ОПЫТ ОТЕЧЕСТВЕННЫХ ПРЕДПРИЯТИЙ ПО УПРАВЛЕНИЮ КАЧЕСТВОМ
Работы по планомерному управлению качеством продукции начались в нашей стране в 50-е годы. Первый опыт системного подхода к повышению качества промышленной продукции в стране был заложен разработкой и внедрением в 1955 г. на предприятиях Саратовской области комплекса мероприятий по обеспечению качества, который в дальнейшем получил название системы бездефектного изготовления продукции и сдачи ее с первого предъявления (система БИП). В основе этой системы лежит принцип самоконтроля исполнителем результатов своей работы и полной ответственности исполнителя за качество выполненной работы. Основным критерием, применяемым для количественной оценки качества труда рабочего, служил процент сдачи продукции с первого предъявления, который вычислялся как процентное отношение количества партий, принятых с первого предъявления, к общему числу изготовленных работником партий и предъявленных ОТК. За сдачу продукции с первого предъявления предусматривалось премирование. Организационной основой системы БИП являлись оперативный контроль качества изготовленной продукции и персональная ответственность каждого рабочего за качество своего труда.
Внедрение системы БИП позволило:
• обеспечить строгое выполнение технологических операций;
• повысить персональную ответственность каждого рабочего за качественные результаты своего труда;
|
|
• более эффективно использовать моральное и материальное поощрение рабочих за качество труда;
• создать предпосылки для широкого развертывание движения за повышение качества продукции.
Принципы и опыт реализации системы БИП в 60-е годы получили широкое распространение на многих предприятиях нашей страны и за рубежом (к примеру, в США подобная программа получила название «нуль дефектов»). Преимущества системы БИП заключались в ее простоте, наглядности результатов, оперативности, что позволило в дальнейшем использовать ее не только на промышленных предприятиях, но и в научно-исследовательских и проектно-конструкторских организациях. Основной недостаток системы заключался в том, что ее действие распространялось лишь на стадию изготовления продукции.
Указанный недостаток был преодолен в системе управления качеством продукции, разработанной и внедренной в 1958 г. рядом проектно-конструкторских организаций и предприятий Горьковской области и получившей название КАНАРСПИ (качество, надежность, ресурс с первых изделий). В этой системе был сделан упор на повышение надежности изделий за счет укрепления технической подготовки работы КБ и технологов производства, на долю которых приходилось 60 - 85 % дефектов, обнаруживаемых при эксплуатации. Создавались опытные образцы узлов, деталей, изделия в целом, проводились их комплексные испытания. Значительное развитие получило опытное производство, стандартизация и унификация, общетехнические системы стандартов, такие как Единая система конструкторской документации (ЕСКД), Единая система технологической подготовки производства (ЕСТПП). Характерным для системы КАНАРСИ являлось то, что она вышла за рамки стадии изготовления продукции и охватывала многие виды работ стадиях проектирования и эксплуатации.
|
|
Внедрение этой системы на ряде предприятий Горьковской области позволило:
• сократить сроки доводки новых изделий до заданного уровня качества в 2-3 раза;
• повысить надежность выпускаемых изделий в 1,5-2 раза, увеличить ресурс в 2 раза;
• снизить трудоемкость и цикл монтажно-сборочных работ в 1,3 - 2 раза.
Дальнейшим развитием системы БИП явилась система бездефектного труда (СБТ), разработанная и внедренная в начале 60-х годов на Львовском заводе телеграфной аппаратуры. Эта система, сохраняя основные принципы БИП, вводит коэффициенты качества труда, с помощью которых можно оценить качество работы как отдельного работника, так и любого подразделения. Такие коэффициенты вычисляются для каждого работника и подразделения за установленный промежуток времени (неделя, месяц, квартал) путем учета количества и значимости допущенных производственных нарушений. За каждое отклонение от нормы, каждую ошибку, допущенный дефект оценка снижается в соответствии со специально разработанным классификатором производственных нарушений: каждому дефекту соответствует фиксированный коэффициент снижения. Максимальная оценка качества труда и наибольший размер премии устанавливался тем работникам и подразделениям, которые за отчетный период не имели ни одного нарушения.
|
|
Внедрение СБТ дало возможность:
• количественно оценить качество труда каждого работника и коллектива;
• повысить заинтересованность и ответственность каждого работника за качество своего труда;
• сократить потери от брака и рекламации, повысить производительность труда.
В 1963-64-х гг. на Ярославском моторном заводе была разработана и внедрена система научной организации работ по повышению моторесурса (НОРМ), которая позволяла повысить надежность изделия на основе повышения надежности и долговечности отдельных узлов и деталей. Организация работ в системе построена по принципу цикличности. Каждый новый цикл по увеличению моторесурса начинался после достижения ранее запланированного уровня и предусматривал определение его фактического уровня, выявление деталей и узлов, которые лимитируют этот ресурс. Охватывая стадии проектирования, изготовления и эксплуатации выпускаемой продукции, система НОРМ обеспечивала не только эффективную реализацию требований документации, но и поэтапное их превышение. На стадии производства система НОРМ включала в себя положения системы БИП и СБТ, на этапе проектирования - некоторые положения системы КАНАРСПИ.
|
|
Внедрение системы НОРМ дало возможность увеличить ресурс двигателей до первого капитального ремонта с 4 тыс. до 10 тыс. часов, повысить гарантийный срок на двигателе на 70 %, снизить потребность в запасных частях более, чем на 20 %.
В середине 70-х годов на передовых предприятиях Львовской области появились комплексные системы управления качеством продукции (КСУКП). Цель КСУКП заключалась в создании продукции, соответствующей лучшим мировым аналогам и достижениям науки и техники. В связи с внедрением на предприятиях КСУКП получили развитие метрологическое обеспечение производства, многоступенчатый анализ дефектов и статистический контроль качества, на предприятиях и объединениях стали разрабатываться программы качества, вводилась аттестация продукции. За 10 лет с помощью КСУКП удалось создать и успешно реализовать конкурентоспособную продукцию, повысить удельный вес продукции высшей категории качества в 2 - 3 раза, значительно сократить потери от брака и рекламаций, уменьшить сроки разработки и освоения новой продукции. В КСУКП были взаимосвязаны между собой технические, экономические, организационные и социальные мероприятия, что позволяло активно влиять на повышение качества на этапах проектирования, производства и эксплуатации изделий.
В 1978 г. на основе опыта применения указанных выше систем управления качеством продукции была разработана Единая система государственного управления качеством продукции (ЕС ГУКП). Основными задачами ЕС ГУКП являлись:
• разработка, подготовка и развертывание в необходимом количестве в кратчайшие сроки производства новой продукции высокого качества;
• своевременное снятие с производства, замена или модернизация морально устаревшей продукции;
• сохранение качества продукции в процессе ее доведения до потребителя и при эксплуатации.
Одним из основных принципов ЕС ГУКП являлась комплексность решения проблемы управления качеством продукции. В этой системе комплексность обеспечивается взаимной увязкой технических, организационных и экономических мероприятий на различных уровнях, включающих межотраслевой, отраслевой уровни и уровни предприятий. Для разных уровней используются различные категории нормативных документов: государственные стандарты (ГОСТ), отраслевые стандарты (ОСТ), стандарты предприятия (СТП).
Внедрение ЕС ГУКП позволило увеличить выпуск качественной продукции, использовать отдельные элементы системы на отраслевом уровне и на предприятиях.
При переходе к рыночным отношениям исчезли директивные методы управления, появилась конкуренция товаропроизводителей, на первое место вышли вопросы качества продукции. Заслугой Госстандарта в переходный период к рынку явилась работа по гармонизации отечественных стандартов в области качества с международными стандартами, где нашел свое отражение отечественный опыт по управлению качеством продукции.
9. ДЕЯТЕЛЬНОСТЬ МЕЖДУНАРОДНОЙ ОРГАНИЗАЦИИ ПО СТАНДАРТИЗАЦИИ В ОБЛАСТИ ОБЕСПЕЧЕНИЯ КАЧЕСТВА.
Международная организация по стандартизации, ИСО (ISO), содействует развитию стандартизации и активизации роли стандартов во всем мире. Ее основной задачей является развитие сотрудничества и международный обмен в интеллектуальной, научной, технической и экономической сферах деятельности. Эта неправительственная организация, учрежденная в 1947 году, в настоящее время объединяет представителей из 140 стран. Результатом деятельности ИСО является публикация согласованных международных стандартов во всех направлениях жизнедеятельности.
Деятельность ИСО осуществляется следующим образом Представители различных государств самостоятельно выбирают для себя форму участия в работе организации и могут являться действительными членами, членами с совещательным голосом и наблюдателями. Головным органом управления ИСО является Генеральная ассамблея. В промежутках между сессиями Генеральной ассамблеи управление осуществляется Советом.
Текущая работа организации происходит по двум вертикалям - политики развития и технического управления, представленных комитетами Совета. На сегодняшний день в ИСО присутствуют следующие основные комитеты:
• КАСКО – комитет по оценке соответствия;
• КОПОЛКО – комитет по защите интересов потребителей;
• ДЕВКО – комитет по оказанию помощи развивающимся странам;
• РЕМКО – комитет по стандартным образцам.
Разработка проектов международных стандартов происходит рабочими группами технических комитетов (ТК). В настоящее время в ИСО работает 224 технических комитета.
В 1979 г. в рамках ИСО был создан ТК-176 «Управление качеством и обеспечение качества», в настоящее время он называется «Менеджмент качества и обеспечение качества». Создание данного комитета было продиктовано ожесточившимися условиями конкуренции, потребовавшими от предприятий внедрения и обеспечения эффективных систем управления качеством. Первая версия стандартов в области обеспечения качества ИСО 9000 была разработана на основе Британских национальных стандартов и опубликована в 1987г. Это была группа взаимосвязанных стандартов, касающихся общего руководства качеством. Следующая концепция 1994г. была значительно расширена за счет рекомендаций по внедрению систем качества в организации. В декабре 2000г. была принята новая версия стандартов, предусматривающая принципиально отличные пути построения системы управления качеством на предприятии.
Принятые в августе 2001 г. российские стандарты в области обеспечения качества аутентичны международным стандартам и имеют одинаковые индексы обозначения.
В 1993 г. в рамках ИСО был создан ТК-207 «Управление охраной окружающей среды», который в 1996 г. принял комплекс стандартов ИСО серии 14000 для построения эффективной системы управления окружающей средой и менеджмента экологическими аспектами деятельности предприятий.
Дата добавления: 2018-02-28; просмотров: 1283; Мы поможем в написании вашей работы! |
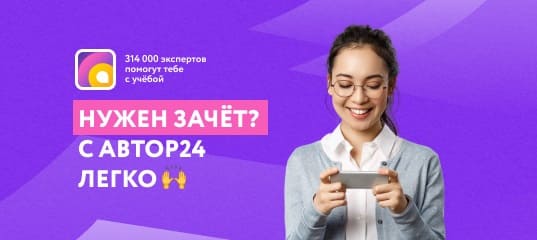
Мы поможем в написании ваших работ!