Система операций подготовки поверхности к нанесению покрытия
Лекция 6
Этапы технологического процесса нанесения покрытия электрохимическим методом
Нанесение покрытия — это сложный технологический процесс, включающий четыре этапа, состоящих в свою очередь из ряда операций. К этапам нанесения покрытия относят: подготовку поверхности к нанесению покрытия, непосредственное нанесение покрытия, дополнительную обработку нанесённого покрытия и его контроль.
Подготовка поверхности к нанесению покрытия
От качества подготовки поверхности к покрытию зависит важнейшее его свойство — адгезионная сцепляемость покрытия с основой. Плохая подготовка поверхности к покрытию в процессе эксплуатации изделия часто приводит к отслоению покрытия от основы.
Подготовка изделия к покрытию заключается в создании на покрываемой поверхности определённой шероховатости, удалении имеющихся на ней загрязнений и активации поверхности.
Шероховатость поверхности под покрытие. Для повышения сцепляемости покрытия с поверхностью заготовки и уменьшения последующей трудоёмкости его обработки необходимо на поверхности заготовки в соответствии с ГОСТ 9.301-86 «Покрытия металлические и неметаллические неорганические. Общие требования» иметь шероховатость по параметру Rа:под защитные покрытия не более 40 мкм, под защитно-декоративные — не более 2,5 мкм, под твердые и электроизоляционные анодно-окисные покрытия — не более 1,25 мкм.Шероховатость поверхности основного металла под функциональные покрытия должнасоответствовать установленной в нормативно-технической и (или) конструкторской документации на изделие.
|
|
Указанныетребованиякшероховатостиповерхностинераспространяютсянанерабочиетруднодоступныедляобработкиинерабочиевнутренниеповерхностидеталей, резьбовыеповерхности, поверхностисрезаштампованныхдеталейтолщинойдо4 мм, рифленыеповерхности, атакженадетали, шероховатостьосновногометаллакоторыхустановленасоответствующимистандартами.
Необходимостьдоведенияшероховатостиповерхностейдоустановленныхзначенийдолжнабытьоговоренавконструкторскойдокументации.
Загрязнения и методы очистки поверхности. К основным видам загрязнений, которые могут быть на поверхности заготовки, относят:
— механические загрязнения, то есть загрязнения, которые химически не связаны с материалом изделия, а просто пристали к поверхности. Такими загрязнениями являются пыль, ветошь, абразивные зерна;
— оксидные плёнки, которые подлежат удалению, так как препятствуют химическому взаимодействию покрытия и материала основы;
— органические загрязнения в виде масла, смазки, воска. Этот вид загрязнений относят к основным, поскольку органические загрязнения приводят к ухудшению адгезионного сцепления покрытия с основой;
|
|
— адсорбированные газы, которыми являются осевшие на поверхность заготовки молекулы газов воздуха, главным образом, азота и кислорода;
— растворы солей, к которым относятся легко растворимые в воде соли различных металлов. Эти соли легко удаляются промыванием.
Поскольку различные виды загрязнений удаляются различными способами, то полная подготовка поверхности под покрытие включает ряд последовательных технологических операций. К методам очистки загрязнений поверхности относят: методы механической обработки, термическую обработку, обезжиривание и травление. В некоторых случаях для подготовки поверхности к нанесению покрытия достаточно лишь одного метода удаления загрязнений, в других же случаях применяют несколько методов, выстраиваемых в строго определённой последовательности. В зависимости от объёма загрязнения отдельные этапы очистки могут повторяться несколько раз. Например, стальные болты, которые хранились в смазочных материалах, могут проходить неоднократное обезжиривание.
|
|
Способы механической очистки поверхности. Механическая обработка поверхности применяется для очистки металла от окалины, ржавчины, оксидных плёнок, литейной корки, старого лакокрасочного материала. Чаще всего этот метод применяется для очистки крупногабаритных изделий и объектов средних размеров с поперечным сечением, обеспечивающим детали высокие прочностные характеристики. При механической очистке загрязнения часто удаляются вместе с верхним слоем металла.
Подготовка поверхности механическими методами может осуществляться абразивной обработкой (пескоструйная, гидропескоструйная, дробеструйная и другие виды абразивной обработки), шлифованием, полированием, крацеванием.
Абразивная очистка поверхности. Осуществляется этот способ обработки в специальных аппаратах барабанного или камерного типов. Рабочие барабаны (камеры) изготавливают из чугуна или сплавов высокой твёрдости. В качестве абразивного материала используют кварцевый песок, корунды, стальную или чугунную дробь, которую часто называют «металлическим песком», и ряд других абразивных материалов.
Под высоким давлением сжатый воздух (либо жидкость) с абразивным материалом выдувается из сопла, направленного на обрабатываемую поверхность. Частички абразива, ударяясь о металл, очищают его. Обработанная таким методом поверхность металла характеризуется чистотой и равномерной шероховатостью.
|
|
Пескоструйная обработка— способ абразивной подготовки поверхности, применимый практически для всех видов покрытий, которые не требуют полированной поверхности. Пескоструйная обработка с использованием сухого кварцевого песка сейчас уже не популярна, так как отличается большой вредностью для оператора, который её проводит. Вместо обычной пескоструйной обработки в настоящее время широко используется обработка стальной или чугунной дробью, абразивными порошками, применяется также гидропескоструйная очистка.
Обработка стальной или чугунной дробью (металлическим песком) получила очень широкое распространение, так как является одним из самых эффективных методов очистки поверхностей заготовок. «Металлический песок» в отличие от кварцевого песка почти не образует пыли. Расход его значительно меньше, а эффективность механического воздействия достаточно высока. После очистки поверхность деталей становится матовой, покрытой большим количеством кратеров, способствующих прочному сцеплению покрытия с основным металлом.
Для реализации этого метода используется стальная или чугунная дробь с размером частиц от 0,15 до 1,5 мм. «Металлическим песком» обрабатывают практически все металлы (кроме алюминия и его сплавов). Размер частиц и силу потока воздуха, выдуваемого металлическую дробь из сопла, устанавливают в зависимости от толщины стенки металлического изделия.
Металлическая дробь должна изготовляться из того же материала, что и очищаемая поверхность; возможно использование и других материалов с электрохимическими характеристиками, близкими к характеристикам обрабатываемой поверхности. При выполнении этого требования исключается развитие подплёночной коррозии, причиной которой могут быть частицы дроби, оставшиеся на окрашенной поверхности после очистки.
Шлифование — это способ подготовки поверхности перед нанесением защитного покрытия, для реализации которого используются абразивные ленты, бруски и вращающиеся шлифовальные круги.
Шлифование проводят для придания металлу блеска, а также для удаления неровностей. Черновым шлифованием можно удалить с поверхности толстый слой окалины, наплывы металла, заусенцы, бугры, раковины. Реализуются этот способ на специальных станках либо вручную при помощи наждачной бумаги.
Абразивом служат крупные фракции электрокорунда (Al2O3), карбида кремния (карборунда SiC), наждака (30…35 % Fe2O3 и 60…70 % Al2O3). Размер зерна находится в диапазоне 250…1200 мкм.
Декоративное (тонкое)шлифованиепроводится специальными эластичными кругами, которые состоят из основы (эластичной части круга) и абразивного материала. В качестве абразива используют мелкие фракции кварца, корунда, наждака. Их наносят на основу при помощи связующих веществ (жидкого стекла, клеев). Основу изготавливают из брезента, кожи, войлока, хлопчатобумажной ткани, фетра и других материалов, которые дальше прессуют, склеивают и прошивают. Эластичный круг зачастую состоит из нескольких слоёв неметаллического материала. Зерно абразивного материала для декоративного шлифования при подготовке поверхности к покрытию по размерам не превышает 75…200 мкм.
Крацевание. Крацеванием называют механическую обработку поверхности изделий металлическими щётками. Этим способом хорошо удаляется с поверхности заготовки разрыхлённая окалина и шлам. Процесс крацевания применяют также для улучшения качества покрытий большой толщины.
Щётки для крацевания состоят из деревянной или металлической втулки, в которую воткнуто несколько рядов подвижных пучков проволоки. Их различают по типам, размерам и материалам рабочей (ворсовой) части. Основными показателями качества щётки являются материал и диаметр ворсинок, свободная длина ворса, плотность рабочей части, ширина и диаметр щётки. Щётки изготавливают из тонкой латунной, стальной или медной проволоки диаметром 0,05…0,10 мм для чистовой обработки и 0,3…0,6 мм — для черновой обработки. При обработке поверхностей под нанесение мягких гальванических покрытий используют волосяные, капроновые или травяные щётки.
Крацевание обычно выполняют на станках или с помощью ручного пневматического или электрического инструмента. Щётки насаживаются на шпиндель станка или используемого для этого ручного электроинструмента. При работе им придаётся вращательное движение. Иногда крацевание производят ручными щётками.
Окружная скорость щёток находится в пределах от 10 до 60 м/с. При обработке металлов мягкими щётками с неметаллическим ворсом окружная скорость вращения щёток принимается в пределах 30…40 м/с; при обработке металлов тонкими проволочными щётками с металлическим ворсом — 20…35 м/с; при очистке поверхности от окалины, ржавчины и других дефектов широкими проволочными щётками с диаметром ворса более 0,4 мм — 15…25 м/с; при зачистке сварных швов, литья с применением тонких дисковых щёток с ворсом, сплетённым в жгут, — 30…45 м/с.
В процессе крацевания вращающиеся щётки должны касаться заготовки только кончиками проволоки, так как сильный прижим щётки к заготовке увеличивает съём металла и изгибает проволоку.
Крацевание жёсткими щетками позволяет получить матовую поверхность изделия, а при обработке мягкими щётками формируется блестящая или полублестящая поверхность. Матовая поверхность характеризуется неровностями с размерами, сравнимыми с длинной волны видимого излучения, вследствие чего происходит хаотичное (диффузное) рассеивание света. Это приводит к тусклому цвету поверхности и выравниванию слабого блеска по всем направлениям. Процесс получения поверхностей таких свойств получил название матирования.
Крацевание является эффективным способом предупреждения выпуска недоброкачественной продукции. Если гальваническое покрытие имеет невидимые пузыри или непрочно сцеплено с основным металлом или промежуточным подслоем, то под действием проволочной щётки происходит отслаивание такого покрытия. Скрытый дефект, таким образом, сразу выявляется.
Матирование поверхности заготовки осуществляют кроме обработки металлическими щётками и другими способами, в том числе травлением и дробеструйной обработкой. Целью матирования при подготовке поверхности к нанесению покрытия является создание формы и размеров шероховатости поверхности, обеспечивающих прочное сцепление покрытия с основой.
Если поверхность ровная, то для матирования используют простой круг с маленьким ворсом или без него. Изделия, которые имеют сложную форму, матируют с помощью специальных кругов, которые изготавливают из полимерных материалов (нейлона, капрона) или морской травы (сизаль, фибер). Для матирования металлов могут быть использованы пасты на основе парафина (стеарина), солидола и абразивного материала — маршаллита, кирпичной пыли, наждака.
Кроме шлифовальных кругов в качестве инструментов для матирования могут использоваться шлифовальные ленты. Ленты применяют в виде бесконечных ремней с нанесённым абразивным материалом. Применяют также тканевые ленты, склеенные между собой полосы шлифовальной шкурки на бумажной или матерчатой основе.
Обезжиривание поверхности. Обезжиривание выполняют химическими, электрохимическими, ультразвуковыми и термическими методами.
Химический способ удаления жиров основывается на взаимодействии с ними органических растворителей или растворов щелочей. Химическое обезжиривание, как правило, предшествует электрохимическому обезжириванию. В основном его применяют при наличии на заготовке толстой жировой плёнки.
Обезжиривание в органических растворителях применяется для очистки поверхности заготовки от минеральных масел, полировальных паст, остатков консервационной смазки. Органические обезжириватели токсичны, использовать их можно только при наличии специального оборудования и при строгом соблюдении правил техники безопасности. Пожароопасные растворители (бензин, керосин, бензол, толуол, ксилол, уайт-спирит) применяют крайне редко. Их заменяют негорючими хлорированными углеводородами: трихлорэтиленом, тетрахлорэтиленом, четырёххлористым водородом, фреоном.
Наиболее универсальными обезжиривающими веществами являются фторосодержащие углеводороды, например, фреон Ф-113. Обезжиривание этими растворителями проводят на оборудовании, исключающем попадание паров фреона в атмосферу.
Обезжиривание органическими растворителями осуществляют погружением, протиркой, струйным методом и обрызгиванием заготовок. При обработке методом погружения заготовки обезжиривают последовательно в двух — трёх ваннах.
После обезжиривания в органических растворителях на поверхности заготовки всё же остается очень тонкая плёнка жиров, которая требует удаления в других растворах или удаления электрохимическим методом.
Очистку поверхностей заготовок от жиров органического и животного происхождения осуществляют в растворах щелочей. Жиры животного и растительного происхождения являются омыляемыми, так как, вступая во взаимодействие со щелочными растворами, образуют растворимые в воде мыла. Например, реакция взаимодействия стеарина с гидроксидом натрия
(C17H35COOO)C3H5 + 3NaOH = 3C17H35COOONa + C3H5(OH)3
приводит к образованию растворимой натриевой соли стеариновой кислоты, которая образует с водой коллоидный раствор.
В целом химическое обезжиривание заключается в том, что под воздействием щёлочи жиры омыляются и переходят в раствор, а минеральные масла в присутствии специальных поверхностно-активных веществ — эмульгаторов — образуют эмульсию.
Растворы для химического обезжиривания обычно содержат щёлочи, фосфаты, силикаты, мыла, различные синтетические моющие вещества — поверхностно-активные вещества, эмульгаторы — органические соединения, кальцинированную соду.
Химическое обезжиривание производят при температуре 70…90 оС, при которой омыление и процесс эмульгирования протекают более интенсивно. Продолжительность обезжиривания зависит от степени загрязнённости заготовок и составляет примерно от 3-х до 20-и минут. Увеличение температуры и перемешивание раствора ускоряют удаление масла с поверхности.
Электрохимическое обезжиривание является эффективным способом очистки поверхности и применяется главным образом для удаления тонких жировых плёнок, которые остаются после других видов обезжиривания и которые трудно удалить другими способами.
При электрохимическом обезжиривании используют те же растворы, что и при химическом обезжиривании, но концентрации веществ берутся меньшими.
Электрохимическое обезжиривание в щелочных растворах проводится при помощи постоянного, а иногда и переменного тока. При постоянном токе обезжиривание осуществляется и на катоде, и на аноде. В процессе электролиза на поверхности заготовки наблюдается интенсивное выделение пузырьков газа, облегчающих отрыв капелек масла от поверхности, чем значительно ускоряется обезжиривание.
Скорость обезжиривания заготовок на аноде меньше, чем на катоде. Это объясняется тем, что в прианодном пространстве не происходит защелачивание электролита, вследствие чего процесс омыления растительных и животных жиров у анода происходит медленнее. Кроме того, объём выделяющегося при электролизе кислорода меньше объёма водорода, а пузырьки кислорода больше пузырьков водорода и задерживают на поверхности меньше капелек масла. Поэтому удаление масла с поверхности заготовки происходит менее интенсивно. Однако процесс катодного обезжиривания сопровождается наводороживанием стальных заготовок, вследствие чего при продолжительном обезжиривании на катоде закалённые или тонкостенные стальные заготовки могут становиться хрупкими. Поэтому катодное обезжиривание заготовок, которые должны обладать упругими свойствами, например, пружины, не допускается.
Недостатком химического обезжиривания является низкая рассеивающая способность применяемых электролитов, вследствие чего очистка сложнопрофильных заготовок затруднительна.
Ультразвуковая очистка заготовок. Качество обезжиривания заготовок и скорость очистки можно значительно повысить ультразвуковой обработкой. Обезжиривание заготовок с помощью ультразвука осуществляется в ванне с органическими растворителями или со слабощелочными растворами моющих средств.
Сущность метода ультразвуковой очистки заключается в следующем. При распространении ультразвуковой волны возникают области резко повышенного давления, чередующиеся с областями пониженного давления. При достаточной интенсивности колебаний в местах пониженного давления происходят разрывы жидкости, которые затем захлопываются при прохождении через пучность. При захлопывании разрывов в жидкости развиваются огромные силы. Это явление называется кавитацией. Огромные механические усилия, развивающиеся при прохождении кавитации, не только удаляют с поверхности жировые загрязнения, но и могут разрушить плёнки оксидов, например, удалять окалину со стальных заготовок. Таким образом, при ультразвуковой обработке поверхность заготовки не только обезжиривается, но и протравливается.
Частота ультразвуковых колебаний, при которых достигается наибольший эффект кавитации, составляет около 20 кГц. Для обработки сложных мелких заготовок, имеющих узкие зазоры или щели, частоту повышают до 200…500 кГц.
Химическое и электрохимическое травление.Эти виды травления поверхности заготовки применяются в основном для удаления ржавчины, окалины и других продуктов коррозии с поверхности многих металлов.
Химическим травлением называют удаление поверхностных слоёв заготовки в химически активных средах (травителях) в результате химических реакций. В промышленности травление получило широкое распространение при выполнении таких видов работ, как очистка поверхности заготовки от окалины (поверхностное травление), глубинное травление (в литературе встречается под названием «химическое фрезерование»), поверхностное травление рельефов на заготовках, химическое полирование.
Химическое поверхностное травление с целью очистки заготовок от окалины.При остывании отливок, поковок и проката, а также при термической и термомеханической обработке на поверхностях стальных заготовок образуется окалина, которая в дальнейшем должна быть удалена.
Внешний слой окалины состоит из высшего оксида железа Fe2О3 (гематита), толщина его не превышает 10 % общей толщины слоя окалины. Этот слой по всей поверхности контакта плотно связан со вторым слоем, представляющим собой оксид железа Fe3О4 (магнетит). Толщина магнетита может достигать 40 % общей толщины окалины. Третий, внутренний слой наиболее значительный. Он состоит из оксидов переменного химического состава, близких к FeO (вюститу). В отличие от первых двух слоёв слой вюстита пористый и рыхлый, имеет заметное на глаз мелкокристаллическое строение.
Химическое поверхностное травление окалины может осуществляться в кислых (кислотное травление), в щелочных (щелочное травление) и в щёлочно-кислотных (щёлочно-кислотное травление) средах.
Кислотное травлениеокалины производят в водных растворах серной, соляной, азотной кислот с добавлением некоторых солей. При травлении оксидный слой вступает в химические реакции с кислотами, в результате которых происходят его растворение и последующее растравливание поверхностного слоя основного металла.
При взаимодействии окисленного железа с разбавленными кислотами могут протекать различные реакции. Так, при взаимодействии с соляной кислотой идёт следующая группа реакций:
FeO + 2HCl = FeCl2 + H2O;
Fe2O3 + 6HCl = 2FeCl3 + 3H2O;
Fe3O4 + 8HCl = 2FeCl3 + FeCl2 + 4H2O;
2FeCl3 + H2 = 2FeCl2 + 2HCl;
2FeCl3 + Fe = 3FeCl2;
Fe + 2HCl = FeCl2 + H2.
Скорость удаления оксидных плёнок невысока и зависит от физико-химических свойств слоя оксидов, его плотности, пористости, толщины, химического состава, свойств продуктов взаимодействия и характеристик травящего раствора.
Наряду с растворением оксидов при травлении заготовки в кислой среде протекают растравливание основного металла и его наводораживание, для уменьшения чего в раствор кислот вводят ингибиторы — вещества, замедляющие или прекращающие происходящие при растравливании химические реакции (например, для сталей — азотнокислый натрий NaNO3). В процессе травления металла кислотность растворов уменьшается. В растворе накапливаются соли Fe, Cr, Ni и других элементов. В результате этого плотность раствора растёт, а его химическая активность снижается.
Кислотное травление имеет ряд недостатков, в том числе низкую скорость растворения оксидов, большие потери травимого металла в связи с сопутствующим растворением основного металла, его наводораживание, значительное испарение электролита с образованием в цехе «кислотного тумана», низкое качество очистки высоколегированных сталей и сплавов на основе титана и никеля.
Щелочное травление.Недостатки кислотного травления в значительной мере устраняются, если травление осуществлять в расплавах на основе щелочей. В щелочной среде удаление окалины происходит не на основе её растворения, а путём восстановления оксидов железа и легирующих элементов.
В качестве щёлочи наиболее часто применяют NaOH. При травлении стальных изделий оксиды железа реагируют с NaOH с восстановлением окалины до металлического состояния или с образованием легко растворимых в кислотных растворах ферритов и ферратов. Очистка от окалины в расплавах щелочей даёт значительный эффект при обработке высоколегированных и коррозионностойких сталей. В этом случае полностью исключено какое-либо воздействие расплава на очищенную поверхность металла, что, в свою очередь, предотвращает потери металла при одновременном увеличении производительности процесса и улучшении качества очистки.
При работе с расплавленными щелочами необходимо строго соблюдать правила техники безопасности. При загрузке щёлочи на рабочих должны быть надеты специальная одежда, сапоги и резиновые перчатки; для защиты глаз следует пользоваться специальными очками. Особую опасностьпредставляет попадание в расплав щёлочи воды, так как это приводит к взрыву расплава. Поэтому очищаемый материал нужно предварительно прогревать, а ванна должна быть всегда закрыта.
Щёлочно-кислотный метод используют преимущественно для удаления окалины с поверхности коррозионно-стойких, кислотоупорных, жаростойких, жаропрочных сталей, а также сплавов на основе никеля и титана. Сущность метода состоит в травлении заготовок в смеси расплава NaOH с окислителями (например, NaNО3, Na2CrО4, Na2B4О7) при температуре 400…600 оС. Окалина при этом частично отслаивается от стальной поверхности и оседает на дно ванны в виде шлама, а оставшаяся её часть «срывается» водяным паром, образующимся при следующем после травления погружении горячих заготовок в холодную воду. Остатки оксидного слоя легко удаляются в растворе кислоты.
Электрохимическое травление — травление поверхностей заготовки в электролите с пропусканием через электролит электрического тока. Этот вид очистки поверхности чаще всего применяют для анодного либо катодного травления углеродистых и легированных сталей. Электрохимическое травление может проводиться в растворах солей железа или щелочных металлов, соляной, серной кислотах и их смесях.
При анодном травлении удаление с поверхности заготовки оксидов происходит вследствие электрохимического растворения анода и механического отрыва оксидов пузырьками выделяющегося водорода. В качестве анода используется обрабатываемое изделие, а катод изготавливают из свинца. В результате анодного травления заготовка получает совершенно чистую от оксидов и слегка шероховатую поверхность, что способствует хорошему сцеплению нанесённого на эту поверхность покрытия с основным металлом. Анодное травление применяется при очистке заготовок простой формы.
Сначала при анодном травлении происходит удаление оксидной плёнки, а затем идёт образование на поверхности заготовки пассивной плёнки. При этом преобладает электрохимический процесс окисления ионов ОН- и выделения газообразного кислорода:
4OH‑ = 2H2O + O2 + 4e-.
При катодном травлении, когда обрабатываемое изделие становится катодом, на его поверхности происходит восстановление ионов водорода:
Н+ + е- = Н; Н + Н ® Н2.
Выделяющиеся пузырьки водорода разрыхляют плёнку оксидов и отрывают её от поверхности заготовки. Электролитом при катодном травлении служат растворы кислот или солей, обладающие хорошей электропроводностью. Аноды при катодном травлении изготавливают из свинца или кремнистого чугуна.
Катодное травление применяется главным образом для заготовок из углеродистой стали, подвергнутых термообработке и закалке в масле. Никелевые и хромовые заготовки плохо поддаются катодному травлению. При катодном травлении не происходит перетравливания поверхности.
Активирование поверхности.Поверхность, на которую наносится покрытие, должна быть активирована. В результате активации на поверхности создаётся такой энергетический потенциал, который способствует улучшению адгезионной сцепляемости основы с покрытием.
Активирование поверхности осуществляется удалением с подготовленной к нанесению покрытия поверхности тончайшего слоя оксидов, которые могли образоваться в промежутках между заключительными операциями, подготавливающими заготовку к нанесению покрытия. При активировании одновременно происходит лёгкое перетравливание верхнего слоя металла и выявление его кристаллической структуры. Это благоприятствует прочному сцеплению покрытия с основой.
Активирование осуществляют непосредственно перед загрузкой заготовок в ванны для нанесения покрытия. Если заготовки поступают в гальванический цех непосредственно после механической обработки и на их поверхностях имеется только тонкая оксидная плёнка, то активирование может производиться без предварительного травления заготовок.
Активирование может осуществляться химическим и электрохимическим методами. Электрохимическое активирование реализуют только на аноде.
Если возможность быстрого нанесения покрытия после активирования отсутствует, то после активирования выполняют операцию пассивации поверхности. На поверхности формируется специальная тонкая оксидная плёнка. Когда заготовка пойдёт под покрытие, то сначала делают механическую обработку (доводку, полировку, обеспечивающую снятие оксидной плёнки). После этого повторяют операции обезжиривания, травления и затем активации (декапирования) поверхности.
Промывка. В технологическом процессе подготовки и нанесения электрохимических покрытий промывка, как правило, предусматривается после каждой технологической операции, относящейся к удалению загрязнений на поверхности заготовки. Недостаточная промывка заготовок может быть причиной плохого сцепления покрытия с основным материалом, появления пятен и других видов брака. Промывка осуществляется путём погружения заготовок в промывочные ванны со стоячей или проточной водой или при помощи струи воды.
Промывочная вода может быть холодной (температура не нормируется), тёплой (49…59 оС) и горячей (60…90 оС). Тёплая вода применяется после операций обезжиривания, травления лёгких металлов и сплавов, снятия шлама, после химического оксидирования чёрных металлов. Горячая вода используется перед сушкой заготовок.
Система операций подготовки поверхности к нанесению покрытия.
ГОСТ 9.305-84 «Покрытия металлические и неметаллические неорганические. Операции технологических процессов нанесения покрытий» определяет общий перечень подготовительных операций к нанесению покрытий и устанавливает последовательность нанесения покрытий на основные конструкционные материалы: стали, медь и медные сплавы, алюминий и его сплавы, цинковые и титановые сплавы.
Перечень основных подготовительных операций и их последовательность приведены на рисунке 4.9. Выбор конкретной схемы подготовки поверхности к нанесению покрытия осуществляется с учётом марки основного металла, наличия и характеристики загрязнений, вида механической обработки поверхности. В схеме не указаны операции промывки, которые в соответствии с ГОСТ 9.305-84 должны проводиться практически после каждой указанной на рисунке 4.9 технологической операции.
Рис. 4.9. Обобщенная схема этапов подготовки поверхности заготовки к нанесению покрытия
Дата добавления: 2018-04-04; просмотров: 4551; Мы поможем в написании вашей работы! |
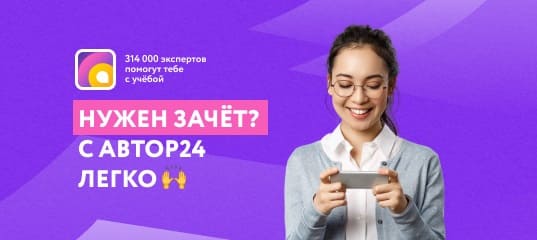
Мы поможем в написании ваших работ!