Исходные данные для проектирования цеха
1. Производственная программа
Данные для составления производственной программы необходимо получать во время прохождения преддипломной практики на базовом предприятии.
Производственную программу составляют в соответствии с заданием на дипломный проект по таблице 1. В программе должны быть указаны: наименование деталей, узлов, агрегатов, подлежащих обработке в данном цехе, их количество, материал, масса заготовки, масса деталей.
Годовую программу выпуска изделий (детали) для которого выполняется расчет механического цеха можно определить по формуле:
(1)
Nв – годовая программа выпуска деталей принятая в дипломном проекте
Nзав – годовая программа выпуска деталей на базовом предприятии
К = 1,3… 3 – коэффициент роста программы, учитывающий возрастание объема выпуска в течение нескольких лет.
Таблица 1.
№ п/п | Наименование детали | Годовая программа выпуска изделий Nв, шт | Марка материала | Количество деталей на одно изделие, n, шт | Количество деталей на годовую программу N= Nв*n, шт | Масса заготовки gз, кг | Масса детали gд, кг | Масса отходов gо, кг |
Деталь N1 | Nв | n1 | n1Nв1 | gз1 | gд1 | gо1 | ||
М | Деталь Nм | Nвм | nм | n1Nвм | gзм | дм | gом |
2.Трудоемкость
Трудоемкость детали или узла, для которых в проекте разрабатывается подробный технологический процесс, определяется расчетом, путем нормирования каждой операции по нормативам времени.
Норма времени должна устанавливаться в расчете на нормальные условия работы т на применение оптимальных режимов резания.
|
|
Для определения общей нормы времени на механическую обработку одной детали предварительно определяют отдельно по каждой операции норму штучного времени на операцию tшт.
[мин] (2)
tо – основное время (технологическое), мин
tвсп – вспомогательное время, мин
tтоб – время на техническое обслуживание рабочего места, мин
tооб – время на организацию обслуживания рабочего места, мин
tф – время на физические потребности, мин
В общем виде формула основного времени имеет следующее выражение:
[мин] (3)
l – расчетная длина обработки в направлении подачи, равная сумме l = l 0 + l вр + l п, мм
l о – длина обрабатываемой поверхности, мм
l вр – длина врезания инструмента, мм
l п – длина перебега инструмента, мм
nо – число оборотов шпинделя в минуту для станков с вращательным движением или число двойных ходов в минуту для станков с прямолинейным движением.
S – подача за один оборот, или за один двойной ход главного движения,
i – число проходов
S мин – подача инструмента за одну минуту.
Вспомогательное время tвсп может быть ручным, машинным или машинно-ручным (например, автоматическое перемещение суппорта станка, установка и снятие обрабатываемой детали с помощью подъемно-транспортных средств).
|
|
Сумма основного tо и вспомогательного времени tвсп составляет оперативное время tоп
tоп = tо + tвсп, мин (4)
Кроме вышеуказанных элементов времени на серийном производстве обязательное предусматривается подготовительно-заготовительное время, которое входит в период штучно-калькуляционного времени и определяется отдельно на всю партию деталей.
(5)
tштк – норма штучно-калькуляционного времени на операцию
tшт – норма штучного времени на операцию
tпз – подготовительно-заготовительное время на партию деталей (т.е. наладочное время операции, настройка станка, смена инструмента, приспособлений0
n – количество деталей в партии.
Размер партии деталей можно рассчитать двумя методами:
Первый – по суммарному подготовительно-заключительному времени и штучному времени на все механические операции тех.процесса.
(6)
∑tпз – суммарное подготовительно-заготовительное время на все операции, мин
∑tшт – суммарное штучное время для изготовления детали, мин
м – число операций, выполненных при обработке детали
α – коэффициент допустимых потерь времени на переналадку оборудования (α = 0,03÷0,1).
|
|
Второй метод – величину партии определяют из расчета пропускной способности сборочного цеха. Отсюда:
(7)
n – количество деталей в партии
N – годовая программа выпуска данных деталей
T – число дней, на которые необходимо иметь запас деталей на складе
Ф – число рабочих дней в году
Сумма штучно-калькуляционного времени по всем операциям составляет общее время обработки детали или трудоемкость мех.обработки детали.
[час] (8)
Трудоемкость по деталям, обрабатываемым в цехе можно принимать по деталям заводской трудоемкости с учетом коэффициента ужесточения норм времени ηу.
(9)
ηу ≈ 0,63 ÷0,8
Учитывая коэффициент ужесточения норм времени можно подсчитать трудоемкость остальных деталей, обрабатываемых в цехе.
Для определения общей трудоемкости по цеху составляется таблица.
Таблица 2.
№ п/п | Наименование детали | Годовая программа выпуска узлов, шт | Количество деталей, узлов | Трудоемкость деталей (час) | Трудоемкость узла (час) | Трудоемкость годовой программы (час) | Формула расчета трудоемкости |
Деталь N1 | N1 | n1 | Т1 | n1Т1 | n1Т1N1 | Опред. путем нормирования | |
М | Деталь Nм | Nм | nм | Тм | nмТм | NмТмNм | ?? |
|
|
(10)
Дата добавления: 2016-01-05; просмотров: 23; Мы поможем в написании вашей работы! |
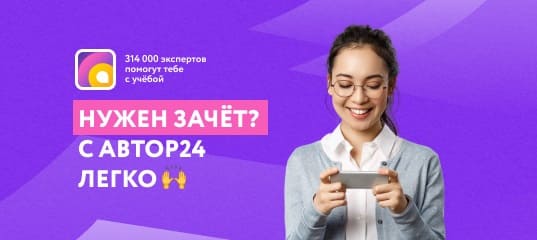
Мы поможем в написании ваших работ!