Основные этапы проектирования новой техники
3.1. Стадии разработки конструкторской документации
Технические решения, принимаемые конструкторами на стадии проектирования, выбираются с учетом перспективного развития техники и технологии буровых работ. Одним из важных направлений считается дальнейшее повышения производительности бурения и снижение стоимости разведки полезного ископаемого. Важную роль в решении этих задач занимает буровая техника, обеспечивающая высокую степень механизации и автоматизации производственных процессов.
Основные стадии и порядок разработки нового изделия (конструкции) машиностроения определяют на основе ЕСКД.
3.1.1.Этапы проектирования и порядок разработки конструкторской документации
Основными стадиями опытно-конструкторских работ являются следующие:
· техническое задание;
· техническое предложение;
· эскизный проект;
· технический проект;
· разработка рабочей документации опытного образца;
· изготовление и предварительные (заводские) испытания опытного образца;
· приемочные испытания опытных образцов;
· разработка рабочей документации установочной серии;
· разработка рабочей документации установившегося серийного производства;
· авторский надзор.
Исходным документом для проектирования любых изделий является техническое задание (ТЗ), разрабатываемое совместно научно-исследовательскими и проектно-конструкторскими организациями с привлечением заводов-изготовителей, заказчиков. ТЗ может разрабатываться заказчиком и самостоятельно.
|
|
Научно-исследовательские организации обеспечивают научное обоснование показателей разрабатываемого изделия, а проектно-конструкторские – разрабатывают его схемное решение, принципиальную конструкцию узлов и изделия в целом.
Техническое задание устанавливает основное назначение техническую и тактико-техническую характеристику, технико-экономические требования, предъявляемые к новому изделию, сроки выполнения работ, объемы изготовления, показатели качества, требования технической эстетики, техники безопасности и гигиены труда, а также дается оценка перспективности разработки. В ТЗ отражают вопросы целесообразности создания модификаций нового изделия, особенности управления и регулирования рабочих органов, унификации узлов машины, сезонности работ, особенности облуживания и состава персонала, а также ценообразования.
В ТЗ следует устанавливать количество опытных образцов или объем опытной партии, которые должны быть достаточными для получения достоверной оценки свойств в предусмотренных условиях ее эксплуатации (или имитации этих условий).
|
|
В ТЗ указывают порядок сдачи и приемки результатов разработки, который в общем случае содержит:
¾ виды изготовленных образцов (экспериментальные, опытные, головные);
¾ категории испытаний;
¾ место проведения испытаний;
¾ необходимость рассмотрения результатов на приемочной комиссии и ее состав;
¾ документы, предъявляемые на приемку.
Наряду со стандартами ЕСКД, разработка технических заданий регламентируется еще целым рядом других стандартов, как отраслевых, так и государственных, различными руководящими материалами по проектированию и т.д. ГОСТ 15.001-88 «Система разработки и поставки продукции на производство. Продукция производственно-технического назначения» устанавливает общий порядок разработки ТЗ, их согласование и утверждение. ГОСТ 15.150-69 регламентирует условия эксплуатации, климатическое исполнение. ГОСТ 16.263-70 устанавливает термины и определения метрологических характеристик. ГОСТ 27.003-89 нормирует показатели качества. В отраслевом стандарте ОСТ 41.01.93-83 «Система разработки и постановки продукции на производство. Изделия геологоразведочной техники» приводятся все требования к структуре проектных работ на новую технику геологоразведочного сортамента.
|
|
ТЗ после его согласования и утверждения является основанием для выполнения проектных работ.
Первой стадией разработки проектной документации является техническое предложение (ТП), выполняемое в соответствие с ГОСТ 2.118-73. Этот документ является как бы ответом проектанта на полученное им техническое задание. Он содержит технические и технико-экономические обоснования целесообразности разработки документации на изделие. Обоснование производится на основе анализа технического задания заказчика, существующих изделий аналогичного назначения, различных вариантов возможных решений изделий, сравнительной оценки решений с учетом конструктивных и эксплуатационных особенностей разрабатываемого и существующих изделий, патентных материалов. ТП должно содержать: обзор существующих образцов аналогичных или близких по назначению изделий отечественного и зарубежного производства, оценку их конструктивных особенностей и эксплуатационных показателей, варианты процессов работы, варианты компоновок будущего изделия, расчет производительности по каждому варианту.
В ТП должны быть указаны преимущества и недостатки каждого варианта, даны технико-экономические показатели изделия в оптимальном варианте (сравнительные данные по производительности, срокам окупаемости), общий вид изделия оптимального варианта, краткое описание его конструкции и принципа действия.
|
|
Возможны случаи, когда в ТЗ дается четкое решение какого-то вопроса, например оптимальный вариант буровой установки – самоходный. В этом случае проектанту в ТП не требуется разрабатывать варианты компоновки и указывать оптимальный вариант.
После согласования и утверждения ТП является основанием для разработки эскизного проекта.
Эскизный проект (ЭП) – это совокупность конструкторских документов, которые должны содержать принципиальные конструкторские решения, дающие общее представление об устройстве и принципе работы изделия. Кроме того, ЭП определяет назначение, основные параметры и габаритные размеры разрабатываемого изделия. Структура ЭП и порядок его разработки регламентируется ГОСТ 2.119-73. При выполнении ЭП производится следующая работа:
¾ конструкторская проработка оптимального варианта;
¾ выполняются в эскизном исполнении основные сборочные единицы изделия;
¾ уточняется общий вид изделия;
¾ разрабатывается кинематическая схема;
¾ разрабатывается циклограмма или предварительная принципиальная электрическая схема и другие основные конструкторские документы в зависимости от специфики изделия;
¾ производится краткое описание конструкции и принципа работы изделия;
¾ указывается уточненная производительность, дается технико-экономический расчет.
На стадии эскизного проектирования могут разрабатываться и изготавливаться макеты отдельных сборочных единиц изделия или изделия в целом для проверки новых или наиболее важных конструкторских решений.
ЭП после согласования и утверждения служит основанием для разработки технического проекта.
Технический проект – это совокупность конструкторских документов, которые должны содержать окончательные технические решения, дающие полное представление об устройстве разрабатываемого изделия и исходные данные для разработки рабочей документации. Основное содержание и порядок выполнения технического проекта определяется ГОСТ 2.120-73.
В техническом проекте содержится:
¾ описание окончательной конструкции изделия и принципа его действия (работы);
¾ обоснование выбора материалов и видов защитных покрытий;
¾ требования к точности сборки отдельных сборочных единиц и всего изделия;
¾ описание всех схем;
¾ окончательный технико-экономический расчет.
Технический проект после согласования и утверждения служит основанием для разработки рабочей конструкторской документации, т.е. рабочего проекта.
Разработка рабочей документации осуществляется проектной организацией обычно совместно с заводом-изготовителем на основе ТЗ и технического проекта в соответствии с требованиями государственных и отраслевых стандартов, которые устанавливают следующие виды рабочей конструкторской документации:
¾ конструкторская документация на опытный образец (опытную партию), имеющая литеру О1, О2, О3 и т.д.;
¾ конструкторская документация на установочную (головную) серию (литера А);
¾ конструкторская документация для установившегося серийного или массового производства (литера Б).
Отдельным пунктом выступает разработка рабочей документации для индивидуального производства (литера И), когда изделие изготавливается в 1 – 2-х экземплярах, например экспериментальная установка специального назначения.
В комплект рабочей документации должны входить следующие конструкторские документы:
¾ чертежи всех деталей (кроме стандартных) с простановкой всех размеров с допусками, степенью обработки и другой информацией, необходимой для изготовления;
¾ чертеж общего вида изделия;
¾ чертежи подузлов, узлов и групп для слесарей-сборщиков;
¾ сборочные чертежи изделия;
¾ технические условия на изготовление, в которых даются допуски на взаимные перекосы, допустимые несоосности, люфты и т.д.;
¾ технические условия на поставку с учетом комплектации установок;
¾ программы стендовых (заводских) и промышленных испытаний;
¾ спецификация (ведомость) материалов, готовых изделий, необходимых для изготовления данного изделия;
¾ дополнительные расчеты, необходимость которых возникает при разработке рабочей документации;
¾ эксплуатационные документы (инструкции по эксплуатации, смазке, ремонту и т.д.);
¾ патентный формуляр.
В рабочем проекте дается предписание о количестве опытных образцов. Их может быть один или несколько. Количество опытных образцов зависит от назначения оборудования, его сложности и возможности получения исчерпывающих и достоверных данных о работоспособности и долговечности нового оборудования или инструмента.
Рабочая документация согласовывается с заказчиком, заводом-изготовителем, утверждается в установленном порядке и передается на завод-изготовитель.
В данной главе рассмотрены все проектные стадии разработки конструкторской документации. Однако наличие всех стадий в процессе разработки того или иного изделия не обязательно. Определяющим фактором в этом случае является степень новизны и сложности разрабатываемого изделия.
С точки зрения новизны все изделия делят на пять групп.
К I группе относятся изделия, которые являются воспроизведением существующих образцов, без существенных переделок или с небольшими переделками.
Ко II группе относятся конструктивные модификации существующих базовых моделей с использованием унифицированных узлов и механизмов.
К III группе относятся изделия, отличающиеся от существующих моделей и типов размерными параметрами.
К IV группе относятся изделия новые по конструктивному оформлению, но предназначенные для выполнения распространенных в практике операций.
К V группе относятся изделия новые по конструктивному оформлению, основанные на принципиально новых конструкторских решениях.
По сложности все изделия можно разделить также на пять групп:
¾ группа А – изделия с простой кинематикой, с нерегулируемыми скоростями главных движений;
¾ группа Б – изделия со ступенчатым переключением скоростей подач;
¾ группа В – изделия, кинематика которых предусматривает ступенчатое или бесступенчатое регулирование скоростей при централизованном, но не автоматизированном управлении;
¾ группа Г – изделия автоматического или полуавтоматического типа;
¾ группа Д – изделия, в которых автоматизация операций осуществляется с применением электроники или специальных электрических и гидравлических схем.
Соответствующее сочетание групп новизны и сложности должно быть решающим аргументом при определении необходимых стадий разработки конструкторской документации. Если предстоит разработка документации на новое и сложное изделие, то предусматриваются все стадии разработки.
3.1.2. Порядок внедрения новой техники в производство
Получив комплект рабочей документации с литерой О1, завод-изготовитель разрабатывает технологию изготовления и изготавливает опытный образец (образцы), которые проходят заводские (стендовые) и приемочные испытания в производственных условиях. Испытания проводят по программе, составленной организацией-разработчиком с учетом требований ГОСТ 2.106-68, а также типовых программ и методик испытаний данного вида продукции.
В процессе испытаний бурового оборудования должна быть подтверждена возможность выполнения его рабочими органами соответствующих технологических функций. На основании результатов испытаний оцениваются скорости выполнения отдельных операций и баланс рабочего времени, для чего проводятся хронометражные наблюдения. В процессе испытаний необходимо определить технико-экономические показатели: механическую скорость, производительность работ, стоимость работ и т.д. Для этого учитываются затраты времени на различные виды основных и вспомогательных работ, расход энергии, горюче-смазочных и истирающих материалов, труб, транспортные расходы и т.д. Оцениваются удобство управления, надежность работы, ремонтопригодность, удобство ремонта в полевых условиях и в мастерских, уровень безопасности проведения работ и др.
Важной задачей испытаний является оценка соответствия требованиям техники безопасности, в том числе с точки зрения уровня освещенности, шума, вибрации.
Как правило, испытания проводятся в сопоставлении с заменяемой техникой и должны подтверждать преимущества нового оборудования с заданной достоверностью. В случае, если выявляется много недостатков или они существенные, то рабочая документация возвращается проектировщику на доработку, который проводит ее корректировку и вносит все изменения в соответствии с ГОСТ 2.503-74. ЕСКД. «Правила внесения изменений». Новому комплекту рабочей документации присваивается литера О2, и по ней изготавливается новый опытный образец, который проходит стендовые и приемочные испытания по принятой программе.
В случае, ели опытный образец успешно пройдет испытания, то проектировщик разрабатывает рабочую документацию на изготовление установочной серии, которой присваивается литера А. Изделия установочной серии проходят испытания в заводских и производственных условиях по программе, разработанной проектировщиком и согласованной с заказчиком. Испытания проводят в различных геолого-технических, климатических, дорожно-транспортных и т.д. условиях.
В дальнейшем по результатам испытаний дорабатывается конструкторская документация с целью улучшения технологичности конструкции. Разрабатываемой документации присваивается литера Б. После этого завод-изготовитель осваивает серийное производство.
В процессе разработки, изготовления, испытания может быть выявлена нереальность или нецелесообразность отдельных требований, предусмотренных в ТЗ. В этом случае в ТЗ должны быть своевременно внесены соответствующие коррективы.
3.2. Система испытаний бурового оборудования
в процессе проектирования и изготовления
При создании нового оборудования значительную часть времени от технического задания до серийного производства занимают различного рода испытания, которые увеличивают сроки внедрения новой техники. Однако проведение испытаний – совершенно необходимый этап в процессе разработки и внедрения новой техники.
Испытания позволяют:
¾ на стадии научно-исследовательских работ (НИР) и разработки проектной документации – выбрать оптимальный вариант конструктивных решений, выбрать материалы;
¾ в процессе разработки и приемки опытных образцов оценить соответствие показателей надежности элементов изделия и конструкции в целом требованиям технического задания;
¾ на стадии освоения производства новой техники – оценить возможности технологического процесса завода-изготовителя в обеспечении заданного уровня надежности при серийном производстве;
¾ на стадии установившегося серийного производства – контролировать работоспособность выпускаемых машин по завершении технологического процесса их изготовления, периодически проверять соответствие показателей надежности требованиям технических условий, контролировать стабильность производства по этим показателям;
¾ при усовершенствовании серийной продукции – оценить эффективность внесенных изменений по показателям надежности;
¾ на стадии ремонта – проверять качество ремонта.
На различных стадиях проектирования и изготовления станков испытания носят различный характер. На стадии НИР и на первых этапах разработки конструкторской документации должны проводиться два вида испытаний материалов:
¾ испытания в эталонных условных режимах, которые позволяют получить объективную сравнительную оценку показателей качества материалов, влияющих на надежность;
¾ испытания в контролируемых условиях внешних воздействий, которые обеспечивают моделирование режимов эксплуатации в реальных условиях.
Все испытания первого вида проводятся по стандартным методикам, к которым относятся определение относительной износостойкости материалов при трении о закрепленный абразив (ГОСТ 17367-71); определение прочности (ГОСТ 21318-75); определение предельных нагрузочных характеристик: предела выносливости (ГОСТ 2860-65), критической температуры смазочных масел при трении (ГОСТ 17604-72), максимально несущей способности по критерию задира и др.
При испытаниях второго вида учитываются конструктивные и эксплуатационные особенности работы реальных узлов. Для узлов трения такие испытания проводятся на машинах трения с герметическим и тепловым моделированием сопряжений с учетом эксплуатационных нагрузок, скоростей, температур и т.д. Результаты этих испытаний для различных материалов сопоставляются, что дает возможность выбрать лучшие материалы для данных условий работы.
При испытании узлов станка оценивают долговечность и безотказность работы применительно к типовым режимам нагрузок, в качестве которых могут использоваться режимы максимальных нагрузок или скоростей.
В системе испытаний очень важным является рациональное сочетание испытаний отдельных элементов изделия и изделия в собранном виде. Преимущества поэлементных испытаний заключаются в следующем:
¾ испытания обеспечивают получение информации о надежности машины на более ранних этапах создания, например на стадии разработки его отдельных узлов. Данные, полученные по результатам испытаний отдельных узлов, могут использоваться для их конструктивной и технологической доводки. Доводка на ранних этапах разработки дает большой экономический эффект, так как на более поздних стадиях изготовления всякая доводка одного узла приводит к изменению (иногда существенному) конструкции и технологии изготовления других узлов;
¾ испытания дают возможность на большом статистическом материале определить надежность машины, оптимальную надежность узлов и деталей.
Однако не все задачи оценки надежности могут быть решены с помощью поэлементных испытаний. При проведении таких испытаний невозможно учесть связь между элементами, качество сборки и т.д. В связи с этим испытания машин в собранном виде занимают важное место в системе испытаний.
Преимущества ускоренных испытаний станка наиболее эффективно можно реализовать при проведении их на стенде. Однако при испытаниях на стенде нельзя оценить фактические технико-экономические показатели (скорость бурения, глубина бурения скважин и др.). Поэтому испытания на надежность следует проводить во время стендовых испытаний, а приемочные испытания проводить в условиях эксплуатации, где кроме технико-экономических показателей можно определить работоспособность станка, удобство обслуживания и т.д.
На этапе освоения производства при испытаниях выявляется связь между надежностью изготовленных образцов установочной серии и показателями технологического процесса (режимами термообработки, точности сборки и т.д.). В процессе испытаний установочной серии изделий целесообразно проводить поэлементные испытания узлов, которые по надежности не отвечают требованиям технических условий.
При серийном производстве бурового оборудования проводятся три вида испытаний: приемо-сдаточные испытания, периодические и, при необходимости, типовые испытания.
Приемо-сдаточные испытания должны включать проведение приработки основных узлов трения машин с одновременным выявлением отказов, связанных с технологическими дефектами. При проведении приемо-сдаточных испытаний выбираются определенные режимы работы узла или всей машины. Для эффективного проведения приработки режим нагружения должен быть ступенчато- или плавновозрастающим. В процессе приработки должны быть отбракованы все «слабые» элементы.
Спецификой периодических испытаний является необходимость оценки стабильности показателей надежности изделий на протяжении всего процесса их производства при ограниченном количестве испытанных образцов.
Опыт показывает, что отказы, выявляемые в процессе периодических испытаний, связаны с технологическими дефектами, обусловленными нарушением стабильности технологического процесса. Для повышения достоверности результатов периодических испытаний применяют дополнительные испытания деталей машины, которые наиболее часто выходили из строя при испытаниях машины в собранном виде.
На основании этих результатов составляется план мероприятий по улучшению технологического процесса, более строгому соблюдению технологической дисциплины и т.д. Реализация этого плана должна обеспечить в дальнейшем повышение стабильности показателей надежности выпускаемых машин.
Постоянное совершенствование конструкций серийно выпускаемых машин требует изменение конструкции и технологии их изготовления. Все это приводит к необходимости проведения определенных испытаний. Наиболее рациональным видом испытаний в этом случае могут служить поэлементные испытания. Как правило, в процессе совершенствования конструкций выпускаются еще изделия старых образцов, это обстоятельство значительно облегчает проведение испытаний, так как в этом случае можно использовать сравнительные испытания.
При ремонте система испытаний содержит те же элементы, что и при производстве новых изделий. Специфика испытаний на этой стадии заключается в существенном различии начального качества разных образцов, так как в ремонт поступают машины неодинаковой степени изношенности. Поэтому для успешного применения принципов испытаний, разработанных для новых изделий, необходимо перед проведением испытаний дифференцировать изделия по их исходному состоянию. Это можно осуществить с помощью методов технической диагностики.
Помимо информации, полученной в процессе испытаний при проектировании и изготовлении, широко используется информация, собранная в процессе эксплуатации. Эксплуатационные наблюдения позволяют выявить ненадежные элементы машин, характер разрушений, значения предельных состояний и т.д.
Наиболее ответственными из всех перечисленных испытаний являются приемо-сдаточные или государственные испытания. Их проведение обеспечивают головные организации, утверждаемые совместно ведомством и Госстандартом. Головной организацией по проведению государственных испытаний важнейших видов продукции для геологоразведочного бурения (буровых установок, алмазного породоразрушающего инструмента) был утвержден ВИТР, а насосов, средств механизации спуско-подъемных операций – СКБ.
ВИТР и СКБ обеспечивают методическое руководство государственными испытаниями основных видов геологоразведочной техники, разрабатывают нормативно-техническую документацию по их проведению, а также проводят работу по метрологическому обеспечению и по аттестации базовых испытательных подразделений.
В систему государственных испытаний, как правило, включаются стендовые полигонные и эксплуатационные испытания изделий и их составных частей. Объем и продолжительность каждого из этих видов испытаний устанавливают в рабочей программе в зависимости от степени новизны и уровня сложности изделия, масштабов его производства и др.
3.3. Система автоматизированного проектирования
буровых машин
Широкое внедрение комплексной механизации и автоматизации в процесс бурения скважин сопровождается усложнением конструкций бурового оборудования, появлением новых технических решений и, как следствие, увеличением срока и трудоемкости проектирования и изготовления. Эти обстоятельства, а также недостаточная эффективность решений при разработке сложных систем, могут привести к моральному старению изделия до ввода его в эксплуатацию и низкой эффективности его дальнейшего использования. Поэтому рост номенклатуры создаваемых машин и повышение их сложности требует от конструкторских организаций ускорения темпов проектирования. Решение этой проблемы возможно при разработке и внедрении систем автоматизированного проектирования буровых машин (САПР БМ), которые предусматривают широкое использование системного подхода при постановке задач, математических методов и ЭВМ при их решении.
САПР определена в ГОСТ 22487-77 как проектирование, при котором отдельные преобразования объекта и алгоритма его функционирования или алгоритма процесса, а также представления описаний на различных языках осуществляется взаимодействием человека и ЭВМ. При этом автоматизируются процедуры и операции ввода (вывода) различных данных, поиска, разработки, оценки, контроля и хранения проектных решений, компоновки, редактирования и вывода (изготовления) проектной документации, а также информационно-справочного обслуживания.
В настоящее время можно выделить четыре группы задач при проектировании бурового оборудования, которые целесообразно решать с помощью ЭВМ:
¾ многовариантные оптимизированные расчеты, то есть расчеты по сложным методикам, которые требуют быстрого получения точных результатов;
¾ проверочные и проектировочные расчеты по специально разработанным методикам;
¾ автоматизированные системы проектирования.
Первые три группы задач могут рассматриваться как ступени, ведущие к довольно перспективному машинному проектированию. Современные методики проверочных и проектировочных расчетов характеризуются большой общностью, что позволяет по одной программе рассчитывать конструкции целого класса. Использование ЭВМ открывает большие перспективы для оптимизации технических решений и позволяет использовать математическую теорию планирования эксперимента, которая позволяет получить необходимые экспериментальные данные с минимальными затратами средств и времени при исследовании сложных технических и технологических систем. Наличие необходимого количества «состыкованных» программ позволяет рассчитывать и оптимизировать сложные конструкции, включающие различные сборки.
Поскольку при машинном проектировании невозможно заранее предусмотреть все варианты поиска оптимального решения, то наиболее эффективным режимом работы является диалоговый режим «человек – машина». Человек в этом случае анализирует информацию, выданную на дисплей или в печать, и после ее анализа может вводить дополнительные данные и определять направление дальнейшего решения. Например, при расчете валов на основании выданных минимальных запасов прочности конструктор может при необходимости изменять конструктивные размеры вала, материал, термообработку и др. После этого машина снова считает слабое сечение и т.д. Режим диалога можно использовать при определении параметров подъемного механизма буровой установки, вращателя, насоса и др.
Применение ЭВМ может дать значительный эффект, так как позволяет ускорить проектирование в 7 – 10 раз и повысить качество проекта за счет выбора наиболее оптимального варианта. При этом в значительной степени исключаются субъективные факторы, влияющие на качество выполнения проекта.
После выбора оптимального варианта САПР позволяет разработать и выдать в готовом виде проектную документацию в полном объеме. Примерная блок-схема процесса синтеза оптимальной конструкции приведена на рис. 2.
ЭВМ разрабатывает, как правило, не один, а ряд допустимых вариантов конструкций, выбор же окончательного решения остается за человеком.
Создание САПР достаточно сложная проблема, так как она связана с решением задач методологии, организации и технического обеспечения.
Современные ЭВМ дают возможность оператору работать со всеми видами графической, текстовой и другой информации в режиме диалога.
При создании САПР разрабатывают единый метод и признаки классификации, основные классификационные группировки и правила обозначения, которые для различных отраслей промышленности устанавливает ГОСТ 23501.108-85. По каждому признаку установлены классификационные группы, их характеристики и коды, порядок работы с ними.
САПР машин строят с учетом единой системы конструкторской документации (ЕСКД), единой системы технологической подготовки производства (ЕСТПП), а также автоматизированной системы управления производством (АСУП).
Постановка задачи |
Формирование матрицы параметров и матрицы нагрузок конструкции |
Проектировочный расчет конструкции и ее отдельных подсистем с учетом существенных взаимосвязей между ними |
нет |
Удовлетворены все ограничения? |
да |
Вычисление и запоминание критериев оптимальности |
да |
Исчерпаны все возможные комбинации параметров? |
нет |
[Введите цитату из документа или краткое описание интересного события. Надпись можно поместить в любое место документа. Для изменения форматирования надписи, содержащей броские цитаты, используйте вкладку "Средства рисования".] |
[Введите цитату из документа или краткое описание интересного события. Надпись можно поместить в любое место документа. Для изменения форматирования надписи, содержащей броские цитаты, используйте вкладку "Средства рисования".] |
[Введите цитату из документа или краткое описание интересного события. Надпись можно поместить в любое место документа. Для изменения форматирования надписи, содержащей броские цитаты, используйте вкладку "Средства рисования".] |
[Введите цитату из документа или краткое описание интересного события. Надпись можно поместить в любое место документа. Для изменения форматирования надписи, содержащей броские цитаты, используйте вкладку "Средства рисования".] |
[Введите цитату из документа или краткое описание интересного события. Надпись можно поместить в любое место документа. Для изменения форматирования надписи, содержащей броские цитаты, используйте вкладку "Средства рисования".] |
Изменение управляемых параметров |
Сравнение всех вариантов конструкции и выбор оптимального |
Рис. 2. Примерная блок-схема процесса синтеза оптимальной конструкции
Дата добавления: 2016-01-05; просмотров: 33; Мы поможем в написании вашей работы! |
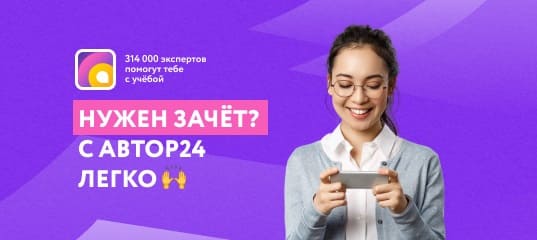
Мы поможем в написании ваших работ!