Бурового оборудования
1.1. Эксплуатационно-технологические требования к буровому оборудованию
Большие объемы бурения скважин в различных отраслях производства предполагают постоянное совершенствование техники и технологии бурения, создание новых технических средств. Уровень развития буровой техники существенно влияет на технико-экономические и эксплуатационно-технические показатели, в том числе долговечность, монтажные качества, транспортабельность бурового оборудования и т.д.
Буровые работы, выполняемые в различных регионах, характеризуются, наряду с назначением, глубиной и конструкцией скважин, большим разнообразием геологических, географических, климатических, дорожно-транспортных, энергетических и других условий. Поэтому для удовлетворения потребностей геологоразведочной службы необходимо располагать буровыми установками разных типоразмеров, соответствующих требованиям бурения скважин в различных условиях. При этом диапазон условий постоянно расширяется, что приводит к необходимости разработки новых буровых установок.
Конструирование (создание) новых машин или механизмов, предназначенных для бурения скважин, представляет собой сложный творческий процесс, вследствие специфических условий работы.
Известно, что любое вновь создаваемое изделие (конструкция) должно выполнять определенный рабочий процесс. Однако конструкция, машина или комплекс, предназначенный для разрушения горной породы на забое, имеет свои специфические условия работы:
|
|
· буровая установка представляет собой сложный комплекс различных по назначению машин и механизмов;
· буровая установка является предприятием сугубо временным, часто перевозится с точки на точку;
· наличие длинной гибкой бурильной колонны изменяет параметры, задаваемые на поверхности, при передаче их до забоя скважины;
· процесс бурения резко меняется вследствие изменения состава и структуры горных пород;
· место рабочего процесса удалено от оператора (бурильщика) на большие расстояния, исчисляемые сотнями метров и даже километров. При этом нет возможности непосредственного наблюдения за процессом разрушения пород;
· правильное протекание процесса определяется многими факторами: физико-механическими свойствами горных пород, типом и состоянием в каждое мгновение породоразрушающего инструмента. Многие параметры при этом самопроизвольно, независимо от воли оператора изменяются по специальным, часто неизвестным законам;
· неисправность любого из механизмов бурового агрегата вызывает остановку агрегата (например, в случае выхода насоса из строя необходимо поднять буровой инструмент). Поэтому для достижения надежности системы необходимо предъявлять самые высокие требования к надежности всех ее элементов;
|
|
· при конструировании и разработке буровых установок необходимо исходить из того, что надежность элементов, входящих в установку, должна быть на несколько порядков выше, чем ожидаемая надежность установки.
Перечисленные особенности усложняют по сравнению с общим машиностроением выбор исходных расчетных величин, необходимых для выяснения напряженного состояния узлов и деталей бурового оборудования.
Поэтому процесс конструирования современных машин и оборудования – комплексная задача, при решении которой конструктор обязан учитывать экономические, социальные, технические, эксплуатационные, технологические и специальные требования, предъявляемые к создаваемой технике.
Экономические требования включают как процесс эксплуатации буровых машин и систем оборудования, так и процесс их производства. Непременным условием выполнения экономических требований является обеспечение минимальных расходов, связанных с процессом создания новой буровой техники и изготовлением ее в заводских условиях.
|
|
Следовательно, производительность машины, обеспечиваемая ею производительность труда обслуживающего персонала и себестоимость получаемой продукции являются важнейшими экономическими показателями создаваемой новой техники.
Одним из важнейших экономических требований при изготовлении машин является снижение (в разумных пределах) возможной массы машин, так как это связано с общегосударственной задачей экономии металла и снижает стоимость изготовления машин.
Социальные требования заключаются в обеспечении максимальной безопасности, легкости управления и создании нормальных условий труда для обслуживающего персонала.
Безопасность обслуживания достигается установкой защитных ограждений вращающихся деталей, исключением возможности поражения рабочих электрическим током, устройством всевозможных средств сигнализации при производстве работ.
Социальные требования при проектировании буровых машин и механизмов должны рассматриваться как обязательные, так как условия труда рабочих относятся к одним из самых тяжелых и опасных, особенно при бурении скважин в подземных условиях.
Технические требования. Основываются на последних достижениях и тенденциях развития отечественного и зарубежного машиностроения. Основные параметры должны быть не ниже стандартов мирового уровня.
|
|
Буровые машины должны иметь высокие прочность, надежность, энерговооруженность, коэффициент полезного действия и минимальные энергозатраты. При создании машин должны быть заложены предпосылки увеличения степени их использования во времени за счет повышения надежности, предусмотрены резервы их дальнейшего конструктивного совершенствования.
Эксплуатационным требованиям нужно уделять первостепенное внимание при разработке конструкции машины, на стадии ее испытаний, при выполнении доводочных работ. Исходя из того, что работоспособность машины в процессе эксплуатации будет поддерживаться проведением технического обслуживания и ремонтов, поэтому необходимо предусмотреть возможности: доступа к узлам машины для технического обслуживания и ремонта; контроля технического состояния узлов машины; быстро заменять узлы и детали, подвергающиеся наиболее интенсивному изнашиванию или разрушению.
Технологические требования определяют затраты труда и средств при изготовлении буровых машин и механизмов. К ним относятся: максимальное применение в конструкции стандартных деталей, рациональный выбор материала и способа получения заготовок с целью экономии металла при наибольшем коэффициенте использования; максимальное уменьшение числа деталей и упрощение кинематической схемы (простота конструкции машин); правильный выбор посадок и допусков, что обеспечит точное взаимодействие деталей при эксплуатации.
Специальные требования определяются специфическими условиями работы буровых машин и механизмов. Машины и механизмы буровых установок должны состоять из транспортабельных, легко монтируемых и демонтируемых узлов с учетом доставки их к месту бурения.
Корпуса машин и все их узлы и детали должны иметь высокую механическую прочность и антикоррозионное покрытие (лакирование, горячее цинкование, хромирование, оксидирование).
При бурении скважин в шахтах электрооборудование буровых машин должно иметь взрывобезопасное исполнение. В конструкциях машин нельзя применять легковоспламеняющиеся материалы.
При разработке конструкции машин специалисты руководствуются многими принципами, которые являются специфичными (индивидуальными) для процесса проектирования конкретной машины, и сравнительно небольшим числом общих принципов проектирования, характерных для процесса создания всех машин.
Принципы конструирования постоянно изменяются и зависят от социальных условий жизни, прогресса, науки и техники. Главенствующее значение тех или иных факторов в различные периоды также может меняться.
Создание новых буровых установок на уровне требований современной науки и техники обязательно должно учитывать тенденцию развития собственно процесса бурения и бурового оборудования. Однако поскольку буровая машина – это, прежде всего машина, выполняющая, как и все машины другого назначения, определенный рабочий процесс, то ее создание подчиняется общим законам машиностроения и к ней предъявляются общие требования как к машине вообще.
Поскольку разработка новой конструкции, изготовление опытных образцов, а затем и серийное производство требуют продолжительных сроков, конструктор должен изыскивать методы ускорения создания новых инструментов. При этом первостепенное значение имеет экономическая эффективность. Она должна учитывать весь комплекс факторов.
Эффективность новой конструкции, по сравнению с существующей, определяется рядом показателей:
· обобщенный показатель (Rо):
Ro=K1C1+K2C2+…+KnCn, (1)
где K1, K2…Kn – свойства конструкции, влияющие на оценку эффективности;
С1, С2…Сn – коэффициенты весомости, характеризующие относительную важность каждого свойства (выбираются на основе экспертных оценок);
· интегральный показатель (RΣ):
где Q – полезная отдача (например, стоимость пробуренного числа метров или скважин новой конструкции, породоразрушающего инструмента);
PΣ – сумма расходов на амортизацию, подготовительные расходы, монтаж, демонтаж, материалы.
Этот показатель должен быть больше единицы, иначе новая конструкция будет убыточной по сравнению с ранее применявшейся;
· суммарный экономический эффект:
=
1.2. Главные направления современного бурового машиностроения
Современное буровое машиностроение характеризуется следующими главнейшими направлениями: высокая производительность, механизация и автоматизация, надежность, стандартизация, специализация и унификация, агрегатность, увеличение агрегатной мощности, минимальный вес машин, техническая эстетика и техника безопасности, непрерывное совершенствование машин при эксплуатации.
1.2.1. Производительность труда
Создаваемые конструкторами машины должны обеспечивать большую производительность по сравнению с существующими. Различают следующие основные направления в повышении производительности машин: увеличение скорости выполнения рабочих процессов и непрерывность технологических процессов.
Скорости бурения разведочных скважин значительно возросли. Это произошло за счет применения рациональных породоразрушающих инструментов, а также в результате использования оптимальных режимов бурения (частота вращения бурового снаряда, осевой нагрузки на породоразрушающий инструмент, качества и количества промывочной жидкости).
У первых буровых станков для колонкового бурения частота вращения составляла 60 – 200 мин-1, в то время как современные буровые станки позволяют вращать породоразрушающий инструмент с частотой 500 – 800 мин-1, а при бурении алмазными коронками 2000 – 3000 мин-1.
Применение различных частот вращения породоразрушающего инструмента, как известно, зависит от геолого-технических условий бурения и глубины скважины.
Возросла и нагрузка на породоразрушающий инструмент: в колонковом бурении при применении твердосплавного породоразрушающего инструмента диаметром 76 – 93 мм она достигает 15 – 25 кН.
Известно, что в повышении производительности бурения важную роль играет очистка забоя скважины от выбуренной породы. В связи с этим возросла и скорость движения восходящего потока промывочной жидкости: при колонковом бурении в настоящее время она достигла 0,5 – 0,8 м/с, а в глубоком разведочном бурении она составила 1,2 – 1,6 м/с.
Одним из условий увеличения скорости выполнения технологических процессов (бурении скважины) является сокращение времени на операции, связанными с монтажно-демонтажными работами, спуском и подъемом инструмента, геофизическими исследованиями в скважинах и др. Применение самоходных буровых установок позволило сократить длительность монтажно-демонтажных работ до нескольких часов; монтажные работы в глубоком бурении сократились с 2 – 3 месяцев до 2 – 3 суток.
Непрерывность технологических процессов. Конструкторские особенности машин, наличие вспомогательных операций и ряд других факторов придают технологическим процессам прерывистый характер течения. Несомненно, это касается и процесса бурения скважин.
Конструкция машины должна удовлетворять принципам научной организации труда, физиологическим и психологическим особенностям обслуживающего персонала.
Значительное влияние на непрерывность протекания рабочих процессов оказывают вспомогательные операции, причем по затратам времени они могут превышать основные технологические процессы. В связи с этим на стадии проектирования бурового оборудования следует уделить особое внимание возможности сокращения непроизводительных затрат.
1.2.2. Механизация и автоматизация
Это один из важнейших резервов повышения производительности труда.
Увеличение мощностей и скоростей машин привело к снижению возможностей человека как управляющего и контролирующего звена. Причиной этого стало весьма существенное препятствие – психологические и физиологические особенности человека, который управляет этим процессом.
На реакцию человека на определенный сигнал необходимо какое-то время, которое обусловлено инерционностью его нервной системы. В среднем, как показали исследования, время простой ответной реакции человека составляет 0,1 с. Время сложной реакции, когда информаторов может быть несколько и на каждый из них должен быть дан особый ответ, не менее 0,4 с. А если при этом учесть, что физические возможности каждого человека в отличие от машины зависят от субъективных факторов и окружающих условий, то можно утверждать, что это время даже у одного человека меняется значительно.
Человек, управляющий машиной и выполняющий подобные операции, быстро устает (физически и психически), замедляет и ограничивает темп выполнения производственных процессов, внимание начинает рассеиваться, что может привести к поломкам, авариям, несчастным случаям. Подтверждением этого может служить факт существования низких и высоких производственных показателей в любой отрасли промышленности, где преобладают ручные и машинно-ручные операции, причем они отличаются друг от друга в 1,5 – 2, а иногда и большее число раз.
Уровень механизации трудоемких процессов и операций можно определить из соотношения:
где Тм – время механизированного труда (без применения ручного труда);
ТΣ – общее время процесса.
Можно воспользоваться также коэффициентом фактической энерговооруженности труда:
где Э1 – энергия, потребленная всеми механическими приводами непосредственно от первичных двигателей, кВт;
Э2 – вся энергия, потребленная электродвигателями, кВт;
Э3 – энергия, потребленная электроаппаратами и приводами, кВт;
Σt – суммарное количество отработанных человеко-часов всем коллективом рабочих предприятия.
По коэффициенту фактической энерговооруженности труда судят об уровне механизации и автоматизации труда.
1.2.3 Надежность
Качественное решение вопросов проектирования производства и эксплуатации буровых машин и механизмов, а также бурового оборудования в настоящее время невозможно без использования и учета основных положений и рекомендаций теории надежности.
Надежностью бурового оборудования называют его свойство выполнять заданные функции, сохраняя во времени значения установленных эксплуатационных показателей в пределах, соответствующих заданным режимам и условиям применения, технического обслуживания, ремонтов, хранения и транспортирования. Надежность является важнейшей качественной характеристикой бурового оборудования.
В зависимости от назначения применяемого объекта надежность может характеризоваться безотказностью, долговечностью, ремонтопригодностью, сохраняемостью в отдельности или определенным сочетанием перечисленных свойств.
Безотказностью систем оборудования различных буровых установок, их узлов и деталей называют свойство сохранения работоспособности в течение некоторого времени или некоторой наработки, измеряемой, например, погонными метрами бурения, машино-часами и др.
Долговечность – свойство объекта сохранять работоспособность до наступления предельного состояния при установленной системе технического обслуживания и ремонтов.
Различают восстанавливаемые и невосстанавливаемые объекты, т. е. их работоспособность в случае отказа подлежит или не подлежит восстановлению в данной ситуации. Кроме того, выделяют: ремонтируемые объекты, т. е. их работоспособность может быть восстановлена, но только на ремонтном предприятии или в ремонтной мастерской (станки, насосы, труборазвороты, электромоторы и др.), и неремонтируемые, работоспособность которых при отказе или повреждении не подлежит восстановлению (резьбовые соединения породоразрушающий инструмент). Неремонтируемые объекты являются одновременно и невосстанавливаемыми.
Надежность элементов одноразового срабатывания характеризуется вероятностью безотказного срабатывания:
где r – число отказавших элементов за время испытаний;
N – число элементов испытываемых объектов.
Сохраняемость – свойство непрерывного сохраненияобъектом исправного и работоспособного состояния в течение и после хранения и транспортирования.
Срок сохраняемости – календарная продолжительность хранения и (или) транспортирования объекта, в течение и после которой значения показателей безотказности, долговечности и ремонтопригодности сохраняются в установленных пределах.
Ниже приводятся также общие понятия о других, не мене важных, терминах надежности.
Исправное состояние (исправность) – состояние объекта, при котором он соответствует хотя бы одному из требований нормативно-технической или конструкторской документации.
Работоспособное состояние (работоспособность) – состояние объекта, при котором значение всех параметров, характеризующих способность выполнять заданные функции, соответствуют требованиям нормативно-технической и конструкторской документации.
Предельное состояние – состояние объекта, при котором его дальнейшее применение по назначению недопустимо или нецелесообразно, либо восстановление его исправного или работоспособного состояния невозможно или нецелесообразно.
Повреждение – событие, заключающееся в нарушении исправного состояния объекта при сохранении работоспособного состояния.
Отказ – событие, заключающееся в нарушении работоспособного состояния объекта.
Показатель надежности представляет собой количественную характеристику одного (единичный показатель надежности) или нескольких (комплексный показатель надежности) свойств, составляющих надежность объекта.
Технический ресурс – наработка объекта от начала его эксплуатации или ее возобновления после ремонта определенного вида до перехода в предельное состояние.
Срок службы – календарная продолжительность от начала эксплуатации объекта или ее возобновления после ремонта определенного вида до перехода в предельное состояние.
Наработка на отказ То это:
(7)
Где – наработка буровой машины или агрегата;
– суммарное число отказов n, соответствующего технического объекта в течение этой наработки;
N – количество однотипных технических объектов, каждый из которых имел наработку ti и ni отказов.
Средняя наработка на отказ – отношение наработкивосстанавливаемого объекта к математическому ожиданию числа его отказов в течение этой наработки.
Среднее время восстановления Тс.в. – показатель ремонтопригодности восстанавливаемого технического объекта:
(8)
где N – количество технических объектов;
τi – суммарное время простоев каждого объекта, ч;
ni – количество отказов.
Коэффициент готовности Кг – комплексный показатель надежности и используется для оценки влияния уровня надежности буровых машин и агрегатов на их производительность.
При установившемся режиме эксплуатации коэффициент готовности определяется из выражения:
(9)
Коэффициент готовности учитывает безотказность и ремонтопригодность объекта, а также характеризует вероятность его работоспособности в любой момент времени, кроме периодов, в течение которых использование объекта по назначению не предусматривается или не производится.
Коэффициент технического использования Кт.и. зависит как от безотказности работы, так и от ремонтопригодности и определяется выражением:
где Траб – суммарная длительность исправной работы бурового оборудования за время его эксплуатации, ч;
Трем – суммарное время простоев оборудования из-за плановых и внеплановых ремонтов, ч;
Тобсл – суммарное время простоев оборудования из-за планового и внепланового обслуживания, ч.
Интенсивность отказов – условная плотность вероятности f(t) возникновения отказа невосстанавливаемого объекта, определяемая для рассматриваемого момента времени при условии, что до этого отказ не возник. Математически она выражается отношением:
где Р(𝑡) – вероятность безотказной работы.
Интенсивность отказов изменяется со временем. В начальный период работы изделия интенсивность отказов велика; здесь многие изделия выходят из строя из-за скрытых дефектов, которые не были обнаружены в процессе производства. Этот период называется периодом приработки.
Во втором периоде интенсивность отказов примерно постоянная (или медленно возрастает). Это период нормальной эксплуатации.
В третьем периоде вероятность отказов возрастает из-за явлений износа и старения, которые наблюдаются в изделиях.
Приведенные выше уравнения являются общими и пригодны они для любых законов распределения наработки до отказа (срока службы).
Наиболее распространенными законами распределения для определения характеристик надежности и долговечности являются следующие:
· экспоненциальное распределение;
· нормальное распределение;
· распределение Вейбулла;
· логарифмически нормальное распределение.
Для оценки долговечности бурового оборудования применяются следующие основные показатели долговечности.
Средний ресурс, который может быть представлен следующим выражением:
(12)
где F(t) – функция распределения ресурса.
Гамма-процентный ресурс – наработка, в течение которой объект не достигнет предельного состояния с заданной вероятностью v, %. Определяется он из уравнения:
где – гамма-процентный ресурс.
Назначенный ресурс – суммарная наработка объекта, при достижении которой применение по назначению должно быть прекращено.
Средний срок службы определяется по формуле (12).
Гамма-процентный срок службы – календарная продолжительность от начала эксплуатации объекта, в течение которого он не достигнет предельного состояния с заданной вероятностью v, %. определяется по формуле (13).
Назначенный срок службы – календарная продолжительность эксплуатации объекта, при достижении которой применение объекта по назначению должно быть прекращено.
Долговечность буровых машин и агрегатов оценивается суммарной наработкой оборудования до полного исчерпания работоспособности или предельного состояния (капитального ремонта). различают три категории долговечности:
а) Физическая долговечность τф бурового оборудования зависит от долговечности составляющих ее частей, агрегатов, сопряжения отдельных деталей. Определяется она по следующей зависимости:
где Sм и Sн – соответственно предельно допустимый и начальный зазоры, мм;
tgβ – характеризует скорость изнашивания сопряжения (нарастание зазора) и определяется опытным путем.
б) Моральная долговечность τм оборудования выражает срок службы, после которого оно становится технически и экономически неэффективным по сравнению с новым более совершенной конструкции. Если последнее оборудование обладает малым «запасом совершенства», оно быстро стареет (морально изнашивается). Моральная долговечность существующего оборудования может быть настолько незначительной, что оно не успеет окупить себя достаточно эффективной работой.
Показателем моральной долговечности бурового оборудования является коэффициент морального износа, который определяется по следующей формуле:
Здесь С1 и С2 – соответственно себестоимость единицы продукции старого и нового оборудования;
ΔС – экономия от ввода в эксплуатацию нового оборудования.
Значения коэффициента морального износа 0-1. В случае С1=С2 коэффициент =0, т.е. оборудование еще морально не износилось и современно. При С2≤С1 значение ΔС →1, а
→1. это означает почти полный моральный износ оборудования, которое независимо от фактического физического состояния необходимо заменить новым, более совершенным. В этом случае ресурс работы оборудования не будет полностью использован и затраты на обеспечение высокой его долговечности окажутся неоправданными.
в) Технико-экономическая долговечность τэ определяет экономически целесообразный срок службы бурового оборудования, который соответствует минимальному значению удельной себестоимости его эксплуатации. В проценте износа оборудования падает его производительность, возрастают эксплуатационные расходы и стоимость ремонта.
Важное значение в теории надежности отводится понятию отказа, или события заключающегося в нарушении работоспособности объекта.
Критерий отказа представляет собой признак или совокупность признаков неработоспособного состояния объекта, которые установлены в нормативно-технической и (или) конструкторской документации.
К независимым относятся отказы, которые не вызваны отказом другого объекта, а к зависимым – отказы, обусловленные отказом другого объекта.
Внезапные отказы вызваны скачкообразным изменением одного или нескольких основных параметров элементов в результате различных воздействий. Причиной внезапных отказов могут быть различные нарушения рабочих режимов машин и механизмов, правил их эксплуатации, а также отдельные дефекты элементов машин. Характерным для внезапных отказов является их независимость от времени эксплуатации элемента. Постепенные отказы характеризуются постепенным изменением заданных параметров объекта, обусловленным изнашиванием, накоплением усталостных повреждений, а также старением деталей. Таким образом, с увеличением времени работы машины опасность постепенных отказов возрастает.
Различают перемежающийся (многократно возникающий самоустраняющийся отказ одного и того же характера), конструкционный (возникающий в результате нарушения правил и норм конструирования), производственный (возникающий при нарушении установленного процесса изготовления или ремонта) и эксплуатационный (нарушение правил и условий эксплуатации) отказы.
Своевременное и правильное установление вида (конструкционный, производственный и др.) и периода (при транспортировании, хранении или в процессе эксплуатации объекта) возникновения отказа позволяет обоснованно подходить к разработке мероприятий по повышению надежности бурового оборудования.
На этапе проектирования новой конструкции нужно придерживаться следующих правил надежности:
· конструкция должна содержать максимально возможное число элементов, проверенных на практике;
· использование стандартных и унифицированных деталей и узлов;
· конструкция должна обладать контролеспособностью;
· элементы конструкции должны подвергаться тщательному расчету на статическую и динамическую прочность (учитываются максимальные нагрузки, наиболее рабочие условия, минимальная прочность материала);
· устанавливаются нормы прочности, регламентирующие допустимые запасы прочности и необходимый объем экспериментальных исследований.
На этапе опытного производства и испытания:
· опытные экземпляры должны быть предназначены для всесторонних исследований и испытаний в лабораторных и стендовых условиях;
· определяется конструкционная прочность и износостойкость отдельных элементов конструкции;
· опытная конструкция испытывается на надежность в условиях, имитирующих натурные;
· проводятся специальные испытания, выявляющие работоспособность в экстремальных условиях эксплуатации;
· после устранения выявленных отказов или неисправностей проводятся приемочные производственные испытания, и утверждается эталон для серийного производства.
1.2.4. Стандартизация, специализация и унификация
Бурение скважин осуществляется для решения самых разнообразных задач в различных геолого-технических условиях. Все это обуславливает применение различных способов и технологических режимов. Разработка и выпуск оборудования узкого и целевого назначения в таких условиях, несомненно, приводят к его многотипности, а это значительно затрудняет организацию его серийного производства, эксплуатацию, обслуживание и ремонт. В связи с этим вопросы стандартизации и унификации бурового оборудования приобретают важное значение.
Стандарт в широком смысле слова – образец, эталон, модель, принимаемые за исходные для сопоставления с ними других подобных объектов.
Стандартизация – деятельность, заключающаяся в нахождении решений для повторяющихся задач в сфере науки, техники и экономики, направленная на достижение оптимальной степени упорядочения в определенной области.
Применение стандарта способствует улучшению качества готовой продукции, повышению производительности труда, уровня унификации, развитию автоматизации производственных процессов, росту эффективности эксплуатации и ремонта изделий.
Стандартизация буровых станков (буровых установок), прежде всего, требует определения их номенклатуры по целевому назначению – станки для геологической съемки, поисков и картирования, для бурения скважин на твердые полезные ископаемые, для инженерно-геологических изысканий и гидрогеологических исследований, бурения разведочных и эксплуатационных скважин на воду, нефть и газ, геофизических исследований, технических (взрывных, кабельных и др.) скважин.
Одним из важнейших требований, предъявляемых к буровому оборудованию, является хорошая транспортабельность. Особенно это важно при разведке в труднодоступных местах (горная местность, болота и др.). По этому признаку могут быть выделены буровые станки, разборные на отдельные узлы, приспособленные для транспортирования вручную, гужевым и водным транспортом, а также вертолетами. Возможно создание самоходных буровых установок на транспортных базах высокой проходимости.
Способ бурения, определяемый условиями бурения и требованиями к опробованию, требует соответствующих параметров оборудования и, несомненно, влияет на его конструктивный облик. А это в свою очередь требует подразделения бурового оборудования в зависимости от способов бурения.
Однако совпадение или близость параметров позволяет сочетать в одном оборудовании возможность применения нескольких способов бурения. Следовательно, могут быть выделены группы оборудования, предназначенные для одного или нескольких технологических способов (вращательный, ударно-вращательный и др.), т.е. разработан определенный ряд буровых установок для применения в данных горнотехнических условиях. Таким образом, при составлении стандартов бурового оборудования учитывают следующие исходные данные: условия эксплуатации; конструкции буровых скважин; телескоп бурового инструмента; промышленные способы бурения скважин; перспективы развития геологоразведочных работ; достижения отечественного и зарубежного опыта бурового машиностроения.
В целях повышения экономической эффективности бурения скважин от 0 до 3000 метров предусмотрено создание параметрического ряда бурового оборудования, отличающихся друг от друга числовыми значениями основных параметров (глубиной бурения, грузоподъемностью, мощностью привода, массой и др.). Стандарты предусматривают использование вращательного и ударно-вращательного способов с применением алмазных, твердосплавных коронок и шарошечных долот.
Параметрический ряд подразделяет все буровые установки на 8 классов и характеризует каждый класс 15-ю значениями параметров.
В качестве главного параметра принята номинальная глубина бурения вертикальных скважин алмазными и твердосплавными коронками. Числовые значения главного параметра для каждого класса установок при построении ряда разбивали на ряды предпочтительных чисел, образующихся по закону геометрической прогрессии.
Основным буровым снарядом для установок 3 - 8-го классов принята стальная бурильная колонна диаметром 50 мм с алмазным породоразрушающим инструментом диаметром 59 мм. Масса 1м такого снаряда (с учетом массы соединительных элементов) для свечей длиной 18,6 – 9,5 м составляет 6,5 – 6,9 кг.
Номинальные геолого-технические условия – бурение скважин в вертикальном направлении при отсутствии интенсивного искривления и сужения ствола, обвалов стенок скважины, поглощений промывочной жидкости.
Мощность станков обеспечивает бурение скважин до проектной глубины частотой вращения до 600 мин-1. Однако применение легкосплавных бурильных труб позволит увеличить возможную глубину бурения с такой частотой вращения. Стандарт предусматривает применение электрического привода, двигателей внутреннего сгорания, а также гидравлических и пневматических двигателей. В технической характеристике дана мощность только для электродвигателя.
Стандарт предусматривает такие модификации станков типа УКБ: стационарные, самоходные, смонтированные на различных транспортных базах, и передвижные на санях или прицепах. Стационарные подразделяются на блочные, перевозимые отдельными блоками, и разборные (на узлы) для транспортирования в подземных условиях на поверхности.
Стандарт предусматривает наименьшую (для алмазного бурения скважин малого диаметра) и наибольшую (при бурении скважин малого диаметра) подачи промывочной жидкости, промежуточные значения которых могут быть получены путем изменения числа ходов вытеснителя (поршня, плунжера) с помощью коробки передач и применения сменных рабочих элементов (вытеснителей) различных диаметров.
Номинальная гидравлическая мощность соответствует сочетанию средних значений подач и давлений нагнетания, по ее величине подбирается двигатель для насоса основной комплектации. Максимальная гидравлическая мощность рассчитана на получение максимального давления при максимальной подаче.
Главным параметром при разработке ряда буровых установок на нефть и газ принята грузоподъемность на крюке.
Основные параметры буровых установок для бурения на твердые, жидкие и газообразные полезные ископаемые приведены в учебной справочной литературе.
Специализация предусматривает выпуск бурового оборудования по отдельным типам, пригодным для конкретных условий бурения. Она ограничивает область применения машины, упрощает ее конструкцию, сокращает массу, снижает стоимость изготовления, повышает производительность труда.
Специализированные установки получают экономически оправданное распространение при массовом производстве. Например, установки шнекового и вибрационного бурения широко применяются при бурении сейсмических, гидрогеологических и инженерно-геологических скважин, т.к. объем бурения достигает значительной величины (десятки миллионов метров). Вполне оправданно создание специализированных установок для разведки россыпных месторождений в прибрежных зонах морей и океанов в связи с широким развитием работ в этом направлении, для бурения геофизических скважин и т.д.
Однако специализация увеличивает разнотипность буровых станков, т.к. они выпускаются небольшими сериями, что вызывает значительные трудности при их эксплуатации – затрудняется освоение бурового оборудования обслуживающим персоналом, ухудшается снабжение запасными частями, нет возможности применять на заводах более сложную технологическую оснастку, что влияет на качество и стоимость изготовления бурового оборудования. Все это отражается на производительности бурения и стоимости проходки скважины.
Конструирование буровых машин и механизмов следует вести таким образом, чтобы их параметры максимально соответствовали технологии того или иного способа бурения и условиям ведения работ. это возможно только при создании унифицированных комплексов.
Подробный анализ стандартов говорит о том, что в пределах каждого типоразмера возможно создание множества разновидностей буровых станков по способам бурения, типу привода, транспортабельности и, как следствие этого, по конструктивному исполнению. Следовательно, стандарты должны рассматриваться как основа для создания унифицированного оборудования.
Унификация – это приведение машин к единой форме или системе. Она получила широкое распространение в машиностроении, так как способствует удешевлению изготовления оборудования, сокращает номенклатуру изделий, упрощает эксплуатацию оборудования и облегчает его освоение и ремонт.
Унифицированная буровая система состоит из базовой модели и ряда ее отдельных модификаций. Базовая модель – основа комплекса; она предназначена для бурения в самых распространенных условиях с использованием широко применяемых способов бурения.
Для работы в специфических условиях разрабатываются различные модификации базовой установки. Следовательно, несколько типов специализированных станков могут быть заменены одним унифицированным комплексом.
Различают внутритипоразмерную, межтипоразмерную и отраслевую унификацию.
При внутритипоразмерной унификации оборудование в пределах каждого типоразмера по мощности и грузоподъемности разрабатывается в виде агрегатированных комплексов унифицированных узлов и элементов, различные сочетания которых позволяют получить модификации станков с требуемыми параметрами.
Основой такого комплекса является группа узлов привода и трансмиссии, обязательная для всех модификаций, а сменными узлами – пары шестерен или элементы цепных или клиноременных передач, вращатели с различными диапазонами частот вращения и крутящими моментами, проходными отверстиями под бурильные или обсадные трубы, механизмы подачи, лебедки.
Возможно различное исполнение оборудования по транспортабельности – разборный станок может монтироваться на санях в составе передвижной установки или на самоходной транспортной базе.
Создание агрегатированных комплексов унифицированных узлов дает возможность сочетать в одной модификации несколько способов бурения (станки вращательного бурения могут комплектоваться съемными ударными механизмами, а станки ударно-канатного бурения – съемными вращателями).
Межтипоразмерная унификация заключается в применении одних и тех же деталей и узлов (лебедки, вращатели и др.) в станках смежных типоразмеров. Важным фактором ее применения, как и внутритипоразмерной унификации, является наличие индивидуального гидропривода рабочих органов буровых станков, что позволяет ограничивать приводную мощность с помощью рассчитанных на определенное давление масла предохранительных клапанов гидросистемы.
Межотраслевая унификация заключается в применении унифицированных узлов и деталей не только в буровом машиностроении, но и в других отраслях промышленности (автомобилестроение, станкостроение, и др.).
Примером межотраслевой унификации могут быть коробки скоростей, муфты сцепления и маслонасосы, сконструированные для автомобилей, но применяемые также в буровых станках (коробки скоростей, главного фрикциона и маслонасоса для привода гидросистемы).
Целесообразность использования в буровых станках автомобильных коробок скоростей очевидна, так как они меньше по габаритам, легче по массе и дешевле специализированных коробок скоростей буровых станков.
Автомобильные коробки скоростей изготавливаются в одном блоке с муфтами сцепления. Это сухие нормально замкнутые фрикционные муфты. По конструктивной схеме они близки к схемам главных фрикционов буровых станков, но легче, качественнее, надежнее в работе и дешевле. Поэтому, применяя автомобильную коробку скоростей, целесообразно использовать в качестве главного фрикциона бурового станка муфту сцепления от того же автомобиля.
1.2.5. Агрегатность и масса
Агрегатность предусматривает объединение рабочей машины и привода в один блок. Собираются блоки агрегата в заводских условиях высококвалифицированными рабочими (слесарями-сборщиками), благодаря чему достигается высокая точность сборки машин. При эксплуатации такая установка не требует частых наладок, а при выполнении монтажно-демонтажных работ не требуются высококвалифицированные монтажники.
Важным фактором агрегатирования машин и привода является также то, что двигатель в этом случае подбирается с нагрузочными характеристиками, которые соответствуют нагрузочной характеристике исполнительных органов рабочей машины, а его мощность строго соответствует мощности, необходимой для выполнения рабочего процесса.
С энергетической точки зрения агрегатированная установка работает более экономично, имеет высокий коэффициент использования установленной мощности.
Мощность вновь создаваемых машин и агрегатов растут. Так, например, в 40-х годах для бурения скважин на 500 м установки комплектовались двигателем мощностью 15 - 20 кВт, в настоящее время установки, предназначенные для бурения на ту же глубину, комплектуются двигателями мощностью 40 - 50 кВт. Почти в 3 - 4 раза возросла установочная мощность оборудования для глубокого разведочного бурения на нефть и газ.
Масса машины является одним из основных показателей, учитываемых при проектировании нового оборудования. Снижение массы обеспечивает транспортабельность бурового оборудования, особенно в горных и труднодоступных районах. Масса бурового станка влияет на его принципиальную схему, а следовательно, на эффективность процесса бурения и скорость вспомогательных операций.
В отдельных случаях конструкторы, наоборот (несомненно, в разумных пределах), стремятся повысить массу проектируемой буровой машины или механизма. Например, установки для бурения взрывных скважин на карьерах шарошечными долотами должны иметь весьма значительную массу, чтобы создать необходимую осевую нагрузку на породоразрушающий инструмент. Нет смысла снижать массу и талевых блоков, так как от нее зависит скорость опускания ненагруженного (порожнего) элеватора.
1.2.6. Техническая эстетика и техника безопасности
Техническая эстетика – это наука о красоте в технике. Основная ее задача сделать труд человека, занятого на производстве, не только высокопроизводительным, но и приятным, доставляющим удовлетворение.
Цель технической эстетики – решение вопросов отношений человека и техники в рабочей обстановке, а также создание таких условий труда, которые способствовали бы гармоничному развитию человека, росту его духовной культуры. При работе с новейшим оборудованием функции человека сводятся к контролю хода технического процесса. Человек воспринимает огромные потоки информации в рабочей среде: взаимодействие света, цвета, формы окружающего интерьера и оборудования, ударов, шума и др. При этом сложный и напряженный характер работы на буровой требует быстроты реакции, сосредоточенности и большого нервного напряжения. Окружающая среда не должна отрицательно влиять на нервную систему рабочего. Человек меньше устает при работе в условиях технически совершенного производства, чистоте и порядке.
Поскольку целый ряд вопросов технической эстетики тесно связан с техникой безопасности и промышленной санитарией, то при конструировании новых буровых машин и механизмов они должны решаться совместно.
Основными объектами технической эстетики являются: световое и цветовое оформление орудия труда и промышленного интерьера; форма машин и механизмов; температура, шум и вибрация; рациональная организация рабочего места; производственная одежда.
Окраска машины и отдельных ее частей, кроме предохранения металла от коррозии, влияет на общий вид машины, является одним из важных требований повышения безопасности работы. Окраска машины не должна быть монотонной: подвижные (вращающиеся) части станка следует окрашивать одним (контрастным) цветом. Контрастный цвет (желтый, красный) настораживает человека, привлекает внимание. Желтый цвет хорошо выделяется на черном фоне, издалека предупреждает об опасности. В красный цвет окрашивают крюки подъемных кранов, рукоятки, кнопки и т.д.
В зависимости от угла зрения на окрашенную поверхность или предмет одни и те же цвета воспринимаются по-разному.
1.2.7. Совершенствование машин
Научно-технический прогресс в геологоразведочном бурении связан с массовым внедрением прогрессивных технологических способов и созданием технических средств, которые позволяют наиболее полно использовать их преимущества и возможности. Сюда относят буровое оборудование, отвечающее требованиям применения различных способов бурения и горнотехнических условий, а также специализированные технические средства – породоразрушающий инструмент, высокочастотные гидроударные машины, снаряды со съемными керноприемниками и др. Все это в сочетании с передовой организацией труда позволяет достигать высоких технико-экономических и качественных показателей.
В то же время следует иметь в виду, что прогресс в области науки и техники, совершенствовании технологии выполнения производственных процессов способствует быстрому старению машин. Сравнительно за короткий срок машина морально устаревает, и становится несовершенной – ее качественные и количественные показатели не соответствуют новым требованиям техники и технологии производства, т.е. дальнейшая эксплуатация такой машины становится нерентабельной. Поэтому устаревшие машины следует своевременно заменять новыми, более совершенными.
Дата добавления: 2016-01-05; просмотров: 79; Мы поможем в написании вашей работы! |
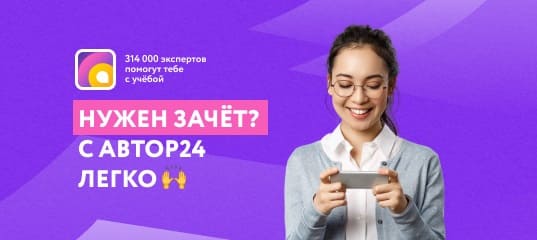
Мы поможем в написании ваших работ!