Технология производства феррохрома
Введение
Ферросплавы – сплавы железа с другими элементами (Cr, Si, Mn, Ti и др.), применяемые главным образом для раскисления и легирования стали (напр., феррохром, ферросилиций). К ферросплавам условно относят также некоторые сплавы, содержащие железо лишь в виде примесей (силикокальций, силикомарганец и др.), и некоторые металлы и неметаллы (Mn, Cr, Si) с минимальным содержанием примесей. Получают из руд или концентратов в электропечах или плавильных шахтах (горнах).
Ферросплавы используются в разных областях металлургии, причем спектр их применения очень широк. Такие ферросплавы, как феррохром или ферросилиций используют для легирования и раскисления стали. Благодаря этому свойства и качества металлов улучшаются: они становятся более износостойкими и устойчивыми к серьезным нагрузкам. В зависимости от того, какой ферросплав используется, металл получает определенные, требуемые в определенном проекте, свойства.
Часто в конкретных проектах инженерами указывается, какой именно ферросплав должен быть использован. То, свойства, которыми будет обладать металл, зависит от исходного сырья ферросплава, механизма введения его в сталь и способа выплавки. Широкое использование ферросплавов в металлургии и объясняется их более выгодными характеристиками по сравнению с чистыми металлами.
Металл при использовании ферросплавов плавится при более низких температурах и в нем сохраняется ведущий элемент. Во время плавления металла с ферросплавами требуется более низкий температурный режим, чем при плавлении металла в чистом виде. А это значит, что при использовании ферросплавов требуются гораздо меньшие энергетические затраты – работа с металлом становится более экономичной и выгодной.
|
|
Технология производства феррохрома
Ферросплавы получают восстановлением окислов соответствующих металлов. Для получения любого сплава необходимо выбрать подходящий восстановитель и создать условия, обеспечивающие высокое извлечение ценного (ведущего) элемента из перерабатываемого сырья. Восстановителем может служить элемент, обладающий более высоким химическим сродством к кислороду, чем элемент, который необходимо восстановить из оксида. Иначе говоря, восстановителем может быть элемент, образующий более химически прочный оксид, чем восстанавливаемый элемент. Восстановительные процессы облегчаются, если они проходят в присутствии железа или его оксидов. Растворяя восстановленный элемент или образуя с ним химическое соединение, железо уменьшает его активность, выводит его из зоны реакции, препятствует обратной реакции - окислению.
|
|
Из всех легирующих элементов в сталях наибольшее применение находит хром. Для выплавки углеродистого феррохрома применяют хромовые руды в основном Донского месторождения, которое находится в Казахстане.
Производство феррохрома можно разделить на три вида:
-феррохром низкоуглеродистый, содержащий углерод до 0,5 %;
-феррохром среднеуглеродистый, содержащий углерод от 0,5 до 4,0 %;
-феррохром высокоуглеродистый, содержащий углерод от 4,0 до 9,0 %.
Феррохром получают при восстановлении достаточно богатых (с высоким содержанием оксида хрома и высоким отношением оксид хрома/оксид железа) хромитовых руд (или концентратов) углеродистым восстановителем (обычно кокс).
Технологический процесс выплавки феррохрома низкоуглеродистого складывается из восстановления оксидов хрома и железа хромовой руды кремнием ферросиликохрома по реакциям:
2 Cr 2 O 3 + 3 Si = 4 Cr + 3 SiO 2,
2 FeO + Si = 2 Fe + SiO 2.
Процесс флюсовый. Шихта, применяемая для выплавки низкоуглеродистого феррохрома: хромовая руда, известь, ферросиликохром. Ферросиликохром дробится, руда и известь подаются без подготовки. Шихта подается в печные бункера, откуда по труботечкам поступает в печи. После проплавления шихты из печи выпускают шлак и металл. Разливка металла производится в чугунные изложницы. Шлак в ковшах вывозится в цех сепарации шлаков.
|
|
Производство среднеуглеродистого феррохрома аналогична производству низкоуглеродистого феррохрома, но сплав содержит повышенное содержание углерода. Увеличение содержания углерода в сплаве производится введением в шихту передельного (высокоуглеродистого) феррохрома. Состав шихты: хромовая руда, известь, ферросиликохром, передельный феррохром.
Производство высокоуглеродистого феррохрома. При выплавке углеродистого феррохрома происходит восстановление железа и хрома из оксидов в руде углеродом восстановителей по реакциям:
3(FеО · Сr 2 O 3) + 3 С = З Fе + З Сr 2 O 3 + 3 СО,
Cr 7 O 2 + 5 С = Сr 7 С 3 + 2 СО.
Выплавка углеродистого феррохрома является шлаковым процессом. Состав шихты при выплавке высокоуглеродистого феррохрома: хромовая руда, восстановитель (кокс, каменный уголь), кварцит.
Температурный режим выплавки высокоуглеродистого феррохрома определяется температурой плавления шлака, так как прогреть сплав, увеличивая выдержку его в печи, в условиях плавки под закрытым колошником не представляется возможным. Температура плавления высокоуглеродистого феррохрома, содержащего 65 %–70 % Сr и 6 %–8 % С, составляет 1550 ºС, поэтому шлак должен иметь температуру плавления около 1650 ºС.
|
|
Основными минералогическими составляющими шлаков являются стекло переменного состава, форстерит (2 MgO · SiO 2) и алюмомагнезиальная шпинель (MgO – Al 2 O 3), возможны кордиерит (2 MgO –2 Al 2 O 3·5 SiO 2), муллит (3 Al 2 O 3–2 SiO 2) и др. Потери хрома в шлаке возрастают с увеличением количества остаточного хромшпинелида и повышением отношения MgO / Al 2 O 3. При увеличении содержания оксида хрома повышается температура кристаллизации шлаков и увеличивается их вязкость вследствие образования шпинели MgO (Cr,Al)2 O 3. Повышение количества оксида магния в шлаке вызывает увеличение вязкости и температуры плавления шлака, приводит к затруднениям при выпуске вязкого шлака. При работе на высокомагнезиальных рудах целесообразно увеличивать содержание SiO 2 в шлаках, что позволит расширить температурный интервал их текучести, повысить степень извлечения хрома и снизить концентрацию углерода в металле.
Состав шлака подбирают, используя различные руды; в качестве флюса используют кварцит, шлак от производства ферросиликохрома, реже – бокситы, бой катодных блоков алюминиевых электролизеров. Кратность шлаков составляет 0,8–1,3, доля шлакообразующих оксидов из хромовых руд достигает 90 %.
В качестве восстановителя при плавке используют кокс, полукокс, газовый уголь. Целесообразно в шихту вводить отходы графитизации электродных заводов, содержащие значительное количество карбида кремния.
Для производства высокоуглеродистого феррохрома используют кусковые руды, для передельного – смесь кусковых и порошковых руд. При производстве чардж-хрома используют низкосортное хромовое сырье. Иногда в шихте используют богатый (27 %–32 % Сr2O3) шлак, получаемый при бесфлюсовом производстве среднеуглеродистого феррохрома, или конвертерный шлак.
Для снижения содержания серы в сплаве по возможности повышают содержание углерода в нем, уменьшают количество крупнокусковой руды в шихте и увеличивают количество богатого шлака от бесфлюсового производства среднеуглеродистого феррохрома. Иногда для тех же целей в шихту вводят некоторое количество марганцевой руды или ферромарганца.
Необходима тщательная подготовка шихты к плавке. Закрытые печи должны работать на усредненных по гранулометрическому и химическому составу хромовых рудах и на коксике с постоянной влажностью (4 %–6 %). Количество кускового или окускованного хромового сырья должно быть более 80 %. При большем количестве мелочи нарушается газопроницаемость шихты и расстраивается ход плавки.
В последнее время в связи с истощением запасов богатых кусковых хромовых руд и увеличением мощности печей приобрело важное значение окускование рудной мелочи, предварительное восстановление и нагрев шихты. При обогащении бедных хромовых руд часто получают весьма мелкий концентрат, который перед плавкой окусковывают с помощью агломерации, брикетирования или окатывания.
Выплавку высокоуглеродистого феррохрома ведут в открытых и закрытых печах мощностью до 115 МВА. Печи футеруют магнезиальным кирпичом, так как использование углеродных блоков привело бы к чрезмерному науглероживанию сплава. Расход электроэнергии на проплавление 1 т. рудной части шихты составляет 5950 МДж (1650 кВт·ч).
При содержании углерода в сплаве выше 7,5% получаемые слитки весьма пористы, легко крошатся. Это затрудняет их транспортировку и приводит к возрастанию потерь хрома при легировании. Пористость слитков уменьшается при снижении доли углерода в разливаемом феррохроме.
Феррохром применяется для легирования многих марок стали. Трудность получения феррохрома и его себестоимость возрастают с уменьшением в нем содержания углерода. Однако при выплавке ряда марок стали (нержавеющие, кислотоупорные и др.) феррохром должен быть с низким содержанием углерода. Кроме того, при выплавке ряда марок стали должно быть ограничено содержание кремния.
Для более полного протекания процесса восстановления расплав переливают несколько раз из ковша в ковш. Уловленная пыль используется при получении рудоизвесткового расплава. При получении феррохрома смешением расплавов создаются более благоприятные условия для удаления углерода, вносимого жидким ферросиликохромом, чем при обычном силикотермическом процессе в печи, благодаря более высокой температуре процесса и большей активности кислорода вследствие более низкой концентрации кремнезема в расплаве.
Дата добавления: 2016-01-04; просмотров: 72; Мы поможем в написании вашей работы! |
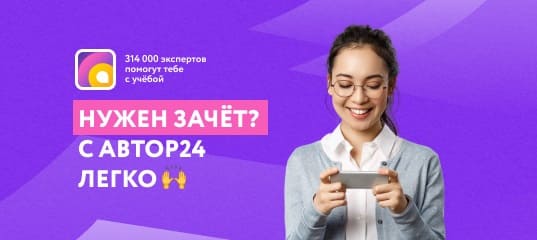
Мы поможем в написании ваших работ!