Уровень технологичности конструкции по шероховатости
поверхности
Рис.1 Рис.2
Рис.3
и 2); удобный подвод режущего инструмента к обрабатываемой поверхности (рис. 3); возможность применения высокопроизводительного прочного и жёсткого инструмента; такое разделение обрабатываемых поверхностей от чёрных, при котором исключается обработка чёрных поверхностей при наличии допустимых погрешностей в размерах заготовки (рис. 4 и 5); свободный выход режущего инструмента при обработке на проход (рис. 6 и 7); возможность одновременной установки нескольких деталей машин для обработки (рис.8); возможность применения нормального или типизированного инструмента.
В ряде случаев в целях снижения стоимости материала следует заменять целые детали литыми армированными или составными, т.е. сборочными узлами (рис. 9).
![]() |
![]() |
Рис.4
Рис. 5
![]() |
![]() |
Рис. 6
![]() |
![]() |
Рис.8
Рис. 7
Рис.9
Применительно к элементарным поверхностям деталей машин можно предъявить следующие технологические требования к конструкции.
Плоскости. 1. Конфигурация обрабатываемых плоских поверхностей должна обеспечивать по возможности равномерный и безударный съем стружки (рис. 10).
2. Размеры обрабатываемых плоскостей должны соответствовать раз
мерам нормальных фрез, т.е. ширины обрабатываемых поверхностей должны
быть унифицированы в соответствии с нормальным рядом диаметров торцевых фрез или длин вальцевых фрез.
|
|
3. В случае, когда не предусмотрен выход для режущего инструмента,
переходная часть должна соответствовать размерам и виду поверхности режущего инструмента (рис. 11 и 12)
![]() |
![]() |
![]() |
![]() |
Рис. 10
Рис. 11
4. Обрабатываемые плоскости должны быть по возможности взаимно
параллельны или перпендикулярны.
5. На сопряжения плоскостей следует делать фаски, а не галтели (рис.13).
![]() |
![]() |
![]() |
Рис. 12 Рис. 13
Фасонные поверхности. 1. Радиусы вогнутых и выпуклых поверхностей (рис. 14) должны соответствовать размерам нормализованных полукруглых выпуклых и вогнутых фрез.
2. При обработке фасонных поверхностей копированием должен быть обеспечен выход инструмента (рис. 15).
![]() |
![]() |
Рис. 14
Рис. 15
Пазы, гнезда и уступы. 1. Следует избегать применения глухих пазов (рис. 16)
![]() |
Рис. 16
2. Пазы должны по возможности допускать обработку на проход
(Рис. 17).
3. При невозможности обработки на проход переходная часть паза
должна соответствовать радиусу фрезы (рис. 18).
![]() |
Рис. 17 Рис. 18
4. Основание паза должно представлять собой плоскую или цилиндрическую поверхность.
|
|
5. Глубина и ширина пазов должны выбираться в соответствии с размерами нормализованных пазовых фрез.
6. Следует избегать пазов с односторонним разрывом (рис. 19).
7. Пазы следует располагать по возможности в одной плоскости (рис. 20)
![]() |
![]() |
Рис. 19
Рис. 20
8. Радиусы закругления у основания гнезд должны быть одинаковыми по
всему периметру (рис. 21) и должны назначаться в соответствии с раз
мерами нормализованных фрез.
9. Следует избегать фасонных, а также глубоких обрабатываемых гнезд;
глубина гнезда не должна превышать трех диаметров концевой фрезы.
10.Поверхности уступов должны быть взаимно перпендикулярны, а конфигурация перехода между ними должна соответствовать конфигурации режущего инструмента (рис. 22).
![]() |
![]() |
Рис.21 Рис. 22
Отверстия. 1. Отверстия должны быть по возможности сквозными.
2. Конфигурация глухих отверстий должна соответствовать конструкции применяемого инструмента: сверла, зенкера, развертки (рис. 23)
3. Отверстия следует располагать так, чтобы можно было применять
сверла нормализованной длины (рис. 24).
![]() |
![]() |
Рис. 23
Рис. 24
4. Отношение длины к диаметру отверстий должно допускать сверление без повторных вводов и выводов сверла.
|
|
5. Следует обеспечить нормальный вход и выход инструмента в соответствии с рис. 25 в отличие от рис. 26.
![]() |
![]() |
Рис. 25 Рис. 26
6. Отверстия должны располагаться не ближе определенного размера к стенке детали: (рис. 27), а отверстия для соединительных болтов
где D2 - диаметр описанной окружности гайки.
5. Расстояние между отверстиями при применении многошпиндельных
![]() |
![]() |
Рис. 27
Рис. 28
головок не должно быть меньше 25 мм.
8. Следует унифицировать расположение и размеры отверстий во фланцах в целях применения многошпиндельных головок.
Количество отверстий во фланцах следует устанавливать с расчетом применения нормальной трех - или четырехшпиндельной сверлильной головки с последовательным поворотом.
9.В стенках деталей следует избегать наклонного расположения отверстий.
10 Отверстия должны быть расположены так, чтобы можно было удобно, разместить кондукторные втулки.
11. При расположении нескольких отверстий на одной оси следует
уменьшать последовательно их размеры на величину, превышающую при
пуск на обработку предшествующего отверстия (рис. 28): D2 = D1— ZD1—),
где ZD1 — припуск на обработку предшествующего отверстия;) — наибольшее смещение осей в заготовке.
|
|
В тех случаях, когда обеспечить ступенчатое расположение отверстий не удаётся, допускаются в условиях серийного производства отверстия одного размера.
12. В случае обработки нескольких отверстий на одной оси расположение их должно обеспечивать возможность постановки направлений для
инструмента (рис. 29).
13. Следует избегать в деталях отверстий с длиной 1 > 10d.
14. Следует избегать конструкций деталей, имеющих два и более точ-
ных параллельных глубоких отверстия.
15. Бобышки под отверстия 0А следует выполнять овальными с тем,
чтобы с учётом соответствующего смещения была обеспечена нужная толщина стенок (рис. 30).
16. Размеры отверстий в пазах следует делать меньше размеров ширины
пазов на 0,5—1 мм.
17. Следует по возможности избегать применения фасонных отверстий
в корпусных деталях, обрабатываемых на агрегатных станках (рис. 31).
18. В фасонных деталях наиболее точную ступень отверстия следует
делать сквозное (рис. 32).
![]() |
![]() |
Рис. 29
Рис.30 Рис.31
19. Конструкция вогнутой сферической поверхности должна быть такой, чтобы при обработке её не было нулевых скоростей резания (рис. 33).
![]() |
![]() |
![]() |
![]() |
Рис. 32 Рис. 33
20. Следует по возможности избегать галтелей, заменяя их фасками или
притуплением кромок (рис. 34).
Наложение фаски целесообразно выполнять свёрлами, для чего угол фаски следует назначать в соответствии с углом при вершине сверла.
21. В отверстиях (рис. 35), обрабатываемых на сверлильных и агрегатных
станках, следует избегать канавок.
![]() |
![]() |
Рис. 34
Рис. 35
22. Следует избегать применения механически обрабатываемых выточек. При наличии литых выточек диаметр их должен быть выбран так, чтобы при максимальном смещении обработанного отверстия не приходилось обрабатывать выточку (рис. 36).
Рис. 36
Дата добавления: 2015-12-21; просмотров: 22; Мы поможем в написании вашей работы! |
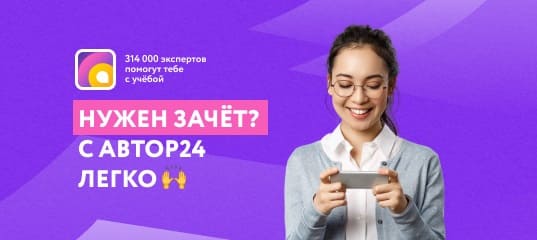
Мы поможем в написании ваших работ!