Организация автоматизированного производства.
Виды и организационно-технические показатели автоматических линий.
Автоматическая линия (АЛ) – это система машин-автоматов, размещенных по ходу технологического процесса и объединенных автоматическими механизмами и устройствами для решения задач транспортировки, накопления заделов, удаления отходов, изменения ориентации. АЛ оснащена системой управления.
В зависимости от используемого состава оборудования выделяют несколько типов АЛ.
· Автоматические линии из агрегатных станков отличаются высокой эффективностью, сокращенными сроками проектно-монтажных работ, высоким уровнем надежности работы агрегатов, так как их собирают из унифицированных агрегатых узлов, отлаженных в ранее действовавших системах.
· Автоматические линии из универсальных станков – автоматов и полуавтоматов – проектируются на базе поточных линий с оснащением механизмами автомитической загрузки-выгрузки деталей.
· Автоматические линии из специального оборудования высокоэффективны при использовании в условиях массового производства. Овычно для процесса из создания характерны длительные сроки проектирования и освоения, значительные затраты.
· Автоматические линии с программируемым устройством оснащены числовым программным управлением, делающим их экономически эффективными не только в массовом и крупносерийном производстве, но и в мелкосерийном производстве.
|
|
· Автоматические линии из многоцелевых станков (гибкие автоматические линии) представляют собой высокоэффективные автоматизированные гибкие технологические комплексы с управлением от ЭВМ. Они свидетельствуют о высоком уровне гибкости, электронизиции и интеграции производства.
· Роторные линии являются разновидностью АЛ из специального оборудования, создаются на основе роторных машин и роторных транспортирующих устройств. Обработка изделий совмещена во времени с непрерывной транспортировкой заготовок по операциям технологического процесса.
· Робототехнические комплексы, которые отличаются от традиционных средств автоматизации широкой универсальностью (многофункциональность) и гибкостью (мобильностью) при переходе без дополнительных затрат на выполнение принципиально новых операций.
В зависимости от способа обеспечения ритмичности различают синхронные(жесткие) АЛ, для которых характерна жесткая межагрегатная связь и единый цикл работы станков, и несинхронные (гибкие) АЛ с гибкой межагрегатной связью.
Каждый станок в этом случае снабжен индивидуальным магазином-накопителем межоперационных узлов.
В зависимости от использования приспособлений-спутников различают спутниковые и бесспутниковые АЛ, а от количества технологических потоков – однопоточные (неветвящиеся) и многопоточные (ветвящиеся).
|
|
В соответствии с функциональным назначением автоматические линии могут быть механообрабатывающими, механосборочными, сборочными, заготовительными, термическими, контрольно-измерительными, упаковочными, консервационными и комплексными.
![]() |
Цикловая (номинальная) производительность АЛ при условии полного отсутствия простоев:
Где Nц - число изделий, изготавливаемых за один цикл.
![]() |
Тц – время одного цикла.
Где tо и tв - основное и вспомогательное время.
С учетом простоев и затрат времени на регулировку и подналадку механизмов потенциальная производительность АЛ:
![]() |
Где tоб.т. – время технического обслуживания.
![]() |
Учет потерь времени по организационным причинам позволяет определить фактическую производительность:
Где tоб.о. – время организационного обслуживания.
![]() |
Технический уровень АЛ определяется коэффициентом технического использования:
Данный коэффициент отражает уровень цикловых непроизводительных затрат времени и внецикловых простоев из-за плановых и внеплановых ремонтов.
|
|
![]() |
Организационно-технический уровень определяется коэффициентом общего использования:
Тогда:
![]() |
Важной характеристикой АЛ является равномерный выпуск продукции в единицу времени, особенно обеспечение ритмичности работы. Такт (или ритм) АЛ определяется суммарным временем обработки to, установки, закрепления и снятия изделия tв, транспортировки его с одной позиции на другую tтр.
![]() |
Автоматические линии расчленяются на участки, и синхронизация обеспечивается по группам операций на каждом участке. Для этого создается компенсационный задел.
Где tк.з. – время создания компенсационного задела.
rmax, rmin – больший и меньший такты смежных участков.
Δr – допустимая величина колебания усредненных тактов.
![]() |
Таким образом, допустимая величина отклонения тактов на смежных участках:
Организация и планирование ремонтного обслуживания производства.
В условиях высокомеханизированного производства конечные результаты работы предприятий определяются техническим состоянием производственного оборудования. В процессе эксплуатации оборудование подвергается моральному и физическому износу, за счет чего происходит снижение его мощности, производительности и точности, нарушение хода производственного процесса.
|
|
Для поддержания оборудования в работоспособном состоянии необходимо проводить качественное техническое обслуживание и ремонт. Специфика и большая трудность работ по ремонту, техническому обслуживанию и модификации технологического оборудования обуславливает необходимость создания на предприятиях специальной ремонтной службы – отдела главного механика (ОГМ), основная задача которой – поддержание оборудования в постоянной эксплуатационной готовности, обеспечение максимального сокращения простоев оборудования в ремонте и минимальных затрат на ремонт, техническое обслуживание и модернизацию. Производственная и организационная структура ремонтной службы предприятия зависит от типа и объемов производства, технологических характеристик и модельности оборудования, кооперации при выполнении ремонтных работ.
В состав ремонтного хозяйства предприятия входят:
q Ремонтно-механический цех (РМЦ), выполняющий ремонт технологического оборудования, изготовление запасных частей, находящийся в подчинении главного механика предприятия;
q Электроремонтный цех (ЭРЦ), выполняющий ремонт электрооборудования и подчиненный главному энергетику;
q Ремонтно-строительный цех (РСЦ), подчиненный отделу капитального строительства, выполняющий ремонт зданий и сооружений;
q Цеховые ремонтные базы (ЦРБ), подчиненные механику цеха;
q Смазочное хозяйство, склады оборудования и запасных частей.
В функции ремонтной службы входят: паспортизация оборудования, его аттестация, техническая и материальная подготовка ремонтных работ, планирование, организация и выполнение работ по обслуживанию, ремонту и модернизации оборудования.
Организация ремонтного хозяйства основывается на системе планового предупредительного ремонта и рациональной эксплуатации технологического оборудования (ППР). В основе ППР лежат плановость и профилактика.
Основные работы по поддержанию оборудования в эксплуатационной готовности подразделяются на ремонтные работы и техническое обслуживание.
Техническое обслуживание включает комплекс операций по поддержанию работоспособности оборудования при использовании его по назначению, хранению и транспортировке. В процессе технического обслуживания по заранее разработанному графику выполняются плановые осмотры оборудования, смена и пополнение масел, проверка геометрической и технологической точности, промывка механизмов станков, очистка от пыли.
Плановое обслуживание выполняется во время работы оборудования или во время установленных перерывов без нарушения производственного процесса. Осмотры проводят слесари-ремонтники и электрики с привлечением (в случае необходимости) рабочих, работающих на этом оборудовании. Проверку точности выполняет персонал отдела технического контроля и главного механика.
Неплановое техническое обслуживание, включающее замену отказавших деталей, восстановление их работоспособности, должно по возможности выполняться без перерывов в работе обслуживаемого оборудования или в обеденные перерывы.
Ремонтные работы подразделяются на три вида:
· Капитальные (К);
· Средние (С);
· Текущие (Т).
Текущий ремонт выполняется для обеспечения или восстановления работоспособности оборудования и состоит в замене и восстановлении изношенных деталей, регулировании механизмов. Он проводится без простоя оборудования (в нерабочее время).
Средний ремонт включает частичный разбор агрегата, капитальный ремонт отдельных сборочных единиц, сборку, регулирование и испытания.
При капитальном ремонте производится полная разборка агрегата со снятием его с фундамента и заменой всех изношенных деталей и узлов с последующей сборкой и испытанием под нагрузкой.
Ремонты, вызываемые отказами оборудования, называются неплановыми (аварийными). При надлежащей организации системы ППР неплановые ремонты, как правило, не должны иметь место.
Основой ЕСППР является нормативная база, позволяющая наиболее рационально планировать и осуществлять техническое обслуживание и ремонт оборудования.
К основным ремонтным нормативам относятся: длительность и структура ремонтного плана, длительность межремонтного периода, категория сложности ремонта, трудоемкость и материалоемкость ремонтных работ, нормативы продолжительности простоя оборудования в ремонте.
Ремонт оборудования и его техническое обслуживание выполняются в определенной последовательности, образуя повторяющиеся ремонтные циклы. Ремонтный цикл – это период времени от момента ввода до первого капитального ремонта или между двумя выполняемыми капитальными ремонтами.
Основными характеристиками ремонтного цикла являются его структура и продолжительность. Под структурой ремонтного цикла понимается перечень и последовательность выполнения ремонтных работ в период между двумя капитальными ремонтами.
Продолжительность межремонтного цикла определяется:
,
где – нормативная величина ремонтного цикла (определяется возрастом оборудования, для металлорежущих станков возрастом от 10 до 20 лет
);
– коэффициенты, учитывающие соответственно тип производства, вид обрабатываемого материала, условия эксплуатации, весовые характеристики оборудования.
Длительность межремонтного периода и межосмотрового периода
определяется на основе продолжительности межремонтного цикла, количества в цикле средних, текущих ремонтов и осмотров:
;
,
где: – количество в цикле соответственно средних, текущих ремонтов и осмотров.
Степень сложности ремонта оборудования определяется категорией сложности ремонта, зависящей от его конструктивных и технологических особенностей. Категорию сложности любого агрегата устанавливают путем сопоставления его с агрегатом-эталоном.
Для плановых расчетов объемов и трудоемкости ремонтных работ наряду с категорией сложности ремонта применяют понятие ремонтная единица (р.е.)
Для отдельного агрегата категория сложности ремонта и соответствующее этому агрегату число ремонтных единиц совпадают.
Нормативы трудоемкости ремонтных работ устанавливаются для различных типов оборудования с учетом характера работ и видов ремонтных операций на одну ремонтную единицу отдельно по механической и электрической части оборудования. Аналогично определяют потребность в материалах на все виды ремонтов и техническое обслуживание, используя нормы расходов материала, установленные на одну ремонтную единицу для различных видов оборудования.
Одним из наиболее важных направлений, определяющих эффективность работы ремонтной службы, является соблюдение нормативов, продолжительности простоев оборудования в ремонте. Продолжительность простоев зависит от вида ремонта, категории сложности, ремонтируемого агрегата, количественного состава ремонтной бригады, технологии ремонта и организационно-технических условий ремонтных работ. Ремонт оборудования в неавтоматизированном производстве организуют в одну, две или три смены, в зависимости от того, насколько лимитирует производство простой данного оборудования. Ремонт автоматических линий проводят в две или три смены. Учет простоев ведется с момента остановки оборудования для ремонта до приемки его контролерами ОТК по акту.
На основе приведенных нормативов разрабатывают годовые планы ремонтных работ и работ по техническому обслуживанию. Основными показателями плана являются:
q Объем ремонтных работ по цехам и предприятию в целом на год и на каждый месяц;
q Виды ремонтных работ и сроки их выполнения;
q Трудоемкость ремонтных работ, производительность труда;
q Численность ремонтных рабочих по профессиям, фонд их заработной платы;
q Себестоимость ремонтных работ.
Среднегодовой объем ремонтных работ в расчете на одну ремонтную единицу:
,
где – трудоемкость соответственно капитального, среднего, текущего ремонта и осмотра одной ремонтной единицы, час;
– продолжительность ремонтного цикла, час.
При переходе на двух видовую структуру ремонта среднегодовой объем ремонтных работ снижается примерно на 7%. На основе рассчитанного объема работ определяется необходимое количество рабочих. Например, количество слесарей для проведения плановых ремонтов и осмотров оборудования определяется:
,
где – годовой объем слесарных работ, н/час;
– действительный фонд времени работы одного рабочего, час/год;
– коэффициент выполнения норм.
При организации ремонтных работ на предприятии применяются централизованная, децентрализованная и смешанная система.
При централизованной системе все виды ремонта и частично межремонтное обслуживание производится силами ремонтно-механического цеха. Применяется эта система на предприятиях единичного и мелкосерийного производства, при ремонтной сложности оборудования предприятия до 5000 ремонтных единиц.
При децентрализованной системе техническое обслуживание и все виды ремонта производятся силами цеховых ремонтных баз под руководством механика цеха. В РМЦ изготавливаются сменные и запасные части, узлы для модернизации, нестандартное оборудование. Эту систему целесообразно применять на предприятиях крупносерийного и массового производства.
Смешанная система характеризуется тем, что капитальный ремонт и изготовление запасных частей производится в РМЦ, а техническое обслуживание и остальные виды ремонта – силами комплексных ремонтных бригад ЦРБ. Это система ремонта целесообразна для больших предприятий с количеством оборудования от 500 до 800 р.е., а также при ремонте сложного автоматического оборудования.
Капитальный ремонт однотипного оборудования, сосредоточенного в одном цехе, целесообразно проводить в цехах, где оно эксплуатируется. Ремонт автоматических линий, тяжелого (нетранспортабельного) оборудования следует производить силами комплексных бригад на месте его установки.
Кроме указанных форм организации, ремонт может производиться: централизованно силами ремонтных заводов, специализированных на определенных типомоделях оборудования с изготовлением запасных частей и отдельных узлов, централизованно силами выездных бригад, организуемых при специализированных заводах для ремонта особо тяжелого, уникального оборудования.
Выбор рациональной организационной структуры ремонтной службы предприятия осуществляется на основе данных о мощности, сложности и точности технологического оборудования, территориальном расположении предприятий, возможности кооперации, при выполнении ремонтных работ.
Основными направлениями повышения эффективности ремонтной службы являются:
§ Совершенствование технологии организации ремонтных работ за счет их механизации, применения типовых технологических процессов, прогрессивных методов ремонта – узлового, последовательно-узлового и поточного;
§ Экономии вспомогательных материалов и запасных частей;
§ Совершенствования материально-технической базы ремонтной службы;
§ Улучшения контроля качества ремонтных работ;
Прогрессивным направлением организации ремонтного хозяйства является создание ремонтных баз на предприятиях-изготовителях оборудования, развитие фирменного ремонта станков с ЧПУ и автоматизированных комплексов, межзаводское кооперирование в области ремонта, модернизация оборудования, изготовление запасных частей.
Дата добавления: 2015-12-17; просмотров: 7; Мы поможем в написании вашей работы! |
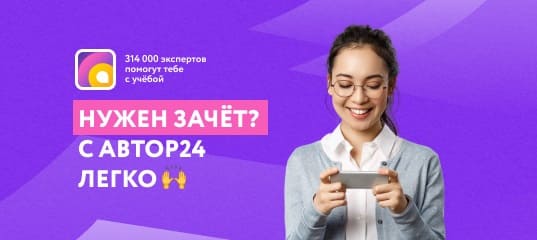
Мы поможем в написании ваших работ!