Показатели исчисления размера частей окружности
Общеизвестно, что конструкторская мысль, прежде чем воплотиться в материале, сначала реализуется на бумаге - в эскизах, рисунках, схемах, чертежах. По этим своеобразным наглядным пособиям затем создаются предметы, вещи, изделия, сооружения заданных размеров, форм. При этом, как правило, не требуется производить прямого переноса (обозначения) этих размеров и форм на материал изготовления.
Однако в некоторых случаях такой перенос просто необходим. Так, швея не начнет кройку, не перенеся (не обозначив) на ткань весь рисунок модели будущего изделия. Слесарь-станочник не приступит к обработке, например, направляющих станины (основания) токарного станка, не выполнив прямо на заготовке соответствующей разметки - четкого обозначения контуров обрабатываемых плоскостей и толщин снимаемого металла.
В ювелирном деле при ручном изготовлении украшений операцией разметки называется процесс прямого, соразмерного переноса рисунка будущего изделия или отдельной его детали на материал. Никогда не следует забывать, что правильно выполненная операция разметки имеет исключительно важное значение для последующей обработки и получения на финише изделия высокого качества. Ведь малейшие неточности, погрешности в разметке могут привести к искажению отдельных, зачастую довольно сложных элементов рисунка, к нарушению целостности формы и содержания всего замысла.
|
|
Правда, в наши дни, когда в ювелирное дело вторгся механический труд, значение операции разметки сильно уменьшилось, особенно с внедрением таких технологических процессов, как штамповка и литье. Штампованные и литые заготовки деталей и изделий, поступая на стол ювелира-монтировщика, уже имеют размеры и, главное, формы, очень близкие к заданным, поэтому нет необходимости на них что-либо обозначать, размечать. Задача ювелира-монтировщика - подправить, доработать эти заготовки, довести точность их форм и размеров до требуемой, а затем собрать, смонтировать в единое целое.
Для выполнения разметки необходимы следующие инструменты и приспособления: чертилка, разметочный циркуль, масштабная линейка, штангенциркуль, ножницы, молоток, кернер, разметочная плита. Процесс разметки условно можно разделить на три стадии: подготовку создаваемого образца изделия, подготовку материала для изготовления, собственно разметку.
Подготовка создаваемого образца изделия заключается в тщательной его прорисовке на кальке или бумаге. Материал для изготовления (заготовка) перед проведением разметки должен быть отожжен - на равномерно окисленной темной поверхности разметочные риски будут более заметны; на заготовке не должно быть никаких пороков (трещин, раковин, вмятин). Непосредственно разметка может быть осуществлена несколькими способами: вычерчиванием рисунка с применением правил построения геометрических фигур (рис. 3.1), переносом рисунка с кальки на заготовку с помощью воска, копировальной бумаги, краски, путем выкалывания.
|
|
Рис. 3.1. Разметка путем построения геометрических фигур
Вычерчивание рисунка с применением правил деления прямых и окружностей, построения ряда геометрических фигур (треугольника, квадрата, ромба, пятиугольника, овала, эллипса) - процесс довольно кропотливый, требующий наличия специальной разметочной плиты, а также значительных затрат времени, в связи с чем на практике применяется редко. Деление окружности на части можно сделать также с помощью готовых, выверенных длительным опытом работы методов исчисления (табл. 3.1).
Таблица 3.1
Показатели исчисления размера частей окружности
Количество частей | Число, умнажаемое на радиус |
3 | 1,7321 |
4 | 1,4142 |
5 | 1,1756 |
6 | 1,0000 |
7 | 0,8778 |
8 | 0,7654 |
9 | 0,6840 |
10 | 0,6180 |
11 | 0,5635 |
12 | 0,5176 |
13 | 0,4786 |
14 | 0,4450 |
15 | 0,4158 |
16 | 0,3902 |
17 | 0,3676 |
18 | 0,3473 |
19 | 0,3292 |
20 | 0,3129 |
21 | 0,2980 |
22 | 0,2845 |
23 | 0,2723 |
24 | 0,2611 |
25 | 0,2507 |
26 | 0,2411 |
27 | 0,2321 |
28 | 0,2240 |
29 | 0,2162 |
30 | 0,2091 |
Перенос рисунка на заготовку с помощью воска осуществляют следующим образом:
|
|
рисунок изделия мягким остро отточенным карандашом изображают на кальке;
заготовку протирают сухим порошком пемзы; на нее наносят небольшое количество воска; затем прогревают для расплавления воска в целях покрытия поверхности заготовки тонкой восковой пленкой, после чего заготовку охлаждают до застывания воска;
кальку с рисунком (карандашными линиями вниз) укладывают на восковую пленку; удерживая кальку в таком положении, проглаживают ее обычным утюгом или каким-либо другим предметом с гладкой поверхностью, после чего кальку убирают - на восковой пленке должен остаться рисунок;
чертилкой, следуя строго изображению, прорезают (процарапывают) рисунок на заготовке (металле);
заготовку (металл) нагревают до расплавления воска, мягкой тканью воск удаляют.
Перенос рисунка на заготовку с помощью копировальной бумаги выполняют в такой последовательности:
заготовку протирают сухим порошком пемзы; копировальную бумагу блестящей (жирной) стороной вниз укладывают на заготовку;
|
|
кальку с изображенным на ней рисунком укладывают обратной (чистой) стороной вниз на копировальную бумагу и удерживают в таком положении до тех пор, пока жестким карандашом полностью не прорисуют рисунок;
кальку и копировальную бумагу удаляют, полученное на поверхности заготовки (металла) изображение рисунка прорезывают чертилкой;
остатки следов копировальной бумаги следует смыть.
Перенос рисунка на заготовку с помощью специального состава краски состоит из нескольких операций:
смешивают одну часть жидкого шеллака, три части спирта и достаточное количество метола - сернокислой соли параметиламинофенола;
полученным раствором густого фиолетового цвета покрывают поверхность заготовки, дают просохнуть;
кальку с рисунком обратной (чистой) стороной вниз укладывают на просохшую краску;
чертилкой прорезают на металле узор, остатки раствора удаляют.
Перенос рисунка на заготовку путем выкалывания, включает ряд операций: поверхность заготовки протирают сухим порошком; затем заготовку покрывают тонким слоем клея, а кальку обратной (чистой) стороной вниз наклеивают на поверхность заготовки;
кернером или чертилкой, следуя строго по изображению рисунка, на металле (через кальку) на близком расстоянии друг от друга выбивают (выкалывают) точки;
кальку и клей удаляют с помощью теплой воды;
чертилкой, процарапывая (прорезая) металл, соединяют все точки - получают необходимый рисунок (узор)
Гибка и правка
Гибка. Процесс деформации материала, когда отдельные его участки под действием внешних сил формоизменяются, причем в самой различной степени, называется гибкой. Гибка - одна из важнейших монтировочных операций. Из общего объема монтировочных работ на долю гибки приходится примерно 30%. Наиболее широко применяется эта операция при изготовлении ювелирных украшений техникой филиграни. Существуют два способа гибки: вручную и с помощью инструмента.
Гибка вручную. Это самый простой способ гибки, при котором для придания материалу необходимой формы достаточно силы пальцев руки. Так можно производить гибку тонкой проволоки и полосы (листа), например тонкого браслета. Значительно тяжелее гнуть таким образом короткую и толстую проволоку, потому что придать материалу сложные формы за счет усилий, создаваемых пальцами рук, практически невозможно.
Гибка с помощью инструмента. Такая гибка выполняется с применением гибочных щипцов, оправок, различных приспособлений (рис. 3.2, а, б).
Гибка звеньев круглой формы из проволоки производится (рис. 3.2, в) с помощью цилиндрических металлических оправок и ригелей, обычного гвоздя, куска латунной проволоки. Оправки выбирают диаметром чуть меньшим внутреннего диаметра звена, потому что упругость проволоки не позволяет ей достаточно плотно пристать к оправке; за счет этой же упругости внутренний диаметр звеньев после снятия их с оправки увеличивается до необходимого. До начала гибки проволоку отжигают; при этом она не должна иметь никаких дефектов. Намотку спирали производят от руки с закреплением оправки в ручных тисках и без такого закрепления. Перед снятием с оправки спираль отжигают (вместе с оправкой). Съем спирали с оправки производят плоскогубцами путем протягивания оправки через отверстие волочильной доски. После того, как спираль снята, ее разрезают на отдельные звенья лобзиком; положение пилки лобзика при этом должно быть перпендикулярным к виткам спирали.
Рис. 3.2. Гибка и правка
Гибка звеньев овальной формы из проволоки осуществляется строго в той же последовательности, что и гибка звеньев круглой формы. Оправками для гибки таких звеньев служат металлические (медь, латунь, сталь) заданного профиля полосы с закругленными (неострыми) краями (рис. 3.2, г).
Гибка спирали, витки которой повторяются равномерно по всей длине, выполняется с помощью приспособления, изображенного на рис. 3.2, д. Гибку производят следующим образом: один конец отожженной, протравленной и зачищенной проволоки сгибают круглогубцами в петлю, петлю жестко (смещения недопустимы) накидывают на крайний штифт приспособления. Затем проволоку, постоянно подтягивая за другой конец, навивают как можно плотнее на второй и последующие штифты. Снимают спираль со штифтов с помощью обычной отвертки.
Гибка полос и листов осуществляется с применением опорных плит и оправок заданных форм. Опорные плиты используют как своеобразные матрицы, а оправки - как пуансоны штампа. Практические приемы гибки показаны на рис. 3.2, е.
Правка. Процесс выправления, выпрямления неровностей поверхности и формы материала изготовления называется правкой. Различают правку ручную и с помощью специальных инструментов и приспособлений: металлических, текстолистовых и деревянных молотков, стальных правочных (рихтовальных) плит-флакейзенов, наковален-шпераков, плоскогубцев, ригелей, оправок, обычных и специальных пуансонов.
Правка ручная. Имеет ограниченное применение, так как усилием пальцев рук можно выправить лишь тонкую проволоку, небольшие ее изгибы. Качество ручной правки невысокое.
Правка с помощью инструмента и приспособлений. Такая правка подразделяется на правку листового, ленточного, пруткового материала, правку штампованных и литых изделий и деталей.
Правка листового, ленточного и пруткового материала выполняется на флакейзене или шпераке молотками с круглой или прямоугольной формой бойка (рис. 3.2, ж). Рабочая поверхность инструмента должна быть гладкой, без каких-либо дефектов. Перед правкой материал отжигают. Правку широкого листа ведут простукиванием от середины к краю.
Правка проволочного и трубчатого материала выполняется несколькими способами (рис. 3.2, з): вытягиванием (протягиванием) плоскогубцами вокруг оправки или без использования оправки; вытягиванием через отверстие волочильной доски и рихтовкой на правочной плите. Последний способ правки необходим, когда требуется абсолютно ровное выправление материала; правку ведут осторожно, постоянно меняя положение материала на плите.
Правка штампованных изделий и деталей сводится в основном к правке шинок колец для придания им правильной круглой формы. Эта операция производится с помощью ригеля (рис. 3.2, и), коническая форма которого позволяет править кольца с самыми различными диаметрами шинок и обеспечивает одновременно необходимую плотность прилегания шинки к поверхности ригеля. Наряду с круглыми бывают еще овальные, квадратные, прямоугольные и шестиугольные ригели.
Правка гладких шинок ведется текстолитовыми молотками равномерными ударами по всей окружности. Правку колец с кастом (оправой для камня) начинают от каста и ведут поочередно в разные стороны сверху вниз и снизу вверх, Во избежание приобретения шинкой формы, близкой к форме ригеля (конической), кольца правят сначала с одной, потом с другой стороны.
В случае необходимости правят также боковые стороны шинок. В качестве ударного инструмента при такой правке используют металлические молотки, а в качестве опорных плит - флакейзен или шперак (рис. 3.2, к). Правку ведут, равномерно (по всей окружности) простукивая металлическим молотком с прямоугольной формой бойка. Правку боковых сторон колец можно осуществить и в специальных приспособлениях. Этот способ (рис. 3.2, л) обеспечивает высокое качество правки, кроме того, исключает последующие запиловку и шабровку. Приспособления для такой правки можно сделать из отслужившего срок штампа, незначительно доработав его. Требуемые точность и качество правки достигаются буквально одним ударом металлического молотка
Процесс снятия с ювелирных украшений определенного (требуемого) слоя металла в целях придания им точности формы, размеров, чистоты поверхности называется опиливанием. Опиливание бывает ручное и механизированное.
Рис. 3.4. Опиливание
Опиливание вручную. Выполняется с помощью напильников, надфилей, рифелей. В практике ювелиров встречается опиливание ровной (рис. 3.4, а), цилиндрической (рис. 3.4, б), криволинейной (рис. 3.4, в) поверхностей, а также опиливание (зачистка) мест пайки (рис. 3.4, г), удаление заусенцев с краев изделия (рис. 3.4,(9), запиловка торцовых сторон (рис. 3.4, е), обработка сложных прорезных узоров (рис. 3.4, ж), запиловка прямоугольных и фасонных пазов (рис. 3.4, з), опиливание внутренних округлых поверхностей (рис. 3.4, и) и т. д. Основной объем опиловочных работ ювелиры выполняют напильниками и надфилями, приведенными в табл. 3.19 и 3.20.
Процесс опиливания ювелиры выполняют сидя за верстаком. Изделие во время опиливания обычно удерживают пальцами одной руки, прижимая его к финагелю. Размах движений инструмента страхуется либо финагелем, либо большим пальцем держащей изделие руки (на палец в этом случае обязательно надевается кожаный чехол). Локти рук в процессе опиливания находятся в свободном состоянии.
Таблица 3.19
Дата добавления: 2018-02-28; просмотров: 359; Мы поможем в написании вашей работы! |
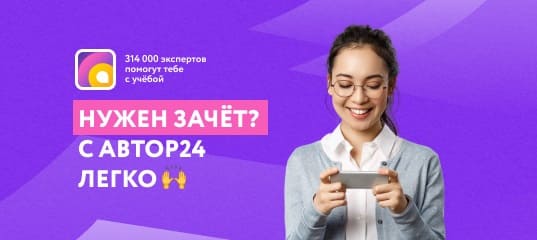
Мы поможем в написании ваших работ!