Контроль качества крупных заготовок,
Упрочняемых термической обработкой
Для облегчения выбора марки стали, введено понятие «Категория прочности» (КП), которое обозначает минимальный предел текучести материала после термообработки по типовому режиму. Деформирование металла увеличивает анизотропию механических свойств.
Поэтому важен правильный выбор технологии горячей пластической деформации и термической обработки. В связи с этим при индивидуальных сдаточных испытаниях крупных и ответственных заготовок (роторов, валов и дисков паровых турбин кованых обечаек для корпусов реакторов и парогенераторов АЕС, листовых заготовок для изготовления котлов и т. д.) проводят контроль равномерности свойств по сечению. Для крупных заготовок контролируют равномерность твердости (НВ) детали.
Контроль содержания ферритной фазы
В сталях аустенитного класса
Ферритная фаза (δ - феррит) образуется в процессе кристаллизации непосредственно из жидкого металла и имеет химический состав, существенно отличающийся от среднего состава стали. Например, содержание хрома в δ- феррите выше на 50 - 30 %, а содержание никеля на 20 - 50 % ниже среднего содержания этих элементов в стали. Также перераспределяются между δ - ферритом и аустенитом MO, TI, AL, SI, V, N, , обогащая δ – феррит на 10 – 20 % по сравнению со средним содержанием элемента в стали.
Увеличение содержания ферритной фазы до 10% и более снижает пластичность при нормальной температуре, может привести к охрупчиванию металла из – за сигматизации при высокотемпературной обработке, стабилизирующем отпуске и эксплуатации при температурах, когда проявляется явление ползучести. При содержании ферритной фазы ниже 1 – 2 % стали аустенитного класса становятся склонными к образованию горячих кристализационных трещин при сварке. В связи с этим при изготовлении ответственного оборудования из этих сталей, работающего при повышенных температурах или подвергающегося сварке, регламентируют содержание ферритной фазы в направленном металле (2 - 8 % при работе до температуры 350 °С и 2 - 5 % при работе при температуре выше 350 °С). В основном металле содержание ферритной фазы регламентируется техническими условиями, требованиями чертежа и, как правило, определяется по требованию потребителя.
|
|
Для количественного определения ферритной фазы используют расчетный, металлографический, рентгенографический и магнитный методы. Наиболее достоверные данные о содержании ферритной фазы получают объемным магнитным методом.
Оценка работоспособности деталей
По изменению ударной вязкости
|
|
Значения ударной вязкости, полученные при испытании металла заготовок, не используются непосредственно в расчётах на прочность, однако позволяют косвенно судить о качестве металла, его работоспособности в процессе эксплуатации. Испытание на ударный изгиб даёт возможность определить пороги хладноломкости, синеломкости и красностойкости стали, оценивать склонность к отпускной хрупкости, работоспособность после механического старения, воздействия высоких температур, различных агрессивных сред и радиационного облучения, условия перехода вязкого разрушения в хрупкое.
Определение специфических
Характеристик заготовок
Надёжность и долговечность многих деталей энергетического и тяжёлого машиностроения зависят от сопротивления их коррозионному разрушению (общему и локальному), знакопеременным нагрузкам, радиационному облучению, воздействию высоких и низких температур.
Тенденция развития современного энергомашиностроения – получение рабочих температур, применение более «грязного» топлива, увеличение скоростей движения рабочих сред, мощностей и габаритов - способствует редкой интенсификации коррозионных процессов.
|
|
Определяют коррозионную агрессивность продуктов сгорания, температурную зависимость коррозии, прогнозируют скорость низкотемпературной коррозии металла, коррозионную стойкость и жаростойкость определяют в основном весовым методом. Параллельно используют метод непосредственного измерения глубины коррозии по уменьшению толщины образца или стенки трубы, измеряемой по металлу, включая изменённый подокисный слой. Оценивают также склонность к точечной коррозии (питтингу) и коррозии под напряжением.
Материалы, предназначенные для изделий атомной энергетики, испытывают на склонность к межкристаллитной коррозии.
Эрозия – постепенное послойное разрушение (изнашивание) поверхности металла под действием различных факторов, обусловленных механическим, химическим, электрическим, тепловым воздействием. Она возникает при трении поверхностей износа, кавитации, а также при воздействии на поверхность сильных потоков струй (жидкостных, газовых). Эрозионное разрушение является причиной выхода из строя многих деталей энергитического оборудования, ухудшения его технико–экономических показателей. На тепловых электростанциях эрозионное повреждение чаще всего происходит на лопатках последних ступеней паровых турбин, деталях топливного и золового тракта, проточной части питательных насосов, на уплотнительных поверхностях регулирующей и запорной арматуры. В гидравлических турбинах наименее эрозионно-стойкие детали – лопасти, в дизелях – гильзы цилиндра.
|
|
Интенсивность эрозионного разрушения образцов при испытаниях (струя жидкости, газа, жидкого металла и др..) оценивается изменением массы во времени.
При одновременном воздействии коррозийной среды и статических растягивающих напряжений у многих сталей и сплавов происходит коррозионное растрескивание - ускоренное образование коррозионных трещин, развивающихся в направлениях близких к перпендикулярным основным растягивающим напряжениям. При оценке склонности металла к коррозионному растрескиванию используют следующие основные критерии:
- при испытаниях по методу постоянной нагрузки - минимальное или среднее арифметическое время разрушения образца или условный предел длительной коррозионной прочности на заданной базе испытаний;
- при испытаниях по методу постоянной деформации минимальное или среднее арифметическое время до появления первой трещины или до полного разрушения образцов.
В качестве дополнительного критерия склонности к коррозионному растрескиванию используют коэффициенты:
- изменения предела прочности
Кδв =[(δв – бвк) ∕ δв] 100%
- изменения значительного сужения (или удлинения)
Кψ = [(ψ - ψк) ∕ ψ] 100%
Кδ =[(δ –бк) ∕ δ] 100%
где δв, ψ, δ, бвк, ψк, δк - среднее значение временного сопротивления, относительного сужения, относительного удлинения исходных образцов и прошедших испытание на коррозионное растрескивание.
Дата добавления: 2018-04-04; просмотров: 409; Мы поможем в написании вашей работы! |
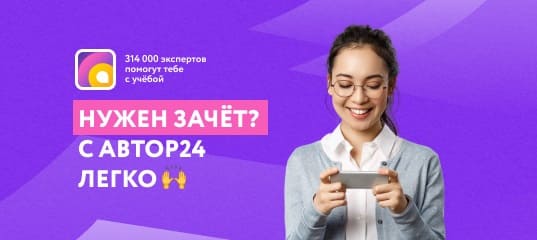
Мы поможем в написании ваших работ!