихтоподачи отличается от рассмотренной выше числом бункеров (меньше в 3 раза для агломерата и в 2 раза для добавок). Данная система шихтоподачи обеспечивает хорошие санитарно-технические условия благодаря значительному уменьшению точек пыле-образования, применению гидросмыва, централизованной вентиляционной системе с трехступенчатой очисткой запыленного воздуха и притоку свежего воздуха.
Раздвоение наклонного колошникового моста, впервые примененное в отечественной практике, позволило скомпоновать шихтоподачу таким образом, что время на набор и доставку материалов к скиповым ямам сократилось. Был успешно решен вариант скиповой загрузки печи большой производительности. Изыскание системы с наиболее простой технологической схемой, определяемой составом шихты современных мощных доменных печей, привело к разработке конвейерной подачи на колошник, к шихтоподаче с механизмами непрерывного действия, имеющей в настоящее время широкое применение в зарубежной практике. Такой системой является шихтоподача доменной печи 5000 м3 (рис.4.14).
|
|
Рис.4.14. Схема конвейерной шихтоподачи доменной печи объемом 5000 м3
По ее схеме кокс и минеральное сырье, поступающее в специализированных составах с дистанционным открыванием разгрузочных люков, разгружаются на двухрядной эстакаде. Схемой предусматривается хранение в первом ряду с двумя железнодорожными путями кокса и добавок, во втором ряду с тремя путями – агломерата и окатышей. Один из двух путей в ряду кокса и добавок может быть заменен транспортером для подачи кокса непосредственно с коксосортировки коксохимического производства. Бункера располагаются с обеих сторон наклонного конвейера на колошник и обеспечивают «гибкую» загрузку доменной печи при любом сочетании порций механизмами одной стороны эстакады. Обычно одна из сторон является резервной.
Материалы (кроме добавок) выдаются из бункеров при помощи грохотов (для агломерата) и окатышей по два грохота 1 под каждым бункером производительностью по 400 м3/ч, а для кокса три грохота 9 по 200 м3/ч в стационарные весовые воронки 2, 10 вместимостью 25 м3 и питатели11. Добавки (двух видов) поступают в весовые воронки 7 грузоподъемностью 2-3 т и питателями 6 производительностью 300 т/ч выдаются на конвейеры 5 периодически в порцию агломерата, окатышей или кокса. Грохоты и питатели б добавок срабатывают по импульсу от весовых воронок 7 – включаются при пустой воронке и останавливаются после набора заданной массы. На конвейеры 5 шихта поступает из весовых воронок 2, оборудованных двумя питателями 3. Производительность каждой воронки 1000 м3/ч. Конвейеры 5, а также конвейер 8 работают непрерывно, и материалы, согласно заданной программе загрузки, размещаются на них порциями с определенными интервалами в зависимости от темпа загрузки. Темп загрузки определяется интенсивностью хода доменной печи. Мелочь агломерата и окатышей конвейерами 4 собирается от грохотов 7 сборным конвейером 18 и направляется соответственно в бункера мелочи 16. Мелочь кокса сборным конвейером 13, собирающим ее с конвейеров 12, направляется в бункер мелочи кокса 14. В случае необходимости подача мелочи в соответствующий погрузочный бункер может переключаться с конвейеров 18 на конвейер 13 при определенном положении шиберов 17 и 19. Выгрузка мелочи из бункеров осуществляется в железнодорожные вагоны питателями 75 через затворы с увлажнением материалов. Вся система шихтоподачи имеет общее число точек пыления 59, в том числе 30 при работе с одной стороной, что является минимальным для всех систем подачи.
|
|
Загрузочный конвейер работает непрерывно для предупреждения излишнего износа механического оборудования, из которого особое внимание должно быть уделено тому, которое не может быть продублировано или дублировать которое экономически невыгодно. Взвешивание материалов предпочтительно в стационарных весовых воронках, поскольку применение ленточных весовых дозаторов и ленточных весов не обеспечивает необходимой точности взвешивания.
Сравнение технико-экономических показателей конвейерной системы подачи на колошник со скиповой выявило следующие преимущества:
1. Удельные капитальные затраты (на 1 т выплавляемого чугуна) ниже на 15-20%. Эксплуатационные расходы благодаря меньшим амортизационным отчислениям, расходам на ремонт, электроэнергию и зарплату ниже на 15-20% .
2. Значительный резерв в производительности при различных величинах коксовой подачи с коэффициентом запаса 1,5.
3. Единая система машин непрерывного транспорта от бункеров до колошника и полная ее автоматизация с применением ЭВМ.
Вагон-весы. Предназначены для набора шихты из бункеров, взвешивания ее, доставки к скиповой яме и загрузки в скипы. Они представляют собой самоходный вагон с двумя саморазгружающимися бункерами (карманами), взвешивающим механизмом, механизмами вращения бункерных барабанных затворов (рис. 4.15).
Рис. 4.15. Вагон-весы и кинематическая схема их работы
Основные механизмы вагона-весов: весовой, затвор карманов, вращения барабанов, подъема качающихся редукторов и передвижения.
В свободном состоянии карманы вагона-весов через тягу 2 и промежуточный рычаг 3 уравновешиваются грузом 5 через контргрузный рычаг 4. Этот же рычаг 4 через тягу 6 в груженом состоянии передает усилие рычагу 7, к которому присоединен демпфер 8, уменьшающий колебания в упругой системе весового механизма. Весовая пружина 9 на тяге 10 с рейкой взаимодействует с вращающимся указателем веса 11. Усилие, передаваемое на пружину, S = к (G/x) Тн, где G - масса материала в карманах вагона-весов; х - передаточное число весового механизма; к - коэффициент, учитывающий натяжение пружины для устранения зазоров, равный 1,25. При взвешивании масса уменьшается пропорционально передаточному числу и воспринимается пружиной 9. Пропорционально ей вращается указатель 11.
Конструкция вагона-весов состоит из сварной рамы 4, снабженной буферами 1 и предохранительными фартуками 2. Рама опирается на две тележки 5 с индивидуальными приводами и пневматическими тормозами. В середине рамы смонтированы две воронки (карманы) 7, опирающиеся на рычаги весового механизма, который подвешен к раме. Днище воронок выполнено в виде двух створок, откидывающихся посредством рычажной системы, и пневмоцилиндра 9. Рычажная система исключает возможность самопроизвольного открывания дверок. Для поддержания давления воздуха в пневмоцилиндрах в пределах 390—590 кПа на раме установлены компрессоры 3 со змеевиками и воздухосборниками 6. При переводе в верхнее положение посредством пневмоцилиндра 9 корпус качающегося редуктора 8 специальным выступом толкает тягу барабанного затвора шихтового бункера, которая в свою очередь поднимает отсекатель затвора. Включением электродвигателя 11 барабан затвора приводится во вращение и материал, высыпаясь из шихтового бункера, попадает в бункер вагона-весов. Вагон-весы снабжены закрытой кабиной управления 10, имеющей принудительную вентиляцию. Управление осуществляется обычно одним человеком, но в 1955 г. впервые в практике доменного производства на Кузнецком металлургическом комбинате оно было полностью автоматизировано для работы без непосредственного управления машинистом.
Вагон-весы имеют защитные блокировки механизмов, исключающие передвижение их, если затворы карманов 7 открыты или корпус качающихся редукторов 8 поднят; открывание затворов карманов 7, если вагон-весы не стоят над скиповой ямой, если под ними нет скипа или если по программе грузится кокс; продвижение их, если корпус качающихся редукторов поднят. Техническая характеристика вагона-весов: грузоподъемность 25-40 т; вместимость карманов 13-18 м3; скорость передвижения 120-180 м/мин. Производительность вагона-весов, кг/ч: а = 3600m/tB, где т — масса рудной части подачи, кг; tB - время цикла работы вагона-весов в течение одной подачи, с. Это время определяется из графика работы вагона-весов, связанного с работой скипового подъемника и расположением материалов по бункерам.
Воронка-весы. Предназначены для дозирования шихтовых материалов, поступающих в них из бункеров. В зависимости от принятой системы транспортирования число и расположение воронок-весов различны. При загрузке через вагон-весы их применяют только для взвешивания кокса, отсева мелочи кокса и устанавливают в скиповой яме за грохотом, а при конвейерной загрузке — в общем потоке после грохотов-питателей или в скиповой яме. Воронка-весы состоит из воронки, затвора с электроприводом и весов. Воронку изготавливают из листовой стали и футеруют защитными плитами; устанавливают на платформе весового механизма. Горловина закрыта затвором, работающим от электропривода.
Рис.4.16. Воронка-весы для кокса
Коксовая воронка (рис. 4.16) имеет затвор шиберного типа, подвешенный на тросе 3 и движущийся в направляющих 1. Трос через барабан 4 соединен с контргрузом 5, уравновешивающим вес затвора. Электродвигатель 6 через муфту 7 и редуктор £ передает вращение барабану. К шиберу 2 крепится также переброшенный через шкив 10 трос 9, который при опускании и подъеме шибера приводит в движение вал шкива 10, связанного через муфту с командоаппаратом 12, обусловливающим работу привода затвора воронки. Трос 9 натягивается противовесом 11.
Затвор воронки для агломерата (рис. 4.17, а) вращающегося типа присоединяется к горловине течки 1 воронки осями 5, проходящими через отверстия в щеках 3 затвора 2 и подвесок, прикрепленных к горловине воронки 6, прикрепленной к стойкам 9.
Оси служат для поворота затвора во время его работы. К щекам затвора присоединяются цапфы 4, с которыми шарнирно сопряжены тяги 8, соединенные затем с кривошипами, закрепленными на концах выходного вала редуктора 7. Этот вал через шестеренную передачу связан с валом командоаппарата. Затвор открывается при повороте кривошипов на 180°.
Затвор воронки для добавок (рис. 4.17, б) отличается от затвора воронки для агломерата тем, что на втором конце вала электродвигателя установлен шарнир 1, а командоаппарат 2 приводится в действие через редуктор 3 и тягу 4, шарнирно соединенную с одним из кривошипов привода.
Вес материала передается через грузоподъемные серьги на призмы главных рычагов, последние опираются на серьги, подвешенные к балкам бункерной эстакады. Усилия двух главных рычагов передаются через передаточные и выходные рычаги на тягу первичного указателя привода – весовую головку 5. Затворы воронок работают автоматически по установленной для общего потока загрузки программе.
Скиповые подъемники коксовой и агломерационной мелочи. Материалы на колошник подают специальными тележками – скипами, перемещающимися по рельсам наклонного моста. Объем материалов одной подачи соответствует объему нескольких скипов, поэтому подача на колошник подается по частям несколькими скипами. При этом одну часть скипов подачи загружают коксом, а другую – железосодержащими компонентами и флюсом. При полностью офлюсованном агломерате подача состоит только из скипов с агломератом и коксом.
Шихтовые материалы подаются на колошник печи скиповым подъемником в двух скипах поочередно. Внешний вид скипа и схема его опрокидывания на колошник представлены на рисунке 4.18 . По наклонному мосту шихтоподъемника одновременно движутся два скипа: груженный поднимается вверх, а пустой опускается. На подъемнике (тросах лебедки) скипы взаимно уравновешиваются. В крайнем верхнем положении скип опрокидывается, благодаря тому, что его передние колеса катятся по рельсам, в то время как задние колеса движутся по вспомогательным, радиально изогнутым рельсам, поднимающим заднюю часть скипа. Материал из скипа высыпается в приемную воронку 1 на поверхность малого конуса 3. При опускании малого конуса шихта ссыпается вниз на поверхность большого конуса. Чтобы обеспечить равномерную загрузку шихты по всей окружности поперечного сечения шахты печи, используется механизмраспределения шихты, работа которого заключается в том, что малый конус с шихтой перед каждым опусканием предварительно поворачивается, совместно со своей воронкой, на угол 60 градусов. Тогда шихта распределяется по окружности большого конуса. Работа конусов и распределителя шихты автоматизирована. Перед каждым опусканием большого конуса с “калошей” (подачей) шихты, малый конус с его воронкой поворачивается (5…6) раз. Но опускание большого конуса контролируется АСУ и может произойти только тогда, когда уровень засыпи шихты опустится до определенного уровня, отсчитывая его от нижнего положения большого конуса (чтобы большой конус не “сел” на шихту). Уровень засыпи непрерывно контролируется, так называемыми, зондами шахты печи.
Рис.4.17. Воронка весы: а – для агломерата; б – для добавок
Рис.4.18 Скиповые тележки
Внутренние поверхности скипа от абразивного износа шихтовыми материалами защищены плитами толщиною до 50 мм 4, изготовленными из марганцовистой стали.
Ходовые колеса 2 насажены на оси попарно и вращаются в радиальных сферических двухрядных подшипниках качения. Задние ходовые колеса имеют две беговые дорожки, разделенные ребордой, что обеспечивает заход колес на криволинейный разгрузочный путь наклонного моста. При этом происходит опрокидывание скипа и выгрузка из него шихтовых материалов. “Упряжное” устройство скипа 3 предусматривает возможность автоматического выравнивания натяжений тяговых канатов и укорачивания при их вытяжке во время работы.
Тема № 5 “Доменная печь: конструкция, принцип работы”
Дата добавления: 2018-04-05; просмотров: 2194; Мы поможем в написании вашей работы! |
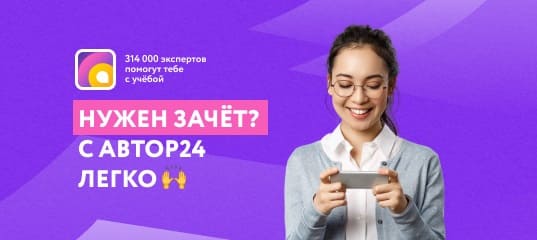
Мы поможем в написании ваших работ!