Методы отделочной обработки зубчатых поверхностей (сущность процессов, применяемое оборудование и технологическая оснастка)
После нарезания точность зубчатых колес для некоторых изделий оказывается недостаточной, т.к. во время обработки на поверхностях зубьев возникают погрешности профиля, недостаточно точным оказывается шаг зубьев и т.д.
Самым совершенным методом отделки стальных незакаленных зубчатых колес, а также колес из цветных металлов и сплавов является шевинговани е, выполняемое дисковыми или реечными шеверами. Шевер представляет собой режущее зубчатое колесо, имеющее точные размеры, боковые стороны зубьев которого имеют мелкие канавки, образующие режущие лезвия. Благодаря этим канавкам зубья шевера, перемещаясь по боковым поверхностям обрабатываемых зубьев со скоростью срезают тонкую волосовидную стружку.
Шеверы изготовляют с различной точностью в зависимости от требований к зубчатым колесам. Диаметр шевера выбирают максимально возможным по размерам шевинговального станка. При этом повышается его стойкость и точность обработки. Для повышения точности колес по шагу число зубьев шевера не должно быть кратным числу зубьев обрабатываемого колеса.
Закаленные зубчатые колеса подвергают отделочной обработке - зубохонингованию для снижения шероховатости боковых поверхностей зубьев, улучшения геометрических параметров колес и уменьшения шума от зацепления с другими колесами. Зубохонингованием также удаляют с зубьев забоины и заусеницы.
В качестве инструмента применяют хон-зубчатое колесо, рабочая часть которого изготовлена из абразивного материала (карбида кремния) на основе эпоксидной смолы. Хон изготовляют с увеличенным наружным диаметром и с учетом износа в процессе обработки колес. Число зубьев хона не должно быть кратным числу зубьев обрабатываемого колеса.
|
|
Процесс зубохонингования заключается в совместной обкатке заготовки и хона. При вращении зубчатой пары абразивные зерна хона обрабатывают боковые стороны зубьев заготовки за счет микрорезания. Скорость вращения пары, находящейся в зацеплении, во много раз больше скорости при шевинговании.
Зубохонингование применяют для закаленных, прямозубых и косозубых цилиндрических зубчатых колес. Этим способом можно обрабатывать и незакаленные колеса. В производстве широко используют алмазно-металлические зубчатые хоны. Стойкость их в 8-12 раз выше, чем у абразивных. Такими хонами можно обрабатывать зубчатые колеса высокой твердости.
Рассмотренные методы отделки не всегда и не в полной, мере могут устранить погрешности предыдущей обработки зубчатых колес. Значительные погрешности, особенно возникающие после термической обработки, устраняют зубошлифованием. Этим методом отделки получают высокую точность и малую шероховатость поверхности зубьев. Применение такого метода необходимо для колес, работающих с большими скоростями.
|
|
Зубья цилиндрических колес можно шлифовать двумя методами: копированием и обкаткой. Метод копирования соответствует зубонарезанию дисковой модульной фрезой. Шлифовальный круг профилируется по форме впадины зубьев заготовки. Круг вращается со скоростью vк одновременно совершает возвратно-поступательное движение, обеспечивая продольную подачуS пр. Шлифуют методом единичного деления. Однако на точность колеса большое влияние может оказать износ шлифовального круга: наибольшая погрешность возникает между первым и последними зубьями. Во избежание этого колесо последовательно поворачивают не на1/2, а на несколько зубьев, но так, чтобы были прошлифованы все впадины. Тогда износ круга влияет на точность меньше. Шлифование зубьев методом копирования можно выполнять на плоскошлифовальном станке. Этот метод более производителен, но менее точен, чем метод обката.
Шлифование зубьев методом обкатки основано на принципе зацепления обрабатываемого колеса с зубчатой рейкой. Роль рейки выполняют два шлифовальных круга, рабочие торцы которых расположены вдоль сторон зубьев рейки. Два шлифовальных круга можно разместить в одной впадине зуба только у крупных колес. Поэтому чаще одновременно шлифуют разноименные стороны двух соседних зубьев. Шлифуемое колесо совершает сложное движение; возвратно-вращательное вокруг своей оси, возвратно-поступательное вдоль оси воображаемой рейки и возвратно-поступательное вдоль своей оси для обработки зубьев по всей ширине. После обработки каждых двух боковых поверхностей зубьев колесо поворачивается на величину углового шага.
|
|
Качество обработки зубчатых колес, получаемых зубошлифованием, можно улучшить зубопритиркой. Её применяют для ответственных передач. Зубопритиркой получают поверхности высокого качества, доводя их до зеркального блеска, что увеличивает плавность работы, уменьшает шум, повышает долговечность пары. Применяют для закаленных зубчатых колес.
Притиры выполняют в виде зубчатых колес. Материалом для зубчатых притиров служит мелкозернистый серый чугун. Для притирки применяют жидкие абразивные смеси и пасты. Абразивные пасты обеспечивают большую производительность, чем жидкие смеси. В зацеплении в результате давления между зубьями притира и обрабатываемого колеса мелкозернистый абразив внедряется в более мягкую поверхности зубьев притира и удерживается на нем. Благодаря скольжению, возникающему между зубьями при вращении пары, зерна абразива снимают с обрабатываемого колеса мельчайшую стружку.
|
|
Зубопритирка обеспечивает более высокое качество обработки, чем зубошлифование, лишь в том случае, если зубчатое колесо было изготовлено точно. Максимальная толщина слоя, удаляемого с помощью притирки, не должна быть больше 0,05 мм. Значительные погрешности зубчатых колес исправить притиркой нельзя. Такие колеса надо предварительно шлифовать, а затем притирать.
В отдельных случаях вместо притирки применяют приработку зубьев. Она отличается от притирки тем, что колесо взаимодействует не с притиром, а с тем колесом, которое будет находиться с ним в зацеплении в собранном изделии. Приработку производят с помощью абразивного материала, ускоряющего процесс взаимного сглаживания поверхностей.
Основные понятия о сборке машин. Методы сборки
Сборка — есть заключительный этап изготовления объекта производства, после которого в большинстве случаев осуществляется путем испытания проверка эксплуатационных свойств этого объекта. Процесс сборки заключается в придании нужной взаимосвязи элементам собираемого объекта производства.
Сборочный процесс, как правило, состоит из таких последовательных стадий, как:
· ручная слесарная обработка и подготовка отдельных деталей к сборке (зачистка заусенцев, снятие фасок и др.), применяется преимущественно в единичном и мелкосерийном производстве и в малых объемах – в серийном;
· узловая сборка – соединение деталей в комплекты, подузлы, агрегаты (механизмы);
· общая сборка – сборка всей машины;
· регулирование – установка и выверка правильности взаимодействия частей и испытание машины.
Технологический процесс сборки – это соединение деталей в сборочные единицы, а сборочных единиц и отдельных деталей – в механизмы (агрегаты) и машины. Технологический процесс сборки подразделяется на операции, установки, позиции, переходы и приемы.
Изделие – это любой предмет или набор предметов основного производства, изготовляемых на предприятии. Изделиями машиностроительных заводов являются разнообразные машины: станки, автомобили, тракторы, экскаваторы, прессы и др., а также отдельные механизмы и агрегаты машин (двигатели, насосы, карбюраторы и др.) или отдельные детали (поршневые кольца, поршни, метизы).
Деталь – это первичный элемент изделия, выполненный из однородного материала без применения сборочных операций, но с использованием, если это необходимо, защитных или декоративных покрытий.
Методы сборки машин. В зависимости от типа производства, конструкции изделия, условий производства в машиностроении используются следующие методы сборки, позволяющие достичь требуемой точности замыкающего звена: сборка с полной, неполной и групповой взаимозаменяемостью деталей, сборка с пригонкой деталей по месту и с регулированием отдельных соединений, составляющих сборочную единицу.
Метод полной взаимозаменяемости предусматривает сборку изделий без какой-либо дополнительной обработки и подгонки деталей в процессе сборки. Основными факторами, обусловливающими использование этого метода, является необходимость обработки большого количества деталей с заданной степенью точности, т.е. в пределах заданных допусков на обработку. Такая обработка предполагает использование сложной и дорогостоящей технологической оснастки и контрольно-измерительных инструментов, что экономически оправдано лишь в крупносерийном и массовом производстве.
При сборке с неполной взаимозаменяемостью на размеры деталей, составляющих размерную цепь, преднамеренно устанавливаются несколько большие допуски, чем при расчете на полную взаимозаменяемость. При этом изготовление деталей будет более экономично. В основе метода лежит положение теории вероятности, согласно которому крайние значения погрешностей, составляющих звеньев размерной цепи встречаются значительно реже, чем средние значения. Такая сборка целесообразна в серийном и массовом производствах при многозвенных цепях. При этом процент сборочных единиц, которые возможно не будут отвечать техническим требованиям, может быть установлен заранее при расчете допусков на детали.
Метод групповой взаимозаменяемости предусматривает сортировку деталей, изготовленных с более широким полем допуска, на несколько групп. Тогда определенная группа допуска охватывающей поверхности собирается с той же группой охватываемой. В этом случае при сборке обеспечивается заданная степень подвижности сочленения без дополнительной пригонки. Такую сборку называют иногда селективной.
Метод групповой взаимозаменяемости применяют при сборке соединений высокой точности, когда точность сборки практически недостижима методом полной взаимозаменяемости (например, шарикоподшипники) или другими методами. При этом обеспечиваются одинаковые зазоры или натяги и необходимая точность соединения, определяемая эксплуатационными требованиями. Применяют этот метод сборки в крупносерийном и массовом производстве.
Недостатками данной сборки являются: дополнительные затраты на сортировку деталей по группам в зависимости от их размеров и на организацию хранения и учета деталей. Кроме того, усложняется работа планово-диспетчерской службы, поскольку требуется четкая организация сортировки деталей и их доставка к местам сборки. Усложняется также ремонт машин в связи с возрастанием номенклатуры запасных частей пропорционально числу размерных групп.
Метод сборки с пригонкой деталей по месту состоит в том, что на одной из сопрягаемых деталей допуск выходит за пределы установленных величин, а требуемый зазор в сопряжении достигается за счет индивидуальной пригонки этой детали путем снятия излишнего слоя металла, например, шабрением, опиловкой, притиркой и др. К недостаткам сборки с пригонкой следует отнести сравнительно высокую трудоемкость пригоночных работ, достигающую иногда до 40…50%, а в тяжелом машиностроении до 85% общей трудоемкости сборки машины, что обусловливает значительную потребность предприятия в слесарях-сборщиках высокой квалификации. Кроме того, имеют место трудности в определении реальной трудоемкости пригоночных работ, что усложняет планирование производства и установление технически обоснованных норм выработки на сборочные работы. Применяют этот метод сборки в единичном и мелкосерийном производствах.
Сборка с регулированием применяется в тех случаях, когда определенное положение (зазор, размер и т.п.) требуется сохранить в процессе эксплуатации. При этом требуемая точность сборки обеспечивается установкой дополнительных деталей – так называемых компенсаторов (регулировочных прокладок, винтов, колец, втулок и т.п.). Преимущество этого метода заключается в возможности восстановления первоначальной работоспособности изношенных сочленений, что осуществляется обычно в период плановых технических обслуживаний и ремонтов.
Дата добавления: 2016-01-04; просмотров: 36; Мы поможем в написании вашей работы! |
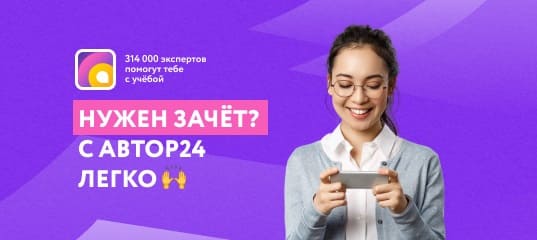
Мы поможем в написании ваших работ!