Нормативные требования к методам испытаний
В разных странах применяют существенно отличающиеся друг от друга методы определения основных физико-механических свойств цемента – прочности, водопотребности, сроков схватывания, равномерности изменения объёма, которые дают различные результаты при испытаниях одних и тех же цементов.
В России и странах СНГ для оценки соответствия применяемых цементов межгосударственным стандартам, действующим в настоящее время на территории большинства этих стран (ГОСТ 10178, ГОСТ 22266, ГОСТ 965, ГОСТ 11052, ГОСТ 25328, ГОСТ 969, ГОСТ 15825) следует применять методы испытаний, регламентированные ГОСТ 310.1 – ГОСТ 310.4.
В настоящее время Европейским Комитетом по стандартизации (CEN) приняты европейские стандарты серии EN 196, регламентирующие единые для стран ЕС методы физико-механических испытаний цемента в пластичных растворах с использованием полифракционного песка и специального оборудования. В странах СНГ вся нормативная база строительства основана на характеристиках цемента, получаемых при испытании образцов, изготовленных из более жёстких растворов с использованием монофракционного песка.
С целью нормативного обеспечения производителей цемента в странах СНГ методиками испытаний своей продукции, позволяющими получить аналогичные со странами ЕС результаты для сопоставимой оценки строительно-технических свойств цемента, разработан ГОСТ 30744 "Цементы. Методы испытаний с использованием полифракционного песка". Указанный стандарт применяют, если в контрактах (договорах) предусмотрена поставка цемента по EN 197-1, а также по требованию потребителя (заказчика) и для целей сертификации цемента на соответствие EN 197-1.
|
|
Для определения прочности цемента по ГОСТ 30744 предусмотрено использование полифракционного песка по ГОСТ 6139, требования которого соответствуют требованиям EN 196-1.
Проведённые в России сравнительные испытания цементов на прочность по ГОСТ 30744 и европейским стандартам свидетельствуют об идентичности результатов с учётом критериев достоверности, установленных EN 196-1.
Испытания цементов для оценки их соответствия межгосударственным стандартам, действующим на территории России и большинства стран СНГ
ГОСТ 310.1 устанавливает общие положения при испытании цементов для определения следующих показателей:
- тонкости помола цемента;
- нормальной густоты и сроков схватывания цементного теста;
- равномерности изменения объема цемента;
- предела прочности при изгибе и сжатии образцов-балочек, изготовленных из цементного раствора.
Отбор проб производят по ГОСТ 30515.
Пробу цемента, отобранную для испытаний, доставляют в лабораторию в плотно закрывающейся таре, защищающей цемент от увлажнения и загрязнения посторонними примесями.
|
|
Пробы цемента до испытания хранят в сухом помещении.
Перед испытанием каждую пробу просеивают через сито с сеткой № 09 по ГОСТ 6613. Остаток на сите взвешивают и отбрасывают. Массу остатка в процентах, а также его характеристику (наличие комков, кусков дерева, металла и пр.) заносят в рабочий журнал. После просеивания пробу цемента перемешивают.
Испытания следует проводить в помещениях с температурой воздуха ()°С и относительной влажностью не менее 50 %. Температура воздуха и влажность должны ежедневно отмечаться в рабочем журнале.
Перед испытанием цемент, песок и воду выдерживают до принятия ими температуры помещения.
Для приготовления и хранения образцов применяют обычную питьевую воду.
Сосуд для отвешивания или отмеривания воды тарируют в смоченном состоянии.
Температура помещения влажного хранения образцов и воды в ваннах должна быть (20±2)°С и ежедневно отмечаться в рабочем журнале.
Цемент и песок отвешивают с точностью до 1 г, воду отвешивают или отмеривают с точностью до 0,5 г или 0,5 мл.
Применение алюминиевых и цинковых форм, чаши, лопаток и т. п. не допускается.
|
|
Определение тонкости помола цемента по остатку на сите производят в соответствии с ГОСТ 310.2.
Тонкость помола определяют просеиванием через сито с сеткой № 008 по ГОСТ 6613-86 с помощью прибора для механического или пневматического просеивания цемента. При отсутствии в лаборатории приборов для механического или пневматического просеивания цемента допускается производить ручное просеивание.
Пробу цемента высушивают в сушильном шкафу при температуре 105-110°С в течение 2 ч. и охлаждают в эксикаторе.
При использовании прибора для механического просеивания отвешивают 50 г цемента с точностью до 0,05 г и высыпают его на сито. Закрыв сито крышкой, устанавливают его в прибор для механического просеивания. Через 5-7 мин от начала просеивания останавливают прибор, осторожно снимают донышко и высыпают из него прошедший через сито цемент, прочищают сетку с нижней стороны мягкой кистью, вставляют донышко и продолжают просеивание.
Операцию просеивания считают законченной, если при контрольном просеивании сквозь сито проходит не более 0,05 г цемента.
Контрольное просеивание выполняют вручную при снятом донышке на бумагу в течение 1 мин.
|
|
Тонкость помола цемента определяют как остаток на сите с сеткой № 008 в процентах к первоначальной массе просеиваемой пробы с точностью до 0,1 %.
Определение тонкости помола цемента по удельной поверхности. В соответствие с ГОСТ 310.2 для проведения данного испытания пользуются прибором для определения удельной поверхности методом воздухопроницаемости типа ПСХ. Испытание производят в соответствии с инструкцией к прибору после предварительного определения плотности цемента.
Определение плотности цемента. Согласно ГОСТ 310.2, перед определением удельной поверхности цемента для определения массы навески, используемой в приборе ПСХ, и выполнения расчётов следует предварительно произвести определение плотности цемента.
Определение плотности осуществляют с помощью прибора Ле-Шателье (см. рис. 3.2). Прибор Ле-Шателье, закрепленный в штативе, помещают в стеклянный сосуд с водой так, чтобы вся его градуированная часть была погружена в воду. Необходимо, чтобы при отсчетах уровня жидкости в приборе температура воды в сосуде соответствовала температуре, при которой производили градуировку прибора. Прибор наполняют обезвоженным керосином до нижней нулевой черты по нижнему мениску. После этого свободную от керосина часть прибора (выше нулевой черты) тщательно протирают тампоном из фильтровальной бумаги.
Отвешивают с точностью до 0,01г 65 г цемента и высыпают его в прибор Ле-Шателье ложечкой через воронку небольшими равномерными порциями до тех пор, пока уровень жидкости в приборе не поднимется до одного из делений в пределах верхней градуированной части прибора.
Для удаления пузырьков воздуха прибор с содержимым вынимают из сосуда с водой и поворачивают его в наклонном положении в течении 10 мин на гладком резиновом коврике. После чего прибор снова помещают в сосуд с водой не менее чем на 10 мин и производят отсчет уровня жидкости в приборе.
Рис. 3.2. Прибор Ле-Шателье для определения плотности цемента
Плотность цемента (gц), г/см3, вычисляют по формуле
(3.5)
где m ц - навеска цемента, г;
V - объем жидкости, вытесненный цементом, см3.
Плотность испытуемого цемента вычисляют с точностью до 0,01 г/см3 как среднее арифметическое значение результатов двух определений, расхождение между которыми не должно превышать 0,02 г/см3.
Определение нормальной густоты цементного теста (ГОСТ 310.3). Для проведения испытания используется прибор Вика с иглой и пестиком, кольцо к прибору Вика, мешалка для приготовления цементного теста.
Прибор Вика (см. рис. 3.3) имеет цилиндрический металлический стержень 1, свободно перемещающийся в обойме станины 2. Для закрепления стержня на требуемой высоте служит стопор-нос устройство 3. Стержень снабжен указателем 4 для отсчета перемещения его относительно шкалы 5, прикрепленной к станине. Шкала имеет цену деления 1 мм.
При определении нормальной густоты цементного теста в нижнюю часть стержня вставляют металлический цилиндр-пестик 6.
При определении сроков схватывания пестик заменяют иглой 7.
Пестик должен быть изготовлен из нержавеющей стали с полированной поверхностью. Игла должна быть изготовлена из стальной жесткой нержавеющей проволоки с полированной поверхностью и не должна иметь искривлений. Поверхность пестика и иглы должна быть чистой.
Рис. 3.3. Прибор Вика (ГОСТ 310.3)
1 - цилиндрический металлический стержень; 2 - обойма станины;
3 - стопорное устройство; 4 - указатель; 5 - шкала; 6 - пестик; 7 - игла
Массу перемещающейся части прибора сохраняют взаимной перестановкой пестика и иглы. Отдельные детали перемещающейся части прибора подбирают таким образом, чтобы их общая масса находилась в пределах (300±2) г.
Размеры иглы и пестика должны соответствовать указанным на рис. 3.4 и 3.5.
Кольцо к прибору Вика и пластинка, на которую устанавливают кольцо, должны быть изготовлены из нержавеющей стали, пластмассы или другого не впитывающего воду материала. Форма и размеры кольца должны соответствовать указанным на рис. 3.6.
Рис. 3.4. Рабочая часть иглы (ГОСТ 310.3)
Рис. 3.5. Рабочая часть пестика (ГОСТ 310.3)
Рис. 3.6. Кольцо к прибору Вика (ГОСТ 310.3)
Мешалка для приготовления цементного теста должна отвечать требованиям соответствующих технических условий.
При отсутствии в лаборатории механизированной мешалки для приготовления цементного теста применяют чашу сферической формы, изготовленную из нержавеющей стали (см. рис. 3.7).
Лопатку для ручного перемешивания цементного теста изготовляют из упругой нержавеющей стали. Основные размеры лопатки указаны на рис. 3.8.
Рис. 3.7. Чаша для приготовления цементного теста
Рис. 3.8. Лопатка для перемешивания цементного теста
Кольцо и пластинку перед началом испытаний смазывают тонким слоем машинного масла.
Для ручного приготовления цементного теста отвешивают 400 г цемента, высыпают в чашу, предварительно протертую влажной тканью. Затем делают в цементе углубление, в которое вливают в один прием воду в количестве, необходимом (ориентировочно) для получения цементного теста нормальной густоты. Углубление засыпают цементом и через 30 с после прилипания воды сначала осторожно перемешивают, а затем энергично растирают тесто лопаткой.
Продолжительность перемешивания и растирания составляет 5 мин с момента приливания воды.
Цементное тесто на механической мешалке готовят в соответствии с прилагаемой к мешалке инструкцией.
После окончания перемешивания кольцо быстро наполняют в один прием цементным тестом и 5-6 раз встряхивают его, постукивая пластинку о твердое основание. Поверхность теста выравнивают с краями кольца, срезая избыток теста ножом, протертым влажной тканью. Немедленно после этого приводят пестик прибора в соприкосновение с поверхностью теста в центре кольца и закрепляют стержень стопорным устройством, затем быстро освобождают его и предоставляют пестику свободно погружаться в тесто. Через 30 с с момента освобождения, стержня производят отсчет погружения по шкале. Кольцо с тестом при отсчете не должно подвергаться толчкам. При несоответствующей консистенции цементного теста изменяют количество воды и вновь затворяют тесто, добиваясь погружения пестика на требуемую глубину. Количество добавляемой воды для получения теста нормальной густоты определяют с точностью до 0,25 %.
Нормальной густотой цементного теста считают такую его консистенцию, при которой пестик прибора Вика, погруженный в кольцо, заполненное тестом, не доходит на 5-7 мм до пластинки, на которой установлено кольцо.
Нормальную густоту цементного теста характеризуют количеством воды затворения, выраженным в процентах от массы цемента.
Определение сроков схватывания цемента в соответствии с ГОСТ 310.3 проводят на цементном тесте нормальной густоты с помощью прибора Вика, в котором пестик заменяется на иглу.
Иглу прибора доводят до соприкосновения с поверхностью цементного теста нормальной густоты, уложенного в кольцо. В этом положении закрепляют стержень стопором, затем освобождают стержень, давая игле свободно погружаться в тесто. В начале испытания, пока тесто находится в пластичном состоянии, во избежание сильного удара иглы о пластинку допускается слегка ее задерживать при погружении в тесто. Как только тесто загустеет настолько, что опасность повреждения, иглы будет исключена, игле дают свободно опускаться. Момент начала схватывания определяют при свободном опускании иглы.
Иглу погружают в тесто через каждые 10 мин, передвигая кольцо после каждого погружения для того, чтобы игла не попадала в прежнее место. После каждого погружения иглу вытирают.
Во время испытания прибор должен находиться в затененном месте, где нет сквозняков, и не должен подвергаться сотрясениям.
Началом схватывания цементного теста считают время, прошедшее от начала затворения (момента приливания воды) до того момента, когда игла не доходит до пластинки на 1-2 мм. Концом схватывания цементного теста считают время от начала затворения до момента, когда игла опускается в тесто не более чем на 1-2 мм.
Определение сроков схватывания цементного теста может выполняться на приборе с автоматической записью – в этом случае испытание производят в соответствии с инструкцией, прилагаемой к прибору.
Определение равномерности изменения объёма цемента. Для проведения испытания по ГОСТ 310.3 используется бачок для испытания кипячением, ванна с гидравлическим затвором, а при необходимости – автоклав с рабочим давлением не ниже 2,1 МПа.
Внутри бачка помещается съемная решетчатая полка для лепешек, которая находится на расстоянии не менее 5 см от дна бачка. Уровень воды в бачке должен перекрывать лепешки на 4-6 см в течение всего времени кипячения. Бачок с водой нагревают на любом нагревательном приборе, обеспечивающем доведение воды в бачке до кипения за 30-45 мин.
Ванны с гидравлическим затвором для хранения образцов изготавливают из стойкого к коррозии материала (оцинкованная сталь). В ваннах устанавливают решетки для размещения на них образцов. Под решеткой всегда должна быть вода (см. рис. 3.9).
Рис. 3.9. Ванна с гидравлическим затвором для испытания на равномерность изменения объёма цемента по ГОСТ 310.3
Для испытания на равномерность изменения объема цемента готовят тесто нормальной густоты. Две навески теста массой 75 г каждая, приготовленные в виде шариков, помещают на стеклянную пластинку, предварительно протертую машинным маслом. Постукивают ею о твердое основание до образования из шариков лепешек диаметром 7-8 см и толщиной в середине около 1 см. Лепешки заглаживают смоченным водой ножом от наружных краев к центру до образования острых краев и гладкой закругленной поверхности.
Лепешки хранят в течение (24±2) ч с момента изготовления в ванне с гидравлическим затвором, а затем подвергают испытанию кипячением.
По истечении времени хранения по две цементные лепешки вынимают из ванны, снимают с пластинок и помещают в бачок, с водой на решетку. Воду в бачке доводят до кипения, которое поддерживают в течение 3 ч, после чего лепешки в бачке охлаждают и производят их внешний осмотр немедленно после извлечения из воды.
Цемент соответствует требованиям стандарта в отношении равномерности изменения объема, если на лицевой стороне лепешек не обнаружено радиальных, доходящих до краев, трещин или сетки мелких трещин, видимых невооруженным глазом или в лупу, а также каких-либо искривлений и увеличения объема лепешек. Искривления обнаруживают при помощи линейки, прикладываемой к плоской поверхности лепешки, при этом обнаруживаемые искривления не должны превышать 2 мм на краю или в середине лепешки. Допускается в первые сутки после испытаний появление трещин усыхания, не доходящих до краев лепешек, при условии сохранения звонкого звука при постукиваний лепешек одна о другую. Образцы лепешек, выдержавших и не выдержавших испытание на равномерность изменения объема, приведены на рис. 3.10.
В случае, когда содержание оксида магния MgО в клинкере, из которого был изготовлен испытуемый цемент, составляет более 5 %, следует дополнительно провести испытание равномерности изменения объема в автоклаве с рабочим давлением не менее 2,1 МПа. Это испытание проводят только для цементов, выдержавших испытание кипячением.
Изготовление и хранение лепёшек, предназначенных для испытания в автоклаве, производят так же, как для лепёшек, испытываемых кипячением. Автоклавную обработку производят вместо кипячения по следующему режиму: подъем давления от атмосферного до 2,1 МПа - в течение 60-90 мин, выдержка при давлении 2,1 МПа - в течение 3 ч, снижение давления от 2,1 МПа от атмосферного - около 60 мин. После этого лепешку извлекают из автоклава, охлаждают до температуры помещения и немедленно ее осматривают.
Лепешки, выдержавшие испытания
на равномерность изменения объема
Лепешки, не выдержавшие испытания
на равномерность изменения объема
Разрушение Радиальные трещины
Лепешки, не выдержавшие Лепешки, выдержавшие испытания
испытания
Искривление Трещины усыхания
Рис. 3.10. Внешний вид лепёшек цементного теста, выдержавших и не выдержавших испытание на равномерность изменения объёма (ГОСТ 310.3)
Определение предела прочности цемента при изгибе и сжатии по ГОСТ 310.4. Для проведения испытания используются: мешалка для перемешивания цементного раствора (лопастная или бегунковая – см. рис. 3.11 и 3.12), чаша и лопатка (см. рис. 3.7 и 3.8), встряхивающий столик и форма-конус (см. рис. 3.13), штыковка (см. рис. 3.14), формы для изготовления образцов-балочек (см. рис. 3.15), насадка к формам (см. рис. 3.16), вибрационная площадка, прибор для испытания на изгиб образцов-балочек, пресс для определения предела прочности при сжатии, пластинки для передачи нагрузки, пропарочная камера (при определении прочности при пропаривании).
Рис. 3.11. Схема лопастной мешалки для перемешивания цементного раствора (ГОСТ 310.4)
1 - чаша; 2 - ведомая лопасть; 3 - ведущая лопасть; 4- лопасть-скребок
____________
* Предельно допустимый размер при износе.
Рис. 3.11. Бегунковая мешалка для перемешивания цементного раствора (ГОСТ 310.4)
1 - основание; 2 - чаша; 3 - ось чаши; 4 - ось бегунка; 5 -бегунок
_____________
* 7 мм при износе.
Конструкция встряхивающего столика должна обеспечивать плавный без перекосов подъем подвижной части на высоту (10±0,5) мм и ее свободное падение с этой высоты до удара о неподвижную преграду. Число встряхиваний за рабочий цикл определения расплыва должно составлять 30 с периодичностью одно встряхивание в секунду.
Пример конструкции столика приведен на рис. 3.13. При помощи кулачка 1, получающего движение от привода, перемещающаяся часть, состоящая из диска 2 и штока 3, поднимается на заданную высоту и затем совершает свободное падение до удара о неподвижную преграду - станину 4. Диск 2 должен быть выполнен из коррозионно-стойкого металла со шлифованной рабочей поверхностью.
Рис. 3.13. Встряхивающий столик и форма-конус (ГОСТ 310.4)
1 - кулачок; 2 - диск; 3 - шток; 4 - станина; 5 - форма-конус с центрирующим устройством; 6 -насадка
___________
* Для испытания цемента с расплывом конуса более 200 мм применяют диск диаметром 300 мм. Указанный допуск - для изготовления.
Рис. 3.14. Штыковка
1 - стержень; 2 – рукоятка
Насадка к формам балочек должна обеспечивать плотное прижатие стенок формы к ее основанию и формы в целой к столу вибрационной площадки. Допускается применять насадку с разделительными перегородками.
Рис. 3.15. Формы для изготовления образцов-балочек (ГОСТ 310.4)
____________
* Допуск для изготовления формы.
Рис. 3.16. Насадка к формам балочек (ГОСТ 310.4)
Вибрационная площадка для уплотнения цементного раствора в формах балочек должна иметь вертикальные колебания с амплитудой (0,35±0,03) мм, частотой колебаний 3000 в минуту и быть укомплектована реле времени.
Для испытания образцов балочек на изгиб могут быть использованы приборы любой конструкции, удовлетворяющие следующим требованиям. Средняя скорость нарастания испытательной нагрузки на образец должна быть (0,05±0,01) кН/с (0,12±0,02) МПа/с в пересчете на единицу площади приведенного сечения балочки. Захват для установки образца должен быть снабжен цилиндрическими элементами, изготовленными из стали твердостью 56...61 HRCэ.
Нижние опорные элементы должны иметь возможность поворота относительно горизонтальной оси, лежащей на нижней опорной плоскости образца и являющейся осью ее продольной симметрии (см. рис. 3.17).
Рис. 3.17. Схема расположения образца на опорных элементах при испытании на изгиб (ГОСТ 310.4)
Для определения предела прочности образцов при сжатии могут быть использованы прессы, любой конструкции с предельной нагрузкой до 500 кН.
Нажимные пластиной для передачи нагрузки на половинки образцов-балочек (см. рис. 3.18) должны быть изготовлены из стали твердостью 56...61 НRСэ.
Рис. 3.18. Пластинки для передачи нагрузки на половинки образцов-балочек при испытании на сжатие (ГОСТ 310.4)
При изготовлении образцов следует вначале произвести определение консистенции цементного раствора. Для этого отвешивают 1500 г стандартного песка по ГОСТ 6139, 500 г цемента и 200 г воды (В/Ц=0,40).
Согласно ГОСТ 6139 стандартный монофракционный песок для испытаний цемента должен удовлетворять следующим требованиям:
1) содержание оксида кремния (SiO2) - не менее 98%;
2) потери при прокаливании - не более 0,3%;
3) влажность - не более 0,2%;
4) содержание глинистых и илистых примесей - не более 1,0%;
5) зерновой состав песка должен соответствовать требованиям, указанным в табл. 3.17.
Таблица 3.17
Зерновой состав стандартного монофракционного песка для испытаний цемента
Размер ячеек сита, мм | Остаток на сите, % |
0,9 0,5 | Не более 1 Не менее 92 |
Компоненты загружают в предварительно протертую влажной тканью чашу лопастной мешалки в следующей последовательности: песок, вода, цемент. Чашу устанавливают на мешалку и производят перемешивание в течение (120±10) с.
При использовании бегунковой мешалки отвешенные песок и цемент высыпают в предварительно протертую мокрой тканью сферическую чашу, перемешивают цемент с песком лопатой в течение 1 мин.
Затем в центре сухой смеси делают лунку, вливают в нее воду в количестве 200 г (В/Ц=0,40), дают воде впитаться в течение 0,5 мин и перемешивают смесь в течение 1 мин.
При применении бегунковой мешалки допускается перемешивать цемент и песок до и после приливания воды в мешалках, обеспечивающих хорошее перемешивание раствора и не изменяющих зерновой состав песка.
При применении бегунковой мешалки раствор переносят в предварительно протертую мокрой тканью чашу мешалки и перемешивают в последней в течение 2,5 мин (20 оборотов чаши мешалки).
По окончании перемешивания заполняют раствором форму-конус на половину высоты и уплотняют 15 штыкованиями металлической штыковкой. Затем наполняют конус раствором с небольшим избытком и штыкуют 10 раз.
После уплотнения верхнего слоя избыток раствора удаляют ножом, расположенным под небольшим углом к торцевой поверхности конуса, заглаживая с нажимом раствор вровень с краями конуса, затем конус снимают в вертикальном направлении. Нож предварительно протирают влажной тканью.
Раствор встряхивают на столике 30 раз за (30±5) с, после чего штангенциркулем измеряют диаметр конуса по нижнему основанию и двух взаимно перпендикулярных направлениях и берут среднее значение. Расплыв конуса с В/Ц=0,40 должен быть в пределах 106-115 мм. Если расплыв конуса окажется менее 106 мм, количество воды увеличивают для получения расплыва конуса 106-108 мм. Если расплыв конуса окажется более 115 мм, количество воды уменьшают для получения расплыва конуса 113-115 мм.
Водоцементное отношение, полученное при достижении расплыва конуса 106-115 мм, принимают для проведения дальнейших испытаний.
Из цементного раствора, приготовленного как указано выше, изготавливают образцы-балочки. Непосредственно перед изготовлением образцов внутреннюю поверхность стенок форм и поддона слегка смазывают машинным маслом. Стыки наружных стенок друг с другом и с поддоном формы промазывают тонким слоем солидола или другой густой смазки. На собранную форму устанавливают насадку и промазывают снаружи густой смазкой стык между формой и насадкой.
Для каждого установленного срока испытаний изготовляют по три образца (одна форма).
Для уплотнения, раствора форму балочек с насадкой закрепляют в центре виброплощадки, плотно прижимая ее к плите. Допускается устанавливать две формы, симметрично расположенные относительно центра виброплощадки, при условии одновременного их заполнения.
Форму по высоте наполняют приблизительно на 1 см раствором и включают вибрационную площадку. В течение первых 2 мин вибрации все три гнезда формы равномерно небольшими порциями заполняют раствором. По истечении 3 мин от начала вибрации виброплощадку отключают. Форму снимают с виброплощадки и избыток раствора удаляют ножом расположенным под небольшим углом к поверхности укладки, заглаживая с нажимом раствор вровень с краями формы. Образцы маркируют. Нож предварительно должен быть протерт влажной тканью.
После изготовления образцы в формах хранят (24±1) ч в ванне с гидравлическим затвором или в шкафу, обеспечивающем относительную влажность воздуха не менее 90 %.
По истечении времени хранения образцы осторожно расформовывают и укладывают в ванны с питьевой водой и горизонтальном положении так, чтобы они не соприкасались друг с другом.
Вода должна покрывать образцы не менее чем на 2 см. Воду меняют через каждые 14 сут. Температура ее при замене должна быть (20±2)°С; как и при хранении образцов.
Образцы, имеющие через (24±1) ч прочность, недостаточную для расформовки их без повреждения, допускается вынимать из формы через (48±2) ч, указывая этот срок в рабочем журнале.
По истечении срока хранения образцы вынимают из воды и не позднее чем через 30 мин подвергают испытанию. Непосредственно перед испытанием образцы должны быть вытерты.
Для определения предела прочности при изгибе образец устанавливают на опорные элементы прибора таким образом, чтобы его горизонтальные при изготовлении грани находились в вертикальном положении. Образцы испытывают в соответствии с инструкцией, приложенной к прибору.
Предел прочности при изгибе вычисляют как среднее арифметическое значение двух наибольших результатов испытания трех образцов.
Полученные после испытания на изгиб шесть половинок балочек сразу же подвергают испытанию на сжатие. Половинку балочек помещают между двумя пластинками таким образом, чтобы боковые грани, которые при изготовлении прилегали к стенкам формы, находились на плоскостях пластинок, а упоры пластинок плотно прилегали к торцевой гладкой плоскости образца (см. рис. 3.19). Образец вместе с пластинами центрируют на опорной плите пресса. Средняя скорость нарастания нагрузки при испытании должна быть (2,0±0,5) МПа/с.
Предел прочности при сжатии отдельного образца вычисляют как частное от деления величины разрушающей нагрузки (в кгс) на рабочую площадь пластинки (в см2) т. е. на 25 см2.
Рис. 3.19. Положение образца между нажимными пластинками при испытании на сжатие
1 -нижняя плита пресса; 2 -пластинки; 3 - верхняя плита пресса
Предел прочности при сжатии вычисляют как среднее арифметическое значение четырех наибольших результатов испытания 6 образцов.
Для определения прочности цемента при пропаривании приготавливают цементно-песчаный раствор, укладывают его в формы и уплотняют, как сказано выше. После уплотнения формы помещают в пропарочную камеру, где выдерживают в течение (120±10) мин при температуре (20±3)°С (при отключенном подогреве).
Для предохранения поверхности образца от попадания конденсата формы накрывают пластинами, выполненными из коррозионно-стойких материалов и не оказывающими давления на образцы.
Пропарку ведут по следующему режиму:
- равномерный подъем температуры до (85±5)°С... (180± 10) мин
- изотермический прогрев при температуре (85±5)°С... (360±10) мин
- остывание образцов при отключенном подогреве... (120±10) мин.
Затем открывают крышку камеры.
Через (24 ± 2) ч с момента изготовления образцы расформовывают и сразу же испытывают.
Определение водоотделения цемента производят по ГОСТ 310.6. Для этого отвешивают 350 г цемента и 350 г воды. Воду выливают в фарфоровый стакан, затем в стакан в течение 1 мин высыпают навеску цемента, непрерывно перемешивая содержимое металлическим шпателем. Полученное цементное тесто перемешивают еще 4 мин и осторожно переливают в градуированный цилиндр. Цилиндр с цементным тестом ставят на стол и тотчас же отсчитывают объем цементного теста. В течение всего времени испытаний цилиндр должен стоять неподвижно и не подвергаться толчкам и встряхиванием.
Объем осевшего цементного теста (в мл) отмечают через 2 ч после первого отсчета и через каждые 30 мин при дальнейших наблюдениях. При совпадении двух последних отсчетов дальнейшее наблюдение прекращают, а содержимое цилиндра выливают.
Коэффициент водоотделения (объемный) (К в) в процентах вычисляют по формуле
, (3.6)
где а - первоначальный объем цементного теста, см3;
в - объем осевшего цементного теста, см3.
Производят два параллельных определения. Водоотделение определяют как среднее из двух определений. Отклонение в результатах параллельных определений не должно превышать 1 %.
Испытания цементов для оценки соответствия европейскому
стандарту
ГОСТ 30744 регламентирует проведение испытаний для определения тонкости помола, нормальной густоты цементного теста, сроков схватывания, равномерности изменения объёма и прочности цементов на соответствие требованиям европейского стандарта EN 197-1.
Определение тонкости помола по ГОСТ 30744, как по остатку на сите, так и по удельной поверхности не имеет принципиальных отличий от проведения этих испытаний по ГОСТ 310.2.
Определение нормальной густоты и сроков схватывания по ГОСТ 30744 проводится также с использованием прибора Вика (см. рис. 3.20). Конструкция и размеры устанавливаемого на нём пестика для определения нормальной густоты цементного теста практически такие же, как и при проведении испытания по ГОСТ 310.3. В отличие от ГОСТ 310.3, предусмотрено использование двух игл: длинной для определения начала схватывания и короткой для определения конца схватывания (см. рис. 3.21). Для приготовления цементного теста используется специальный смеситель.
При определении нормальной густоты время от начала затворения до начала погружения пестика должно составлять 4 мин. Глубину погружения пестика фиксируют через 30с после освобождения стержня прибора Вика. Нормальной густотой, как и при проведении испытания по ГОСТ 310.3, считают такую консистенцию, при которой пестик не доходит до дна на 5-7 мм.
Началом схватывания считается время от начала затворения до момента, когда длинная игла прибора Вика при проникновении цементное тесто не доходит до дна на 3-5 мм.
а
![]() | б
![]() |
Рис. 3.20. Прибор Вика (ГОСТ 30744)
а — положение кольца при определении нормальной густоты и начала схватывания;
б — положение кольца при определении конца схватывания
1 — кольцо; 2 — пестик; 3 — пригруз; 4 — цилиндрический металлический стержень; 5 — обойма станины; 6 — стопорное устройство; 7 — пластинка; 8 — шкала, 9 — указатель; 10 — игла; 11 — основание станины
![]() | ![]() |
Рабочая часть пестика | Рабочая часть длинной иглы |
![]() | Рис. 3.21 Приспособления к прибору Вика для определения нормальной густоты и сроков схватывания (ГОСТ 30744) |
A — канал для выхода воздуха Рабочая часть короткой иглы с кольцеобразной насадкой |
Для определения конца схватывания кольцо с цементным тестом, использованное для определения начала схватывания, переворачивают с тем, чтобы определение конца схватывания проводить на ровной поверхности. Погружение короткой иглы выполняют с интервалом 30 мин. Концом схватывания считают время от начала затворения до момента, когда игла проникает в цементное тесто не более чем на 0,5 мм, что соответствует положению иглы, при котором кольцеобразная насадка впервые не оставляет отпечатка на поверхности цементного теста. Результат записывают с округлением до 15 мин.
Равномерность изменения объёма цемента характеризуют величиной расширения образца цементного теста нормальной густоты в кольце Ле-Шателье при кипячении. Испытание проводят параллельно на двух кольцах (см. рис. 3.22). Кольца, предварительно смазанные машинным маслом, заполняют цементным тестом, накрывают сверху пластинами, на которые устанавливают пригруз, и помещают в камеру влажного хранения или в воду на 24 ч. Затем штангенциркулем замеряется начальное расстояние между концами индикаторных игл, кольца освобождают от пластин и пригруза и помещают в бачок для кипячения индикаторными иглами вверх. Воду в бачке доводят до кипения за 30±5 мин и выдерживают кольца в кипящей воде в течение 180±5 мин. Уровень воды в бачке должен быть выше размещённых на подставке колец на 4-6 см. После окончания кипячения кольца извлекают из воды, дают им остыть до температуры помещения и измеряют расстояние между концами индикаторных игл (конечное измерение). Вычисляют разность между значениями конечного и начального измерений расстояний для каждого кольца и принимают их среднеарифметическое значение за расширение в кольце Ле-Шателье.
а
б
в
Рис. 3.22. Кольцо Ле-Шателье (ГОСТ 30744)
а — кольцо Ле Шателье (вид сверху), б — кольцо Ле Шателье с пластинками и пригрузом (вид сбоку), в — схема поверки упругости кольца Ле Шателье
1 — кольцо с прорезью, 2 — индикаторная игла, 3 — пластинка, 4 — пригруз
Определение прочности цемента производят на образцах размером 40х40х160 мм. Для уплотнения раствора в форме используется встряхивающий столик, обеспечивающий подъём платформы стола на 15±0,3 мм и её свободное падение. Число ударов за рабочий цикл должно составлять 60 с частотой один удар в секунду.
Образцы изготавливают из стандартного цементного раствора, состоящего из цемента и стандартного полифракционного песка по ГОСТ 6139, требования к которому соответствуют требованиям EN 196-1, в соотношении 1: 3 по массе при водоцементном отношении, равном 0,50.
Стандартный полифракционный песок состоит из трех (тонкой, средней, крупной) или четырех (тонкой I, тонкой II, средней, крупной) фракций в отношениях, установленных поставщиком.
Стандартный полифракционный песок должен удовлетворять следующим требованиям:
1) содержание оксида кремния (SiO2) - не менее 98%;
2) потери при прокаливании - не более 0,5%;
3) влажность - не более 0,2%;
4) зерновой состав должен соответствовать требованиям, указанным в табл. 3.18.
Таблица 3.18
Зерновой состав стандартного полифракционного песка для испытаний цемента
Размер ячеек сита, мм | Остаток на сите, % |
2,00 1,60 1,00 0,50 0,16 0,08 | 7±5 33±5 67±5 87±5 99±1 |
Стандартный полифракционный песок должен получить сертификат соответствия этого песка эталонному. В качестве эталонного песка для полифракционных песков принимают песок месторождения Чешской меловой области.
Перемешивание раствора осуществляется в специальном смесителе. Уплотнение раствора в формах производят в три слоя путём встряхивания каждого слоя 60 раз на встряхивающем столике. Порядок расформовывания образцов, их хранения, определения прочности образцов на сжатие и изгиб, включая схемы нагружения, принципиально не отличается от требований ГОСТ 310.4.
За прочность при изгибе принимают среднеарифметическое значение результатов испытаний трёх образцов, округлённое до 0,1 МПа, за прочность при сжатии – среднеарифметическое значение результатов испытаний шести половинок образцов-балочек, округлённое до 0,1 МПа. Если один из шести результатов отличается более чем на 10% от среднеарифметического значения, то этот результат исключается и среднеарифметическое значение вычисляется по оставшимся результатам. Если ещё один результат отличается более чем на 10% от среднеарифметического значения оставшихся пяти результатов, то испытание признаётся недействительным.
Список литературы к главе III
1. ГОСТ 125-79 Вяжущие гипсовые. Технические условия
2. ГОСТ 310.1-76 Цементы. Методы испытаний. Общие положения
3. ГОСТ 310.2-76 Цементы. Методы определения тонкости помола
4. ГОСТ 310.3-76 Цементы. Методы определения нормальной густоты, сроков схватывания и равномерности изменения объёма
5. ГОСТ 310.4-81. Цементы. Методы определения предела прочности при изгибе и сжатии
6. ГОСТ 310.6-85 Цементы. Метод определения водоотделения
7. ГОСТ 30744-2001 Цементы. Методы испытаний с использованием полифракционного песка
8. ГОСТ 965-89 Портландцементы белые. Технические условия
9. ГОСТ 969-91 Цементы глинозёмистые и высокоглинозёмистые. Технические условия
10. ГОСТ 1581-96 Портландцементы тампонажные. Технические условия
11. ГОСТ 3476-74 Шлаки доменные и электротермофосфорные гранулированные для производства цементов
12. ГОСТ 4013-82 Камень гипсовый и гипсоангидритовый для производства вяжущих материалов. Технические условия
13. ГОСТ 6139-91 Песок стандартный для испытаний цемента
14. ГОСТ 6266-97 Листы гипсокартонные. Технические условия
15. ГОСТ 9179-77 Известь строительная. Технические условия
16. ГОСТ 10178-85 Портландцемент и шлакопортландцемент. Технические условия
17. ГОСТ 11052-74 Цемент гипсоглинозёмистый расширяющийся
18. ГОСТ 15825-80 Портландцемент цветной. Технические условия
19. ГОСТ 22266-94 Цементы сульфатостойкие. Технические условия
20. ГОСТ 23789-79 Вяжущие гипсовые. Методы испытаний
21. ГОСТ 24640-91 Добавки для цементов. Классификация
22. ГОСТ 24748-81 Изделия известково-кремнезёмистые теплоизоляционные. Технические условия
23. ГОСТ 25328-82 Цемент для строительных растворов. Технические условия
24. ГОСТ 26798.1-96 Цементы тампонажные. Методы испытаний
25. ГОСТ 26798.2-96 Цементы тампонажные типов I-G и I-H. Методы испытаний
26. ГОСТ 26871-86 Материалы вяжущие гипсовые. Правила приёмки. Упаковка, маркировка, транспортирование и хранение
27. ГОСТ 30515-97 Цементы. Общие технические условия
28. ГОСТ 9574-90 Панели гипсобетонные для перегородок. Технические условия
29. ГОСТ 11118-73 Панели из автоклавных ячеистых бетонов для наружных стен зданий. Технические требования
30. ГОСТ 25094-94 Добавки активные минеральные для цементов. Методы испытаний
31. ОСТ 218.2.001-2002 Портландцемент для бетонов искусственных сооружений и дорожных одежд Санкт-Петербургской кольцевой автомобильной дороги. Технические условия
32. ОСТ 21-27-76 Породы карбонатные для производства строительной извести. Технические условия
33. ТУ 21-13-6-89 Добавки к цементу. Добавки-наполнители. Технические условия
34. ТУ 21-26-11-90 Добавки для цементов. Активные минеральные добавки. Технические условия
35. ТУ 5734-072-46854090-98 Цемент напрягающий. Технические условия
36. ТУ 5732-003-24089832-98 Портландцемент безусадочный. Технические условия
37. EN 197-1 Цемент. Состав; технические характеристики и критерии соответствия (Европейский стандарт)
38. Бутт Ю.М. Технология цемента и других вяжущих. М., Стройиздат, 1964.
39. Бутт Ю.М., Сычев М.М., Тимашев В.В. Химическая технология вяжущих материалов. – М.: Высш. школа, 1980.
40. Волженский А.В. Минеральные вяжущие вещества. М., 1986.
41. Горчаков Г.И. Строительные материалы. М., 1981.
42. Домокеев А.Г. Строительные материалы. – М.: Высшая школа, 1989.
43. Кузнецова Т.В., Сычев М.М., Осокин А.П. и др. Специальные цементы. – СПб, Стройиздат, 1997.
44. Рамачадран В., Фельдман Р., Бодуэн Дж. Наука о бетоне: Физико-химическое бетоноведение. – М.: Стройиздат, 1986.
45. Рояк С.М., Рояк Г.С. Специальные цементы. М.: Стройиздат, 1988.
46. Строительные материалы: Справочник / А.С. Болдырев, П.П. Золотов, А.Н. Люсов и др. М.: Стройиздат, 1989.
47. Химия цементов / Под ред. Х.Ф.У. Тейлора. – М., Стройиздат, 1969.
Глава 4. Органические вяжущие материалы
Органические вяжущие материалы – природные или полученные в результате переработки природных материалов вещества, состоящие из смеси высокомолекулярных соединений.
Они могут находиться в жидком, вязко-пластическом или твердом состоянии.
Органические вяжущие материалы применяются для строительства дорожных и аэродромных покрытий, изготовления кровельных и гидроизоляционных материалов, защиты различных материалов от коррозии.
Дата добавления: 2016-01-05; просмотров: 38; Мы поможем в написании вашей работы! |
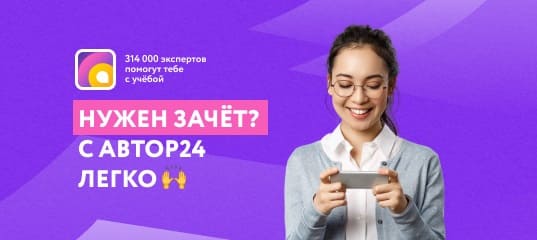
Мы поможем в написании ваших работ!