Проектирование обводообразующих элементов приспособления.
Согласно схеме базирования (рис.3а) верхний поз.3 (рис.2), нижний поз.4 и задний поз.6 профиль имеют базу по внешней поверхности полки. Для реализации этих баз необходимы базирующие обводообразующие элементы.
Обводообразующими элементами приспособления для сборки носка нервюры являются ложементы. Они неподвижно крепятся к каркасу приспособления.
Каждый ложемент должен иметь базовые отверстия (Б.О.) и отверстия для крепления (рис.5а).
Приспособление для сборки носка нервюры будет содержать три ложемента (рис.5а): верхний поз.1, нижний поз.2 и задний поз.3. Разбивка на ложементы может быть и иной, но данная разбивка является оптимальной.
Все ложементы лежат на одной плоскости, которая совпадает с плоскостью полки профиля (рис.5 в)
Б.О. используются при изготовлении ложементов для позиционирования заготовки на станке с ЧПУ. Так же Б.О. необходимы для монтажа ложементов в приспособлении и последующей его проверке.
Ложементы крепятся к каркасу через отверстия для крепления.
Диаметр отверстий для крепления и Б.О. выбирается из следующего ряда: Æ8Н9, Æ12Н9, Æ18Н9. Диаметр зависит от габаритов приспособления.
Ложементы приспособления для сборки носка нервюры будет иметь Б.О. и отверстия для навески Æ18Н9.
Ложементы, как правило, выполняются из материала Д16чТ. Толщина и ширина ложементов зависит от расстояния между соседними точками навески. При задании толщины и ширины ложементов (рубильников) можно руководствоваться таблицей 4.
|
|
Таблица 4
Расстояние между соседними точками навески, мм | Толщина ложемента h, мм | Ширина ложемента b, мм |
менее 200 | 10, 15 | 30-50 |
от 200 до 500 | 15, 20 | 50-80 |
от 500 до 1000 | 80-150 | |
от 1000 до 2000 | 20, 30 | 150-250 |
более 2000 | более 250 |
Необходимо учитывать, что листы материала Д16чТ выпускаются длиной 2500 мм. Поэтому максимальный размер ложемента должен быть не больше габаритов листа. Если возникает потребность в ложементах (рубильниках) длиной более 2500 мм, их необходимо выполнять составными, из нескольких частей. Отдельные части ложемента должны состыковываться между собой через стыковые отверстия.
При проектировании конструкции ложементов необходимо соблюдать единообразие, т.е. диаметры Б.О. и отверстий для навески должны совпадать. Остальные параметры ложементов (ширина, толщина, размеры ушей для навески, радиуса скруглений) так же не должны различаться, кроме тех случаев, когда это вызвано конструктивной или технологической необходимостью.
Ложементы не должны содержать внутренних острых углов без особой необходимости. Например, на рис.5б все внутренние острые углы скруглены радиусами R50.
|
|
Радиус проушин для навески ложементов (рис.5б) выбирают в пределах R30-R35, чтобы они совпадали с радиусом элементов навески (ушей или вилок).
Расстояние между Б.О. и отверстиями для навески должно быть кратно 50 мм (рис.6). Это необходимо для удобства монтажа и последующей проверки приспособления.
Ложементы должны содержать дополнительную справочную информацию, а именно направление полета (Н.П.), оси стрингеров, шпангоутов, риски обозначающие обреза обшивок и кромки деталей, установочные риски и т.д. (рис.7).
Риски служат для облегчения процесса сборки, как приспособления, так и СЕ так как по ним производится ориентация деталей.
Для фиксации прижима уплотнителя (рис.2б, поз.8, рис.4б, поз.8) на ложементах требуется установить дополнительные упоры, т.к. прижим уплотнителя расположен за плоскостью ложементов. Упоры лучше сделать неподвижно зафиксированными на ложементах (рис.8, 9). Как вариант, можно использовать подвижные (выдвижные) упоры, но они значительно усложнят конструкцию, а эффект от их использования будет небольшой. Основная проблема при изготовлении выдвижных упоров для данного случая следующая: полка прижима уплотнителя поз.8 имеет переменную малку, поэтому все упоры будут иметь упорную поверхность с разными углами, что в совокупности с выдвижной конструкцией приведет к значительному усложнению. Неподвижные упоры с разной малкой выполнить намного проще.
|
|
Проектирование каркаса приспособления.
Каркас приспособления состоит из элементов навески рубильников/ложементов (уши, вилки, репера) и рамы.
Элементы навески фиксируются в стаканах рамы карбинольным цементом. Для точного задания местоположения элементов навески используется координатно-монтажный стенд. Он позволяет производить установку с точностью ±0,05 мм.
Рама имеет сварную конструкцию. Основные элементы рамы – палки и колонны выполняются из швеллерных коробок. В некоторых случаях авиационное предприятие может использовать стандартизированные колонны. Для установки рамы в требуемое положение при эксплуатации используются опоры. Они имеют разнообразную конструкцию и могут быть так же стандартизованными.
Первым шагом, при проектировании каркаса приспособления, является расстановка элементов навески (ушей, вилок или реперов) с привязкой к отверстиям для навески ложементов. Элементы навески являются стандартизированными и выбираются согласно соответствующим ОСТам. Если имеющиеся стандартные элементы не подходят для конструкции приспособления, то разрабатывается их собственная конструкция.
|
|
В приспособлении для сборки носка нервюры ложементы являются несъемными, поэтому для их фиксации используются уши (рис.10а). Крепление ложементов к ушам осуществляется с помощью классных болтов (рис.10б).
Рама каркаса выполняется из швеллеров №14. При проектировании рамы необходимо производить расчет на жесткость. Но можно использовать статистические данные, взяв за основу ранее спроектированные конструкции. На основе этих данных, по аналогии выбирается требуемый номер швеллера.
Уши крепятся к раме в стаканах путем заливки карбинольным цементом (рис.12). Хвостовик каждого уха имеет оребрение, а в стенках стаканов выполнены отверстия. Ухо вставляется хвостовиком в стакан, неподвижно фиксируется, и пространство между хвостовиком и стенкой стакана заполняется цементной массой. После затвердевания цемента, ухо сохраняет заданное положение.
Расстояние между внутренней стенкой стакана рамы и хвостовиком уха должно быть 5-10мм. За счет этого обеспечивается большая компенсация положения вилок при неточно установленных стаканах.
Монтаж ушей выполняется на инструментальном стенде. На подвижный стол стенда устанавливается и фиксируется рама приспособления. К порталу стенда с помощью дополнительных кронштейнов крепиться ухо приспособления. Затем раму приспособления подводят к уху путем приведения стола стенда в движение. После того, как рама заняла требуемое положение, стол стенда фиксируют и заливают цемент в стакан, где расположено ухо.
Для лучшего доступа при сборке, стаканы расположены на боковой стороне каркаса (рис.11,12). При данном расположении рабочая зона над ложементами остается свободной, упрощая доступ рабочим при сборке носка нервюры.
Фиксация стаканов к раме осуществляется с помощью ребер (рис.12а, в, рис 13).
Швеллерные коробки варят дуговой электросваркой (ДЭС) по месту стыка (рис.12б). Сварка осуществляется прерывистым швом длиной 100 мм, шаг 100 мм, для снижения внутренних напряжений и уменьшения коробления. Катет сварного шва не менее 5мм.
Угловые места стыков балок и колон усиливают накладками (рис.12а, рис.13).
Для монтажа и последующего контроля сборочного приспособления на раме необходимо установить репера (рис.14). Они устанавливаются с шагом 50 мм (рис.15) в стаканы на раме и заливаются карбинольным цементом.
При монтаже и последующей проверке на репера приспособления навешиваются монтажные линейки (рис.16) согласно схеме монтажа и производится проверка положения Б.О. ложементов относительно положений отверстий монтажных линеек. Каждая монтажная линейка имеет ряд отверстий Æ18Н9 выполненных с шагом 50±0,05. В разрабатываемом приспособлении совпадение положений соответствующих отверстий производится путем их проштыривания скалкой Æ18Н9. Если расстояние от линеек до плоскости ложементов/рубильников велико (более 100мм), совпадение отверстий проверяется с помощью лазерных или оптических систем.
Проектирование прижимных и фиксирующих элементов.
Согласно приятой схеме базирования (рис.3а) стенка носка нервюры поз.1 (рис.2) базируется по КФО, а верхний поз.2 и нижний поз.4 профиль – по внутреннему контуру обшивки. Для выполнения этих требований необходимо в конструкции приспособления предусмотреть фиксаторы КФО и прижимы профилей к ложементам.
Так же необходимо обеспечить заданное положение стенки и профилей по плоскости ложементов.
Фиксаторы КФО стенки необходимо закрепить на ложементах (рис.17). Этот вариант является оптимальным, так как КФО будут зафиксированы на кратчайшем расстоянии от ближа2шего жесткого элемента (ложемента).
Как еще один вариант можно рассмотреть фиксацию КФО с базой за раму. Но в этом случае для обеспечения требуемой жесткости необходимо значительно усложнять конструкцию приспособления, что приведет к возрастанию ее стоимости. Усложнение конструкции произойдет из-за необходимости обеспечения жесткости фиксаторов КФО. А так как ближайшие точки крепления к раме приспособления расположены значительно дальше, чем ложементы, это приведет к значительному увеличению массы фиксаторов КФО.
Каждый фиксатор крепиться к ложементам классными болтами (рис.18) и является несъемным в процессе сборки носка нервюры. Для крепления стенки нервюры к фиксаторам КФО используется резьбовой штырь (рис.18б). Своей гладкой частью он проходит через КФО и отверстие фиксатора, и прижимает стенку носка нервюры к плоскости фиксатора.
Конструкция кронштейнов фиксаторов КФО состоит из фигурной пластины и приваренным к ней бобышкам (рис.19).
Плоскость стенки верхнего поз.2 (рис.2) и нижнего поз.4 профиля должны находиться в одной плоскости (рис.5 в). Для выполнения данного условия на плоскости ложементов необходимо установить упоры, имитирующие эту плоскость. Для удобства работы упор должны быть съемными или выдвижными (рис.20).
Конструкция упора (рис.21) состоит из корпуса (рис.22) и выдвижной планки (рис.23). Для установки упора в требуемое положение ослабляется гайка с накаткой (рис.21), планка выдвигается и гайка затягивается, фиксируя планку.
Для фиксации верхнего поз.2 (рис.2) и нижнего поз.4 профиля необходимо обеспечить поджатие полок профилей к обводообразующей поверхности ложементов. Для этих целей наиболее всего подходят прижимы (рис.24). Конструкция прижима (рис.25) включает корпус (рис.26) и прижимной болт (рис.27) состоящий из штока, штифта и упора.
Прижим и выдвижной упор устанавливаются друг напротив друга на противоположных сторонах ложемента (рис.28). Благодаря их совместной работе происходит фиксация профилей в требуемом положении.
Для сборки носка нервюры приспособление должно быть установлено в цехе в заданное положение. С целью выполнения этой задачи к раме приспособления прикрепляются опоры (рис.29).
Каждая опора (рис.30) состоит из кронштейна (рис.31,32) плиты опорной (рис.34), винта упорного и шайбы (рис.33) и из стандартных изделий.
Кронштейн опоры имеет сварную конструкцию (рис.31,32). Он выполнен в виде сужающейся двутавровой балки. Благодаря этому кронштейн может воспринимать большую нагрузку при меньшей собственной массе.
Конструкция опоры позволяет выполнять регулировки по высоте. Благодаря этому можно отнивелировать положение сборочного приспособления в цехе. После выполнения регулировки, гайки опор контрятся, фиксируя тем самым положение приспособления.
На последнем этапе проектирования сборочного приспособления (рис.35) в его конструкцию вводятся все крепежные и фиксирующие элементы (болты, гайки, штифты и т.д.) соединяющие элементы приспособления между собой.
Полный комплект чертежей содержит:
1. Сборочные чертежи приспособления (рис.36,37).
2. Сборочные чертежи рубильников/ложементов (рис.38).
3. Чертеж для установки ушей в раму каркаса (заливочный чертеж, рис.39).
4. Сварочный чертеж рамы каркаса (рис.40).
5. Чертеж для установки фиксирующих элементов приспособления (рис.41).
6. Сборочные чертежи на мелкие узлы приспособления (опоры, фиксаторы, прижимы и т.д.).
7. Чертежи деталей приспособления.
Литература
1. ГОСТ 14.204-89 Правила обеспечения технологичности конструкций деталей. М.: Изд-во стандартов, 2005, 23с.
2. ГОСТ 14.203-89 Правила обеспечения технологичности конструкций сборочных единиц. М.: Изд-во стандартов, 2005, 23с.
3. ГОСТ 14.202-87 Правила выбора показателей технологичности конструкций изделия. М.: Изд-во стандартов, 2005, 23с.
4. ГОСТ 14.201-87 Общие правила отработки конструкции изделия на технологичность. М.: Изд-во стандартов, 2005, 32с.
5. ГОСТ 18.831-89 Технологичность конструкции. Термины и определения. М.: Изд-во стандартов, 2005, 37с.
6. ГОСТ 3.1109-92 Единая система технологической документации. Основные термины и определения. М.: Изд-во стандартов, 2006, 112с.
7. Григорьев В.П., Ганиханов Ш.Ф. Приспособления для сборки узлов и агрегатов самолетов и вертолетов. М.: Машиностроение, 2005. 253с.
8. Кваша А.Н. и др. Технология производства летательных аппаратов. М.: Машиностроение, 2006. 232с.
9. Брагин В.А., Турьян В.А. Производство самолетов, сборка и испытания. М.: Машиностроение, 2005, 319 с.
Дата добавления: 2016-01-05; просмотров: 66; Мы поможем в написании вашей работы! |
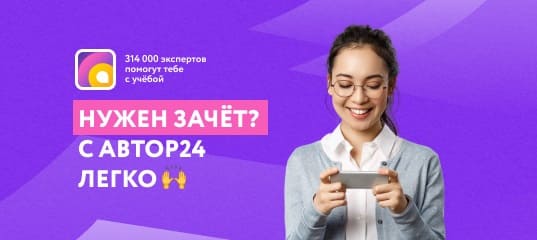
Мы поможем в написании ваших работ!