Брак при фрезеровании уступов,пазов,канавок и его предупреждение
При фрезеровании уступов, шпоночных канавок, прямоугольных пазов возможны следующие виды брака;
Несовпадение оси шпоночной канавки с осью вала (непараллельность или несимметричность). Брак неисправимый. Причины: неправильная установка по центру вала дисковой или шпоночной фрезы.
Ширина канавки или паза больше чертежного размера. Брак неисправимый. Причины: биение торцов дисковой фрезы или радиальное биение шпоночной концевой фрезы.
Ширина канавки или паза меньше чертежного размера. Брак исправимый. Причины: при переточке фрезы она потеряла размер по ширине (для дисковой фрезы) или по диаметру (для концевой и шпоночной фрез), а фрезеровщик не проверил ее размеры. Для исправления брака нужен добавочный проход.
Глубина уступа, канавки или паза больше чертежного размера. Брак неисправимый. Причины: при перемещении стола станка фрезеровщик неправильно произвел отсчет по шкале лимба подачи стола.
Длина закрытой шпоночной канавки или закрытого паза больше чертежного размера. Брак неисправимый. Причины неправильно установлены кулачки механического выключения продольной подачи стола; фрезеровщик несвоевременно выключил-механическую подачу стола; фрезеровщик, фрезеруя с ручной подачей, невнимательно следил за разметочными рисками.
Глубина и длина закрытой шпоночной канавки или паза меньше чертежных размеров. Брак исправимый. Причины: невнимательность фрезеровщика при установке глубины фрезерования и продольного перемещения стола. Для исправления брака нужен добавочный проход.
|
|
Обработанная поверхность уступа, шпоночной канавки или паза не соответствует заданной чистоте, имеет рваные края, вмятины. Брак неисправимый. Причины: неправильный режим фрезерования, большая подача на зуб фрезы, малая скорость резания, большая скорость резания при отсутствии охлаждающей жидкости.
Вмятины и забоины на поверхности детали (бруска, призмы, вала). Брак неисправимый, если детали не подлежат последующему шлифованию. Причины: отсутствие мягких накладок на губках тисков при зажиме заготовки; следы ударов при креплении заготовки (применяли стальной молоток вместо латунного).
К возможным случаям брака, кроме несоблюдения размера по чертежу, относится несоответствие качества обработки чистоте поверхности, например3, предписанной чертежом.Одной из причин этого может быть затупление или биение фрезы, что вызывает волнистую поверхность обработки. Другой причиной может оказаться слишком большая подача на один зуб фрезы; достаточно увеличить число оборотов или уменьшить минутную подачу, чтобы устранить этот недостаток.Чаще этот брак происходит от явления, которое называют подрезанием. Иногда приходится останавливать подачу, когда проход еще не закончен. Как бы аккуратно ни была заточена фреза, она всегда несколько бьет во время работы. Кроме того, оправка во время работы несколько пружинит вследствие усилия резания. Поэтому, если остановить подачу в то время, когда фреза еще продолжает вращаться, она врежется в металл несколько глубже в том месте, которое окажется под фрезой в момент выключения подачи .
|
|
76.резиновые и эбонитовые материалы… Резиной называется продукт специальной обработки (вулканизации) смеси каучука и серы с различными добавками.
Резина как технический материал отличается от других материалов высокими эластическими свойствами, которые присущи каучуку – главному исходному компоненту резины. Она способна к очень большим деформациям (относительное удлинение достигает 1000%), которые почти полностью обратимы.
При эксплуатации толстостенных деталей (например, шин) вследствие низкой теплопроводности материала нарастание температуры в массе резины снижает ее работоспособность. Для резиновых материалов характерны высокая стойкость к истиранию, газо- и водонепроницаемость, химическая стойкость, электроизоляционные свойства и низкая плотность.
|
|
В результате совокупности технических свойств резиновых материалов их применяют для амортизации и демпфирования, уплотнения и герметизации в условиях воздушных и жидкостных сред, химической защиты деталей машин, в производстве тары для хранения масел и горючего, различных трубопроводов (шлангов), для покрышек и камер колес самолетов, автотранспорта и т. д.
Эбонит — высоко-вулканизированный каучук с большим содержанием серы, обычно тёмно-бурого или чёрного цвета; химически инертен, имеет высокие электроизоляционные свойства. В отличие от мягкой резины, эбонит не проявляет высокой эластичности при обычных температурах и напоминает твёрдую пластмассу. Эбонит становится высокоэластичным при температуре больше плюс 55 градусов по Цельсию.
Эбониты применялись как электроизоляторы и кислотостойкие материалы при производстве электроизоляционных деталей приборов, при гуммировании различных ёмкостей для агрессивных жидкостей, корпуса кислотных аккумуляторов и т. д.
Эбониты также использовались как заменители дорогих материалов типа черного дерева, слоновой кости, рога или черепашьего панциря.
|
|
Графит — минерал из класса самородных элементов, одна из аллотропных модификаций углерода.
Хорошо проводит электрический ток. В отличие от алмаза обладает низкой твёрдостью (1 по шкале Мооса). Относительно мягкий. После воздействия высоких температур становится немного твёрже, и становится очень хрупким. Плотность 2,08—2,23 г/см³. Цвет тёмно-серый, блеск металлический. Неплавкий, устойчив при нагревании в отсутствие воздуха. Жирный (скользкий) на ощупь. Природный графит содержит 10—12 % примесей глин и окислов железа. При трении расслаивается на отдельные чешуйки (это свойство используется в карандашах).
Использование графита основано на ряде его уникальных свойств.
электродов, нагревательных элементов — благодаря высокой электропроводности и химической стойкости к практически любым агрессивным водным растворам (намного выше, чем у благородных металлов).
Для получения химически активных металлов методом электролиза расплавленных соединений. В частности, при получении алюминия используются сразу два свойства графита:
Хорошая электропроводность, и как следствие — его пригодность для изготовления электрода
Газообразность продукта реакции, протекающей на электроде — это углекислый газ. Газообразность продукта означает, что он выходит из электролизёра сам, и не требует специальных мер по его удалению из зоны реакции. Это свойство существенно упрощает технологию производства алюминия.
твёрдых смазочных материалов, в комбинированных жидких и пастообразных смазках.
наполнитель пластмасс.
замедлитель нейтронов в ядерных реакторах.
компонент состава для изготовления стержней для чёрных графитовых карандашей (в смеси с каолином).
для получения синтетических алмазов.
в качестве эталона длины нанометрового диапазона для калибровки сканеров сканирующего туннельного микроскопа и атомно-силового микроскопа.
для изготовления контактных щёток и токосъёмников для разнообразных электрических машин, электротранспорта и мостовых подъёмных кранов с троллейным питанием, мощных реостатов, а также прочих устройств, где требуется надёжный подвижный электрический контакт.
для изготовления тепловой защиты носовой части боеголовок баллистических ракет и возвращаемых космических аппаратов.
как токопроводящий компонент высокоомных токопроводящих клеёв.
77.спецификация, её назначение и форма. Для сборочных единиц основным конструкторским документом является спецификация. Она определяет состав сборочной единицы, комплекса или комплекта и является главным документом для изготовления, комплектования конструкторских документов и планирования запуска в производство указанных изделий. Форму и порядок заполнения спецификаций конструкторских документов на изделия всех отраслей промышленности устанавливает ГОСТ 2.108—68. Спецификацию составляют на отдельных листах формата А4 по форме, изображенной на рисунке.
Спецификация состоит из разделов, которые располагают в такой последовательности: документация, комплексы, сборочные единицы, детали, стандартные изделия, прочие изделия, материалы, комплекты. Наличие тех или иных разделов определяется составом специфицируемого изделия. Наименование каждого раздела указывают в виде заголовка в графе «Наименование» и подчеркивают.
78.приборы рычажного типа. Измерительные головки бывают рычажные, рычажно-винтовые, рычажно-пружинные, рычажно-зубчатые и зубчатые.
В производственных условиях и измерительных лабораториях широко используют для абсолютных измерений индикаторы или индикаторные измерительные головки. Индикаторы можно разделить на два типа: индикаторы часового типа (с зубчатой передачей) и рычажно-зубчатые.
Механизм передачи индикатора часового типа состоит из зубчатых пар. На измерительном стержне головки нарезана зубчатая рейка, которая находится в зацеплении с зубчатым колесом. Возвратно-поступательное перемещение измерительного стержня преобразуется в круговое движение стрелки с помощью зубчатых колес. Устранение зазора в зубчатых колесах обеспечивает спиральная пружина, один конец которой закреплен на зубчатом колесе, а другой — в корпусе индикатора. Индикатор имеет две шкалы: большую — для отсчета долей миллиметра и малую — для отсчета целых миллиметров. Один оборот стрелки соответствует перемещению измерительного стержня на 1 мм. Большая шкала имеет 100 делений, цена деления индикатора равна 0,01 мм.
К приборам с рычажно-зубчатой передачей относятся рычажные скобы, рычажные микрометры, рычажно-зубчатые измерительные головки и т.д. Эти приборы предназначены для относительных измерений наружных размеров в основном цилиндрических деталей.
В рычажных скобах (рис. 4, а) при измерении чувствительная пята 1, перемещаясь, воздействует на рычаг 2, зубчатый сектор которого поворачивает зубчатое колесо 3 и стрелку, неподвижно укрепленную на его оси. Пружина 4 постоянно прижимает колесо 3 к зубчатому сектору, устраняя таким образом зазор. У рычажной скобы микровинт 5 не имеет отсчетного устройства. Пределы измерения рычажной скобы от 0—25 мм через 25 мм до 75—100 мм, цена деления шкалы — 0,002 мм; пределы измерения по шкале ±0,08 мм. Рычажные микрометры аналогичны рычажным скобам и отличаются от них лишь наличием микрометрической головки.
Рычажно-зубчатые измерительные головки (рис. 5) отличаются от индикаторов часового типа тем, что у них, наряду с зубчатой передачей, имеется рычажная система, что позволяет увеличить передаточное число механизма и тем самым повысить точность измерений. При перемещении измерительного стержня 1 в двух направляющих втулках 8 поворачивается рычаг 3, который воздействует на рычаг 5, имеющий на большем плече зубчатый сектор, входящий в зацепление с зубчатым колесом (трибом) 4. На оси колеса 4 насажены стрелка и втулка, связанная со спиральной пружиной 6, выбирающей зазор. Измерительное усилие создается пружиной 7.
Уход за фрезерными станками.
Срок службы, производительность и точность станка зависят от внимательного и аккуратного ухода за ним.
Чистка станка. Очень важное значение имеет очистка станка от грязи, пыли и стружки. Чистить станок следует тогда, когда он не работает. Хлопчатобумажными концами, смоченными в керосине, смывают со станка грязь и засохшее масло, а затем протирают сухими концами. Если на станке производилась обработка чугуна, надо щеткой смести всю стружку, которая накопилась на столе станка и забила пазы стола.
Чистку труднодоступных частей и углов нужно производить кистью или деревянной заостренной палочкой, обернутой тряпкой. Ни в коем случае не разрешается для очистки станка применять металлические предметы и наждачную бумагу.
Перед выходным днем следует тщательно протереть тряпкой с керосином весь станок, даже необработанные части его, а затем хорошо смазать трущиеся части, чтобы защитить их от ржавления.
После чистки станка все использованные тряпки и концы должны быть сложены в специальный ящик.
Для предохранения от попадания стружки в направляющие салазок и консоли на многих станках имеются защитные щитки с фетровыми прокладками. Эти прокладки следует промывать периодически керосином и очищать их от стружки.
Ограждения препятствуют разлетанию стружки, но не собирают ее на столе. Поэтому по окончании работы рекомендуется собрать стружку и аккуратно высыпать ее в ящик. Для больших нехов современных машиностроительных заводов разработаны способы механической уборки стружки.
Перед сдачей смены рабочий обязан убрать станок, смазать его и привести свое рабочее место в порядок, с тем чтобы следующая смена получила станок и рабочее место в полной готовности для выполнения заданной работы.
Смазка станка. Постоянный контроль смазки трущихся частей станка обеспечивает точную и долговременную его работу без ремонта.
Для смазки следует применять машинное масло марки «Л» или веретенное марки «2» и консистентные смазки.
Смазка коробки скоростей. В станках старых моделей применяется смазка разбрызгиванием; станки 6Н81, 6Н81Г, 6Н11, 6Н82, 6Н82Г, 6Н12, 6Н83, 6Н83Г и 6Н13 имеют плунжерный насос для смазки зубчатых колес коробки скоростей. Шпиндельные узлы вертикальных станков смазываются насосом или капельной масленкой. Масло, заливаемое в масляную ванну, следует периодически обновлять. При смене масла ванну и смазочную систему нужно промывать керосином.
Смазка коробки подач. В станках старых моделей смазка производится фитильными масленками или ручными насосами два раза в день или раз в смену; у станков 6Н81, 6Н81Г, 6Н11, 6Н82, 6Н82Г, 6Н12, 6Н83, 6Н83Г и 6Н13 смазка производится разбрызгиванием на зубчатые колеса и на ролик фрикциона и подачей масла к отдельным точкам под давлением из маслораспределителя.
Смазка консоли и стола. В станках старых выпусков смазка производится фитильными масленками, заполняемыми раз в смену; в станках 6Н81, 6Н81Г, 6Н11, 6Н82, 6Н82Г, 6Н12 и др. — под давлением от плунжерного насоса. Смазка салазок производится ручным насосом.
Подшипники стола смазываются ежедневно из масленок с поворотной крышкой.
Направляющие стола, консоли, станины смазывают перед началом работы из ручных масленок.
Подшипники оправки, размещенные в серьгах, смазывают периодически ручной масленкой.
Шарикоподшипники электродвигателя смазывают консистентной смазкой раз в шесть месяцев.
Прочие места смазывают согласно инструкции к станку.
На рис. 122 дана схема смазки универсально-фрезерного станка 6Н82 и горизонтально-фрезерного станка 6Н82Г. Коробка скоростей /, консоль 5 и коробка подач 6 смазываются централизованно от маслонасосов машинным маслом марки «Л». Салазки 3 смазывают при помощи ручного насоса — шесть качаний в смену; в насос следует доливать масло раз в неделю. Подшипники стола 2 и направляющие поперечного хода 4 смазывают из масленок машинным маслом марки «Л» раз в смену.
Места заливки и спуска масла, а также расположение маслоуказателей и фильтров показаны на рис. 122. Смену масла и очистку фильтра следует производить раз в полгода.
Смена охлаждающей жидкости. Охлаждающая жидкость должна быть чистой. При загрязнении жидкости надо остановить станок, удалить жидкость из резервуара, очистить резервуар
Дата добавления: 2018-04-04; просмотров: 1812; Мы поможем в написании вашей работы! |
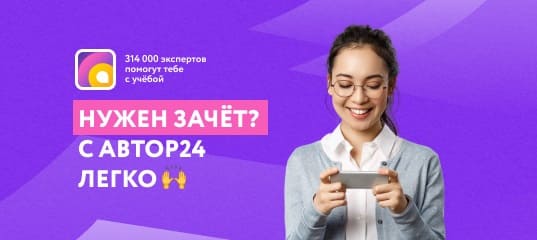
Мы поможем в написании ваших работ!