З.4 Технология прокатки алюминиевых сплавов
Листы толщиной свыше 5 мм подвергают прокатке в горячем состоянии.
При листовой прокатке листы тоньше 3,5 мм в горячем состоянии обычно не катают из-за их быстрого остывания. Такие листы, как правило, получают холодной прокаткой, которая обеспечивает высокое качество поверхности и большую точность по толщине. Чаще всего холодную прокатку ведут рулонным способом до толщины 0,1- 0,12 мм.
Одна из проблем при получении тонких листов и лент- разнотолщинность, на ЗАО «ALCOA СМЗ» два стана холодной прокатки: «SIMAG 1800» - содержит 5 клетей и «SIMAG 2300» одноклетьевой непрерывный стан. С целью снижения разнотолщинности автоматическая система управления станом контролирует (измеряет) разнотолщинность в центре и по краям проката и управляет противоизгибным устройством валков, а так же системой охлаждения валков.
Листы из алюминиевых сплавов могут быть двух видов: плакированные и не плакированные. Плакированный лист имеет тонкое поверхностное покрытие из чистого алюминия для повышения коррозионной стойкости.
Плакированными изготовляют листы из сплавов Д1, Д16, В95 как наименее стойких к коррозии. Толщина плакирующего слоя составляет,примерно, 2-4 % от высоты слитка.
Рис. 17- Схема наложения планшет пли плакировке
Плакирование листа осуществляется следующим образом – большие грани слитка выравнивают фрезерованием, затем обезжиривают и высушивают. Затем на них сверху и снизу накладывают листы (планшеты) из чистого алюминия толщиной 20-40 мм (при высоте основного металла 300-400 мм). После нагрева такого комплекта его подвергают горячей прокатке. На первых проходах происходит сварка планшет с основным металлом. После дальнейшей прокатки до конечной толщины получают лист, покрытый тонким слоем чистого алюминия. Сварка планшет с основным металлом происходит за счет образования металлических связей при высоких температурах и давлении. Прокаткой также изготавливают и не плакированные листы.
|
|
Рассмотрим технологию изготовления плакированного листа.
1. Фрезерование слитка осуществляют по большим и малым граням слитка;
2. Мойка слитков осуществляется в моечных камерах горячей водой (80-90 Со) под большим давлением;
3. Сушка слитков осуществляется горячим воздухом в сушильной камере;
4. Наложение планшет из АДО и их предварительный обжим –гибка кромок осуществляется на специальном оборудовании;
5. Нагрев перед прокаткой осуществляется либо в электрических печах, либо в газовых (печах с шагающими балками), температура нагрева составляет 0,7 То С плавления.
6. Горячая прокатка на семи клетьевом полунепрерывном стане горячей прокатки кварто 2800;
|
|
Нагретый слиток подается из печи к прокатному стану по рольгангу. Прокатка ведется последовательно в первой реверсивной клети до толщины 150-200 мм, затем во второй реверсивной клети до толщины 30-90 мм. После чего полученный раскат обрезают на гильотинных ножницах с переднего торца, затем передают в 5-и клетьевую непрерывную. группу, где осуществляется деформация металла одновременно во всех клетях за один проход.
Рис. 18- 7-ми клетьевой стан горячей прокатки «КВАРТО 2800 »
При выходе из последней клети, боковые кромки полосы обрезают дисковыми ножницами. Далее, в зависимости от толщины катаемой полосы и назначения проката, его направляют либо на приемный рольганг, где подвергают разрезке гильотинными ножницами при толщине больше 5 мм, либо полосу сматывают в рулон с помощью подпольной моталки при толщине менее 5 мм. После горячей прокатки на стане «КВАРТО 2800» рулон может быть направлен на дальнейшую обработку по следующим маршрутам;
а) получение горячее- катанных листов;
б) получение холодно-катанных листов.
а) Горячекатаные листы
7. Предварительная резка рулонов на листы.
Осуществляют на специальных линиях резки, где производят размотку рулона и разрезку на листы предварительной длины;
|
|
Рис. 19- Линия резки
8. Термическая обработка. По требованию заказчика листы могут быть подвергнуты отжигу, либо закалке и старению (в зависимости от марки сплава).
Закалке подвергаются сплавы Д1, Д16, В95. Закалку осуществляют путем нагрева листов в специальных вертикальных закалочных печах (ВЗП), где лист располагают в вертикальной плоскости. После нагрева листы подвергают резкому охлаждению в ванне с охлаждающей жидкостью (вода с «хромпиком») методом окунания. Ванна располагается под печью в полу цеха, а сама печь- установлена над ванной.
Отжигу подвергаются листы из сплавов: АМГ2, АМЦ, АД31, и др. практически все алюминиевые сплавы по желанию заказчика. Листы укладываются на поддон в стопу и направляют в печь отжига с защитной атмосферой.
Рис. 20- Термическая печь отжига
После термообработки осуществляют промежуточный контроль качества поверхности листов на наличие на поверхности пузырей (вздутий), особенно на плакированных листах. ГОСТом определено допустимое количество пузырей на один квадратный дециметр. Если требования ГОСТ выполняются, лист считается годным и направляется на дальнейшую обработку, в противном случае он бракуется;
|
|
9. Отделказаключается в прокате листов в холодном состоянии в двухвалковом прокатном стане с полированными валками. В результате лист приобретает блестящую поверхность;
10. Правказаключается в придании листу плоскостности, планшетности. Правку производят методом растяжения (увеличения длины листа на 2-4%) в растяжных машинах Рис.- 21;
Рис. 21- Правка растяжением
11. Резкав меру- резка листа на окончательный размер в соответствии с заданием. Срезают переднюю и заднюю части листа, приблизительно по 100 мм, которые испорчены зажимными губками растяжной машины.
Если листы должны подвергается закалке и естественному старению, то после правки и резки листы вылеживаются не менее суток, а затем поступают на контроль. Листы которые подвергаются искусственному старению после правки и резки направляются в печь старения, а после этого на контроль. Листы, прошедшие отжиг или не имеющие никакой термической обработки после резки сразу поступают на контроль;
12. Контролькачества осуществляют по следующим параметрам: контроль геометрии, контроль разнотолщинности, контроль механических свойств, микро и макроструктурный анализ (по необходимости), качество поверхности (полосы, пятна, царапины);
13. Упаковка.В зависимости от требований технических условий упаковка может осуществляться различными вариантами:
1) перекладывание листов сухой или промасленной бумагой и далее упаковка стопы листов в фольгу;
2) перекладывание листов влагостойкой бумагой, обертка фольгой, укладка в деревянные ящики;
3) перекладывание листов бумагой, стягивание стопы струбцинами, обертка бумагой снаружи и укладка в деревянные ящики.
14. Сдача на склад готовой продукции.
б) Холоднокатаные листы
7. Укрупнение рулонов.Осуществляется на линии «ЛУР» - линия укрупнения рулонов. Здесь осуществляют размотку рулона, обрезку боковых кромок, при необходимости, сварку двух рулонов встык из свариваемых сплавов (кроме Д1, Д16, В95) и смотку в новый рулон. Укрупнение рулонов, то есть сваривание, осуществляют с целью повышения производительности станов холодной прокатки;
Рис. 22- Линия укрупнения рулонов
8. Холодная прокаткаосуществляется на двух типах станов (ЗАО “АЛКОА-СМЗ”):
а) Пяти клетьевом непрерывном стане 1800 «SIMAG» Рис.23;
б) Одно клетьевом непрерывном стане кварто 2300 «SIMAG» Р. Температура холодной прокатки не превышает 50 градусов С.
Прокатка осуществляется с использованием двух моталок.
Рис. 23- Стан холодной прокатки кварто 1800 «SIMAG»
Скорость полосы на выходе 25-30 м/с. Такой стан имеет автоматическую систему управления, которая в процессе прокатки согласовывает скорость вращения валков в соседних клетях. Система контролирует разно толщинность полосы и управляет противоизгибными устройствами, а также системой охлаждения валков для уменьшении разнотолщинности полосы;
9. Термическая обработка. По требованию заказчика осуществляют либо закалку + последующее искусственное или естественное старение, либо отжиг. Если нет требований по термообработке то заказчик получает холоднокатаный нагартованный лист.
Рис. 24- Линия непрерывной термообработки ЛНТО
Для термической обработки используют специальную машину:
линию непрерывной термообработки – ЛНТО, здесь осуществляют нагрев под закалку и охлаждение водяным душем, а, отжиг при необходимости. После термообработки осуществляется правка на правильной машине и резка на листы гильотинными ножницами;
10. Контроль качества;
11. Упаковка;
12. Сдача на склад готовой продукции.
Дата добавления: 2015-12-20; просмотров: 176; Мы поможем в написании вашей работы! |
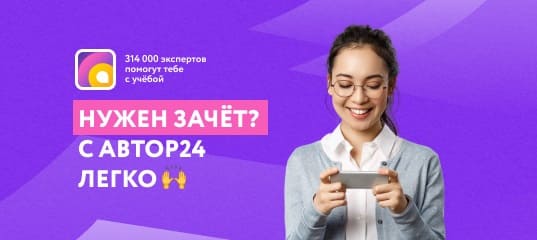
Мы поможем в написании ваших работ!