Точность при сборке машин. Особенности достижения требуемой точности при сборке типовых узлов машин
Точность сборки — характеристика и свойство технологического процесса сборки изделия. Точность сборки призвана обеспечивать соответствие действительных значений параметров изделия значениям, заданным в технической документации. Точность сборки зависит от ряда факторов:
1. точности размеров и формы,
2. шероховатости сопрягаемых поверхностей деталей,
3. взаимного положения деталей при сборке,
4. технического состояния средств технологического оснащения,
5. деформации системы «оборудование — приспособление — инструмент — изделие» в момент выполнения сборки и т. п.
Сборка — заключительный этап изготовления машины, в значительной степени определяющий ее эксплуатационные качества, так как в процессе сборки по разным причинам могут возникать погрешности взаимного расположения деталей и узлов. Одни и те же точно изготовленные детали при разных условиях соединения могут изменить долговечность машин в сотни раз.
К основным показателям точности сборки относят: точность относительного движения исполнительных поверхностей; точности их геометрических форм и расстояний между этими поверхностями; точность их относительных поворотов.
Точность сборки машин зависит от точности изготовления ее деталей, а последняя в свою очередь — от точности изготовления заготовок, поскольку их свойства в определенной степени передаются готовым деталям. Поэтому вопросы точности сборки решают комплексно для всего технологического процесса изготовления машины.
При сборке машины могут появляться ошибки взаимного расположения ее элементов, некачественные сопряжения, а также недопустимые деформации соединяемых деталей.
Основным критерием выбора метода достижения заданной точности сборки является обеспечение минимума затрат на изготовление деталей и сборку из них машины. При прочих равных условиях рекомендуется в первую очередь выбирать метод полной взаимозаменяемости одинаковых деталей, при котором сборка производится без подбора, пригонки и регулирования. Если применение указанного метода экономически нецелесообразно или технически невозможно обеспечить требуемую точность обработки деталей, то применяет методы неполной взаимозаменяемости.
При сборке методом полной взаимозаменяемости происходит лишь соединение сопрягаемых деталей и узлов, что обеспечивает поточную форму организации сборки, возможность кооперирования производства. Этот метод применяется в массовом и серийном производстве.
При сборке с неполной (частичной) взаимозаменяемостью допуски на размеры деталей больше, чем при полной взаимозаменяемости, а себестоимость изготовления деталей ниже. При этом имеется определенный незначительный процент риска сборки некачественного изделия, затраты на исправление которого перекрываются экономией при изготовлении собираемых деталей.
Метод групповой взаимозаменяемости применяют в тех случаях, когда конструктивные допуски меньше технологически выполнимых. Детали изготовляют с широкими допусками (низкой себестоимостью), разбивают на группы с более узкими допусками и собирают узлы по группам. Метод неприемлем для поточной сборки.
Метод регулирования точности сборки заключается в том, что размеры деталей, входящих в данное соединение, изготавливают с широкими и технологически приемлемыми допусками. Требуемая точность сборки обеспечивается введением необходимого числа прокладок или компенсирующего элемента. Метод позволяет регулировать точность не только при сборке, но и при эксплуатации.
Метод пригонки заключается в том, что заданная точность сопряжения обеспечивается пригонкой (удаление слоя материала опиливанием, притиркой и другими методами) детали, выбранной в качестве компенсирующей. Метод применяется в мелкосерийном производстве, исключается поточная сборка.
|
|
|
|
Дата добавления: 2016-01-04; просмотров: 53; Мы поможем в написании вашей работы! |
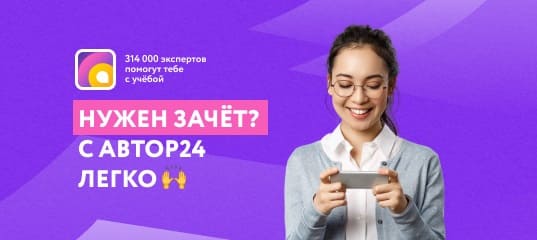
Мы поможем в написании ваших работ!