Дополнительная обработка покрытия
После нанесения покрытия на поверхность заготовки, как правило, проводится её дополнительная обработка. Эта обработка должна устранить или, по крайней мере, снизить отрицательные последствия процесса нанесения покрытия на работоспособность изделия. К таким отрицательным последствиям относят:
— насыщение поверхности заготовки и покрытия водородом (наводороживание поверхности);
— пористость покрытия;
— возникновение в покрытии внутренних напряжений;
— недостаточную адгезионную сцепляемость покрытия с основой;
— повышение шероховатости поверхности с покрытием вследствие отрицательной выравнивающей способности электролита.
Основными методами обработки покрытий, направленными на повышение их функциональной стойкости, являются: термическая обработка, обезводороживание, механическая обработка, гидрофобизирование, наполнение в воде, наполнение в растворе хроматов, нанесение лакокрасочного покрытия, оксидирование, оплавление, пропитка (лаком, клеем, эмульсией), тонирование, фосфатирование, химическое окрашивание, хроматирование, электрохимическое окрашивание и консервация.
Снятие внутренних напряжений. В процессе электроосаждения в металлических осадках возникают внутренние напряжения первого, второго и третьего родов: напряжения первого рода, уравновешиваемые в областях, соизмеримых с размерами заготовки; напряжения второго рода, уравновешиваемые в объёмах, имеющих порядок величины зерна кристалла; напряжения третьего рода, уравновешиваемые в объёмах, имеющих порядок элементарной кристаллической ячейки. Наибольшее влияние на прочность сцепления покрытия с основным металлом оказывают напряжения первого рода, определение которых осуществляется при контроле качества покрытия.
|
|
При электрокристаллизации такие металлы, как никель, железо, кобальт, родий, палладий, хром, марганец, стремятся к сжатию. В связи с этим в покрытиях возникают напряжения растяжения. Цинк, кадмий, свинец при электроосаждении расширяются, вызывая в покрытиях напряжения сжатия.
Наибольшие величины внутренних напряжений отмечены в осадках хрома, они достигают 10 ГПа. В осадках кобальта внутренние напряжения составляют 100…400 МПа, меди — 10…50 МПа, никеля и железа — 50…400 МПа, кадмия — 0,5…1,5 МПа.
Внутренние напряжения снижают, подбирая основу покрытия, близкие коэффициенты линейного расширения покрытия и основы, применяя многослойные покрытия с переходными слоями. Для снижения остаточных внутренних напряжений в покрытии и для упрочнения покрытия делают термообработку.
Упрочняющая обработка покрытия. Этот метод обработки увеличивает прочность покрытия, снижает пористость, выравнивает микро- и макроструктуры.
|
|
Для упрочнения покрытия используют высокотемпературные методы, в том числе спекание, пропитку, оплавление, пластическое деформирование, диффузионное насыщение. Пластическая обработка покрытия осуществляется накаткой наружной поверхности роликами или шариками или раскаткой внутренних отверстий. Поры при этом закрываются и прекращается доступ воздуха к поверхности основного материала.
Механическая обработка. Цели механической обработки состоят в придании заготовке после нанесения покрытия окончательных размеров и заданной по чертежу шероховатости поверхности. Для этого используют шлифование и полирование покрытия. Режимы обработки определяются свойствами материала покрытия, его толщиной и заданными параметрами шероховатости.
Удаление газовых включений из покрытия. Насыщение газами (Н2, О2, N2) происходит в процессе подготовки поверхности к нанесению покрытия и непосредственно при выполнении операции. Удаление газов из покрытия и основного металла необходимо для восстановления исходных физико-механических свойств основного металла и улучшения свойств покрытия. Особо в ряду газовых включений выделяют насыщение поверхности водородом, поскольку наличие водорода приводит не только к возможному отслоению покрытия, но и к водородному охрупчиванию материала.
|
|
Эффективным методом удаления газовых включений является термическая обработка заготовки. Основными её параметрами являются температура и продолжительность процесса. Так, при нанесении покрытий из Zn, Cd, Cr температура последующей термообработки находится в пределах 140…230 оС при продолжительности обработки 2…3 часа.
Скорость удаления водорода из покрытия при термообработке не одинакова во времени: вначале происходит быстрое выделение водорода, но примерно через два часа наступает сильное замедление процесса. Для полного удаления водорода требуется значительное время нагрева. Поскольку в течение трёх часов выделяется основное количество водорода, а оставшаяся часть практически не влияет на механические свойства основного материала, то увеличивать продолжительность обезводороживания свыше 3-х часов нет необходимости.
Пропитка и консервация покрытия. Если изделие имеет поры, то в процессе работы и при вылеживании оно поглощает влагу и корродирует. Кроме того, в местах разрыва покрытия с основой могут идти электрохимические реакции, приводящие к коррозии. Устранение структурной или случайной пористости покрытий путём заполнения пор уплотняющими составами является эффективным методом повышения защитной способности поверхности.
|
|
Консервацию проводят таким образом, что сначала с поверхности удаляется влага, поверхность высушивается, а потом её пропитывают слоем смазки или покрывают слоем смазки или воска.
Наиболее эффективные результаты повышения коррозионной стойкости изделий с хромовыми покрытиями показали пропитки пассивирующими растворами на основе нитратов, хроматов и фосфатов, полимеризующихся материалов — льняного масла и клея БФ-2, смазками АМС-3.
Дата добавления: 2018-04-04; просмотров: 750; Мы поможем в написании вашей работы! |
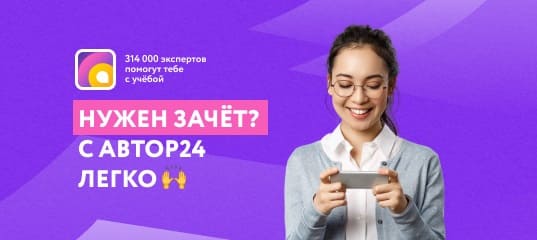
Мы поможем в написании ваших работ!