ПРИВОД МАШИНЫ, ХАРАКТЕРИСТИКА ЕГО ЭЛЕМЕНТОВ
МИНИСТЕРСТВО ОБРАЗОВАНИЯ И НАУКИ УКРАИНЫ
Севастопольский национальный технический университет
СИНТЕЗ ЭЛЕКТРОМЕХАНИЧЕСКОГО ПРИВОДА
СУДОВОЙ МАШИНЫ И ПАЛУБНОГО МЕХАНИЗМА
Методические указания
к выполнению курсового проекта (расчетно – графической работы)
по дисциплине
«Теория машин, механизмов и детали машин»
для студентов специальностей:
7.100301 «Судовождение на морских и внутренних водных путях»,
7.100302 «Эксплуатация судовых энергетических установок»
всех форм обучения
Севастополь
2008
УДК 531
Синтез электромеханического привода судовой машины и палубного механизма: Методические указания к выполнению курсового проекта (расчетно -графической работы) по дисциплине «Теория машин, механизмов и детали машин»для студентов специальностей: 7.100301 «Судовождение на морских и внутренних водных путях», 7.100302 «Эксплуатация судовых энергетических установок» всех форм обучения. Часть 1.Подбор и расчет элементов привода/ Сост. А.В. Неменко – Севастополь: Изд – во СевНТУ 2006. - 168 с.
Целью указаний является оказание помощи студентам при выполнении курсового проекта (расчетно – графической работы) по дисциплине «Теория машин, механизмов и детали машин». В методических указаниях изложена методика синтеза узлов привода, расчета его конструктивных элементов, а также установление энерго – кинематических и эксплуатационных характеристик судовых механизмов
|
|
Методические указания составлены в соответствии с рабочей программой курса «Теория машин, механизмов и детали машин», рассмотрены и утверждены на заседании кафедры технической механики и машиноведения 21.02.2006, протокол № 6
Допущено учебно – методическим центром СевНТУ в качестве методических указаний
Рецензенты: заведующий кафедрой «Судовождение и безопасность судоходства»,
доктор технических наук, профессор В.В. Капустин;
доцент кафедры «Эксплутация морских судов и сооружений»,
кандидат технических наук О. В. Владецкий
ISBN ББК 39.45 + 34.447
© Издательство СевНТУ, 2008
СОДЕРЖАНИЕ
Введение.………………….……………… …………………………………………….4
1.Привод машины. Характеристика его элементов и параметры эксплуатации....…5
1.1. Состав привода машины и описание его компонентов.……………………….....5
|
|
1.2. Характеристики нагружения.….…………………………………………………15
1.3. Режимы нагружения....……………………………………………………………17
2. Механизмы передачи вращательного движения..………..………………………24
2.1. Синтез механизмов передачи вращательного движения.………………………24
2.2. Синтез зубчатых передач с эвольвентным профилем.…..………………..……30
2.3. Основы расчета элементов механических передач на прочность...…..………..42
2.3.1.Силы, действующие в зацеплении....……………………………………………42
Напряжения в зацеплении....................................................................................44
2.4. Материалы элементов передач..…...……………………………………………46
2.5. Особенности планетарных и волновых передач..……………………………….47
2.5.1. Планетарные передачи.………………………………………………………….47
2.5.2. Волновые передачи.……………………………………………………………..50
2.6. Энерго – кинематические параметры привода.....……………………………….52
3. Расчет элементов привода.....………….………………………………………….54
3.1. Исходные данные......………………………………………………………..…….54
3.2. Расчет исполнительного органа...………………………………………….……..54
3.3. Выбор электродвигателя привода (механизма подъема груза......……………..57
3.4. Передаточное отношение механизма и выбор редуктора......…………………..58
|
|
3.5. Подбор муфт......……………………………………………………….…………..58
3.6. Характеристика работы механизма подъема груза..…..…………….…………..60
3.7. Выбор тормоза......…………………………………………………………..……..62
4. Расчет элементов редуктора.......………………………………………………….63
4.1. Передаточные характеристики.....………………………………………..………63
4.2. Передача цилиндрическая.....……………………………………………………..65
4.3 Передача планетарная с цилиндрическими колесами.....……………………….85
4.4 Передача волновая………………………………………………………………..114
4.5. Передача коническая……………………………………………………………..127
4.6. Передача червячная с цилиндрическим червяком....…..………………………140
4.7. Передача ременная...……………………………………………………………..149
4.8. Передача цепная....…………………………………………………………..….. 152
4.9. Валы, их опоры и соединения....……………….……………………………….156
4.10. Расчет элементов передачи и корпуса редуктора....………………………….162
4.11. Выбор уплотнительных устройств и подбор смазки...…………………….…164
5. Мероприятия по эксплуатации...….…………………………………………….165
5.1. Организация технического обслуживания и ремонта………………………….165
|
|
5.2 Контроль состояния узлов привода….…………………………………………..165
Библиографический список……………………………………………………….….166
Приложение А. Справочные данные………………………………………………..168
Приложение Б. Примеры выполнения чертежей……..……………………………284
Приложение В. Виды и система условных обозначений
подшипников качения……………………………………………...319
ВВЕДЕНИЕ
Привод машины – система передачи энергии от источника к исполнительному органу, состоящая из двигателя и связанных с ним устройств.
В учебном пособии рассматриваются вопросы расчета механических компонентов электропривода машин.
Технический уровень любого агрегата определяется качеством составляющих его узлов, которые могут быть изготовлены или на специализированных производствах серийно, или индивидуально с использованием нормативных рекомендаций.
Правильное компонование привода позволяет получить оптимальные эксплуатационные характеристики проектируемой машины, к которым относятся долговечность и надежность, безопасность обслуживания и экономичность в изготовлении.
Критерий долговечности обеспечивается рядом свойств, среди которых важнейшие – прочность, износоустойчивость, твердость, технологичность.
Машины разнообразны по назначению, и разными могут быть условия их эксплуатации. Тем не менее, существует определенная типичная архитектура их приводов, которая позволяет унифицировать их расчеты и провести рациональный композиционный синтез. В данной работе приведена методика расчета и проектирования механических компонентов электропривода грузоподъемной машины. Для других типов машин расчет механических компонентов электропривода проводится аналогично. Однако в каждом конкретном случае он будет индивидуальным и включать в себя необходимые разделы. Поэтому материал пособия состоит из отдельных тематических глав и представлен в табличной форме.
В данном учебном пособии рассмотрены вопросы подбора и расчета механических компонентов электропривода машины, приведены необходимые справочные и пояснительные материалы, а также примеры выполнения технической документации.
В первом разделе представлено описание состава привода, его элементов. Во втором разделе рассматриваются параметры эксплуатации привода: режимы работы машины, типовые режимы нагружения, а также некоторые теоретические аспекты, которые могут быть полезны перед переходом к расчетной части. Рекомендации, изложенные в третьем разделе, позволяют скомпоновать привод в целом. В четвертом разделе представлены расчеты разных типов передач, их опор и других механических элементов конструкций электропривода. Основные рекомендации по эксплуатации привода изложены в пятом разделе.
В приложениях приведены справочные данные и примеры выполнения технической документации
ПРИВОД МАШИНЫ, ХАРАКТЕРИСТИКА ЕГО ЭЛЕМЕНТОВ
И ПАРАМЕТРЫ ЭКСПЛУАТАЦИИ
1.1. Состав привода машины и характеристика его элементов
Привод машины состоит из узлов, которые условно можно разделить на категории по характеру их использования:
- сообщающие движения;
- преобразующие движение;
- узлы соединительные (муфты и т.п) и поддерживающие (валы и их опоры);
- терминалы или исполнительные органы.
Примеры приводов машин представлены на рисунке 1.1
Рисунок 1.1 – Схемы типовых приводов машин:
а) привод конвейера, б) привод грузовой лебедки
1 – электродвигатель; 2 – передача клиновидным ремнем; 3 – редуктор;
4 – передача цепью; 5 – муфта эластичная; 6 – тормоз; 7 – муфта зубчатая;
8 – барабан; 9 – гибкий орган; 10 – крюковая подвеска
В качестве источника энергии для привода чаще всего используются электродвигатели. Для приводов машин преимущественно применяют трехфазные электродвигатели переменного тока: асинхронные двигатели с короткозамкнутым ротором серии МТКF, МТКН и АИР и электродвигатели с фазным ротором серии МТF и МТН, а также электродвигатели переменного тока серии МАП (машины асинхронные повышенного скольжения).
Применяются также и двигатели постоянного тока серии ДПМ (двигатели постоянного тока морского исполнения).
На рисунке 1.2 представлен электродвигатель серии МАП.
Рисунок 1.2 – Электродвигатель серии МАП
Исполнительная часть механизма может включать в себя либо барабан, гибкий орган и грузозахват, как в механизме подъема груза (рисунок 1.1,б), либо цепную часть конвейера (рисунок 1.1,а), либо другие типы исполнительных механизмов.
В качестве гибких органов применяют стальные, проволочные канаты различных типов. Канаты различают по диаметру, по маркировочной группе (для подъемно – транспортных машин 1372, 1470, 1668, 1666, 1764, 1862, 1960, 2156, 2254, 2352 МПа), по количеству проволок в прядях и количеству прядей в канате, по материалу сердечника (пеньковый, асбестовый, стальной и т.п.) и другим специальным признакам. Подбор каната производят по расчетному разрывному усилию по нормам Госгортехнадзора в зависимости от режима работы механизма.
В грузоподъемных машинах общего назначения для захватывания груза служат крюки. При двух и более несущих ветвях применяют крюковые подвески
(рисунок 1.3).
Рисунок 1.3 – Подвеска крюковая:
1– крюк; 2 – ось блок канатный; 3 – ось блока; 4– подшипник блока;
5– подшипник крюка
Для изменения направления движения и поддержания каната служат блоки. Они бывают подвижные и неподвижные. Подвижные блоки, кроме изменения направления каната, обеспечивают получение выигрыша в силе.
Система подвижных и неподвижных блоков, огибаемых канатом, образует полиспаст (рисунок 1.4). Характеристикой полиспаста является его кратность. Полиспасты бывают одинарные и спаренные. Кратность одинарного полиспаста равна числу ветвей каната, воспринимающих нагрузку.
Рисунок 1.4 – Схемы полиспастов с различной кратностью:
1 – барабан; 2 – неподвижный блок; 3 – подвижный блок
Для преобразования вращательного движения привода механизма в поступательное движение подъема или опускания груза служат канатные барабаны (Рисунок 1.5).
Рисунок 1.5 – Барабан для однослойной навивки каната:
1 – корпус; 2 – вал; 3 – канат; 4 – планка прижимная; 5 – опора
В приводах производственных машин частота вращения элементов исполнительного органа, как правило, не равна частоте вращения выходного вала двигателя. Для согласования энерго – кинематических параметров «входа – выхода» привода применяют узлы, преобразующие движение, композиция которых определяется передаточной функцией привода. В случае, когда эта функция направлена на понижение частоты вращения узел называется редуктором (от лат. reductor – отводящий назад, понижающий). Если выходные энерго – кинематические параметры привода не могут быть обеспечены одной передачей, используют необходимое количество сочетаемых передач, которые образуют двух- трех- или многоступенчатые редукторы. В приводах машин используют, как стандартные редукторы, так и разработанные индивидуально. В таблицах А.10 – А.14 Приложения А представлены типы и некоторые параметры распространенных редукторов.
В редукторах применяют различные типы передач: цилиндрические (прямозубые, с наклонным зубом, шевронные), конические, червячные, планетарные и волновые, а также передачи с гибкой связью (ременные и цепные).
Цилиндрическая зубчатая передача (рисунок 1.6) осуществляет движение между
параллельными осями. Колеса, образующие ее, имеют начальные и делительные поверхности в виде цилиндров.
Рисунок 1.6 – Передача цилиндрическая: 1– колесо ведущее; 2 – колесо ведомое
Коническая зубчатая передача (рисунок 1.7) осуществляет передачу движения между пересекающимися осями. У зубчатых колес конической передачи начальные и делительные поверхности – конические.
Рисунок 1.7 – Передача коническая: 1 – колесо ведущее; 2 – колесо ведомое
Планетарная зубчатая передача (рисунок 1.8) служит для передачи и преобразования вращательного движения и содержит центральные колеса (a, b) и колеса с перемещающимися осями вращения, которые называют сателлитами (g). Звено, на котором установлены опоры сателлитов, называется водилом (h). Число сателлитов обозначается nw. Наибольшее распространение получили передачи с nw =3. Ось вращения водила называется основной осью. В планетарных передачах сочетаются внешнее (a–g) и внутреннее (g–b) зацепление. Звенья, вращающиеся вокруг основной оси называются основными звеньями. Неподвижным может быть любое из основных звеньев.
Рисунок 1.8 – Передача планетарная: а, b – колеса центральные; h – водило;
g1, g2, g3 – колеса с перемещающимися осями вращения (сателлиты)
Волновая зубчатая передача (Рисунок 1.9) является конструктивной разновидностью планетарной передачи с одним центральным жестким колесом b и сателли-том g, выполненным в виде тонкостенного гибкого цилиндра с зубчатым венцом, деформируемым в процесее работы водилом h (генератором волн).
Рисунок 1.9 – Схема образования волновой передачи: а) – передача планетарная с одним сателлитом; б) – передача волновая с одной зоной зацепления; в) – передача волновая с двумя зонами зацепления (b – колесо центральное; g – сателлит – колесо гибкое зубчатое; h – водило)
Движение между валами со скрещивающимися осями осуществляется червячной передачей, которая состоит из червяка и червячного колеса (рисунок 1.10).
Рисунок 1.10 – Передача червячная: 1 – червяк; 2 – колесо червячное
Зацепление червячного колеса подобно зацеплению цилиндрического колеса с рейкой. Для нормальной работы червячного зацепления необходимо соблюдение равенства шагов (расстояний между одноименными точками соседних зубцов) на делительном диаметре в осевой плоскости червяка и делительном диаметре колеса. Червячные передачи дают возможность получения большого передаточного отношения в одноступенчатой передаче, плавность и бесшумность работы, возможность самоторможения. Различают передачи с цилиндрическими (делительная поверхность червяка – цилиндрическая) и глобоидными (делительная поверхность червяка является частью вогнутой поверхности тора) червяками.
При передаче движения червячное колесо вступает в зацепление с витками червяка, расположенными на его поверхности вращения. Угол наклона зуба червячного колеса равен углу подъема g линии витка червяка.
В приводах также используют передачи с гибкой промежуточной связью: ременную (рисунок 1.11) и цепную (рисунок 1.12) В качестве гибкой связи выступает ремень или цепь.
Рисунок 1.11 – Передача ременная: 1 – шкив ведущий;
2 – шкив ведомый; 3 – ремень
Рисунок 1.12 – Передача цепная:
1 – звездочка ведущая; 2 – звездочка ведомая; 3 – цепь
Передающие движение элементы (колеса, звездочки, шкивы) устанавливаются на валах с определенной посадкой с использованием дополнительных связей в виде шпонок и других элементов.
Опоры валов (рисунок 1.13) служат для их поддержания и обеспечения стабильной работы передачи. Подшипник – часть опоры вала, который обеспечивает перемещение вала в опоре.
Рисунок 1.13 – Вал с опорами: 1 – вал шестерни; 2 – колесо; 3 – шпонка;
4 – подшипник; 5 – крышка подшипника
Узлы, комплектующие машину, соединяются между собой с помощью специальных устройств (муфт и т.п.).
Приводные муфты передают вращательное движение и крутящий момент с одного вала на другой, расположенный соосно, или с вала на установленную на нем деталь. С помощью муфт решается кинематическая и силовая задача, а также ряд монтажных и эксплуатационных аспектов. Муфты бывают глухие, компенсирующие предельные и управляемые.
На рисунке 1.14 изображена компенсирующая упругая втулочно – пальцевая муфта (МУВП), на которую может устанавливаться тормоз (размеры ВТ и DT соответствуют внутренним размерам тормозных колодок). Она, как правило, устанавливается в приводе между электродвигателем и редуктором и демпфирует динамические нагрузки. Полумуфта под тормоз располагается со стороны редуктора.
Рисунок 1.14 – Муфта упругая втулочно - пальцевая
На рисунке 1.15 изображена зубчатая муфта, которая устанавливается между редуктором и барабаном и компенсируют угловые отклонения валов под нагрузкой. При необходимости установки на ней тормоза, полумуфта, расположенная со стороны исполнительного органа выполняется по размерам тормозного шкива.
Рисунок 1.15 – Муфта зубчатая
Для остановки и пуска механизма служат тормоза ( см. приложение А, табли-
цы А.21, А.22). В машинах часто применяют тормоза, пристроенные к двигателю. В приводе возможна установка двух тормозов.
В приводах используются тормоза колодочные (рисунок 1.16), ленточные, дисковые, конические. По направлению действия усилий нажатия на тормозной элемент они бывают с радиальным и осевым замыканием, по источнику замыкающей силы – ручные, пружинные, грузовые и гидравлические, а по характеру действия приводного усилия – закрытого типа (постоянно замкнуты внешней силой и размыкаются во время работы механизма), открытого типа (замыкаются для остановки механизма) и комбинированные (в нормальных условиях работают как открытого типа, в аварийных – закрытого). Тормоза бывают автоматические и управляемые.
Рисунок 1.18 – Схема колодочного тормоза: 1, 2 – тормозные колодки;
3, 4 – рычаги; 5 – пружина
Правила эксплуатации машин и механизмов определяются требованиями Госгортехнадзора. Они обязательны для предприятий всех министерств и ведомств. В Правилах даны указания по вопросам, относящимся к технической эксплуатации и ремонту механизмов: организация надзора и обслуживания, порядок регистрации; разрешение на пуск в работу; технические освидетельствования; разрешение на изготовление и ремонт; материалы и сварка. Технические освидетельствования, предусматриваемые Правилами, делятся на полные (включающие дефектоскопию, статические и динамические испытания) и частичные, проводимые без испытаний.
Полному техническому освидетельствованию подвергают вновь установленные механизмы, находящиеся в эксплуатации (не реже одного раза в 3 года), а также механизмы после переноса их на новое место работы, реконструкции и некоторых ремонтных работ. Частичное освидетельствование предусматривается не реже одного раза в 12 месяцев.
Правила вкдючают в себя три вида освидетельствований: первоначальное, периодические и внеочередные.
Первоначальное освидетельствование сопровождается испытанием и полным освидетельствованием механизмов.
Периодические испытания проводят не реже чем один раз в пять лет.
Внеочередные освидетельствования и испытания производят после замены, пе-
реоборудования или ремонта механизмов или их деталей, а также после аварий.
Механизм сначала испытывают пробной нагрузкой при статическом режиме. Затем производят испытания пробной нагрузкой при работе механизмов с полными
скоростями и предусмотренным совмещением движений. Одновременно проверяют действие тормозов и концевых выключателей.
Статические испытания механизмов проводят нагрузкой, превышающей ее номинальное значение на 25 %. Динамические испытания механизмов производят нагрузкой, превышающей на 10 % номинальное значение.
Нагрузку, воспринимаемую механическими компонентами привода в процессе эксплуатации машины, называют рабочей.
Номинальной считают рабочую нагрузку, наиболее характерную для рассматриваемого механизма и его элементов. Номинальную нагрузку принимают в качестве исходной для определения расчетной нагрузки.
Расчетная нагрузка зависит от рабочей нагрузки и критериев работоспособности конкретных механизмов, с учетом условий их нагружений.
Состояние механизма, при котором он способен выполнить заданные функции сохраняя значения параметров в пределах, установленных нормативной регламентацией, зависит от ряда критериев к числу которых нужно отнести прочность, жесткость, износостойкость, теплостойкость, виброустойчивость и т.д.
В зависимости от условий работы те или иные критерии получают приоритет по отношению к остальным.
Характеристики нагружения
Под действием внешних нагрузок возникает деформация в материале элемента, связанная с механическим напряжением, которая является мерой внутренних сил, возникающих под влиянием внешних воздействий. Под действием нормально приложенных сил (растяжение, сжатие) или изгибающих моментов возникают нормальные напряжения s, перпендикулярные к сечениям деформируемого элемента. Под действием поперечных сил или крутящих моментов возникают касательные напряжения t, которые расположены по касательной к деформируемому сечению.
Нагрузки, и соответветственно, напряжения от них, возникающие в элементах конструкции в процессе эксплуатации могут быть постоянными и переменными.
Переменной является нагрузка, когда деталь не сохраняет неизменным свое положение относительно вектора нагружения. Эта нагрузка вызывает внутреннее усилие непостоянного характера. Когда ее изменение по величине и направлению повторяется с определенной последовательностью (цикличностью), нагрузку называют циклической.
Совокупность последовательных значений нагрузок (внешних или внутренних) за один период их изменения называют циклом.
В случае, когда переменная нагрузка имеет циклический характер, она вызывает циклические изменения напряжений со следующими характеристиками цикла:
- среднее напряжение sm или tm
sm=(smax+smin)/2, (1.1)
tm=(tmax+tmin)/2; (1.2)
- амплитуда sa или tа
sa=(smax- smin)/2, (1.3)
tа=(tmax - tmin)/2; (1.4)
- коэффициент асимметрии Rs или Rt
Rs=smin/smax , (1.5)
Rt=tmin/tmax . (1.6)
Коэффициент асимметрии цикла проставляется нижним индексом при знаке напряжения (sR – при обозначении нормальных напряжений; tR – при обозначении касательных напряжений).
В механических компонентах привода машин возникают следующие циклы изменения напряжений: отнулевой , когда напряжения меняются от нуля до максимума (s0, t0), знакопеременный симметричный, когда напряжения меняются от отрицательного до такого же положительного значения (s-1, t-1), асимметричный, когда коэффициент асимметрии цикла не равен нулю и не равен ±1 .
Под действием циклических нагрузок детали выходят из строя быстрее, чем при статических, т.к. при циклическом нагружении изменения структуры материала накапливаются и вызывают отказ в работе объекта более ранний, чем при статическом нагружении. Происходит усталостное разрушение детали.
Кривая выносливости (кривая Веллера) представляет собой зависимость предельного числа циклов нагружения, при которых произошло разрушение на фиксированных уровнях напряжений. Кривая выносливости строится для каждого конкретного материала на основе экспериментальных данных.
Наибольшее напряжение цикла, которое деталь может выдержать не разрушаясь с заданной вероятнстью при практически неограниченном цикле нагружений, называют пределом выносливости.
Уравнение кривой выносливости имеет вид
sq×Nc=const, (1.7)
где s – заданный уровень напряжения, МПа; Nc – предельное число циклов нагружения; q – показатель степени кривой выносливости (зависит от напряженного состояния, формы детали, механических характеристик, термообработки и т.п. и колеблется в пределах, q=6…9).
На уровне предела выносливости кривая выносливости становится практически горизонтальной линией.
Если число циклов нагружения ограничено базовой величиной, то наибольшее напряжение цикла называют пределом ограниченной выносливости (slim b).
Предел контактной выносливости (sНlim b) и предел выносливости на изгиб (sFlim b), соответствующие базовым числам циклов перемены напряжений устанавливают по полуэмпирическим зависимостям для конкретных случаев.
Расчеты на прочность ведут по допускаемым напряжениям, по запасам прочности или по вероятности безотказной работы.
Расчет по допускаемым напряжениям обычно выполняют как проектировочный, а проверочный расчет производят сравнением действительного коэффициента запаса прочности s рассчитываемого элемента с его допускаемым значением [s]
s³[s]. (1.8)
Запас прочности механического элемента учитывает условия эксплуатации и регламентные рекомендации.
Оценка прочности элементов механизма состоит в сравнении напряжений, возникающих при действии эксплуатационных нагрузок, с их допускаемыми значениями (нормальными s и касательными t):
s£[s] (1.9)
t£[t] (1.10)
Допускаемые напряжения устанавливают по следующим зависимостям:
[s]=slim/[ss], (1.11)
[t]=t lim/[st]. (1.12)
Здесь slim и t lim – предельные значения нормальных и касательных напряжений, соответственно; [ss] и [st]– допускаемые (требуемые, заданные или нормативные) коэффициенты запаса прочности для рассчитываемого элемента.
Для пластичных материалов в качестве предельных напряжений принимают предел текучести (sт – при растяжении, сжатии, изгибе; tт – при кручении) . Для хрупких материалов в качестве предельных напряжений принимают предел прочности
(sв – при растяжении, сжатии, изгибе; tв – кручение, срез).
В расчете на прочность элементов при переменных напряжениях в качестве предельных напряжений принимают соответствующие пределы выносливости
(sR – растяжение, сжатие и изгиб; tR – кручение, срез).
Расчетный (фактический) коэффициент запаса прочности при симметричном цикле перемены напряжений определяют по зависимостям:
- при растяжении, сжатии, изгибе
ss=s-1/( КsD×sа +ys×sm); (1.13)
- при кручении
st=t-1/( КtD×tа +yt×tm); (1.14)
- при совместном действии нормальных и касательных напряжений
s=ss× st/( s2s+ s2t)1/2 . (1.15)
Здесь s-1 и t-1 – пределы выносливости материала при знакопеременном симметричном цикле напряжений; КsD и КtD – коэффициенты, учитывающие размер деталей и концентрацию напряжений; ys и yt – коэффициенты, учитывающие чувствительность материала к аксимметрии цикла.
Одним из наиболее общих условий применимости элементов механизма является условие равнопрочности.
Режимы нагружения
В течение всего срока службы величины нагрузок на механизм различны, что учитывается режимами работы, которые устанавливаются совокупной оценкой характерных нагружений с учетом их времени действия и общим временем эксплуатации. При расчете механизмов и их элементов учитывают режимы работы (таблица 1.1), которые установлены по классу использования (таблица 1.2) и классу нагружения (таблица 1.3).
Таблица 1.1 – Группа режима работы механизмов по ГОСТ 25835 – 83
Класс использования | Группа режима работы механизма для класса нагружения | Класс использования | Группа режима работы механизма для класса нагружения | ||||||
В1 | В2 | В3 | В4 | В1 | В2 | В3 | В4 | ||
А0 | 1М | 1М | 1М | 2М | А4 | 3М | 4М | 5М | 6М |
А1 | 1М | 1М | 2М | 3М | А5 | 4М | 5М | 6М | 6М |
А2 | 1М | 2М | 3М | 4М | А6 | 5М | 6М | 6М | 6М |
А3 | 2М | 3М | 4М | 5М |
Класс использования механизма (таблица 1.2) устанавливают по времени Lh его работы
Таблица 1.2 – Классы использования механизмов (ГОСТ 25835-83)
Класс использования | А0 | А1 | А2 | А3 | А4 | А5 | А6 |
Общее время работы механизмов Lh, ч | До 800 | 800… 1600 | 1600… 3200 | 3200… 6300 | 6300… 12500 | 12500… 25000 | 25000… 50000 |
Общее время работы Lh механизма рассчитывают по следующей формуле
Lh =365×24 ×Тг×Kг×Kс×Kр× ПВ /100 , (1.16)
где Тг – срок службы (требуемый), лет;
Kг – коэффициент годового использования при числе дней в году T г равен
Kг=T г/365, (1.17)
Kс – коэффициент суточного использования механизма, который при количестве работы часов в сутки tс составит
Kс=t с/24, (1.18)
Kр – коэффициент часового использования механизма, который при количестве минут работы механизма в течение часа tр, вычисляется соответсвенно
Kр=tр/60, (1.19)
ПВтехн – относительная продолжительность включения, характеризующая интенсивность использования механизма и определяемая отношением той части времени tв цикла, когда механизм работает к полному времени технологического цикла tц, равному сумме времени tп пуска, времени tуст движения с установившейся скоростью, времени tт торможения и времени tпауз пауз (tц =tп+tуст +tт +tпауз)
ПВ=(tв/tц)×100% . (1.20)
Для механизмов принимают tц не более одного часа. При этом ПВ может принимать значения 15, 25, 40, 60.
Для двигателей повторно - кратковременного режима допустимое время цикла установлено равным 10 мин. Если tц >10 мин, то режим работы двигателя считается продолжительным ПВ=100%.
Общее времени работы механизма назначается с учетом наибольшей экономичности для ожидаемых условий использования механизма. Для механизмов, у которых предусмотрен капитальный ремонт норма устанавливается до капитального ремонта. Для механизмов, у которых капитальный ремонт не предусмотрен норма устанавливается до списания.
Класс нагружения механизмов (таблица 1.3) устанавливают по коэффициенту нагружения К.
Таблица 1.3– Класс нагружения механизма и его характеристики (ГОСТ 25835-83)
Класс нагружения | Коэффициент нагружения К | Качественная характеристика класса нагружения |
В1 | До 0,125 | Работа при нагрузках значительно меньшей номинальной и в редких случаях с номинальной нагрузкой |
В2 | 0,125…0,25 | Работа при средних и номинальных нагрузках |
В3 | 0,25…0,5 | Работа преимущественно при номинальных и близких к номинальным нагрузкам |
В4 | 0,5…1,0 | Постоянная работа при номинальных и близких к номинальным нагрузкам |
Коэффициент нагружения К вычисляют по следующей формуле
К=å[(Qi/Qmax)3×(ti/åti)], (1.21)
где Qi – нагрузка, действующая на механизм в течение времени ti; Qmax – наибольшая нагрузка, действующая на механизм в течение времени его работы;
ti – продолжительность времени действия нагрузки Qi; åti – суммарное время действия нагрузок на механизм.
Значения нагрузок определяют для концевого звена кинематической цепи механизма (канатный барабан и т.п.), с учетом всех факторов, включая и процессы неустановившегося движения.
Нагрузки могут быть заданы усилием F (Н), моментом Т (Н×м), а также мощностью Р (кВт) при частоте вращения n (об/мин) или угловой скорости w (рад/с).
Число циклов Nсi нагружения элемента вращающим моментом Тi (или другим каким – либо силовым эквивалентом)за время ti при частоте вращения ni устанавливается по формуле
Nсi=60× ni×ti. (1.22)
Суммарное число циклов нагружения Nсå за время Lh нагружения элемента равно
Nсå= Nс1 + Nс2+…+ Nск, (1.23)
где Nс1, Nс2,…, Nск - число циклов нагружения элемента моментами Т1 , Т2, …,Тк за периоды времени t1, t2,…,tк соответственно, (t1 +t2 +…+tк =Lh). Величины t1, t2,…,tк представляют собой совокупное время действия нагружающих воздействий Т1, Т2, …,Тк в различные периоды в течение всего срока службы. Эксплуатационные нагрузки Т1,Т2, …,Тк можно сгруппировать по величине в относительных единицах, сопоставив с максимальной Тmax величиной (Т1/Тmax, Т2/Тmax, …,Тк/Тmax) и установить их время действия относительно всего срока службы (t1/th, t2/th,…, tк/th) или относительно общего числа циклов нагружения (Nс1/Nсå, Nс2/Nсå, …, Nск/Nсå).
Удельный вклад каждой совокупности нагрузок в сочетании со временем их действия относительно общей загрузки механизма является основанием для назначения типа режима нагружения.
В Правилах Госгортехнадзора различают режимы работы механизма легкий (Л), средний (С), тяжелый (Т) и весьма тяжелый (ВТ) .
На рисунке 1.19 показаны циклограммы нагруженности механизма подъема.
Рисунок 1.19 – Графики загрузки механизма подъема груза по режимам: 1 – легкий режим; 2 – средний режим; 3 – тяжелый режим
На основе статистической обработки реальных эксплуатационных режимов полу-
чены типовыережимы нагружения механизмов.
ГОСТ 21354 – 87 предлагает следующие типовые режимы нагружения: постоянный П, тяжелый Т (b - распределение), средний равновероятный Р (равновероятное распределение), средний нормальный Н (нормальное распределение), легкий Л (g - распределение) и особо легкий Ло (b - распределение).
В таблице 1.4 и на рисунке 1.20 изображена упорядоченная зависимость между нагружающими моментами и числом циклов нагружения в относительных коор-
динатах T/Tmax и Nс/Nсå.
Таблица 1.4 – Типовые режимы нагружения (ГОСТ 21354 –87)
Виды режимов нагружения | Функция распределения | Параметры функции распределения |
1) Тяжелый режим – интегральная функция b- распределения | ni Ф(ni)=ònia-1(1-ni)b-1dni/B(a,b) 0 | a=6; b=2 nср=0,77 |
2) Средний – равновероятный, интегральная функция равновероятного распределения | ni Ф(ni)= òdni 0 | nср=0,5 |
3) Средний – нормальный, интегральная функция нормального распределения | n - (ni-nср) 2 /2s2 Ф(ni)=òe ×dni/[s(2×p)1/2] -¥ | nср=0,5; s=0,19 |
4) Легкий – интегральная функция b - распределения | ni Ф(ni)=ònia-1× (1-ni)b-1×dni] B(a,b) 0 | а=2,2; b=3,0 nср=0,42 |
5) Особо легкий - интегральная функция b- распределения | ni Ф(ni)=ònia-1× (1-ni)b-1×dni/B(a,b) 0 | a=1,8; b=4,0 nср=0,31 |
Примечание. Коэффициенты: ni= Тi / Tmax ; nср= Tср / Tmax, где Ti – текущий вращающий момент на ведущем элементе, соответствующий числу циклов нагружения Nсi; Тmax – максимальное значение вращающего момента; Tср – среднее значение вращающего момента. |
Рисунок 1.20 – Типовые режимы нагружения (ГОСТ 21354 – 87): 0 – постоянный;
1 – тяжелый ; 2 – средний равновероятный;3 – средний нормальный; 4 – легкий ;
5 – особо легкий
Особенности циклограмм отражает коэффициент интенсивности m, который характеризует интенсивность типового режима при базовом числе циклов Nlim:
- для ступенчатой циклограммы
m =å( Тi / Тmax )3(Nci/Nlim). (1.24)
- при плавном характере циклограммы (рисунок 2.19)
Tmax
m =ò( Тi / Тmax )3(Nci/Nlim), (1.25)
Tmin
Соответствие режима нагружения механизма одному из типовых режимов устанавливается по подобию форм кривых и по среднему значению нагрузок. В расчетах следует принимать типовой режим наиболее близкий к фактическому в области больших нагрузок путем сравнения реальной циклограммы с типовыми или эквивалентными режимами нагружения.
Группы режимов работы механизмов по ГОСТ 25835–83, типовые режимы по ГОСТ 21354 – 87 и режимы по правилам Госгортехнадзора приведены в таблице 1.5
Таблица 1.5 – Соответствие групп режимов работы механизма
Режим эксплуатации по ГОСТ 21354–87 | «0» непрерывный | «1» тяжелый | «2» средний равновероятностный | «3» средний нормальный | «4» легкий | «5» Особо легкий |
Режим работы по ГОСТ 25835–83 | 6М | 5М | 4М | 3М | 2М | 1М |
Режим по правилам Госгортехнадзора | «ВТ» ПВ(%)= 63…100 | «Т» ПВ(%)= 40…63 | «Срв» ПВ (%)= 25…40 | «Сн» ПВ (%)= 25…40 | «Л» ПВ(%)= 16…25 | «Ло» ПВ<16% |
При оценке прочности элементов, на которые действуют нагрузки непостоянные по величине, в качестве рабочей принимают эквивалентную нагрузку, полагая, что эта нагрузка по воздействию равна реально действующей.
Эквивалентное число циклов нагружений определяется по формуле
NЕ=m×Nсå. (1.26)
Этот параметр используют для установления эквивалентности реальных режимов типовым, а также для определения коэффициента долговечности КL .
Коэффициент долговечности KL устанавливает соответствие между базовым N0 и эквивалентным числом циклов NE нагружений при заданном режиме, конкретном типе цикла напряжений и для определенного вида прочностного расчета
KL =(N0/NE)1/q. (1.27)
Методы учета нагрузок, изменяющихся во времени, регламентированы номативной документацией.
Величина нагрузок на элементы механизма может быть установлена по одному из нижеприведенных методов (ГОСТ 21354 – 87).
Метод эквивалентных циклов
Дата добавления: 2018-04-04; просмотров: 1395; Мы поможем в написании вашей работы! |
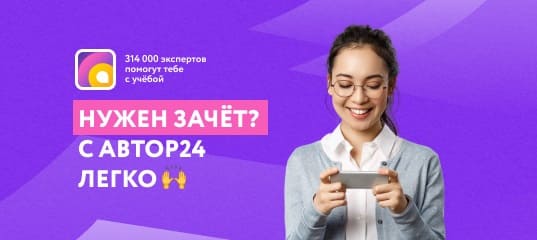
Мы поможем в написании ваших работ!