Наростообразование при резании металлов
При обработке пластичных металлов резанием на передней поверхности инструмента образуется слой металла, который называют наростом. Существует много различных гипотез о причинах возникновения наростов. Считается, что это сильно деформированный металл, структура которого отличается от структур обрабатываемого металла и стружки. Наростообразование находится в тесной взаимосвязи с условиями трения, высокими контактными температурами и давлениями. Наиболее вероятной причиной наростообразования можно считать то, что геометрическая форма инструмента не идеальна с точки зрения обтекания ее металлом. При некоторых условиях обработки силы трения между передней поверхностью инструмента и частицами срезанного слоя металла становятся больше сил внутреннего сцепления, и при наличии определенных температурных условий металл прочно оседает на передней поверхности лезвия инструмента, происходит торможение («схватывание») тонких контактных слоев стружки на шероховатой передней поверхности инструмента
Организация рабочего места фрезеровщика.
Основным оборудованием рабочего места фрезеровщика является фрезерный станок или группа станков с постоянными комплектами принадлежностей к ним. Оргоснастка на рабочем месте размещается в зависимости от расположения фрезерного станка (станков).
При групповом расположении фрезерных станков инструментальные шкафы должны быть вынесены за пределы рабочих мест. В этом случае на рабочем месте устанавливают стеллаж-этажерку для подготовленных к работе инструментов, оснастки и деталей. Такие приспособления, как делительные головки, поворотные столы, пневмотиски, следует хранить на стеллажах и подставках.
|
|
Для предотвращения поломки фрез и порчи поверхности стола станка тяжелые фрезы предварительно ставят на специальную деревянную подставку (в крайнем случае на кусок толстой доски) на стол станка. Для центрирования фрезы со шпинделем ее перемещают вместе с подставкой по поверхности стола или без подставки, с помощью стола и консоли станка. Затем ручным перемещением гильзы или ползуна шпинделя (на горизонтальных станках — перемещениями стола) конус оправки фрезы вводят в конусное отверстие шпинделя и закрепляют фрезу ручным завинчиванием (в резьбовое отверстие оправки) или механизированным зажимом.
Набор инструментов и оснастки на рабочем месте фрезеровщика определяется типом станка, номенклатурой обрабатываемых деталей, технологическим процессом и соблюдением требования о наличии на рабочем месте только самых необходимых, постоянно используемых приспособлений и инструментов.
|
|
Обработанные детали по мере их накопления следует увозить с рабочего места. Пол должен быть ровным, без выбоин и неровностей, на нем не должно быть потеков и капель масла или СОЖ. Следует своевременно очищать станки от стружки. Уровень шума на рабочем месте должен быть не выше 70 дБ. Оптимальная освещенность — 200 лк. Для защиты глаз от стружки необходимо применять защитные очки, индивидуальные щитки и специальные кожухи для фрез, устанавливаемых на станке.
Эффективная эксплуатация фрезерного станка обеспечивается постоянным уходом за рабочим местом: смазкой узлов станка в соответствии с требованиями, изложенными в руководстве по его эксплуатации; периодической проверкой точности перемещения узлов станка (стола и др.) и при необходимости соответствующей регулировкой. В обязанности фрезеровщика входят уборка стружки и СОЖ, а также контроль исправности электрооборудования и электропроводки.
Правильная организация рабочего места принесет положительные результаты. Фрезеровщик должен быть предельно внимательным, так как станок является зоной повышенной опасности.
26.стали. Сталь – это сплав двух химических элементов: железа (Fe) и углерода (С), причем содержание последнего не должно превышать 2%. Если углерода больше, то этот сплав относится к чугунам. Получают ее промышленным способом из чугуна, из которого под влиянием высоких температур выжигают избыток углерода и другие примеси. Стали в основном получают двумя способами: плавление в мартеновских печах и плавление электропечах.
|
|
По химическому составу стали классифицируются на углеродистые и легированные.
По назначению стали подразделяются на конструкционные, инструментальные и стали специального назначения.
По способу производства изделий стали классифицируются на деформируемые и литейные.
Все стали по качеству подразделяют на: - сталь обыкновенного качества; - качественная; - сталь повышенного качества; - высококачественная.
Углеродистая обыкновенного качества – Ст.1, Ст.2, Ст3пс и т. д. Цифры от 0 до 6 обозначают марку, с увеличением номера увеличивается содержание углерода. Буквы пс, кп; сп – индексы степени раскисления материала: полуспокойная, кипящая, спокойная соответственно.
Углеродистая качественная сталь – 05; 08; 10; 20пс; 08 кп. Цифры до 60 - это среднее содержание С в сотых долях процента, буквы пс, кп; сп – аналогично п.1.
|
|
Высоколегированные стали и сплавы, коррозионностойкие, жаропрочные и жаростойкие – 30ХГСА, ГН2; 50Х; 20ХН3А. Первые цифры - это содержание углерода: 30 – 0,3%; 40 - 0,4%; 45 – 0,45%, буквы – соответствующий легирующий элемент (Х-хром; Г – марганец; Т – титан; А-азот и т. д.), цифра за буквой – процентное содержание легирующего элемента. Если цифры нет, то доля вещества составляет 1,5%, буква А в конце означает, что это высококачественная сталь. Это применимо и для инструментальных, и для легированных сталей.
Углеродистая инструментальная – У7, У8, У10А. Расшифровка: У7 – 0,7%С; У8 – 0,8%С; У – углеродистая; А – высококачественная.
Легированная инструментальная – 5ХГН; Х12; 8Х3 и т.д. Расшифровка марки аналогично п.3, но содержание С указано в десятых долях процента. Если углерода менее 0,1%, то цифры не указываются – ХВ4; ХГС; ХВГ и т. д
Подшипниковая – ШХ4; ШХ15; ШХ15СГ. ШХ – подшипниковая, цифра – содержание хрома: ШХ4 – 0,4% хрома, ШХ15 – 1,5% хрома, другие буквы и цифры – содержание дополнительных легирующих элементов.
Конструкционная повышенной и высокой обрабатываемости резанием – А12, А20, А30, А40Г. Расшифровка содержания углерода: А20 – 0,2%С, А12 – 0,12%С, А30- 0,3%С.
27.определение формы детали, анализ всех элементов чертежа. Последовательность чтения чертежей деталей [1]:
1)прочитать основную надпись чертежа, уяснить название детали, применяемый материал, масштаб изображений;
2)установить взаимосвязь между всеми изображениями на чертеже, а также уяснить, какие виды и условные изображений элементов детали представлены на чертеже;
3)установить форму детали путем мысленного расчленения ее на составляющие геометрические элементы;
4)уяснить, к каким элементам детали относятся размеры, какую величину они обозначают (диаметр, длину, ширину, глубину и т. д.), что поможет уточнить форму не ясных элементов детали. Найти размерные базы, а затем установить наиболее ответственные размеры сопрягаемых элементов, т. е. размеры, для которых обозначены предельные отклонения, поля допусков с более высоким классом точности, а обозначения шероховатости поверхностей поставлены непосредственно у изображений этих элементов;
5)установить все технические требования и другие указания, которые обусловливают особенности и последовательность работы по чертежу. Особое внимание следует обращать на указания о допустимых отклонениях от номинальных размеров геометрической формы и положения поверхностей детали, на параметры шероховатости поверхностей;
6)уяснить порядок и все рациональные действия, необходимые в процессе изготовления детали для превращения заготовки или полуфабриката в готовую деталь, а также установить метод контроля, определить приспособления, обеспечивающие ускорение работы, повышение качества детали, экономию материала.
Дата добавления: 2018-04-04; просмотров: 520; Мы поможем в написании вашей работы! |
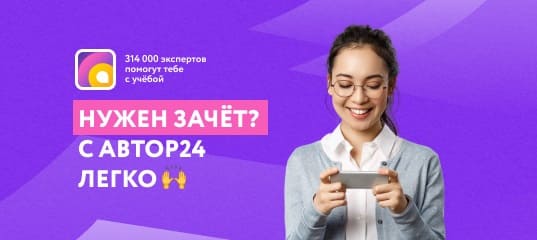
Мы поможем в написании ваших работ!