Контроль качества нанесения покрытия
Общие требования к покрытиям представлены в ГОСТ 9.301-86 «Покрытия металлические и неметаллические неорганические. Общие требования».Объектами контроля качества нанесённого покрытия являются:
— внешний вид;
— толщина покрытия;
— остаточные внутренние напряжения в покрытии;
— твёрдость и пористость покрытия;
— прочность сцепления покрытия с основой;
— шероховатость поверхности покрытия
и ряд других защитных и функциональных свойств, в частности, износостойкость, трибологические, коррозионно-защитные свойства.
Среди них отметим ряд требований к толщине качеству покрытий.
1). Превышение максимальной толщины покрытия не является браковочным признаком, если это не влияет на сборку и работоспособность изделия.
2). В отверстиях, пазах, вырезах, на вогнутых участках сложнопрофилированных деталей, на внутренних поверхностях и местах сопряжения неразъемных сборочных единиц допускается уменьшение толщины покрытия до 50 %, а для хромовых покрытий — отсутствие, если нет других требований в конструкторской документации к толщине покрытия на указанных участках.
3). В глухих гладких и резьбовых отверстиях и пазах диаметром (или шириной) до 12 мм и в сквозных гладких и резьбовых отверстиях и пазах диаметром (или шириной) до 6 мм толщина покрытия на глубине более одного диаметра (или одной ширины) не нормируется; допускается отсутствие покрытия, если в конструкторской документации не указаны требования к толщине покрытия на этих участках.
|
|
4). На поверхности покрытий, если нет специальных указаний в конструкторской документации, не являются браковочными следующие признаки:
— следы механической обработки и другие отклонения, допускаемые нормативно-технической документацией на основной металл; незначительная волнистость поверхности покрытия после вытяжки, выявляющаяся после травления;
— темные или светлые полосы или пятна в труднодоступных для зачистки отверстиях и пазах, на внутренних поверхностях и вогнутых участках деталей сложной конфигурации, местах сопряжения неразъемных сборочных единиц, в сварных, паяных швах, околошовной зоне и местах снятия плакировочного слоя; неравномерность блеска и неоднотонность цвета;
— неоднотонность цвета покрытий на деталях из плакированных металлов с частичной механической обработкой;
— следы от потеков воды, хроматирующих и фосфатирующих растворов без остатков солей;
— блестящие точки и штрихи, образовавшиеся от соприкосновения с измерительным инструментом, приспособлениями и от соударения деталей в процессе нанесения покрытий в барабанах, колоколах и сетчатых приспособлениях;
|
|
— изменение интенсивности цвета или потемнение после нагрева с целью обезводороживания и проверки прочности сцепления, снятия изоляции и пропитки;
— единичные черные точки на участках, предназначенных под заливку компаундами, герметиками, клеями;
5). Допускается отсутствие покрытия:
— в порах, местах включений, допускаемых нормативно-технической документацией на литье; на сварных и паяных швах и около них на расстоянии не более 2 мм по одну и другую сторону от шва и во внутренних углах взаимно перпендикулярных плоскостей при условии последующей дополнительной защиты этих мест;
— в местах контакта детали с приспособлением, кроме особых случаев, оговоренных в конструкторской документации.
Нормы контроля гальванических покрытий установлены ГОСТ 9.302-88 «Покрытия металлические и неметаллические неорганические. Методы контроля».
Контрольвнешнего вида покрытия. Требования, предъявляемые к внешнему виду покрытий, обычно определяются соответствующими техническими условиями к изделию. Внешний вид покрытия обычно оценивается осмотром невооружённым глазом. При осмотре выявляются непокрытые места на отдельных участках поверхности, наличие губчатых отложений, пригаров, трещин, тёмных чёрных полос и пятен.
|
|
Методы определения толщины гальванических покрытий. Для определения толщины покрытия применяют физические неразрушающие и разрушающие методы и химические методы. Последние во всех вариантах являются разрушающими.
В зависимости от используемого метода в качестве результата получают данные о средней или местной толщине покрытия. Перед определением толщины покрытия (это относится и к контролю пористости, защитных и функциональных свойств покрытий) испытуемую деталь выдерживают для выравнивания её температуры с температурой помещения, в котором проводят контроль, и тщательно обезжиривают этиловым спиртом или пастой из окиси магния, промывают дистиллированной водой и сушат фильтровальной бумагой.
К физическим неразрушающим методам относят магнитные и радиационные методы, весовой метод, оптический метод и метод вихревых токов. Практическое применение получили в основном магнитные методы. Эти методы применяют при условии, что значение шероховатости поверхности Raосновного металла и покрытия меньше толщины покрытия. Наиболее простым среди магнитных методов является магнитоотрывной метод. Действие этого метода основано на изменении зависящей от толщины покрытия силы отрыва магнита или электромагнита от ферромагнитной основы.
|
|
К разрушающим физическим методам контроля толщины покрытия относят гравиметрический, аналитический, профилометрический, металлографический и кулонометрический методы. Гравиметрический метод основан на взвешивании заготовки на аналитических весах до и после нанесения покрытия либо до и после растворения покрытия или основного материала в соответствующем растворе. Погрешность измерения этим методом находится в пределах ± 10 %. Аналитический метод предусматривает определение толщины покрытия по массе растворённого металла, которую могут определить химическим анализом раствора.
Металлографический метод. Метод основан на определении толщины покрытия на поперечном шлифе при 500…1000-кратном увеличении с помощью металлографического микроскопа при толщине покрытия менее 20 мкм и 100…200-кратном увеличении для покрытий толщиной более 20 мкм. Этот метод достаточно трудоёмок и используется при арбитражах и структурных исследованиях покрытий.
Химические методы определения толщины покрытия. К методам данной группы относят методы струи, капли и снятия покрытия.
Метод струи основан на растворении покрытия раствором, вытекающим на поверхность заготовки в виде струи. Расчёт толщины покрытия производят по времени, затраченному на снятие покрытия или по объёму раствора, израсходованному на растворение покрытия. Окончание растворения покрытия устанавливают визуально или с помощью прибора, регистрирующего изменение потенциала или тока в момент полного растворения покрытия.
Метод капли основан на растворении покрытия каплями раствора, наносимыми на поверхность и выдерживаемыми на покрытии в течение определённого промежутка времени. Расчёт толщины покрытия производят по числу капель, затрачиваемых на растворение покрытия. Методы струи и капли дают погрешность измерения толщины ± (15-30) %.
Пористость гальванических покрытий, как правило, контролируется периодически для оценки качества подготовки и точности режима процесса электроосаждения. Для определения пористости применяют метод паст и метод наложения фильтровальной бумаги.
Метод паст основан на химическом взаимодействии основного металла в местах пор и других несплошностей покрытий с веществами, входящими в состав пасты. В результате такого взаимодействия образуются окрашенные соединения, по которым и выявляются поры. Метод применим для определения пористости металлических покрытий на стали, алюминии, цинке, меди и их сплавах, а также нахождения степени пористости неорганических покрытий на алюминии и его сплавах.
Метод наложения фильтровальной бумаги основан на том же принципе взаимодействия основного металла и веществ фильтровальной бумаги, пропитанной специальными растворами. После снятия бумаги с отпечатками пор её просушивают и определяют число пор, приходящихся на единицу площади поверхности, на каждом участке покрытия. Метод может быть применён для определения пористости катодных покрытий на стали, меди и медных сплавах.
Определение прочности сцепления покрытия с основным металлом. Методы контроля этой группы основаны на различии физико-механических свойств покрытия и основного металла. В данной группе методов контроля используют как качественные, так и количественные методы. К качественным методам относят методы полирования, крацевания, нанесения сетки царапин, изгиба, нагрева, метод навивки (для контроля покрытий на проволоке). В группе количественных методов выделяют методы опиловки, отрыва полоски и некоторые другие. Количественные методы требуют изготовления образцов, применения специального оборудования и оснастки.
При контроле методом полирования заготовку с покрытием полируют в течение 15…60 секунд с помощью хромовой, крокусной или другой пасты при окружной скорости круга 20…30 м/с. Прочность сцепления считается достаточной, если на поверхности покрытия не образуется вздутий и не происходит отслаивание покрытия. Используют данный метод при толщине покрытия до 30 мкм.
Метод крацевания характеризуется тем, что покрытие толщиной до 20 мкм обрабатывают в течение 15…60 секунд с помощью стальных или латунных щёток при определённом режиме обработки. Отсутствие вздутий на поверхности или отслаивания свидетельствует о достаточной прочности сцепления.
Для контроля прочности сцепления покрытия с основным металлом методом нанесения сетки царапин на поверхности покрытия стальным остриём наносят четыре – шесть параллельных линий глубиной до основного металла и столько же линий, перпендикулярно им. При этом не должно происходить отслаивания покрытия.
Для испытания прочности покрытий на листовых материалах используют метод изгиба. Заготовку при испытании изгибают под углом 90ов обе стороны до излома. В месте излома не должно наблюдаться отслаивание покрытия.
Метод нагрева. Для контроля прочности сцепления заготовку нагревают в течение 30…60 минут и охлаждают на воздухе. После этого на поверхности заготовки не должно наблюдаться вздутия или отслаивания покрытия. Температуру нагрева выбирают в зависимости от марки основного металла в границах от 120 оС (для магния и его сплавов) до 355 оС (для сталей и чугунов).
Оценку прочности сцепления основы с покрытием разрушающим методом контроля выполняют методом опиловки. Его используют для покрытий толщиной более 5 мкм. Контроль проводят на образцах, вырезанных из детали, перпендикулярно к поверхности покрытия. Образец зажимают в тисках и опиливают по срезу напильником с мелкой насечкой. Опиловку производят в направлении от основного металла к покрытию под углом 45о. После контроля не должно быть отслаивания покрытия.
При проверке прочности сцепления покрытия с основой применяют и другие методы контроля, например, метод отрыва покрытия от поверхности заготовки. В основу этого метода положено измерение силы отрыва покрытия 2, нанесённого на торец цилиндрического образца 1 (рис. 4.10,а).
Рис. 4.10. Этапы контроля прочности сцепления покрытия с основой методом отрыва покрытия
Образец с нанесённым покрытием подвергается механической обработке для создания площадки сцепления, определяемой наружным D и внутренним d диаметрами (рис. 4.10, б). С помощью механического устройства или гидравлического пресса создаётся постепенно возрастающее усилие на внутреннюю поверхность покрытия, параллельно оси образца. При достижении усилием значения Р происходит отрыв покрытия от основы (рис. 4.10, в). Прочность сцепления s (Па) покрытия с основой рассчитывают по формуле
s = Р/S = , (4.5)
где Р — усилие отрыва, Н; S — площадь поверхности отрыва покрытия от основного металла, м2.
Контроль покрытия на наличие внутренних напряжений. В соответствии с ГОСТ 9.302-88 в основе метода определения внутренних напряжений в металлических электрохимических покрытиях лежит изменение длины образца при осаждении покрытия и вычисление на основе полученных данных внутренних напряжений первого рода.
Контроль проводят в электролитических ваннах на плоских образцах размером (250 ´ 110 ´ 0,5‑0,1) мм или на проволочных образцах (при контроле покрытия пружин). Перед испытанием образец обезжиривают, активируют его поверхность в растворе серной кислоты и промывают в проточной воде. К образцу прикладывают растягивающее усилие, соответствующее напряжению 4...10 МПа, и защищают покрытием органического стекла все поверхности, не подлежащие покрытию.
Подготовленный таким образом образец погружают в электролит и включают электрический ток. Нанесение покрытия производится с двух сторон образца. В процессе нанесения покрытия в связи с возникновением внутренних напряжений образец изменяет свою длину. Если заранее известна скорость осаждения покрытия, то изменение длины образца отсчитывают после достижения заданных толщин покрытия, например, 2, 3, 5, 10 мкм и т. д. Если скорость осаждения покрытия неизвестна, то изменение длины образца отсчитывают в зависимости от продолжительности осаждения покрытия через определённые промежутки времени. Затем по полученным данным определяют скорость осаждения покрытия по средней толщине покрытия или по разнице массы образца до и после покрытия. После этого строят график зависимости изменения длины образца от продолжительности процесса, проводят его математическую обработку и на основе полученной зависимости определяют внутренние напряжения sвнв МПа для плоского образца по формуле
, (4.6)
где Ео — модуль упругости при растяжении металла образца, МПа; Ер — модуль упругости при растяжении материала покрытия, МПа; b— толщина образца, мм; h — толщина покрытия, мм; lо — длина покрывающейся части образца, мм; Dl — укорочение или удлинение образца при заданной толщине покрытия, мм; m— коэффициент Пуассона.
Если при осаждении покрытия образец укорачивается, то в покрытии возникают напряжения растяжения. Если образец удлиняется, в покрытии возникают напряжения сжатия. Соответственно этому результаты по формулам обозначают знаком «+» или «‑».
Для измерения внутренних напряжений применяют и другие методы, в основе которых лежат измерения величины деформации катода — образца, возникающей в процессе нанесения на него покрытия. Наиболее широкое распространение получил метод изгиба тонкого плоского катода. При реализации этого метода одну сторону катода — образца изолируют непроводящим химически стойким лаком. Металл осаждают на вторую сторону катода, что приводит к деформации — изгибу пластины под действием внутренних напряжений.
Измерения производят в электрохимической ячейке. У торцовых стенок ячейки размещают анод и катод в виде пластинок толщиной 0,1…0,3 мм, перекрывающих всё сечение электролита, чтобы обеспечить равномерное распределение тока. Верхний конец катода (вне электролита) жёстко закрепляется в неподвижном контактном устройстве. Нижний конец катода может перемещаться.
При электролизе ведут наблюдение за смещением конца катода с помощью измерительного микроскопа. Величину внутренних напряжений определяют по формуле
, (4.7)
где sвн — внутреннее напряжение в покрытии, МПа; Е — модуль упругости металла катода, МПа; b1 — толщина катода, мм; b2 — толщина покрытия, мм; l — длина рабочей части катода, мм; Dl — смещение конца катода, мм.
Измерение деформации катода может производиться также с помощью проволочных тензодатчиков, наклеиваемых на нерабочую сторону катода. Деформация катода, возникающая под влиянием внутренних напряжений осаждаемого при электролизе покрытия, изменяет электрическое сопротивление тензодатчиков. Эти изменения регистрируются с помощью электрических мостов тензометрических схем. Показания приборов затем пересчитывают на величину внутренних напряжений.
Обозначения покрытий
Покрытия на чертежах обозначают с помощью ряда символов в соответствии с ГОСТ 9306–85 «Покрытия металлические и неметаллические неорганические. Обозначения». Эти символы отражают структуру итехнологию получения покрытия. В них указывают следующие данные:
— способ обработки материала основы;
— способ получения основного покрытия;
— материал основного покрытия и отдельных слоёв для многослойных покрытий;
— минимальную толщину покрытия (толщину покрытия менее 1 мкм без особой необходимости не указывают);
— электролит, из которого получают покрытие;
— функциональные и декоративные свойства покрытия;
— вид дополнительной обработки покрытия.
Перечень характеристик, указываемых в обозначении покрытия, может варьироваться в зависимости от типа и назначения покрытия.
Например, покрытие кадмием толщиной 3 мкм с подслоем никеля толщиной 9 мкм и последующей термообработкой и хроматированием химическим методом нанесения покрытий обозначают следующим образом: Н9. КдЗ. т. хр.
Примеры обозначений наиболее распространённых гальванических покрытий и области их рационального применения приведены в таблице 4.5.
Таблица 4.5
Примеры некоторых химических и гальванических покрытий и области их применения
Вид покрытия и примеры обозначения | Характеристика покрытия | Примеры применения |
Хим. Окс. прм | Химическое окисное с промасливанием (чёрное, блестящее) | Стальные детали, работающие в масле, или в условиях сухой атмосферы. Покрытие декоративное, имеет невысокие защитные свойства. |
Ан. Окс. хром | Анодно-окисное с хроматированием (обработкой хромовым ангидридом) | Детали из алюминиевых сплавов. Покрытие обладает защитными и декоративными свойствами. |
Хмол15 | Хромовое, молочное, толщиной 15 мкм | Поверхности деталей, работающих на трение. |
Х6.тв | Хромовое, толщиной 6 мкм, твёрдое | Покрытие имеет декоративные свойства. |
Хим. Фос. прм | Химическое фосфатное с пропиткой маслом (чёрное) | Стальные детали, подлежащие окраске, заготовки перед волочением, накатыванием резьбы (для снижения трения), работающие в масле. |
М24.Нд15.Х6.б | Трёхслойное: медь 24 мкм, никель двухслойный 15 мкм, хром 6мкм, блестящее | Стальные детали, работающие в агрессивной атмосфере, покрытие имеет высокие декоративные свойства. |
Н12.б | Никелевое, толщиной 12 мкм, блестящее | Слесарно-монтажный инструмент. |
Кд21.хр | Кадмиевое, толщиной 21 мкм, с хроматированием (толщина слоя менее 1 мкм) | Стальные детали, работающие в условиях влажной атмосферы, тропического климата. |
О15 | Оловянное, толщиной 15 мкм | Стальные тонкие листы для консервной тары (белая жесть), детали подвергаемые пайке. |
М6 | Медное, толщиной 6 мкм | Детали, подвергаемые пайке. В основном, покрытие медью используется в качестве подслоя при покрытии никелем, хромом. |
М6.О3 | Оловянное с подслоем меди | Детали, подвергаемые пайке. |
Ц12.хр | Цинковое толщиной 12 мкм с хроматированием | Детали машин, работающие в сухих условиях (пружины, метизы); стальные листы (оцинкованное железо) для использования в атмосферных условиях умеренного климата. |
Дата добавления: 2018-04-04; просмотров: 3966; Мы поможем в написании вашей работы! |
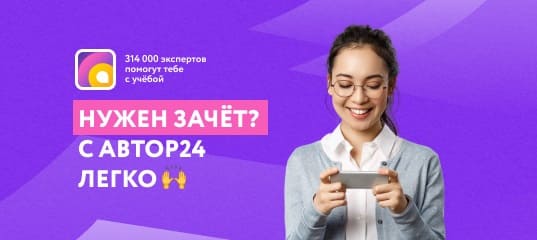
Мы поможем в написании ваших работ!