Характеристики нагружения механических компонентов привода
Нагрузку, которую воспринимают детали в процессе эксплуатации машины называют рабочей. Наиболее характерную для конкретного эксплуатационного режима рабочую нагрузку называют номинальной. Номинальную нагрузку принимают в качестве исходной при определении расчетной нагрузки, которая зависит от условий нагружения элемента конструкции и критериев его работоспособности.
Различают нормативные, случайные и эквивалентные нагрузки. Нормативные нагрузки формируются основными характеристиками механизма в предполагаемых условиях эксплуатации. Случайные нагрузки представляют собой отклонения от нормативных. Эквивалентной считается нагрузка при условно – стационарном режиме работы механизма, которая по своему воздействию равноценна фактически действующей в реальном нестационарном режиме.
Нагрузки могут быть заданы усилием F (Н), моментом Т (Н×м), а также мощностью Р (кВт) при частоте вращения n (об/мин) или угловой скорости w (рад/с).
Нагрузки, влияющие на показатели работы механических компонентов различны по характеру, величине и длительности действия.
Они могут быть постоянными и переменными. Величина и направление переменных нагрузок могут повторяться с определенной последовательностью. Такие нагрузки называют циклическими. Совокупность последовательных значений нагрузок (внешних или внутренних) за один период их изменения называют циклом.
|
|
Переменные нагрузки вызывают внутренние усилия непостоянного характера.
Под действием нагрузок в материале механических компонентов привода возникают напряжения, вызывающие деформацию структуры материала. Под действием нормально приложенных сил (растяжение, сжатие) или изгибающих моментов возникают нормальные напряжения s, перпендикулярные к сечениям деформируемого элемента. Под действием поперечных сил или крутящих моментов возникают касательные напряжения t, которые расположены по касательной к деформируемому сечению.
В случае, когда переменная нагрузка имеет циклический характер, она вызывает циклические изменения напряжений со следующими параметрами цикла:
- среднее напряжение sm или tm
sm=(smax+smin)/2, tm=(tmax+tmin)/2; (1.17)
- амплитуда sa или tа
sa=(smax– smin)/2, tа=(tmax – tmin)/2; (1.18)
- коэффициент асимметрии Rs или Rt
Rs=smin/smax , Rt=tmin/tmax . (1.19)
В выражениях (1.13)…(1.15) smax и smin, tmax и tmin максимальные и минимальные значения соответственно нормальных и касательных напряжений.
Коэффициент асимметрии цикла проставляется нижним индексом при знаке напряжения (sR – при обозначении нормальных напряжений; tR – при обозначении касательных напряжений).
|
|
В механических компонентах привода машин возникают различные циклы изменения напряжений: отнулевой, когда напряжения меняются от нуля до максимума (R=0); знакопеременный симметричный, когда напряжения меняются от отрицательного до такого же положительного значения (R = –1) и другие.
Под действием циклических нагрузок детали выходят из строя быстрее, чем при статических, т.к. при циклическом нагружении изменения структуры материала накапливаются и вызывают отказ в работе объекта более ранний, чем при статическом нагружении. Происходит усталостное разрушение детали.
Зависимость предельного числа циклов нагружения, при которых произошло разрушение, на фиксированных уровнях напряжений отражается функцией выносливости (кривая Веллера).
Функция выносливости устанавливается для каждого конкретного материала на основе экспериментальных данных.
Наибольшее напряжение цикла, которое деталь может выдержать не разрушаясь с заданной вероятнстью при практически неограниченном цикле нагружений, называют пределом выносливости.
|
|
Уравнение функции выносливости имеет вид
s q×Nc=const, (1.20)
где s – заданный уровень напряжения, МПа; Nc – предельное число циклов нагружения; q – показатель степени кривой выносливости (зависит от напряженного состояния, формы детали, механических характеристик, термообработки и т.п.).
На уровне предела выносливости кривая выносливости становится практически горизонтальной линией.
Если число циклов нагружения ограничено базовой величиной, то наибольшее напряжение цикла называют пределом ограниченной выносливости slimb.
Предел контактной выносливости, соответствующий базовому числу циклов перемены напряжений, sНlimb является предельным значением, при котором не наступает отказ по причине разрушения активных поверхностей контактирующих элементов в результате развития усталостного выкрашивания.
Предел выносливости при изгибе, соответствующий базовому числу циклов перемены напряжений, sFlimb является предельным значением, при котором не наступает усталостного разрушения детали.
Режимы нагружения машин
Эксплуатационные нагрузки машины (механизма) в течение всего срока службы неодинаковы. Совокупная оценка характерных нагрузок с учетом их времени действия и общим временем эксплуатации называется режимом работы механизма.
|
|
Режимы работы (таблица 1.1) устанавливают по классу использования (таблица 1.2) и классу нагружения (таблица 1.3).
Таблица 1.1 – Группа режима работы механизмов по ГОСТ 25835 – 83
Класс использования | Группа режима работы механизма для класса нагружения | Класс использования | Группа режима работы механизма для класса нагружения | ||||||
В1 | В2 | В3 | В4 | В1 | В2 | В3 | В4 | ||
А0 | 1М | 1М | 1М | 2М | А4 | 3М | 4М | 5М | 6М |
А1 | 1М | 1М | 2М | 3М | А5 | 4М | 5М | 6М | 6М |
А2 | 1М | 2М | 3М | 4М | А6 | 5М | 6М | 6М | 6М |
А3 | 2М | 3М | 4М | 5М |
Класс использования механизма (таблица 1.2) устанавливают по времени работы Lh.
Таблица 1.2 – Классы использования механизмов (ГОСТ 25835-83)
Класс использования | А0 | А1 | А2 | А3 | А4 | А5 | А6 |
Общее время работы механизмов Lh, ч | До 800 | 800 … 1600 | 1600 … 3200 | 3200 … 6300 | 6300 … 12500 | 12500… 25000 | 25000… 50000 |
Общее время работы Lh механизма рассчитывают по следующей
формуле
Lh =365×24 ×Тh×Kг×Kс×Kр× ПВ% /100 , (1.21)
где Тh – срок службы , лет; Kг – коэффициент годового использования при числе дней работы в году T г (Kг=T г/365); Kс –коэффициент суточного использования механизма при количестве работы часов в сутки tс (Kс=t с/24); Kр– коэффициент часового использования механизма, который при количестве минут работы механизма в течение часа tр, (Kр=tр/60); ПВ – относительная продолжительность включения.
Относительная продолжительность включения (ПВ) характеризует интенсивность использования механизма и вычисляется по формуле
ПВ=(tв/tц)×100%, (1.22)
где tв – часть цикла, когда механизм включен и работает; tц - полное время цикла.
Полное время цикла включает в себя: время пуска tп, время движения с установившейся скоростью tу, время торможения tт и время пауз tпауз (tц =tп+tу +tт +tпауз). Для механизмов принимают tц не более одного часа. При этом ПВ может принимать значения 15, 25, 40, 60.
Для двигателей повторно - кратковременного режима допустимое время цикла установлено равным 10 мин. Если tц >10 мин, то режим работы двигателя считается продолжительным ПВ=100%.
Общее времени работы механизма назначается с учетом наибольшей экономичности для ожидаемых условий использования механизма. Для механизмов, у которых предусмотрен капитальный ремонт норма устанавливается до капитального ремонта. Для механизмов, у которых капитальный ремонт не предусмотрен норма устанавливается до списания.
Класс нагружения механизмов (таблица 1.3) устанавливают по коэффициенту нагружения К.
Таблица 1.3– Класс нагружения механизма и его характеристики
(ГОСТ 25835-83)
Класс нагружения | Коэффициент нагружения К | Качественная характеристика класса нагружения |
В1 | До 0,125 | Работа при нагрузках значительно меньше номинальной и в редких случаях ей равных |
В2 | 0,125…0,25 | Работа при средних и номинальных нагрузках |
В3 | 0,25…0,5 | Работа преимущественно при номинальных и близких к номинальным нагрузкам |
В4 | 0,5…1,0 | Постоянная работа при номинальных и близких к номинальным нагрузкам |
Коэффициент нагружения К вычисляют по следующей формуле
К=å[(Qi/Qmax)3×(ti/åti)], (1.23)
где Qi – нагрузка, действующая на механизм в течение времени ti; Qmax – наибольшая нагрузка, действующая на механизм в течение времени его работы; ti – продолжительность времени действия нагрузки Qi; åti – суммарное время действия нагрузок на механизм.
Значения нагрузок определяют для концевого звена кинематической цепи механизма (канатный барабан и т.п.), с учетом всех факторов, включая и процессы неустановившегося движения.
Число циклов Nсi нагружения элемента каким – либо силовым воздействием, выраженным через Тiили Qi , за время ti при частоте вращения ni равно
Nсi= 60× ni×ti. (1.24)
Суммарное число циклов нагружения Nсå за время Lh нагружения элемента равно
Nсå= Nс1 + Nс2+…+ Nск, (1.25)
где Nс1, Nс2,…, Nск - число циклов нагружения элемента внешним воздействием Т1 , Т2, …,Тк соответственно за периоды времени t1, t2,…,tк , (t1 +t2 +…+tк =Lh).
Величины t1, t2, …,tк представляют собой совокупное время действия нагружающих воздействий Т1, Т2, …,Тк в различные периоды в течение всего срока службы.
Эксплуатационные нагрузки Т1, Т2, …,Тк можно сгруппировать по величине в относительных единицах, сопоставив с максимальной Тmax величиной (Т1/Тmax, Т2/Тmax, …,Тк/Тmax) и установить их время действия относительно всего срока службы (t1/th, t2/th,…, tк/th) или относительно общего числа циклов нагружения (Nс1/Nсå, Nс2/Nсå, …, Nск/Nсå).
Удельный вклад каждой совокупности нагрузок в сочетании со временем их действия относительно общей загрузки механизма является основанием для назначения типа режима нагружения.
В Правилах Госгортехнадзора различают режимы работы механизма легкий (Л), средний (С), тяжелый (Т) и весьма тяжелый (ВТ) .
На рисунке 1.17 показаны циклограммы нагруженности механизма подъема.
Рисунок 1.17– Графики загрузки механизма подъема груза по режимам:
1 – легкий режим; 2 – средний режим; 3 – тяжелый режим
На основе статистической обработки реальных эксплуатационных режимов получены типовыережимы нагружения механизмов.
ГОСТ 21354 – 87 предлагает следующие типовые режимы нагружения: постоянный П, тяжелый Т (b - распределение), средний равновероятный Р (равновероятное распределение), средний нормальный Н (нормальное распределение), легкий Л (g - распределение) и особо легкий Ло (b - распределение).
В таблице 1.4 и на рисунке 1.18 изображена упорядоченная зависимость между нагружающими моментами и числом циклов нагружения в относительных координатах T/Tmax и Nс/Nсå.
Таблица 1.4 – Типовые режимы нагружения (ГОСТ 21354 –87)
Виды режимов нагружения | Функция распределения | Параметры функ- ции распределения |
1) Тяжелый режим – интегральная функция b- распределения | Ф(ni)= ![]() | a=6; b=2 nср=0,77 |
2) Средний – равновероятный, интегральная функция равновероятного распределения | Ф(ni)= ![]() | nср=0,5 |
3) Средний – нормальный, интегральная функция нормального распределения |
Ф(ni)= ![]() | nср=0,5; s=0,19 |
4) Легкий – интегральная функция b - распределения | Ф(ni)= ![]() | а=2,2; b=3,0 nср=0,42 |
5) Особо легкий – интегральная функция b- распределения | Ф(ni)= ![]() | a=1,8; b=4,0 nср=0,31 |
Примечание. Коэффициенты: ni= Тi / Tmax ; nср= Tср / Tmax, где Ti – текущий вращающий момент на ведущем элементе, соответствующий числу циклов нагружения Nсi; Тmax – максимальное значение вращающего момента; Tср – среднее значение вращающего момента. |
Рисунок 1.18 – Типовые режимы нагружения (ГОСТ 21354 – 87): 0 – постоянный; 1 – тяжелый ; 2 – средний равновероятный;3 – средний нормальный; 4 – легкий ; 5 – особо легкий
Особенности циклограмм отражает коэффициент интенсивности m, который характеризует интенсивность типового режима при базовом числе циклов Nlim.:
- для ступенчатой циклограммы
m =å( Тi / Тmax)3(Nci/Nlim); (1.26)
- при плавном характере циклограммы (рисунок 2.19)
m = (1.27)
Соответствие режима нагружения механизма одному из типовых режимов устанавливается по подобию форм кривых и по среднему значению нагрузок. В расчетах следует принимать типовой режим наиболее близкий к фактическому в области больших нагрузок путем сравнения реальной циклограммы с типовыми или эквивалентными режимами нагружения.
Группы режимов работы механизмов по ГОСТ 25835–83, типовые режимы по ГОСТ 21354 – 87 и режимы по правилам Госгортехнадзора приведены в таблице 1.5
Таблица 1.5 – Соответствие групп режимов работы механизма
Режим эксплуатации по ГОСТ 21354–87 | «0» непрерывный | «1» тяжелый | «2» средний равновероят-ностный | «3» средний нор-мальный | «4» легкий | «5» Особо легкий |
Режим работы по ГОСТ 25835–83 | 6М | 5М | 4М | 3М | 2М | 1М |
Режим по правилам Госгортехнадзора | «ВТ» ПВ(%)= 63…100 | «Т» ПВ(%)= 40…63 | «Срв» ПВ (%)= 25…40 | «Сн» ПВ (%)= 25…40 | «Л» ПВ(%)= 16…25 | «Ло» ПВ<16% |
Эквивалентное число циклов нагружений определяется по формуле
NЕ=m×Nсå. (1.28)
Этот параметр используют для установления эквивалентности реальных режимов типовым, а также для определения коэффициента долговечности КL .
Коэффициент долговечности KL устанавливает соответствие между базовым N0 и эквивалентным числом циклов NE нагружений
KL =(N0/NE)1/q. (1.29)
Характеристики режимов учитываются при расчетах на прочность конструкции.
1.6. Учет нагрузок, изменяющихся во времени
Расчет нагрузок, изменяющихся во времени, может быть произведен по одному из нижеприведенных методов (ГОСТ 21354 – 87).
Метод эквивалентных циклов ориентирован на приведение переменной нагрузки к величинам, вызывающим наибольшее повреждение элементов передачи:
- при расчете на контактную выносливость за исходную нагрузку Т1Н принимают наибольшую из подводимых к передаче, для которой число циклов перемены напряжений не менее 0,03×NНlim1; соответствующее этой нагрузке эквивалентное число циклов напряжений NНЕ1 определяют по формуле
NНЕ1 =mН× NНlim1 , (1.30)
где NНlim1 – базовое число циклов нагружений; mН – коэффициент, учитывающий характер циклограммы, который для ступенчатой циклограммы равен
mН =å( Т1i / Т1Н)3(Nci/NНlim1) , (1.31)
а при плавном характере циклограммы его величина устанавливается по формуле
T1max
mН =ò( Т1i / Т1Н)3(Nci/NНlim1) . (1.32)
T1min
- при расчете на выносливость при изгибе за исходную расчетную нагрузку Т1F (или Т2F ) принимают наибольшую длительно действующую с числом циклов перемены напряжений более 5×104; соответствующее этой нагрузке эквивалентное число циклов напряжений NFЕ определяют по формуле
NFЕ =mF× NFlim , (1.33)
где mF – коэффициент, учитывающий характер циклограммы
mF =å( Т1i /Т1F)qF ×(Nci/ NНlim1), (1.34)
(qF – показатель степени кривой выносливости при циклическом изгибе).
Метод эквивалентных моментов предусматривает, что эквивалентный момент учитывает значение и длительность всех уровней нагрузки:
- при расчете на контактную выносливость за исходную расчетную нагрузку Т1Н (или Т2Н ) принимают эквивалентный момент
ТНЕ =Тmax[å(Ti/Tmax)3×(Nci /NK)]1/3 . (1.35)
- при расчете на выносливость при изгибе за исходную расчетную нагрузку Т1F (или Т2F) принимают эквивалентный момент
ТFЕ =Тmax[å(Ti/Tmax)3×(Nci / NK)]1/qF , (1.36)
Метод эквивалентных напряженийоснован на определении расчетного напряжения для каждой ступени циклограммы:
- при расчете на контактную выносливость эквивалентное напряжение sНЕ определяют по формуле
sНЕ=КНЕ×sН1, (1.37)
где sН1 – расчетное напряжение соответствующее первой ступени циклограммы; КНЕ - коэффициент эквивалентности, который равен:
КНЕ =[å(sНi /sН1)6×(Nci / NНå)]1/6 при sНi >sНlim; (1.38)
КНЕ =[å(sНi /sН1)20×(Nci / NНå)]1/20 при sНi £sНlim , (1.39)
где NНå - суммарное число циклов всех ступеней циклограммы; sНi - расчетное напряжение, соответствующее i -й ступени циклограммы (sНi³0,75×sНlim ); Nci – соответствующее этой ступени число циклов перемены напряжений (Nci ³0,03 ×NНlim);
-при расчете на выносливость при изгибе эквивалентное напряжение sFЕ определяют по формуле
sFЕ=КFЕ×sF1, (1.40)
где sF1 – расчетное напряжение соответствующее первой ступени циклограммы;
КFЕ - коэффициент эквивалентности, который равен
КFЕ =[å(sFi /sF1)qF×(Nci /NFå)]1/qF , (1.41)
где NFå - суммарное число циклов всех ступеней циклограммы, принятых в расчете на изгибную выносливость; sFi - расчетное напряжение, соответствующее i -й ступени циклограммы; Nci - соответствующее этой ступени число циклов перемені напряжений; qF – показатель кривой усталости.
1.7. Оценка прочностной надежности механических
Компонентов привода
Оценку рабочего состояния механических элементов машин производят по показателям их напряженно – деформированного состояния.
Наиболее распространен метод сравнения расчетных (рабочих) напряжений, возникающих под действием эксплуатационных нагрузок, с допускаемыми их значения-
ми для данного материала, вида нагружения и прочности:
s£[s], (1.42)
t£[t], (1.43)
где s и[s] соответственно рабочее и допускаемое нормальные напряжения; t и [t] соответственно рабочее и допускаемое касательные напряжения.
Расчет по допускаемым напряжениям обычно выполняют как проектировочный.
Допускаемые напряжения и коэффициенты запаса прочности устанавливают с помощью нормативных документов или аналитически.
При статических нагрузках допускаемые напряжения [s] и [t]определяются по следующим зависимостям:
[s]=slim/[Ss], (1.44)
[t]=t lim/[St], (1.45)
где slim и t lim – соответственно предельные значения нормальных и касательных напряжений; [Ss] и [St] – допускаемые (требуемые, заданные или нормативные) коэффициенты запаса прочности для рассчитываемого элемента.
Для пластичных материалов в качестве предельных напряжений при постоянных во времени нагрузках принимают предел текучести sт (при растяжении, сжатии, изгибе) и tт (при кручении).
Для хрупких материалов в качестве предельных напряжений при постоянных во времени нагрузках принимают предел прочности sв (при растяжении, сжатии, изгибе) и tв (при кручении и срезе).
В расчете на прочность элементов при переменных напряжениях в качестве предельных напряжений принимают соответствующие пределы выносливости sR (растяжение, сжатие и изгиб) и tR (кручение, срез).
Допускаемый коэффициент запаса прочности равен
[S]= [S1]×[S2]×[S3], (1.46)
где [S1] – коэффициент, учитывающий точность определения нагрузок и напряжений, [S1]= 1…1,6; [S2] – коэффициент, учитывающий однородность материала, [S2]=1,2…2,5; [S3] – коэффициент, учитывающий специфические требования безопасности, [S3]=1…1,5.
Расчет по коэффициенту запаса прочности обычно выполняют как проверочный. В этом случае производят сравнение действительного коэффициента запаса прочности S с его допускаемым значением [S].
S³[S]. (1.47)
Расчетный (фактический) коэффициент запаса прочности при симметричном цикле перемены напряжений определяют по зависимостям:
- при растяжении, сжатии, изгибе
Ss=s-1/( КsD×sа +ys×sm); (1.48)
- при кручении
St=t-1/( КtD×tа +yt×tm); (1.49)
- при совместном действии нормальных и касательных напряжений
S=Ss× St/( S2s+ S2t)1/2 . (1.50)
В вышеприведенных выражениях: s-1 и t-1 – пределы выносливости материала при знакопеременном симметричном цикле напряжений; КsD и Кt D – коэффициенты, учитывающие размер деталей и концентрацию напряжений; ys и yt – коэффициенты, учитывающие чувствительность материала к асимметрии цикла.
Неоднородная структура материала и технологические погрешности изготовления вызывает разброс показателей напряженно – деформированного состояния элемента. В этом случае разрушающие и действующие напряжении являются величинами случайными с соответствующей функцией распределения, которая отражает вероятность разрушения элемента и характеризует качественные особенности оценки прочностной надежности. Для конструктивных элементов машин допускают вероятность разрушения [P]= 0,10…0,001.
Одним из наиболее общих условий применимости элементов машины является условие их равнопрочности.
Дата добавления: 2018-04-04; просмотров: 1203; Мы поможем в написании вашей работы! |
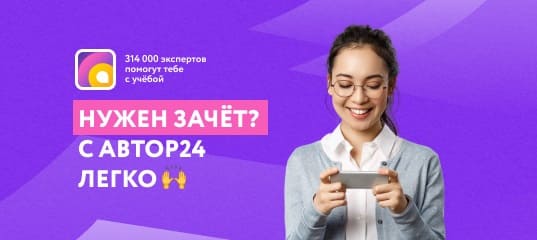
Мы поможем в написании ваших работ!