Заготовка под прокатку
Получение слитка
Исходной заготовкой при прокатке являются слитки: стальные массой до 60 т и до 15 т для цветных металлов и сплавов.
При прокатке сортовых профилей стальные слитки прокатываются на обжимных станках - блюмингах для получения заготовок примерно квадратного сечения (блюмов) от 450х450мм до 150х150 мм. Блюмы в дальнейшем прокатываются на сортовых станах, в которых заготовка последовательно проходит через ряд калибров, постепенно приобретая форму и размеры требуемого профиля.
Заготовкой для горячей прокатки алюминиевых сплавов в листопрокатном цехе является слиток, имеющий форму сляба с размерами: толщина = Но, ширина = Во, длина = Lо Рис.13
Рис. 13- Плоский слиток
Эти размеры заготовки назначаются технологом листопрокатного цеха в рамках тех- условий и стандартов, имеющихся в литейном производстве. В литейных цехах существует номенклатура размеров заготовок под которые имеется оснастка.
Но - толщина заготовки ограничивается свойствами алюминиевого сплава, способом прокатки вдоль оси или поперек, а так же максимальным раствором валков.
Во - ширина заготовки назначается в зависимости от ширины конечной полосы в соответствии с заказом.
Lо - длина заготовки определяется максимальным весом слитков, подлежащих прокатке на данном прокатном стане.
Отливка слитков в литейном цехе производится на специальных литейных машинах методом полунепрерывного литья, в состав которой входит: колодец глубиной до 10 м., кристаллизатор, который формирует поперечное сечение слитка по длине, фильтры для фильтрации расплава и устройство для регулирования скорости разливки и скорости опускания поддона Рис.14.Из одного слитка можно изготовить одну, две и более заготовок под прокатку.
|
|
Рис. 14- Схема литейной машины для полунепрерывной разливки алюминиевых сплавов
Для отливки плоских слитков из алюминиевых сплавов применяются два вида кристаллизаторов.
Кристаллизатор скольжения (КС). При отливке слитков жидкий металл касается стенок, формирующего отверстия кристаллизатора. При застывании и перемещении слитка сверху вниз, его поверхность скользит вдоль стенок кристаллизатора, при этом поверхность слитка получается в виде наплывов каплевидной формы. Эту грубую поверхность с большим количеством дефектов и удаляют фрезерованием на глубину до 15 мм с каждой плоскости. Потери металла, снижение выхода годного – недостаток КС.
Электромагнитный кристаллизатор (ЭМК)
Электромагнитный кристаллизатор имеет индуктор,который размещается вокруг формирующего слиток отверстия кристаллизатора.
Рис.15 Индуктор ЭМК
|
|
При подаче переменного тока через индуктор в жидком металле возникает индукционный ток того же направления, что и в индукторе. Известно, что параллельные токи отталкиваются, этими силами жидкий расплав «отжимается» от стенок кристаллизатора, при этом образуется небольшой зазор. Таким образом боковые стенки слитка не касаются стенок кристаллизатора. За счет сил поверхностного натяжения боковые стенки жидкого расплава приобретают гладкую поверхность, в таком виде и происходит затвердевание расплава. В результате поверхность всех граней застывшего слитка получается гладкой и ровной.
Преимущества:
а) прокатку можно вести без фрезерования слитка (для мягких сплавов и неответственных заказов);
б) в случае фрезерования слитка глубина снимаемого слоя значительно меньше, чем при фрезеровании слитков после кристаллизации в КС;
в) индукционные токи способствуют перемешиванию жидкого расплава, что приводит к измельчению зерна готового слитка.
После окончания литья слитки извлекают из литейного колодца мостовым краном и отправляют на гомогенизацию.
Гомогенизация
Это термическая операция, которая заключается в нагреве до температуры близкой к температуре солидуса Тs и выдержку слитка при этой температуре до 24 часов. В результате гомогенизации выравнивается химический состав по всему объему слитка, разрушается за счет рекристаллизации дендридная структура, что придает металлу равномерность механических свойств.
|
|
Гомогенизация осуществляется в специальных печах, которые называются гомогенизационными колодцами. Слиток располагается вертикально. После гомогенизации слитки остывают и направляются на следующую операцию - резка.
Резка слитков на заготовки под прокатку
Рис. 16- Резка слитков на заготовки под прокатку
Слиток имеет литейную ось. Длина слитка может составлять приблизительно 8 м. Для получения заготовки под прокатку слиток режут на заготовки. Отрезанная часть отправляется в прокатный цех (размеры отрезанной части задаются технологом прокатного цеха). При этом необходимо учитывать в каком направлении относительно литейной оси слитка будет прокатка.
Прокатка может быть: продольная- вдоль литейной оси и поперечная - поперек литейной оси. В зависимости от этого назначается длина отрезаемой заготовки. Резка слитков на заготовки под прокатку осуществляется на специальной линии резки. После резки слитка на заготовки их направляют на склад листопрокатного цеха. Механическая обработка заготовок осуществляется в условиях листопрокатного цеха.
Дата добавления: 2015-12-20; просмотров: 27; Мы поможем в написании вашей работы! |
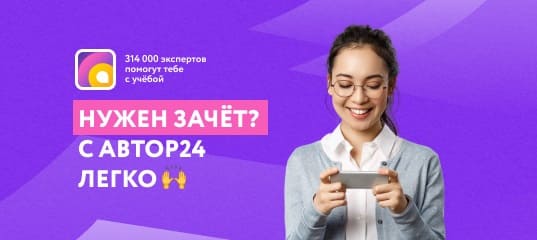
Мы поможем в написании ваших работ!