Продольная прокатка
Общие сведения
Прокатка — технологический процесс пластического деформирования тел, между вращающимися приводными валками. Слова "приводными валками" означают, что энергия необходимая для осуществления деформации передается через валки, соединенные через редуктор с двигателем прокатного стана. С точки зрения сортамента (совокупность катанных профилей) прокатку делят нагруппы: 1) сортовой прокат 2) листовой прокат 3) специальные виды проката и 5) периодический прокат.
В качестве исходной заготовки под прокатку используют литую заготовку, при обработке которой на черновых станах получают блюмы и слябы. При листовой прокатке алюминиевых сплавов в качестве исходной заготовки используется плоский слиток с предварительно обработанной механическими методами поверхностью.
1) Сортовой прокат (рис. 1), в свою очередь, можно разделить на профили массового потребления и профили специального назначения. К первой группе профилей относят круглую квадратную,.шестигранную, полосовую и угловую сталь, проволоку, швеллеры, двутавровые балки и др. Ко второй группе рельсы, профили особой формы, применяемые в строительстве (шпунтовые сваи и др.), машиностроении (автообод, кольцо автообода, опорная планка направляющего ножа трактора др.) и других областях техники.
Рис. 1- Профили сортового проката
1 — квадратный; 2 — круглый; 3 — полосовой; 4 — угловой; 5- двутавровый; 6-швеллерный; 7 — рельс железнодорожный; 8 — рельс трамвайный; 9 — балочный; 10 — швеллерный равной толщины с изгибом полок; 11 — опорная планка направляющего колеса трактора; 12 — зетовый профиль; 13 — шпунт
|
|
2) Листовой прокат в зависимости от толщины листов разделяют на две основные группы: h >4 мм толстолистовой, h <4 мм тонколистовой;
3) Периодический прокат;
4) Специальный прокат: бандажи, шары, цельнокатаные колеса и др.
Прокатке подвергается до 90% всей выплавленной стали и большая часть цветных металлов. Причем большинство продукции получается продольной прокаткой.
С точки зрения реализации выделяют три основных способа прокатки: продольную, поперечную и поперечно винтовую.
Рис. 2- Схема продольной прокатки на двухвалковом стане
1- рабочие валки; 2-заготовка;
3- прокатанная полоса;
ОО 1 - геометрическая ось прокатки
ХХ 1 - ось прокатки
При продольной прокатке заготовка деформируется между валками, вращающимися в разные стороны и перемещающиеся перпендикулярно геометрической оси прокатки.
При поперечной прокатке валки, вращаются в одном направлении, придают заготовке вращение. При этом подаваемая вдоль оси заготовка деформируется - обжимается.
|
|
Рис. 3- Поперечная прокатка
При поперечно-винтовой прокатке валки расположены под углом и сами сообщают заготовке при деформировании не только вращательное, но и поступательное движение.
Рис. 4- Поперечно-винтовая прокатка
При всех схемах прокатки металл подвергается деформации только на некотором участке (в очаге деформации), который по мере вращения валков и движения заготовки перемещается по ней. В процессе прокатки уменьшается толщина заготовки при одновременном увеличении длины и ширины.
Продольная прокатка
Способ продольной прокатки является наиболее распространенным. При продольной прокатке полоса подводится к валкам, вращающимся в разные стороны, и втягивается в зазор между ними за счет сил трения на контактной поверхности. Полоса обжимается по высоте и принимает форму зазора (калибра) между валками. При этом способе прокатки полоса перемещается только вперед, то есть совершает только поступательное движение.
Рис. 5- Схема продольной прокатки: α- угол захвата металла валками, АВ - дуга захвата.
Рис. 6- Вид продольной прокатки в плане
С точки зрения деформации процесс продольной прокатки характеризуется следующими параметрами:
|
|
γ=h0/hk - коэффициент обжатия.
β=bk/b0- коэффициент уширения.
µ=lk/l0- коэффициент удлинения.
Рис.7 Схема продольной прокатки
Процесс прокатки делится на две стадии: начальную –захват металла валками и установившуюся. На начальной стадии при касании заготовки и инструмента возникает сила "N", стремящаяся вытолкнуть заготовку. Одновременно с силой "N" возникает сила трения "Т", захватывающая заготовку в зазор между валками. Процесс прокатки начнется или не начнется в зависимости от соотношения проекций сил "Т" и "N" на ось прокатки.
При горячей прокатки стали α не должно превышать 200 , при холодной 3-40 .Угол захвата α зависит прежде всего от величины обжатия γ=h0/hk, природы материала, граничных условий,скорости прокатки, диаметра валков др.
На установившейся стадии после захвата валками заготовка деформируется в зоне ограниченной АВ А1В 1 и приобретает размеры и форму, соответствующую зазору между валками.
Прокатка является непрерывным процессом, при котором в каждый последующий момент в зазор между валками поступает новый объем прокатываемого металла. Установлено, что в большинстве случаев скорость полосы на выходе из валков V1 больше окружности валков Vв , а скорость полосы на входе в валки V0 меньше горизонтальной составляющей окружной скорости валков Vв соsα, где α угол захвата. Поскольку выполняется неравенство V1 >Vв >V0, то в очаге деформации должно существовать хотя бы одно сечение, в котором скорость течения полосы будет равна горизонтальной составляющей скорости валка. Это сечение NN' называют нейтральным сечением, а центральный угол γ, определяющий положение этого сечения нейтральным углом.
|
|
A
Рис. 8- Зона опережения и отставания при прокатке
Зона опережения - участок очага деформации NBB/N/ (II), в котором средняя скорость металла V1 выше горизонтальной составляющей окружной скорости валков Vв.В зоне опережения силы трения, действующие на прокатываемый металл от валков, направлены против движения материала они реактивны. Скорость выхода прокатываемого металла из валков на 2-6% выше окружной скорости валков. Превышение скорости выхода металла из валков V1 по сравнению с окружной скоростью валков Vв называют опережением и определяют соотношением:
Зона отставания – участок очага деформации ANN/A/ (I) в котором скорость металла на входе V0 меньше, чем горизонтальная составляющая окружной скорости валков в точке «А» V0 < Vв соsα. Здесь металл отстает в своем перемещении от перемещения поверхности бочки валка. Отставанием называют отношение разности горизонтальной проекции окружной скорости валка Vв соsα и скорости входа металла V0 к величине Vв соsα и определяют по формуле:
Sот= (Vв cos α - Vв) / Vв cos α
3. 2 Прокатные станы для продольной прокатки
Рис.9 Схема рабочей клети и привода прокатного стана
Рис. 10- Непрерывный 5-ти клетьевой прокатный стан
На непрерывном прокатном стане клети установлены одна за другой на одинаковом расстоянии. В процессе прокатки заготовка деформируется одновременно во всех клетях, каждая со своим обжатием. В каждой последующей клети скорость вращения валков больше, чем в предыдущей. При этом необходимо выполнять условие: чтобы скорость выхода полосы из предыдущей клети должна быть равна скорости входа полосы в последующую клеть. В противном случае между соседними клетями будет наблюдаться либо обрыв полосы, либо образование петель.
Рис. 11- 7-ми клетьевой полунепрерывный прокатный стан
На полунепрерывном прокатном стане первая и вторая клети- реверсивные, т.е. в каждой клети прокатку можно в прямом и обратном направлении.Полунепрерывный прокатный стан - это совмещение реверсивного и непрерывного станов. Примером служит семи клетьевой полунепрерывный стан горячей прокатки «Кварто 2800» на «АLCOA-СМЗ».
Прокатные валки
Инструментом для прокатки являются валки, которые в зависимости от прокатываемого профиля могут быть:
· гладкими (для изготовления листов, ленты и т.д.);
· ручьевыми (для получения сортового проката).
Материал валков:
· при горячей прокатке мягких материалов используется - серый чугун, модифицированный чугун
· для обжимных станов,работающих в более тяжелых условиях при больших контактных давлениях, используются стали 40Х, 60ХН.
· При холодной прокатке, где контактные давления наибольшие используются инструментальные стали 9Х, 9ХФ, 9Х2, 9Х2МФ, иногда ШХ15.
Валки состоят из бочки (рабочая часть валка), шейки (цапфа) и трефы.
а)
б)
Рис. 12- Валки для продольной а) и сортовой б) прокатки
На каждой паре ручьевых валков обычно размещают несколько калибров.
Для размещения подшипников валков (бочки которых соприкасаются или почти соприкасаются при прокатке),при диаметре шейки валков соизмеримых с диаметром бочки, конструктивно остается очень мало места. Кроме того, при прокатке в подшипниках валков возникают чрезвычайно большие удельные давления, во много раз превышающие удельные давления в подшипниках машин другого назначения. Из-за ограниченных размеров шейки валка и подшипников, а также больших нагрузок к подшипникам при прокатке,к конструкции подшипниковых узлов прокатных станов предъявляют особые требования.
Подшипники прокатных станов можно разделить на две группы: скольжения и качения. Подшипники скольжения конструктивно выполняют двух видов: открытыми и закрытыми; подшипники качения применяют роликовые, с коническими и реже со сферическими цилиндрическими роликами. При горячей прокатке на обжимных и сортовых станах, валки которых установлены на подшипниках скольжения открытого типа, применяют интенсивное охлаждение эмульсией как бочки, так и шеек валков. Вкладыши подшипников изготавливают из текстолита.
Дата добавления: 2015-12-20; просмотров: 44; Мы поможем в написании вашей работы! |
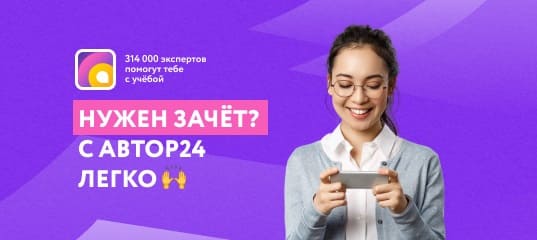
Мы поможем в написании ваших работ!