Принципы расчета элементов бурового оборудования
4.1. Прочность конструкции
Это способность конструкции, детали машины не разрушаясь воспринимать нагрузки в определенных режимах и условиях нагружения.
Большое влияние на прочность оказывают материалы, способы упрочнения, размеры геометрической формы конструкции. Вопросы прочности приобретают особое значение в связи с возрастающими требованиями к повышению надежности и долговечности, снижению массы конструкции. В обеспечении прочности важную роль играют методы прочностных расчетов. Расчеты любой конструкции или элементов бурового оборудования ведутся по условно принятым величинам нагрузок, продолжительности и характеру их действий.
Нагрузкой, как известно, называется силовое воздействие, вызывающее изменение напряженно-деформированного состояния конструкции или отдельных ее деталей.
Действующие нагрузки классифицируются следующим образом: по характеру действия статические и динамические; по характеру рабочего процесса стационарные и нестационарные.
Статические нагрузки характеризуются тем, что их значение направление и место приложения постоянны либо изменяются так незначительно, что при расчете конструкции пренебрегают влиянием сил инерции. В свою очередь они подразделяются на постоянные и временные.
К постоянным относятся нагрузки, значения которых для данной конструкции принимаются неизменными. Примером постоянной статической нагрузки является собственный вес конструкции. Постоянные нагрузки могут вызвать в деталях конструкции переменные напряжения. Так, в результате изгиба с вращением в сечениях вала за один оборот происходит смена растягивающих и сжимающих напряжений. Аналогично в результате периодического входа в зацепления зубья зубчатых передач испытывают переменные напряжения при постоянной рабочей нагрузке, действующей на исполнительный орган машины.
|
|
К временным статическим относятся нагрузки, действующие в течение длительного цикла работы (например, начальная затяжка резьбовых соединений, давление жидкости или газа в различных аппаратах, нагрузки от снега, гололеда и температурного воздействия, предварительное натяжение тяговых органов и др.).
Динамические нагрузки характеризуются быстрым изменением значения, направления или точки приложения, вызывающим в элементах конструкции значительные силы инерции. Причины появления динамических нагрузок – неравномерность рабочего процесса; ускорение при пусках, торможениях и реверсированиях; неуравновешенность быстровращающихся деталей; чрезмерный износ зубчатых и цепных передач; зазоры в подвижных соединениях и др. Динамические нагрузки, вызываемые неравномерностью рабочего процесса, характерные для поршневых машин (насосов и двигателей), и особенно для машин и инструмента ударного и вибрационного действия (молотов, копров, буровых долот, вибросит и др.).
|
|
Стационарным называют нагружение с постоянными характеристиками рабочего процесса. Нагружение с изменяющимися характеристиками рабочего процесса относят к нестационарному. К машинам, испытывающим стационарное нагружение, относят вентиляторы, машины центральных насосных станций и некоторые другие. Большинство машин испытывает нестационарное нагружение. Изменение характеристик рабочих процессов в буровых машинах обусловлено непрерывным увеличением глубины забоя в процессах бурения скважины, а также ступенчатым изменением веса бурильной и обсадной колонн труб при спуско-подъемных операциях.
Изменение уровня нагрузок и частота повторения нагрузок определенного уровня зависит от технологического процесса, выполняемого машиной, и передаточного числа от исполнительного органа до рассматриваемой детали.
Под действием эксплуатационных нагрузок возникают отказы деталей буровых машин и оборудования, которые по принятым критериям прочности относятся к усталостным и хрупким разрушениям, пластическим деформациям, ползучести и нарушениям сцепления. Виды отказов по критериям прочности их возникновения и характерные примеры приводятся в таблице 2.
|
|
Виды отказов по критериям прочности
Таблица 2
Вид | Причины возникновения | Характерные примеры |
Усталостные разрушения | 1. Переменные напряжения, уровень которых превышает предел выносливости. Разрушению предшествует постепенное развитие усталостных трещин 2. Термическая усталость, развивающаяся под действием повторных температурных напряжений | 1.Резьбовые соединения бурильных, ведущих и УБТ, валов, штоков насосов, пружин, деталей вышек и мачт, металлических оснований 2. Тормозные шкивы буровых лебедок |
Пластическая деформация | Перегрузка деталей, изготовленных из незакаленных и высокоотпущенных сталей | Искривление валов, осадка пружин, удлинение болтов при чрезмерных затяжках, смятие труб, шпонок и их канавок и др. |
Ползучесть | Длительное силовое воздействие в сочетании с нагревом | Появляется у пластмассовых деталей |
Хрупкие | Ударные и статические нагрузки, чрезмерные напряжения при посадках с натягом (в деталях из чугуна и низкоотпущенных сталей) | Ступицы колес дисков, пластины втулочно-роликовых цепей и т.д. |
Отказы, вызванные нарушениями сцепления | Провороты и осевые смещения в прессовых соединениях, относительное проскальзывание во фрикционных муфтах и ременных передачах, самоотвинчивание резьбовых соединений |
|
|
4.2. Выбор конструкционных материалов и способов упрочнения деталей
Конструкционные материалы в общем случае выбирают исходя из требований к их механическим, физическим и технологическим свойствам, предъявляемых условиям работы и изготовления данной детали. Механические и физические свойства позволяют судить о служебной пригодности материала.
По технологическим свойствам оценивается возможность обработки материала при изготовлении деталей. Основные механические, физические и технологические свойства, учитываемые при выборе материала, приводятся в таблице 3.
Свойства, учитываемые при выборе материала
Таблица 3
Механические | Физические | Технологические |
Прочность Деформативность Упругость Пластичность Хрупкость Твердость Сопротивление усталости | Плотность (удельный вес) Температура плавления Коэффициент теплопроводности Коэффициент линейного расширения Коэффициент трения | Обрабатываемость материалов резанием Литейные свойства Свариваемость Обрабатываемость давлением в горячем и холодном состоянии |
Прочность – способность сопротивляться нагрузкам без разрушения.
Деформативность – способность изменять размеры и форму без разрушения.
Упругость – способность восстанавливать первоначальные размеры и форму после снятия нагрузки.
Пластичность – способность получать значительную деформацию, оставшуюся после снятия нагрузки.
Поскольку физические величины хорошо известны, охарактеризуем технологические свойства.
Обрабатываемость резанием, характеризуемая пригодностью материалов к обработке всеми видами режущих инструментов при больших скоростях резания и подачах с получением необходимых параметров шероховатости поверхности, являются важным технологическим свойством.
Литейные свойства – это способность жидких металлов заполнять литейные формы и образовывать плотные отливки.
Свариваемость – способность металлов свариваться при комнатных и низких температурах с образованием прочных сварных соединений.
Обрабатываемость давлением в горячем и холодном состоянии, оценивается технологическими пробами (на осадку, загиб) и характеристиками пластичности, упрочнения и твердости при температуре обработки.
Обоснованный выбор материала для заданной детали из обширного ассортимента машиностроительных материалов может быть сделан на основе сравнительной оценки возможных вариантов. Критериями сравнительной оценки материалов являются минимальная масса и стоимость материала при заданных прочности, выносливости, жесткости и других требованиях к рассматриваемой детали.
При выборе материалов следует учитывать интересы заводов-изготовителей машин. Ограничение номенклатуры применяемых материалов дает заводам-изготовителям ряд важных преимуществ, связанных с укрупнением поставляемых партий материалов, упрощением их учета и хранения, снижением брака, благодаря более стабильной технологии в литейном, термическом и других участках производства. Поэтому без крайней необходимости не следует пользоваться нетрадиционными для данного завода материалами.
На заводах бурового оборудования для ответственных деталей и несущих элементов применяют хромоникелевые, хромомолибденовые и хромоникельмолибденовые стали. В ассортимент материалов, применяемых в производстве буровых машин и оборудования, кроме легированных сталей, вводят углеродистые общего назначения, цветные металлы, чугун, резину, полимерные и прочие материалы.
Привычные для деталей буровых машин и оборудования марки материалов периодически заменяются новыми марками. Это объясняется закономерным процессом развития производства более качественных и экономичных материалов, применение которых способствует дальнейшему повышению прочности и надежности буровых машин и оборудования.
Важный резерв повышения прочности деталей – выбор способов их упрочнения. Как известно, усталостные разрушения деталей в большинстве случаев происходит от действия повышенных местных напряжений, которые порождаются концентратами напряжений металлургического, технологического и конструктивного происхождения. Переходные сечения, канавки, резьбы, отверстия и прочие изменения формы деталей, а также соединения с натягом относятся к конструктивным концентраторам напряжений, в зоне которых местные напряжения значительно превосходят номинальные. Концентрация напряжений вызывает снижение сопротивляемости детали усталости.
4.3. Методы расчета на прочность
Выполняются с целью определения размеров и формы деталей той или иной конструкции, исключающих возможность их поломок и недопустимых деформаций в условиях нормальной эксплуатации. Сущность и эффективность существующих методов сведены в таблицу 4.
Таблица 4
Методы | Сущность | Эффективность | |
Детерминистические | проектные | Определяются наиболее характерные размеры, необходимые для начала конструирования | Результат окончательный в простейших случаях, размеры и форма деталей изменяются при дальнейшем их согласовании с требованиями и действующими стандартами |
проверочные | Оценивается конструкционная прочность путем сопоставления расчетных запасов прочности с допустимыми | Если Sрасч < [S] вносятся необходимые конструктивные и технологические изменения, повышающие рассчитываемую прочность | |
Вероятностные | Нагрузки и прочностные свойства задаются законами и распределениями, полученными на основе статистической информации. Запасы прочности устанавливаются в зависимости от планируемого уровня безотказной работы | Использование затрудняется из-за отсутствия или недостаточного объема статистической информации, необходимой для выявления законов распределения нагрузок и прочности деталей конструкции |
Прочностные расчеты, имеющие детерминистический характер, основаны на предположении, что расчетные нагрузки и параметры прочности имеют определенную (детерминированную) величину. Между тем известно, что горнобуровые машины относятся к категории машин, в которых нагрузки являются случайными функциями времени, а параметры прочности изменяются в определенных пределах, зависящих от однородности материала деталей, стабильности технологии изготовления и других факторов.
Поэтому детерминистические методы прочностных расчетов в ряде случаев недостаточны.
Более эффективны вероятностные методы, при которых нагрузки и прочностные свойства задаются законами их распределения, полученными на основе статистической информации. Однако использование этих методов затрудняется из-за отсутствия или недостаточного объема статистической информации, необходимой для выявления законов распределения нагрузок и прочности деталей.
4.4. Принципы расчета на статическую прочность
Буровое оборудование относится к категории машин, в которых нагрузки и время их действия – случайные величины. Расчеты элементов бурового оборудования ведутся по условно принятым величинам нагрузок, продолжительности и характеру их действий, а расчеты на прочность и долговечность элементов – по общепринятым методам с учетом специфических особенностей, выявленных многолетней практикой.
В качестве исходной максимальной расчетной нагрузки принимают:
· для подъемного комплекса – максимальную вероятную нагрузку на крюке, превышающую прочность на разрыв поднимаемой бурильной колонны или составляющую 0,8 наибольшего веса обсадной колонны;
· для механизмов вращения бурильной колонны – наибольший крутящий момент, равный разрушающему моменту кручения, применяемых для данной буровой установки бурильных труб;
· для циркуляционной системы – наибольшее давление, необходимое для восстановления и обеспечения циркуляции, ограничиваемое предохранительным клапаном.
При расчете на статическую прочность на стадии конструирования должно соблюдаться условие, при котором запас на статическую прочность
(16)
где Rн – вероятная несущая способность конструкции на растяжение, сжатие, изгиб или кручение, определяемая размерами конструкции, прочностными характеристиками материалов и др.;
Р – вероятная максимальная действующая нагрузка растяжения, сжатия, изгиба или кручения, определяемая условиями эксплуатации.
Так как от величины коэффициента запаса прочности (КЗП) зависят масса и стоимость изделия, то его величину следует выбирать в соответствии с условиями эксплуатации объекта. Большинство элементов бурового оборудования в процессе эксплуатации теряет прочность по мере старения. Поэтому определение статического КЗП справедливо только на стадии конструирования. Под прочностью объекта понимают вероятность того, что его несущая способность будет больше или равна некоторой величине, а под действующей нагрузкой – только вероятность того, что она будет равна или меньше некоторого значения, поэтому нельзя точно предсказать возможность разрушения.
Условие минимального риска отказа должно соблюдаться для элементов подъемного комплекса. Так, для подъемных комплексов вероятность безотказной работы трансмиссии, двигателей, муфты включения может находиться в пределах 0,9-0,99. Вероятность же безотказной работы элементов этой системы, разрушение которых может привести к человеческим жертвам, должна быть >0,999, т.е. на порядок – два выше.
В то же время для ротора, насоса, трансмиссии привода риск отказа может быть допущен. Например, требование «нормативная вероятность безотказной работы не меньше 0,7» для этих агрегатов приемлемо, так как два – три отказа в десяти случаях вызовут незначительные расходы на ремонт. Нормативная вероятность безотказной работы отдельных элементов должна назначаться из условий обеспечения не только технических, но и экономически обоснованных требований безотказной работы всей системы за рассматриваемый период времени.
При выборе КЗП необходимо учитывать условия работы и старение объекта, так как КЗП нового объекта будет значительно выше, чем изношенного. Например, новые талевый канат, ствол и стропы крюка и другие элементы имеют коэффициенты статического запаса прочности значительно большие, чем бывшие в эксплуатации. При выборе КЗП надо учитывать и характер действия нагрузки. Так, для нового талевого каната при динамических нагрузках в процессе спуско-подъемных операций Smin=3 (ОСТ 26-02-80-73), а при статических нагрузках (спуск обсадных колонн) Smin=2. В условиях сложного напряженного состояния КЗП выбирается по отношению к приведенным напряжениям, определяемым по одной из теорий прочности.
В расчетах элементов конструкций бурового оборудования, находящихся под действием сил, которые вызывают сложное напряженное состояние материалов, могут использоваться различные теории прочности в зависимости от характера действия нагрузок и свойств материалов. Большая часть материалов имеет прочность, возрастающую по мере перехода из области растяжения в область сжатия, особенно это проявляется при работе деталей в агрессивных средах при коррозии металлов.
При расчете бурового оборудования чаще используется теория наибольших касательных напряжений (Мора). В ряде случаев энергетическую теорию прочности.
Расчетные напряжения по теории наибольших касательных напряжений:
(17)
Приведенные напряжения по энергетической теории прочности:
в области растяжения
; (18)
в области сжатия
, (19)
где sдоп и sпр – допустимое и приведенное напряжения,
sр, sс – напряжения растяжения и сжатия;
m ‒ коэффициент Пуассона;
τ – касательное напряжение.
Общий КЗП деталей, в которых возникают нормальные s и касательные τ напряжения,
, (20)
где Ss и Sτ – КЗП по нормальным и касательным напряжениям.
При определении несущей способности конструкции исходят из нормативных пределов прочности или текучести материала. В зависимости от материала детали, размеров и метода горячей обработки фактическая прочность может значительно отличаться от нормативной, указываемой в справочниках для различных материалов. Более точные данные о физико-механических свойствах материалов можно получить из сертификатов или результатов лабораторных испытаний.
Для определения КЗП надо знать фактическую несущую способность конструкции вероятную действующую нагрузку, которую следует принять за расчетную. Наиболее достоверные данные о конструкции можно получить при сопоставлении КЗП рассчитываемой конструкции и аналогичной конструкции – прототипа, прошедшего эксплуатацию в течение достаточного времени.
Для бурового оборудования КЗП, отнесенный к пределу текучести Sτ, принимают в зависимости от степени пластичности материала, характеризуемой отношением предела текучести sτ к пределу прочности sв:
![]() | 0,45-0,55 | 0,55-0,70 | 0,7-0,9 |
Sτ ………….. | 1,2-1,5 | 1,4-1,8 | 1,7-2,6 |
Коэффициент запаса прочности по пределу прочности:
. (21)
При конструировании сложных объектов идеальным является случай, когда все элементы конструкции равнопрочные, однако это практически невозможно, и прочность конструкции всегда определяет ее наиболее слабое звено.
Список литературы
1. Анурьев В.И. Справочник конструктора-машиностроителя. М., Машиностроение, 1982.
2. Ганджумян Р.А. Практические расчеты в разведочном бурении. Справочное пособие. М., Недра, 1987.
3. Гланц А.А., Алексеев В.В. Справочник механика геологоразведочных работ. М., Недра, 1987.
4. Даниелян А.А. Основные направления проектирования оборудования для бурения глубоких скважин. М., Недра, 1967.
5. Дудля Н.А. Проектирование буровых машин и механизмов. Киев, Выща шк., 1990.
6. Ильский А.Л., Миронов Ю.В. Расчет и конструирование бурового оборудования. М., Недра, 1985.
7. Кирсанов А.Н., Зиненко В.П., Кардыш В.Г. Буровые машины и механизмы. М., Недра, 1981.
8. Общетехнический справочник под ред. проф. Малова А.Н. М., Машиностроение, 1971.
9. Поляков Г.Д., Булгаков Е.С. Проектирование, расчет и эксплуатация буровых установок. М., Недра, 1983.
10. Проников А.С. Надежность машин. М., Машиностроение, 1978.
11. Рябчиков С.Я. Проектирование буровых машин и механизмов. Учебное пособие. Изд.ТПУ, Томск, 2005.
12. Сергиенко И.А. Основы проектирования установок разведочного бурения. М., МГРИ, 1985.
13. Соловьев Н.В., Ганджумян Р.А. и др. Основы конструирования алмазного породоразрушающего инструмента. М., МГГА, 2000.
14. Справочник по бурению геологоразведочных скважин. С-Пб., ВИТР, Недра, 2000.
Дата добавления: 2016-01-05; просмотров: 129; Мы поможем в написании вашей работы! |
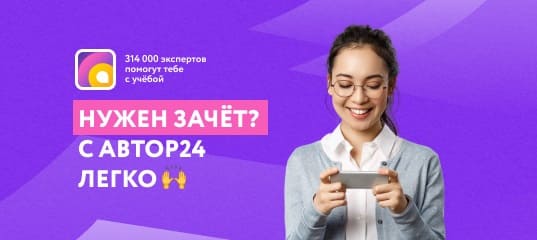
Мы поможем в написании ваших работ!