Технические требования на обработку резьбовых поверхностей деталей. Виды обработки резьбовых поверхностей деталей
Резьба - винтовая поверхность, образованная на телах вращения и применяемая для соединения, уплотнения или обеспечения заданных перемещений деталей машин и механизмов.
Общим требованием является полная взаимозаменяемость, т.е. обеспечение безусловной свинчиваемости деталей, образующих резьбовое соединение при их независимом изготовлении без подгонки или подбора, и надежное выполнение предписанных эксплуатационных функций. Несмотря на существенные различия типов резьб основные принципы достижения взаимозаменяемости, а также системы допусков и посадок резьбовых соединений являются едиными.
Наряду со срезанием припуска режущий инструмент должна обеспечиваться точность размеров (шага резьбы, наружного, среднего и внутреннего диаметров) формы заданного профиля резьбы и взаимного расположения поверхностей.
Резьбовые поверхности используют в технике как элементы крепежа и как кинематические звенья.
Все резьбы разделяются на 3 типа:
- крепежные;
- ходовые;
- конические.
По расположению резьбы делятся на:
- наружные;
- внутренние.
Наружные резьбы изготовляют различным инструментом: резцами, гребенками, плашками, резьбонарезными головками, дисковыми и групповыми фрезами, шлифовальными кругами и накатным инструментом.
Внутренняя резьба нарезается резцами, метчиками, групповыми фрезами и накатными роликами.
В машиностроении наиболее распространена метрическая резьба. Метрические резьбы выполняют с отклонениями, обозначаемыми для болтов буквами h, g, е, d, для гаек H, G. По точности различают три класса резьбы: точные (Т), средние (С) и грубые (Г), и соответственно им устанавливают поля допусков. Для класса Т устанавливают поля допусков 4h, 4H5Н, 5Н; для класса С - 6h, 6g 6е, 6d и 5H6H, 6H,6G; для класса Г - 8h, 8g и 7H, 7g. Метод нарезания резьбы выбирают в зависимости от профиля резьбы, материала заготовки, типа производства и требуемой точности. При нарезании резьбы необходимо выдержать средний диаметр, угол профиля и шаг, а также обеспечить требуемое качество поверхности.
|
|
Обработка резьбовых поверхностей осуществляется двумя способами: резанием и пластическим деформированием (накатыванием).
Наиболее точные резьбовые поверхности получают на токарно-винтовом оборудовании нарезанием. Существует несколько схем получения резьб, например, с поперечной подачей резца. При данной схеме обработки, выдерживая обратную величину шага (подача на оборот) можно получить одно и многозаходные резьбы.
Аналогично обрабатывают внутренние резьбовые поверхности. При достаточной трудоёмкости данный метод позволяет обеспечить наиболее точные резьбы.
|
|
Наружные резьбы можно получить также с помощью лерок и плашек. Плашками получают наружные резьбы в единичном и серийном производстве. Плашка может быть зафиксирована, то есть вращение сообщается заготовке, либо заготовка неподвижна, а вращается плашка (при слесарных работах). Внутренние резьбы получают метчиками. Метчик, как и плашка, имеет заходную часть, то есть крайние режущие зубья выполнены не в полную геометрию режущего зуба.
Нарезание резьбы происходит при подаче СОЖ, обладающих хорошими смазывающими свойствами, для уменьшения трения.
Резьбы получают также фрезерованием, фрезеруя профильным однониточным инструментом, или используя многозубые фрезы.
При получении резьбы пластическим деформированием (накатыванием), резьбовые поверхности получаются за счёт перераспределения некоторой части материала заготовки под действием усилий инструмента. Данный метод характеризуется высокой производительностью, а также тем, что поверхностный слой заготовки не разрушается, а пластически деформируется. В результате, повышается твёрдость и прочность изделия, при этом отсутствие следов режущего инструмента уменьшает опасность возникновения коррозии. Недостатком метода является его невысокая точность
Накатывание осуществляется тремя способами:
- плоскими плашками;
- накатными роликами;
- сегментами.
Основные требования к крепежной резьбе:
- прочность;
- технологичность;
- относительно большие силы трения в резьбе, предотвращающие самоотвинчивание.
Основные требования к ходовой резьбе:
Дата добавления: 2016-01-04; просмотров: 49; Мы поможем в написании вашей работы! |
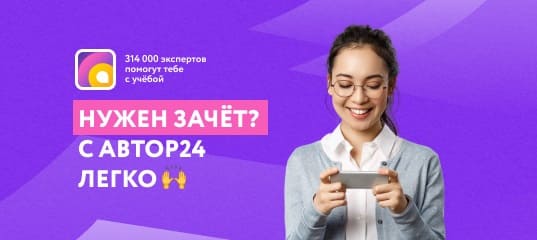
Мы поможем в написании ваших работ!